Both planned and scheduled maintenance are preventive maintenance (PM) strategies that involve proactive activities. The two maintenance methodologies complement each other, with scheduled maintenance picking up where planned maintenance ends. However, despite their overarching similarities, they are not the same.
Planned Maintenance Definition
Planned maintenance refers to a maintenance process that details which resources will be needed to solve a particular equipment malfunction. The goal is to determine which tasks will be completed and how they will be completed.
The process of planning maintenance involves identifying potential equipment issues, outlining steps required for upkeep, and procuring necessary tools and parts for execution. Equipment inspections, process descriptions, ordering replacement parts, and work prioritization make up the planning process of planned maintenance and are overseen by a maintenance planner.
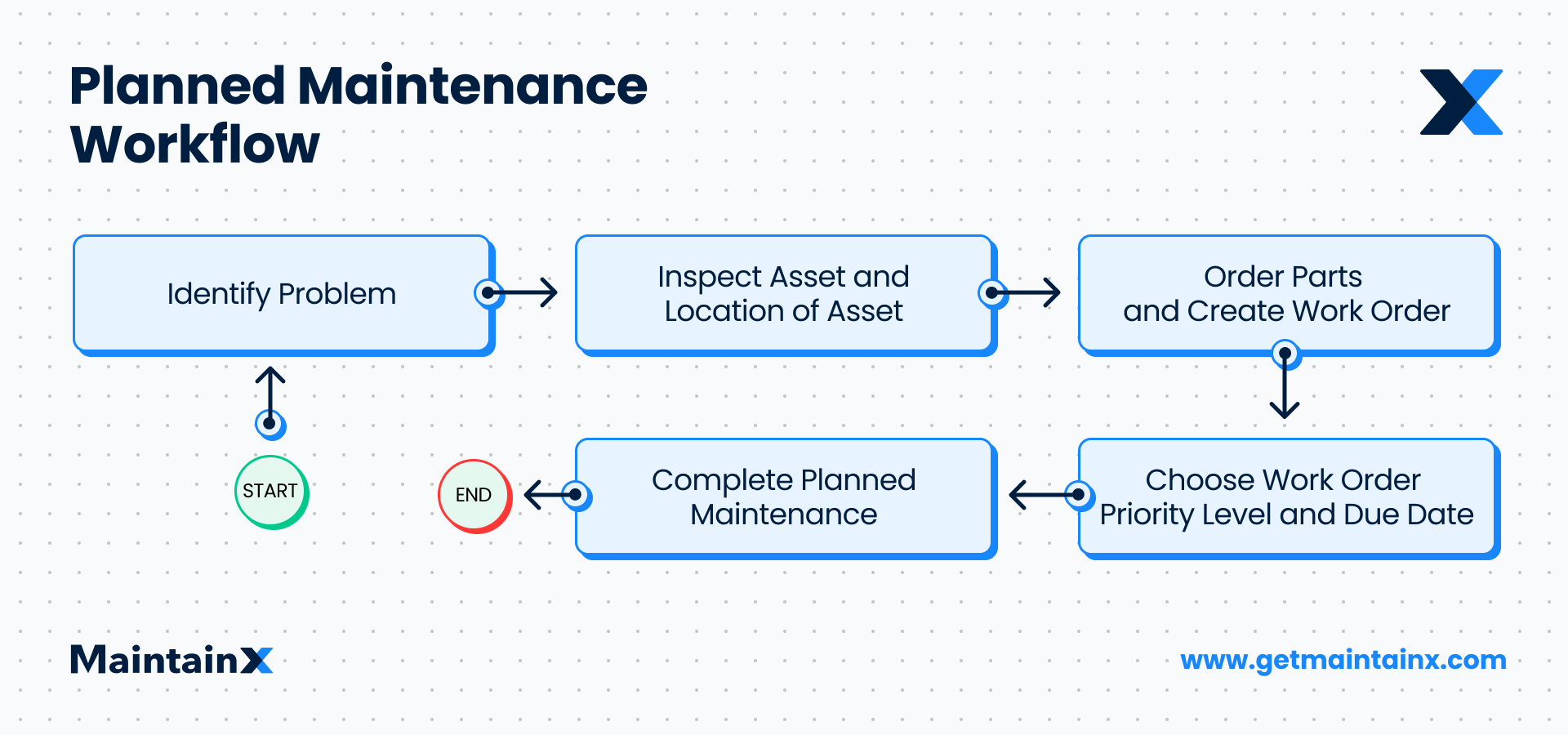
Example of Planned Maintenance
A fleet manager assesses the various routine maintenance activities needed to extend the vehicles’ lifespan and creates standard operating procedures (SOPs) for technicians to follow according to recommendations.
Scheduled Maintenance Definition
On the other hand, scheduled maintenance refers to a maintenance process that details who will complete maintenance tasks and when. It focuses on when planned maintenance tasks will be completed and by whom. The goal is to ensure all maintenance activities are completed within a given timeframe.
Work orders can be scheduled via paper, spreadsheets, or CMMS maintenance software. Scheduled maintenance is completed at repeated intervals according to the manufacturer’s recommendations or per work requests.
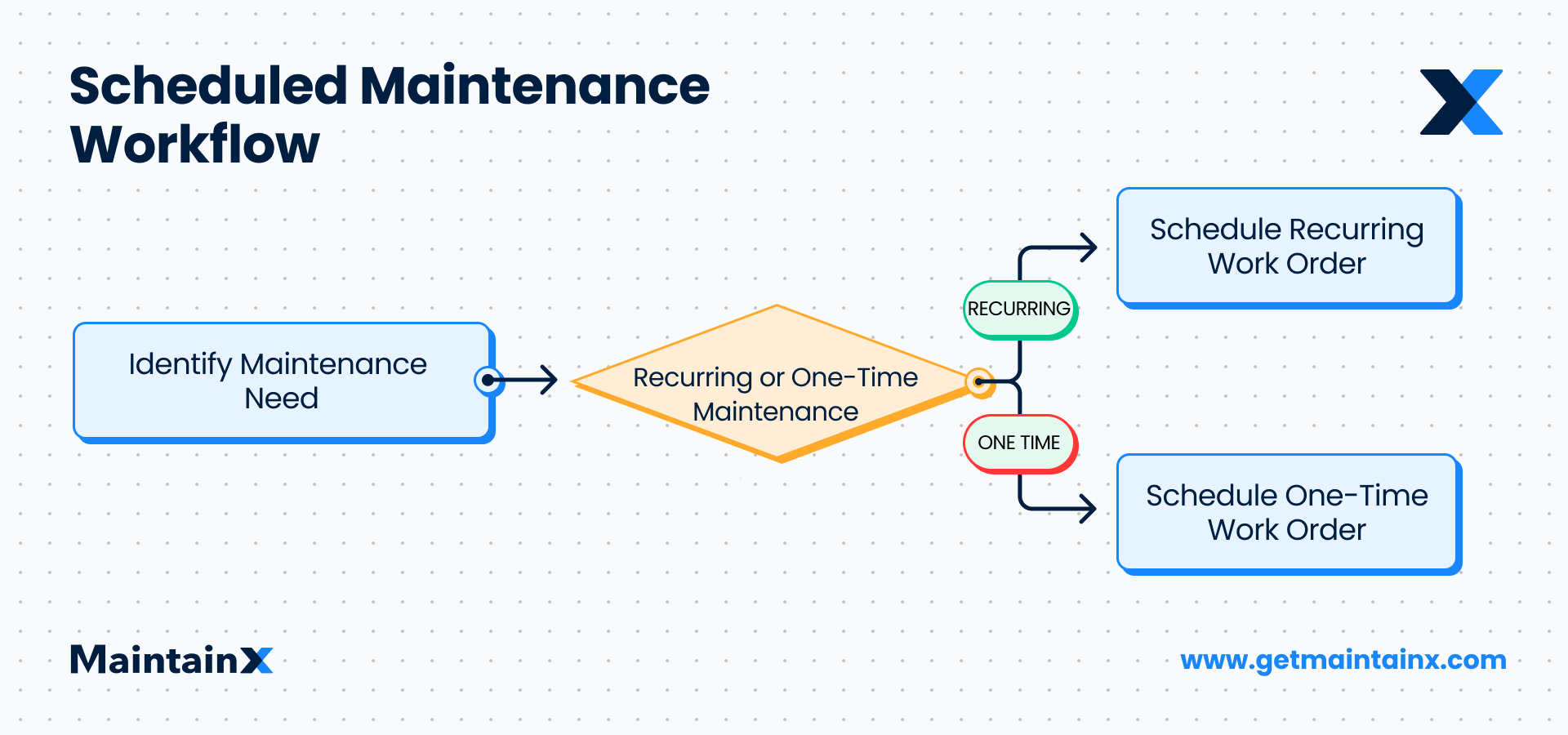
Example of Scheduled Maintenance
The fleet manager schedules recurring work orders based on time and/or usage intervals. For example, every 3,000 miles, or 3 months, vehicles undergo engine oil changes.
Two Sides of the Same Coin
Despite the differences in planned and scheduled maintenance, neither of the two maintenance strategies can work without the other. Planned maintenance without proper scheduling can result in unplanned downtimes when teams aren’t sure who is responsible or how work certain tasks should be done.
Reliable Plant recommends that at least 90 percent of maintenance activities be planned maintenance. Conversely, scheduled maintenance without proper planning results in shoddy workmanship due to a lack of the necessary materials, work tools, and documentation.
The Benefits of Planned and Scheduled Maintenance
The benefits of planned maintenance and scheduled maintenance include:
- Reduced Downtimes: When maintenance tasks are planned and scheduled, small problems can be taken care of before they develop into major issues or equipment failures. Planned and scheduled maintenance allows maintenance teams to gather data and prioritize work orders depending on their urgency.
- Reduced Maintenance Costs: For critical assets, the more they deteriorate the more expensive it becomes to repair or replace them. Planning and scheduling maintenance tasks in the initial stages of a problem significantly lower the maintenance costs.
- Improved Asset Lifespan: If you keep an asset in good working condition, it will be able to serve you for a longer period of time. Proper maintenance extends the lifespan of an asset.
- Reduced Liability: When assets are in good condition, workplace safety is improved, and you don’t have to worry about paying liabilities for workplace disasters.
- Improved Workplace Culture: Reduced downtimes means more engaged employees and positive workplace culture. It also makes collaboration among different teams much easier.
Quick Glance: Planned vs. Scheduled Maintenance
The table below compares planned and scheduled maintenance:
Frequently Asked Questions
What Is the Difference between Planned and Preventive Maintenance?
Preventive maintenance is a form of planned maintenance. Once PM tasks are identified based on time or equipment usage, planned maintenance organizes the resources needed and prioritizes work orders for their effective completion.
What Is the Best Way to Plan and Schedule Maintenance?
Planned maintenance can reduce unplanned downtimes and save organizations from the high costs associated with emergency maintenance. The best way to plan and schedule maintenance is with a user-friendly Computerized Maintenance Management System (CMMS) platform. The software enables users to create, assign, and track work orders; keep track of inventory; and monitor Key Performance Indicators that allow for better maintenance decision-making.
Conclusion
High-performing maintenance teams place all critical assets on PM schedules to reduce downtime, cut extraneous costs, and extend asset longevity. When evaluating Planned vs. Scheduled Maintenance, keep in mind that they are two sides of the same PM maintenance coin.
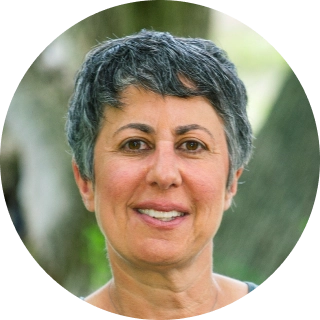
Caroline Eisner
Caroline Eisner is a writer and editor with experience across the profit and nonprofit sectors, government, education, and financial organizations. She has held leadership positions in K16 institutions and has led large-scale digital projects, interactive websites, and a business writing consultancy.
See MaintainX in action