No organization enjoys dealing with equipment breakdowns. However, it’s impractical for busy maintenance teams to perform preventive maintenance (PM) on every asset under their care. For this reason, companies often look toward corrective vs. emergency maintenance. Corrective maintenance is practiced on machines and parts that are cheap to replace, easy to repair, and non-critical to production goals.
Corrective vs. Emergency Maintenance
As the phrase suggests, corrective maintenance happens after equipment malfunctions occur, unlike PM, which happens before malfunctions occur. Thus, corrective maintenance is a reactive maintenance strategy chosen for efficiency. Unfortunately, not all equipment breakdowns can be serviced “whenever time allows.”
Emergency maintenance is another form of reactive maintenance performed in response to unacceptable, unexpected, or potentially hazardous breakdowns. Asset malfunctions that fall into this category require immediate action to resolve health, safety, and productivity threats. Let’s explore the differences between corrective and emergency maintenance by further defining the two terms below:
Corrective Maintenance Definition
Corrective maintenance focuses on restoring equipment to proper working condition after unplanned downtime. It’s a type of maintenance that involves identifying, isolating, and resolving non-critical equipment issues.
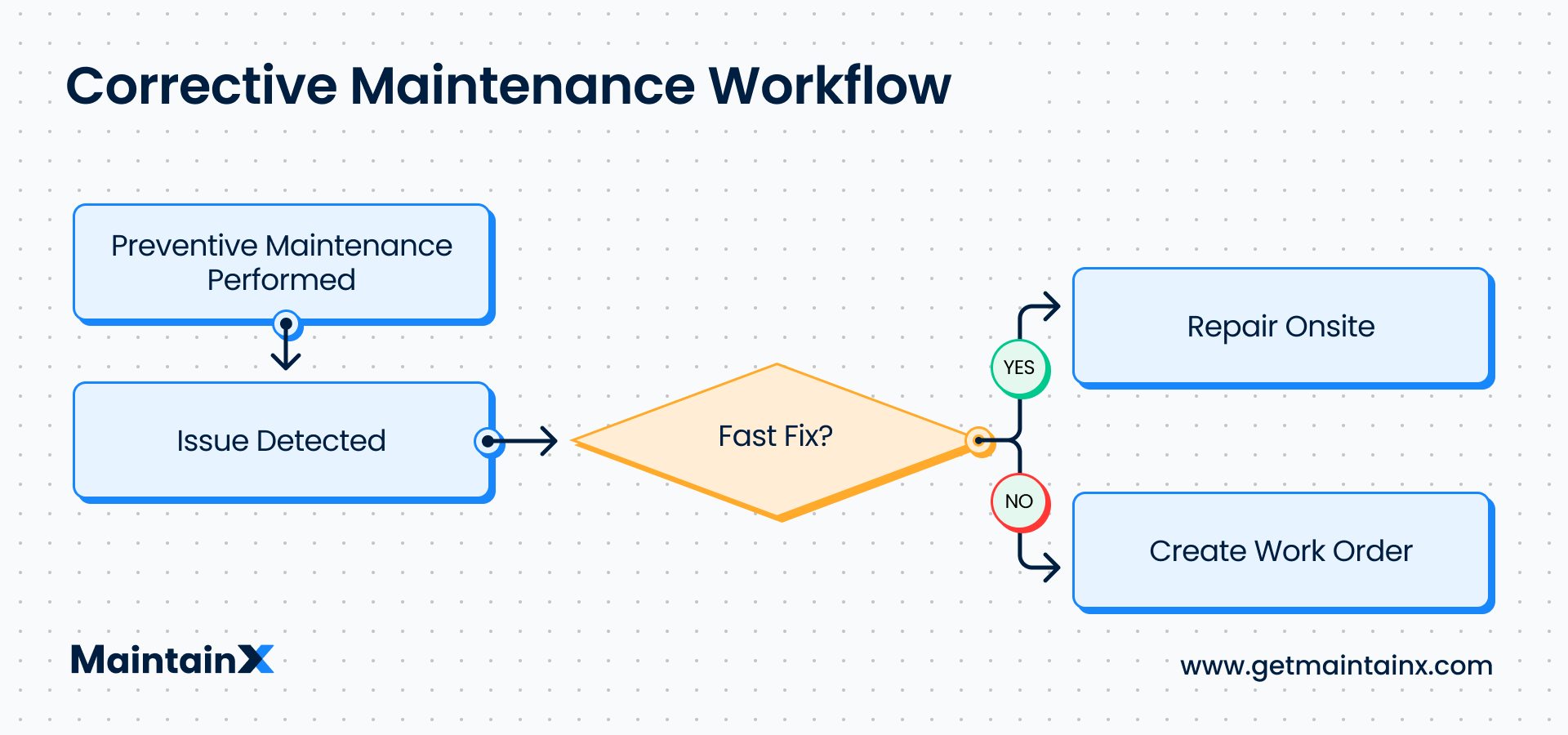
Technicians often identify corrective maintenance opportunities while fulfilling routine work orders, quality control inspections, and other standard operating procedures (SOPs). Commonly performed corrective maintenance tasks include troubleshooting, realigning, readjusting, disassembling, repairing, and replacing equipment. The most common example of corrective maintenance is changing a burnt-out light bulb.
It’s worth mentioning that the term is often divided into either planned or scheduled corrective maintenance. Planned corrective maintenance includes tasks that are deferred because of budgetary constraints, limited staff/time, or outsourced services. Alternatively, unplanned corrective maintenance is simply another term for emergency maintenance.
How Often Should You Practice Corrective Maintenance?
Maintenance experts recommend organizations strive for an 80/20 ratio of preventive maintenance to corrective maintenance for optimal efficiency. However, a whopping 60 percent of companies still use reactive maintenance as their primary maintenance strategy, according to a Reliable Plant Survey. Alternatively, organizations should try to eliminate emergency maintenance.
Emergency Maintenance Definition
As previously mentioned, emergency maintenance refers to maintenance activities performed after an unexpected breakdown that could negatively impact productivity and safety without immediate attention. Due to the urgent nature of the risks involved, emergency maintenance tasks must be prioritized above all existing work orders.
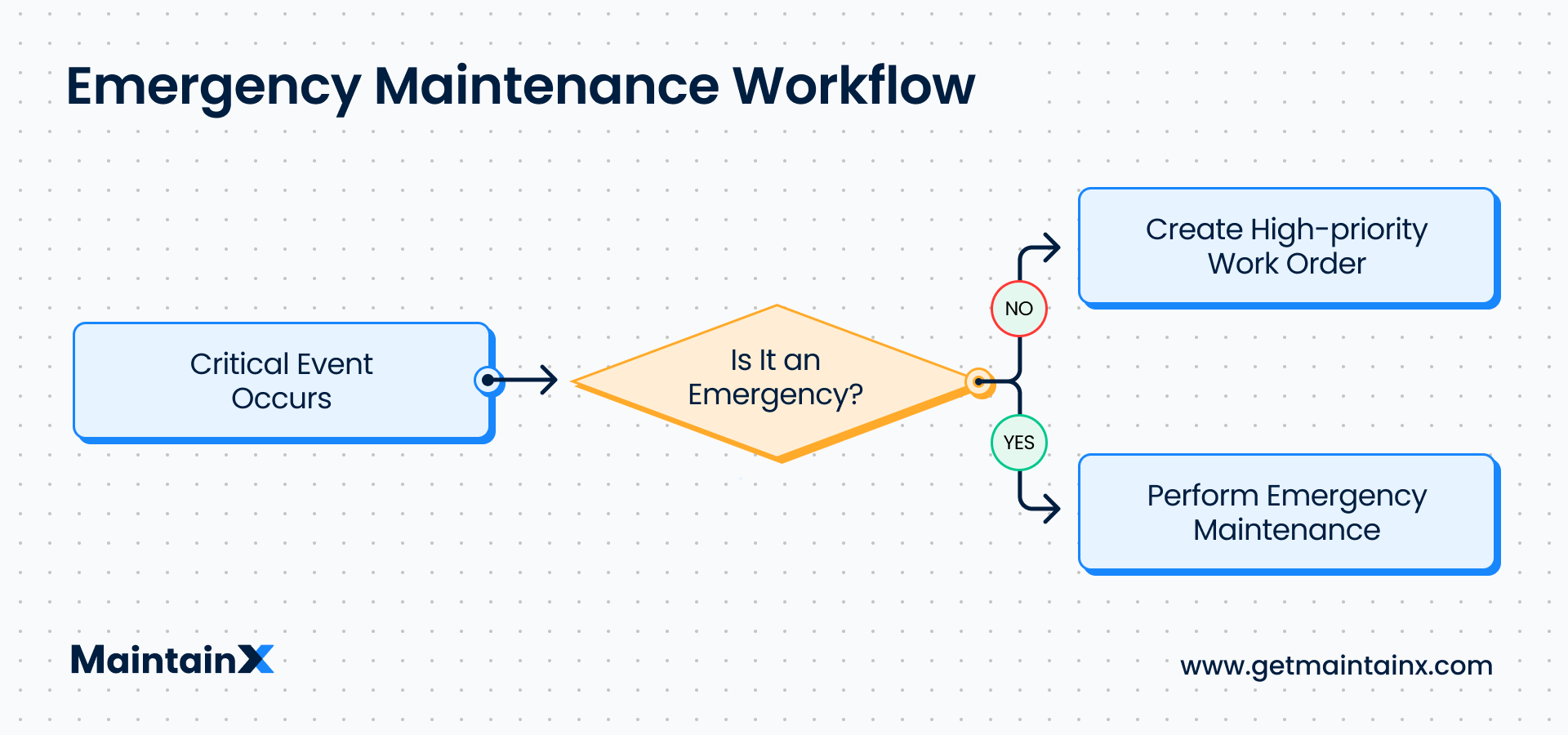
One common example of emergency maintenance is replacing a burst water pipe. If left running too long, a large leak can cause sizable property damage, financial losses, and even physical harm. Though some emergency maintenance is inevitable, organizations are advised to minimize unplanned downtime as much as possible. According to Deloitte, emergency maintenance costs industrial plants as much as $50 billion per year.
Quick View: Corrective vs. Emergency Maintenance
Here’s a summary of the differences between corrective maintenance and emergency maintenance:
FAQ: Corrective vs. Emergency Maintenance
When Is Corrective Maintenance Better Than Preventive Maintenance?
Corrective maintenance is best suited for non-critical equipment that doesn’t substantially impact production or safety. It’s preferred over preventive maintenance when taking care of problems after they’ve occurred is more economical than proactively preventing future failure.
What Are the 4 Types of Maintenance?
Most organizations practice a combination of different types of maintenance. The four most commonly discussed types of maintenance are:
- Corrective Maintenance: A maintenance strategy that involves taking planned or unplanned corrective actions after equipment issues occur. The goal is to return broken assets to operational capacity.
- Preventive Maintenance (PM): A maintenance strategy that involves completing scheduled maintenance tasks to keep assets in optimal working condition, curb unplanned downtime, extend life cycles, and reduce costs associated with equipment failure.
- Condition-Based Maintenance (CBM): An advanced form of PM that uses condition-based diagnostic measurements (e.g., vibrations, temperature, ultrasounds) to predict equipment failure. Operational managers use CBM intervals to make more reliable, efficient, and cost-effective decisions about when to perform maintenance tasks.
- Predictive Maintenance (PdM): An advanced form of PM, and an even more advanced form of CBM, that relies on sensors to relay real-time data in combination with predictive algorithms to precisely predict future breakdown times. Though many resources use the terms PdM and CBM interchangeably, they are not the same. While CBM often includes the same sensor-based technology as PdM, it doesn’t utilize predictive technology.
What Are the Advantages of Corrective Maintenance?
Corrective maintenance has many benefits when properly planned and executed. These benefits include:
- Easy Set-Up: Corrective maintenance doesn’t require intensive planning like PM, CBM, and PdM.
- Enhanced Productivity: It allows maintenance teams to focus on other duties until a problem is identified and needs to be taken care of.
- Simplicity: Organizations don’t need complex tools to identify faults for corrective maintenance. Problems are identified during routine inspections, work orders, or preventive maintenance tasks.
- Cost-Effective: Corrective maintenance saves money, especially on non-critical assets, by performing maintenance only when necessary.
Get a CMMS to Schedule Your Maintenance Tasks
While corrective maintenance isn’t effective as an overarching maintenance strategy, it can complement other proactive maintenance strategies. Corrective maintenance is most effective when combined with a preventive maintenance program that is organized via CMMS maintenance software for scheduling maintenance tasks and assigning work orders.
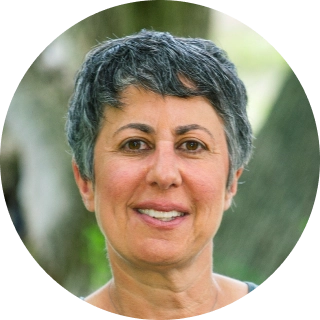
Caroline Eisner
Caroline Eisner is a writer and editor with experience across the profit and nonprofit sectors, government, education, and financial organizations. She has held leadership positions in K16 institutions and has led large-scale digital projects, interactive websites, and a business writing consultancy.
See MaintainX in action