Ahlstrom Reduced MTTR by 90% through Centralized Tribal Knowledge
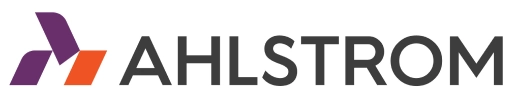
With over 100 registered projects to its name, Karn Custom Woodwork offers high-quality work across the Richmond area to a range of clients across industries, including higher education, medical facilities, courthouses, libraries, churches, offices, and sports facilities.
Bobby Nisbeth, Karn facilities manager since January 2019, owned a mechanical services company before joining Karn’s president Ken Kueny, an engineer, who brought his 30 years of aerospace industry experience to the architectural millwork needs of the greater Richmond area. Ken hired Bobby to focus on building production systems, return equipment to OEM (original equipment manufacturer) conditions, and move forward in a way that allows the company to maintain that operational stability.
Ken said he needed someone to take care of the place because it wasn’t being maintained as he knew it should be. Prior to Bobby’s coming on board, Karn’s facility maintenance worked along the lines of “fly ‘til failure.” Before taking up MaintainX, Karn’s maintenance plan was all reactive.
One night after work, Bobby was browsing online for web-based maintenance applications and found MaintainX. He liked the MaintainX logo. He downloaded the app that night and played around with it. The next day, he showed Ken, and “right off the bat, we could see that MaintainX was a quality solution.” Karn decided to purchase MaintainX’s enterprise plan.
“It was user friendly, intuitive, and very easy to fully implement documented work orders with pictures and even pdf files. We knew we had something good right off—an excellent clean platform that continuously delivers for us.”
—Bobby Nisbeth, Facilities Manager
Bobby said, “I just wanted an app where all I need to do is use one interface. No problem. MaintainX has it covered. It even gives team members communication abilities. When a team plays together, they stay together—like when people throw the ball to each other, they learn how to work together. When people can shoot digital messages back and forth, all related to work orders, with files and pictures, it solves problems. People learn to develop an interconnectedness. The organization becomes more efficient because people learn how to work together. The issues become 10x easier to manage.”
One of Bobby’s first steps was to identify the electrical and air systems that needed to be in good shape to operate the business successfully. Fixes, upgrades, or replacing systems—whatever it takes, Bobby says—so that “we can count on the systems to deliver for the guys the machines they are operating so they have what they need on a daily basis.”
When asked about how MaintainX works for Karn Custom Woodwork, Bobby explained: “All you need to do is load MaintainX on your phone. You go out on the floor. Take pictures in the app. And then here’s your service work order with the picture plugged right in. From that first ticket, the entire system starts. You don’t have to build a bunch of stuff to start using it. You’ve documented the whole experience. You can send a request directly to a vendor from a work order.”
For Bobby, MaintainX is the easiest way to directly collect all the information for a service work order, an incident, or a job. “We started with just me and are adding request users as needed. It will be easier for the whole company when everyone else is on board.”
Bobby said that when he first came to Karn, he created an Excel spreadsheet template, to be filled out manually to track the data. “But no one else could easily integrate with paper forms without copying and sharing.” With MaintainX, Bobby documents the work orders, and executive management sees the benefits. “When you get so that you are just doing preventive work, and you can count on it, that’s when you really start to see change. We’ve even started up preventive maintenance walkthroughs to inspect everything. We are a far cry from the old ‘fly ‘til failure.’”
In less than a year on MaintainX, Bobby has brought the small company on board with more than 350 work orders, 9 teams, and over 200 assets, with locations, vendors, and procedures all in place.
Bobby noted that “The value of MaintainX is far beyond the cost of it. Ten people can write notes in a work order and load pictures. All dashboards are updated for each user. This is key in construction: we always need to verify and meet specifications and the contract specs and required codes and standards. With MaintainX, anyone can verify the level of detail that is being accomplished and glean whatever is necessary from it at any time.”
Karn Custom Woodwork’s expertise is in managing large and complex commercial millwork and casework projects and providing the finest products and workmanship for the Richmond-area commercial market. The company is certified by AWI (Architectural Woodwork Institute) and the FSC (Forestry Stewardship Council), as well as being a SWaM-certified small and veteran-owned business.
Get more done with MaintainX