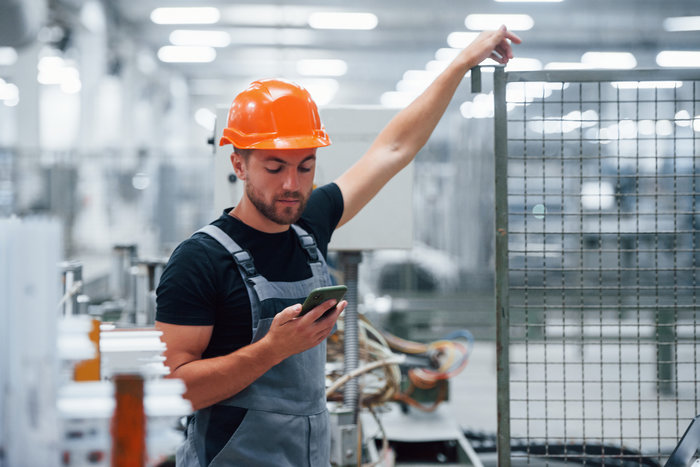
At MaintainX, we believe work order software systems with chat capabilities will revolutionize the way maintenance teams around the world troubleshoot asset failures, discuss work orders, and stay in touch. In this post, we’ll discuss the advantages that organizations are already experiencing via work order instant messaging.
Let’s think about chats for a second. Hollywood made movies about it. Teenagers stayed up late using it. An entire generation mourned its discontinuation (even though hardly anyone used it anymore). What are we talking about? AIM—the world’s first instant messaging (IM) platform that launched in 1997.
Revolutionizing Maintenance with Chat
As the story goes, AOL software developers created the platform during their off-time before releasing it free of charge, much to the chagrin of company executives. The online application revolutionized modern communication by providing a real-time chat alternative to email.
“Online chat was the thing that, until it came around, no one knew they needed, but once they started using it, it became impossible to live without.”
AIM creator Barry Appelman
Several years later, business apps like Slack began integrating instant messaging, private forums, and file sharing into user-friendly hubs for workplace collaboration. Once again, office employees didn’t know they needed workplace IM until they experienced the difference in efficiency.
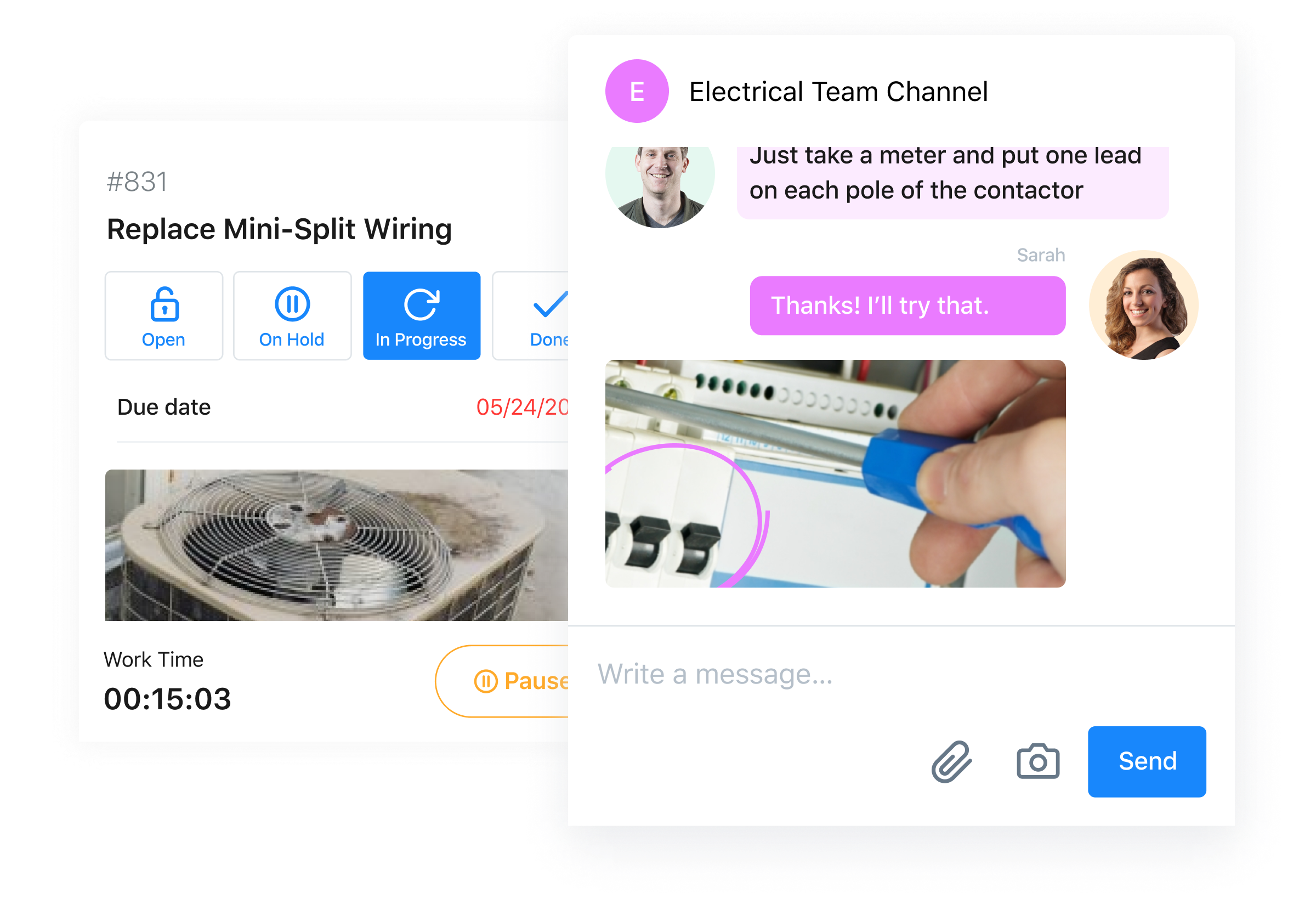
Four Reasons Work Order Software with Chat Is Crucial
MaintainX released the world’s first work order software platform with workflow collaboration and chat functionality designed for mobile, tablet, and desktop in 2018.
Also called Computerized Maintenance Management Systems (CMMS), work order management systems are used by industrial plants, manufacturing facilities, and industries across the board to automate maintenance programs, track inventory, and manage assets. Put simply, any organization responsible for maintaining critical assets via preventative maintenance (PM), predictive maintenance (PdM), and/or reactive maintenance can benefit from CMMS.
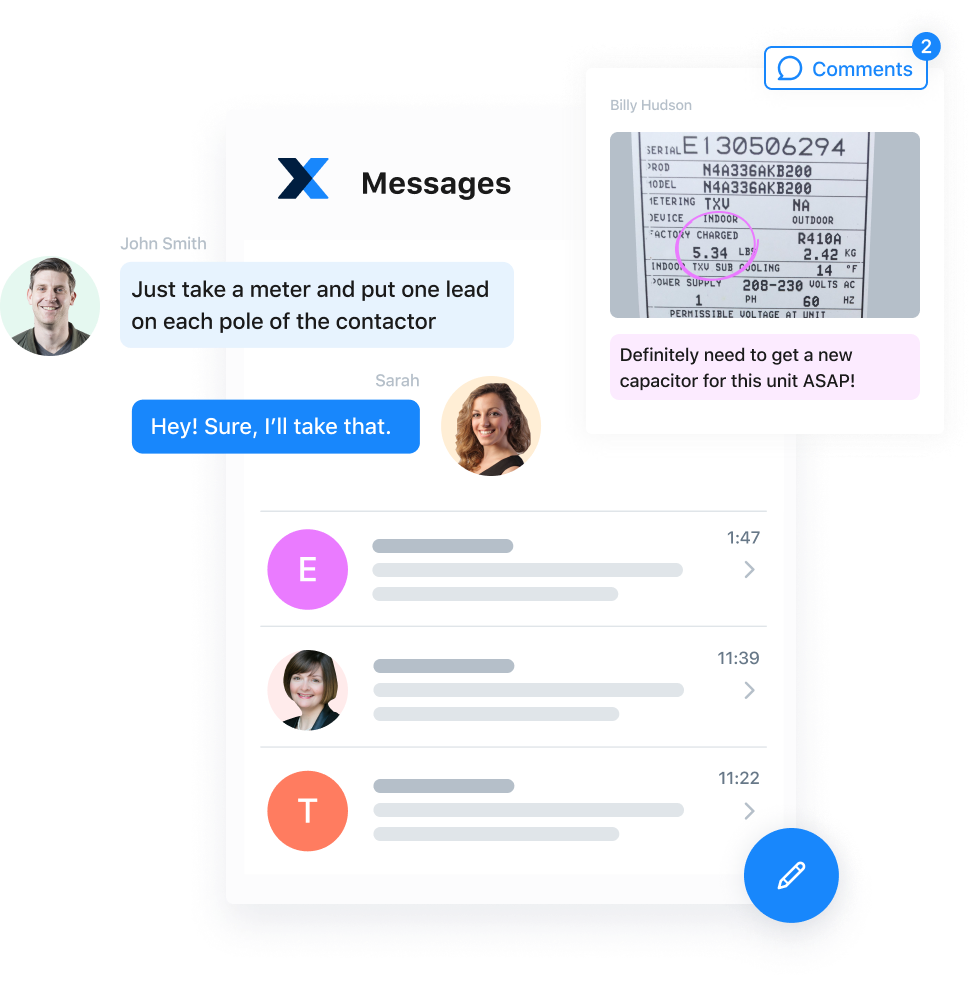
Work Order Software with Chat
Here’s a closer look at how work order mobile apps with chat streamline maintenance tasks, simplify service requests, and eliminate stress:
1. Chat Saves Time and Avoids Mistakes
Not only can operational managers utilize the typical capabilities provided by work order software solutions— work order scheduling, asset management, advanced reporting, inventory management, and work requests automation—they can also now experience greater efficiency with integrated chat.
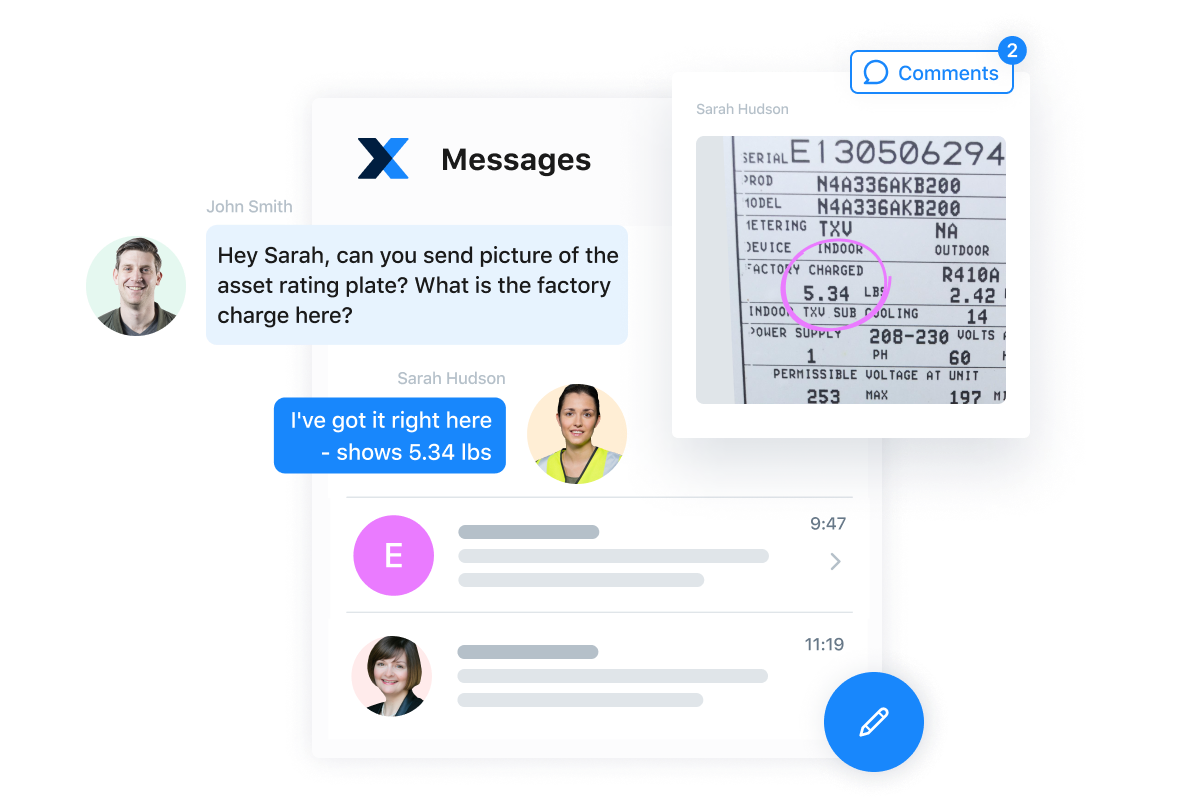
Unlike email, instant messaging (IM) provides immediate, synchronous resolution to maintenance concerns that may have otherwise lingered unnoticed. Here’s how work order software chat saves time:
- It encourages brevity: Users pause and ask themselves: What is the easiest way to say this? Alternatively, email and paper communications lend themselves to over-explaining, and phone calls lend themselves to time-consuming small talk.
- It organizes ongoing communication: Managers can organize discussions within work orders, topic categories, and specific groups. For example, the important detail management shared with Ted about asset #105 won’t get lost in a stack of papers or email threads.
- It reduces procrastination: It’s pretty easy to put off returning a phone call, responding to an email, or even responding to a text message (assuming one puts their smartphone on “silent mode” during work hours. However, receiving an instant message directly within a work portal encourages quicker response times.
Once your team starts using work order chat, you will probably wonder how you ever went without it. No more PMs falling through the cracks, no more arguing over who dropped the ball, and faster resolution of equipment failures to avoid downtime!
2. Managers Can Support Their Teams
As seasoned technicians increasingly retire, managers are responsible for training new hires. According to a survey by Futurestep, millennials want more feedback at work than other generations have. With that said, it doesn’t mean everyone feels comfortable admitting when they don’t know how to do something.
Less experienced employees may feel hesitant to “bother” managers with small questions throughout the day. Instant messaging provides a less-intimidating form of communication, allowing new employees to quickly get the answers they need to complete work orders. Additionally, program administrators can upload equipment manuals as PDFs directly into work order comment threads.
3. CMMS Software with Chat Simplifies Compliance
One of the biggest challenges faced by operational managers regarding work order software is compliance. Computerized Maintenance Management Systems (CMMS) that are too difficult to navigate don’t get used. Consequently, not much changes after implementing costly preventive maintenance and SOP programs.
Translation: Team members often feel comfortable using chat-based software more quickly than traditional work order programs. Most folks already use some type of chat function every day, whether it be Facebook Messenger, WhatsApp, or standard text messaging.
According to the Radicati Group, more than 7 billion IM accounts (not including mobile messaging) existed worldwide in 2019. This number is expected to reach more than 8.9 billion by 2023. Adopt a popular tool that employees already enjoy using, and they will be more likely to jump on board with its other software features.
4. In-App Chat Streamlines Time-Sensitive Announcements
Recently, maintenance facilities in industries across the board have been implementing new procedures to increase efficiency. The fastest and easiest way to communicate important policy changes to team members is via instant messaging. Instead of waiting for workers to check their inboxes, management can relay important information ASAP.
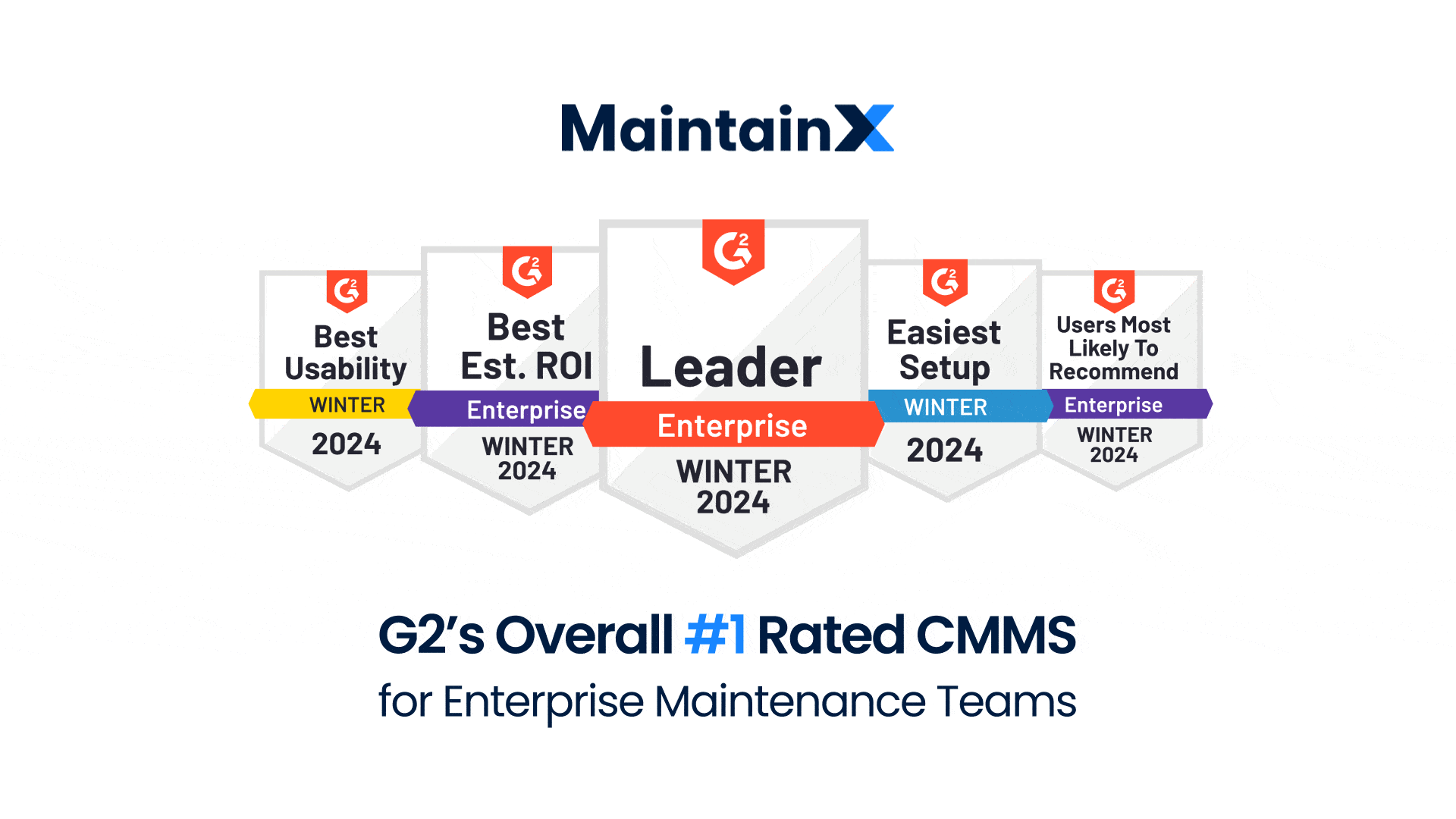
MaintainX: Enhanced Work Order Software with Chat
Work order software should do more than enable the scheduling of PMs—field technicians should feel confident quickly communicating, problem-solving, and uploading files related to maintenance requests in real time. MaintainX is the world’s first work order software platform that a) contains chat functionality and b) is designed for mobile devices from the get-go. Managers can access it from desktops, and field technicians can access maintenance schedules via iOS or Android.
MaintainX is the perfect solution for maintenance teams wanting to streamline communication between technicians, managers, and executives. It is ideal for facility managers, property managers, restaurant managers, safety managers, plant managers, and more. The best part? It’s easy to use.
FAQs
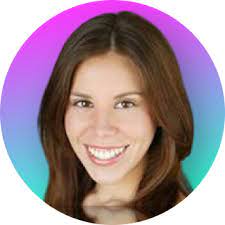