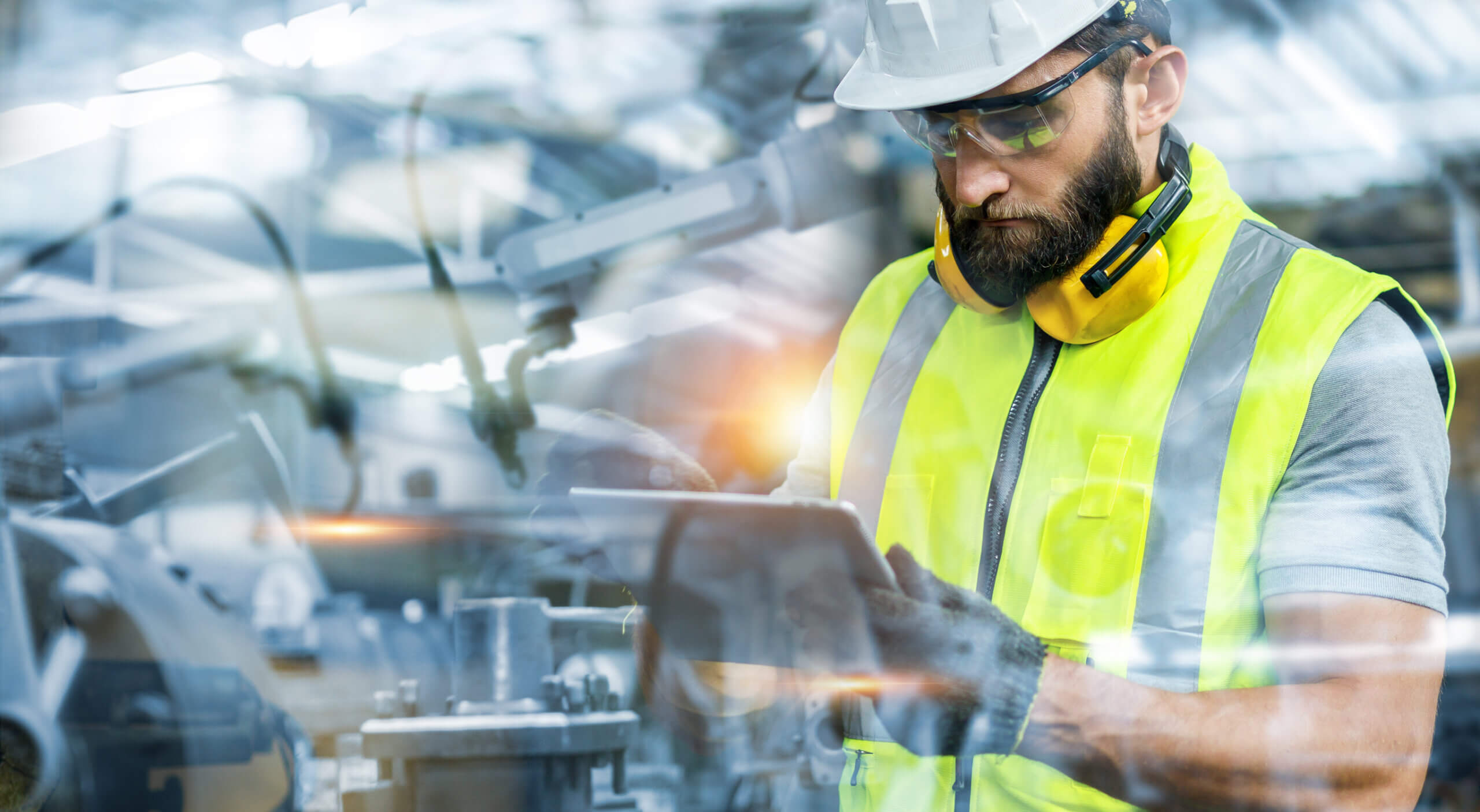
The maintenance software solutions market is vast. Most solutions fall into two categories: Operations Platforms and Point Solutions. Yet, despite overwhelming choices, the landscape isn’t difficult to navigate.
The main difference between both categories relates to scale. Operations platforms can be applied broadly, while point solutions have a specific focus.
Before we get deeper into the differences and why you might choose one over the other, let’s take a closer look at what they mean individually.
“Choosing the right software solutions for your business can be challenging and contentious, with long-term implications. For many companies, the debate may be whether to embrace one or more point solutions or an integrated platform that addresses multiple processes and functions.”
Forbes
Operations Platforms
An operations platform is a large-scale, comprehensive IT solution that manages business processes. They are integrated, end-to-end solutions for gathering data and connecting people and processes. Platform solutions are customizable and scalable.
If you’re using a platform, you can create customized solutions tailored to your business needs. A good example is Microsoft Sharepoint, through which you can produce various solutions based on the needs of your department or business.
Point Solutions
On the other hand, a point solution is a software or IT tool that enables a single business process. Unlike operations platforms that work across multiple use cases, point solutions aim to handle one use case. They range from predictive maintenance planning to work order automation. You can’t customize or apply point solutions to multiple problems.
“Put simply, the difference between a point solution and a platform is that one is a toy car, and the other is a set of Lego blocks. [A] point solution is a very specific piece of software, developed for a specific problem…. [A] platform is typically described as a robust foundation for you to build solutions on. It allows you to solve one specific problem and address several others.”
Checkbox
Operations Platforms vs. Point Solutions
Beyond the general and specific use, it all comes down to flexibility and scalability. In this case, it’s easy to decide which one you need.
Do you want a robust foundation you can apply in different ways? An operations platform is the obvious choice. Or do you want solutions to specific problems? Point solutions it is.
Still, it’s a bit more nuanced than this. There are advantages and disadvantages to both. Let’s think through a few of these now.
Advantages of Operations Platforms
The advantages of the platform approach include the following:
- Platforms allow you to customize solutions to your specific business needs.
- You can execute digital transformation more quickly from your existing foundation to operations platforms.
- You can scale an operations platform up or down as your business requires. For growing teams or businesses, this makes adaptation easier.
- You can onboard staff more easily to platforms. Workers only need to learn one system instead of multiple interfaces.
- One integrated platform means you only have to deal with one vendor or technology partner, reducing miscommunication risk.
- You will likely have lower maintenance costs by maintaining only one platform.
Disadvantages of Operations Platforms
- Operations platforms cost more upfront. Therefore, depending on your business, spending upfront on one comprehensive solution may be challenging instead of spending on various point solutions over time.
- If you want an approach you can quickly jump into, platform solutions aren’t the best bet. These solutions tend to be long-term investments because of how much they cost. As such, they require more thought and research before adopting.
- Unfortunately, operations platforms run the risk of being a single point of failure. This is because they make your business reliant on one vendor or technology stack. As such, if one thing goes wrong, you’ll face more challenges adapting.
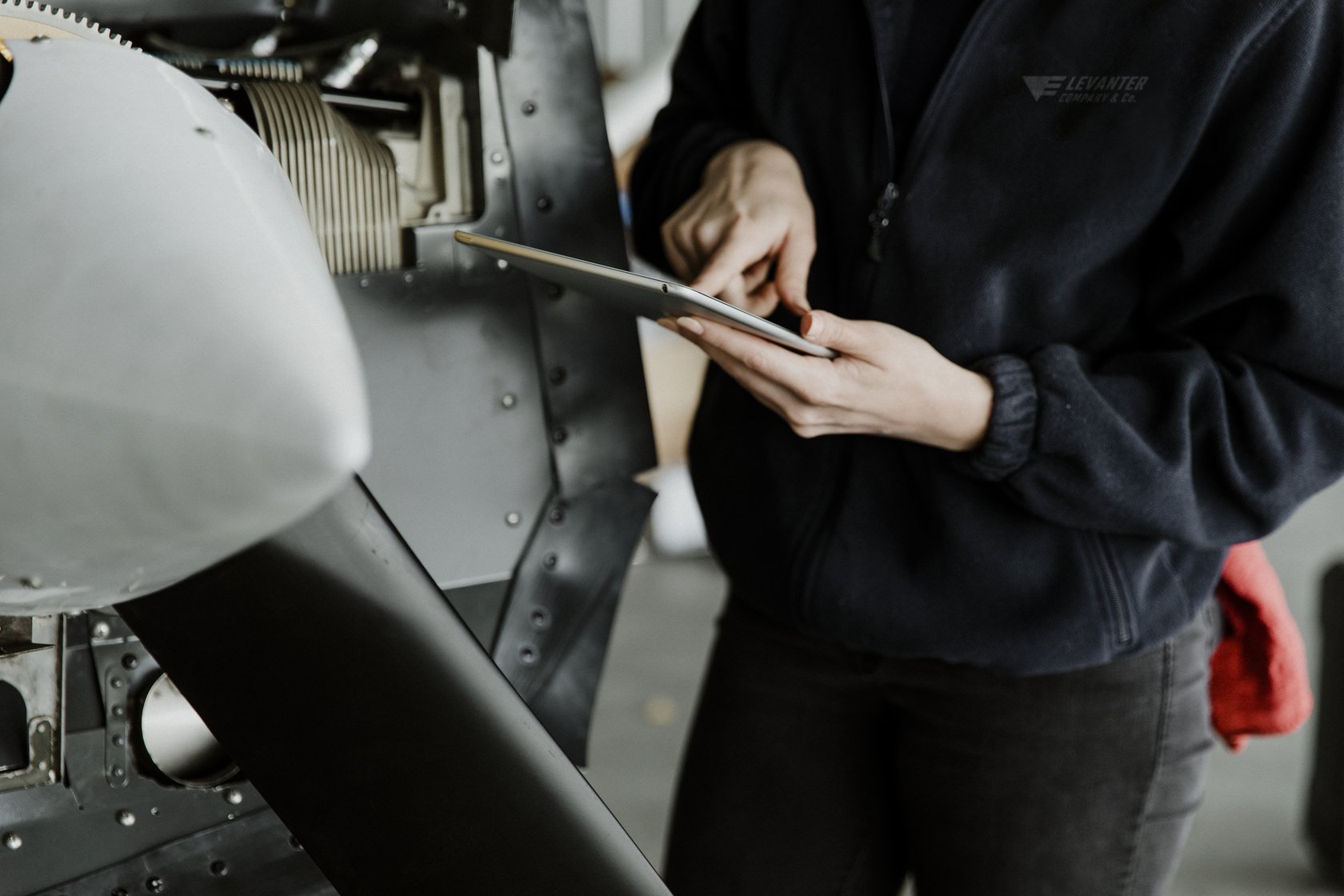
Advantages of Point Solutions
- You can choose the best-in-class solution to a specific problem. In addition, vendors often focus on fewer things, enabling a higher degree of functionality for their specific solution.
- Apps are quicker to get up and running because they have limited complexity. Point solutions are thus better for solving short-term problems.
- You aren’t locked into a particular ecosystem. If you have a problem, you can switch to a different vendor more easily.
- If need be, you can quickly upgrade to a new technology.
Disadvantages of Point Solutions
- While offering best-of-breed solutions, they are challenging for new employees who have to learn multiple technology stacks.
- Existing employees (including your IT team) can find it challenging to interact with multiple interfaces.
- Individual systems may be simple, but managing multiple systems across a business can be complex.
- Dealing with multiple service providers can be challenging.
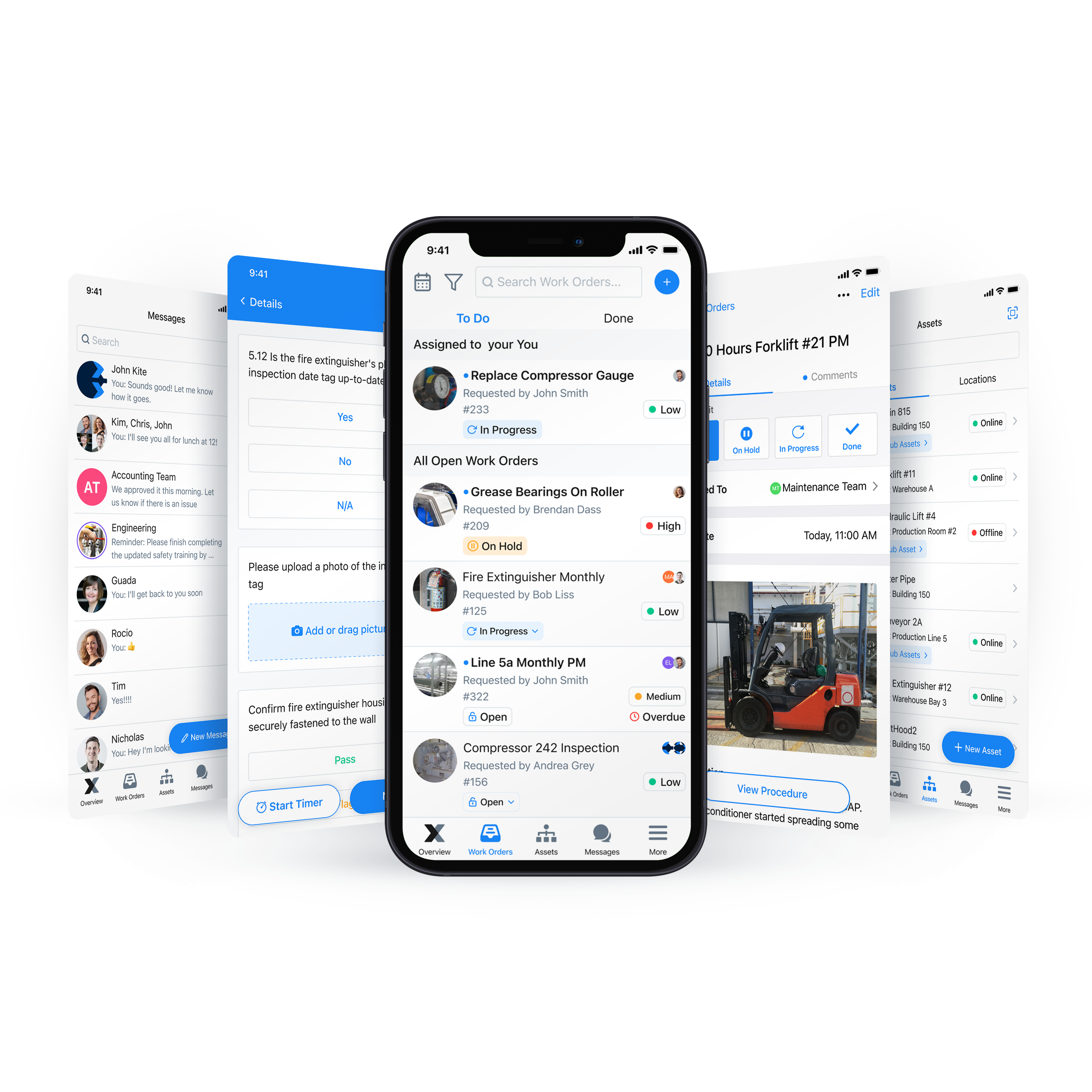
Four Ways to Optimize Your Processes with a CMMS
If you’re looking for an operations solution to optimize your business processes, consider a Computerized Maintenance Management System (CMMS). As the name suggests, a CMMS typically focuses on helping to streamline your maintenance workflows. However, well-designed CMMS platforms can also offer a lot more functionality.
MaintainX, for example, offers a wide range of features to help organize many of your processes beyond maintenance. Here are a few:
- Work order management: MaintainX allows you to receive and create all kinds of work orders. You can create maintenance requests and assign them to assets, technicians, and teams. MaintainX is a mobile-first software. As a result, your team members can receive real-time notifications about work orders directly from their mobile devices.
- Asset tracking: MaintainX offers built-in asset management features that allow you to know which assets are active and when. You can keep track of your downtime and uptime and access detailed maintenance logs. MaintainX’s reporting features are robust and allow you to track KPIs in real time.
- Safety management: Automatically schedule inspections and safety protocols across your organization. With MaintainX, you can set due dates for specific activities and decide how frequently you want them to run. You also can access asset and work order histories to ensure everything runs smoothly. Not only will this help with your in-house audits, but you’ll also be in compliance with outside regulators.
In addition, MaintainX offers other features, such as a Parts Inventory module and a Global Procedure Library. You can access APIs to integrate programmatically with MaintainX entities. Check out the website to learn more about the features, read a case study on customer experience, or get your hands on the app today!
FAQs
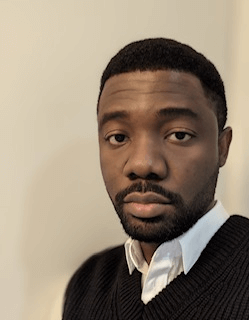
Lekan Olanrewaju is a content writer with years of experience in media and content creation. He has held positions at various media organizations, working with and leading teams at print magazines, digital publications, and television productions.