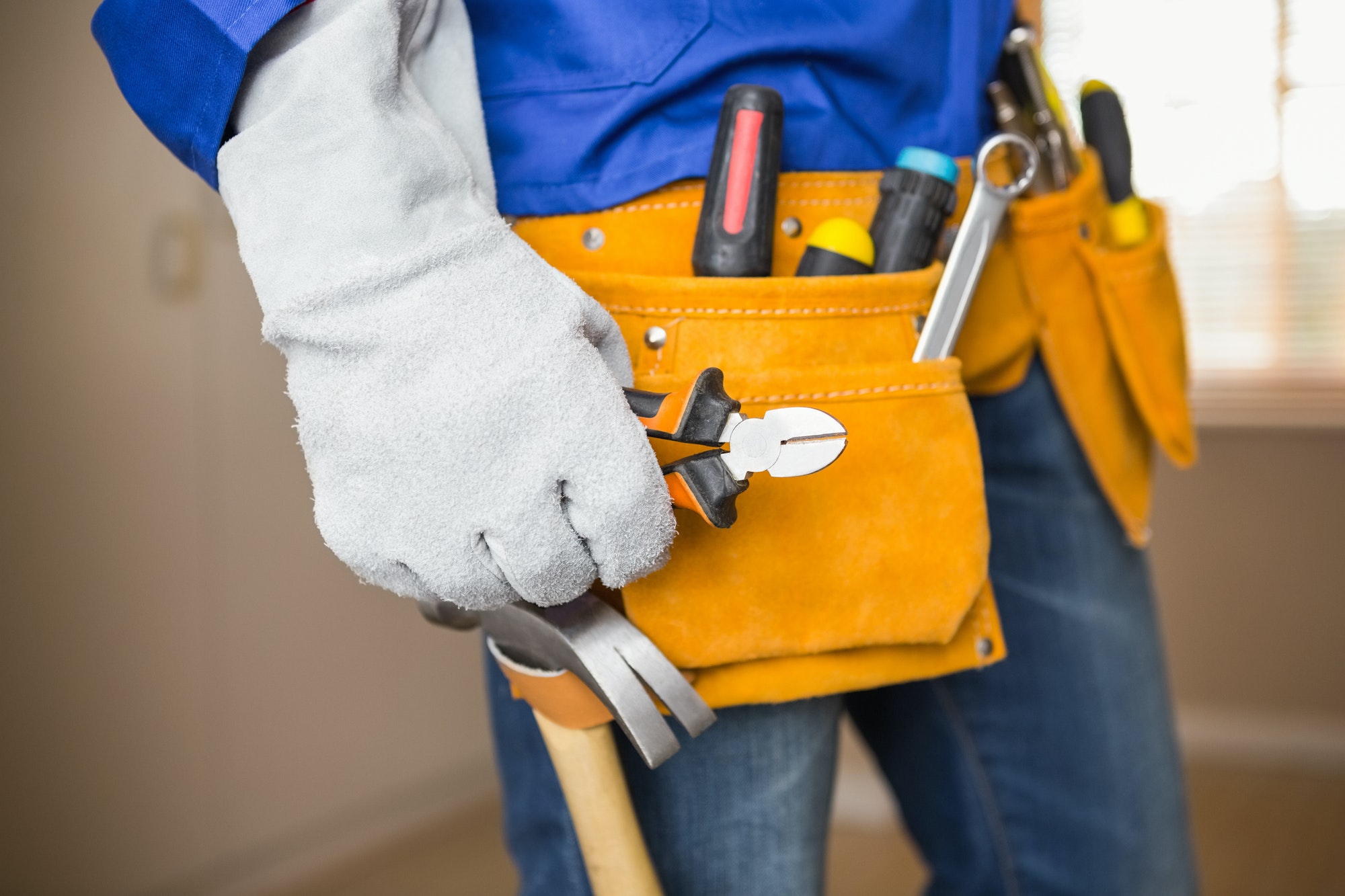
Maintenance is the backbone of every successful business. This article provides an overview of how to run a high-performing maintenance team. It will cover the primary objectives of maintenance, how to set reasonable goals, and how to streamline O&M management for greater efficiency.
From restaurants to manufacturing, industries around the globe depend on functioning equipment to fulfill customer promises every day. According to the Bureau of Labor Statistics, the maintenance industry is projected to experience a 4 percent annual job growth up to 2029. Of course, when equipment operates as expected, maintenance teams largely go unnoticed.
However, the longer critical equipment remains idle, the more everyone starts asking, “Hey, where are the maintenance technicians?!” McDonald’s cashiers don’t hope restaurant POS systems will ring up customers any more than package handlers hope warehouse forklifts will turn on—they just expect them to work.
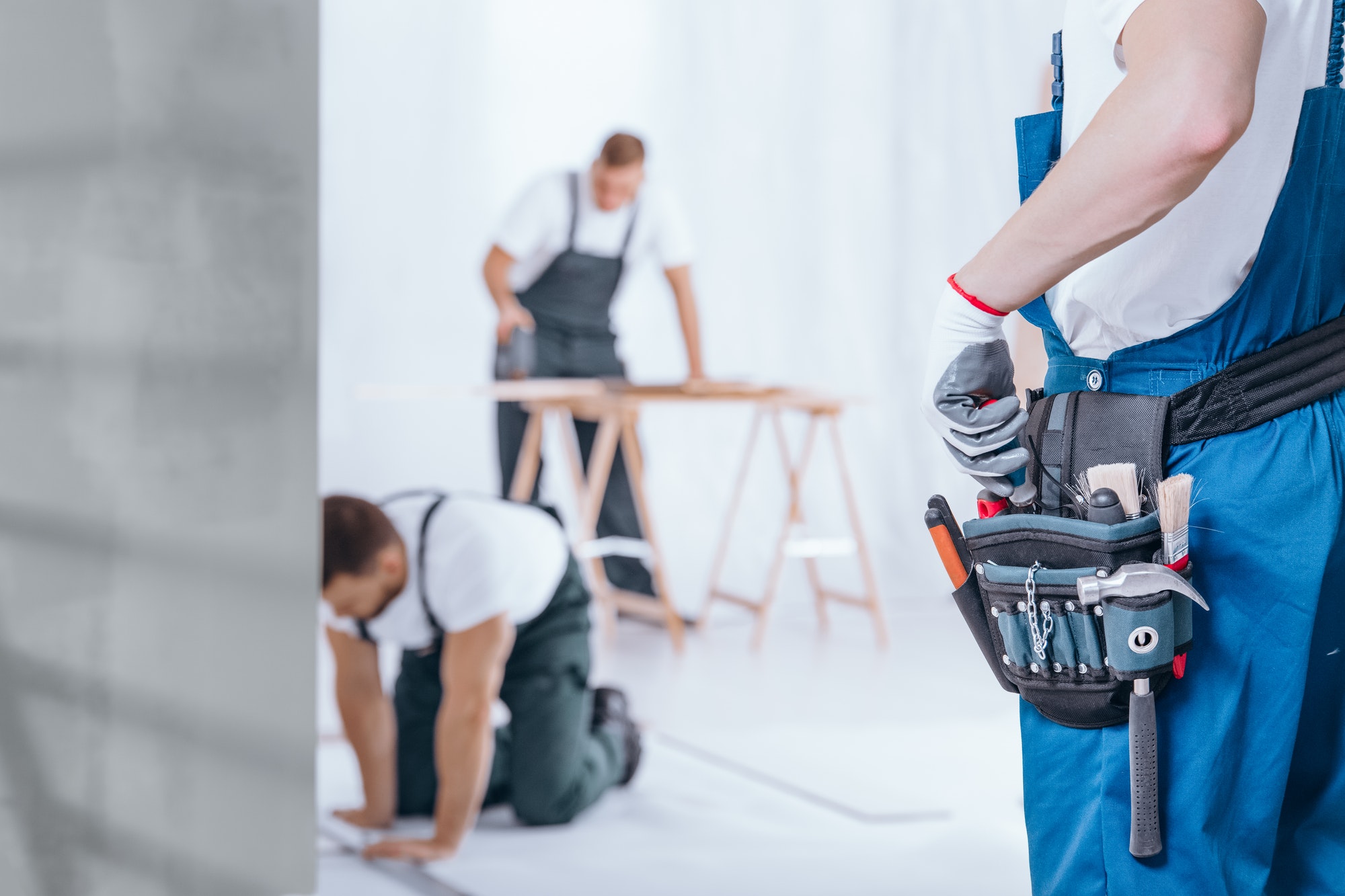
The Quick Guide to Building a Maintenance Team
Running a modern-day maintenance department goes beyond simple upkeep. Considering the large number of assets many companies depend on, maintenance management involves juggling several financial, operational, and functional balls.
Numerous daily decisions may lead to successful outcomes or colossal failures that impact organizational productivity. However, one of the most impactful decisions a maintenance manager can make is who to bring on board. World-class maintenance teams aim to perform preventive maintenance (PM) on assets at non-disruptive times, maintain high schedule compliance rates, and minimize unexpected breakdowns. But these things don’t just happen without effective maintenance technicians.
Let’s look closer at some of the most frequently asked questions surrounding maintenance departments and the roles within them before discussing how to build the dream team.
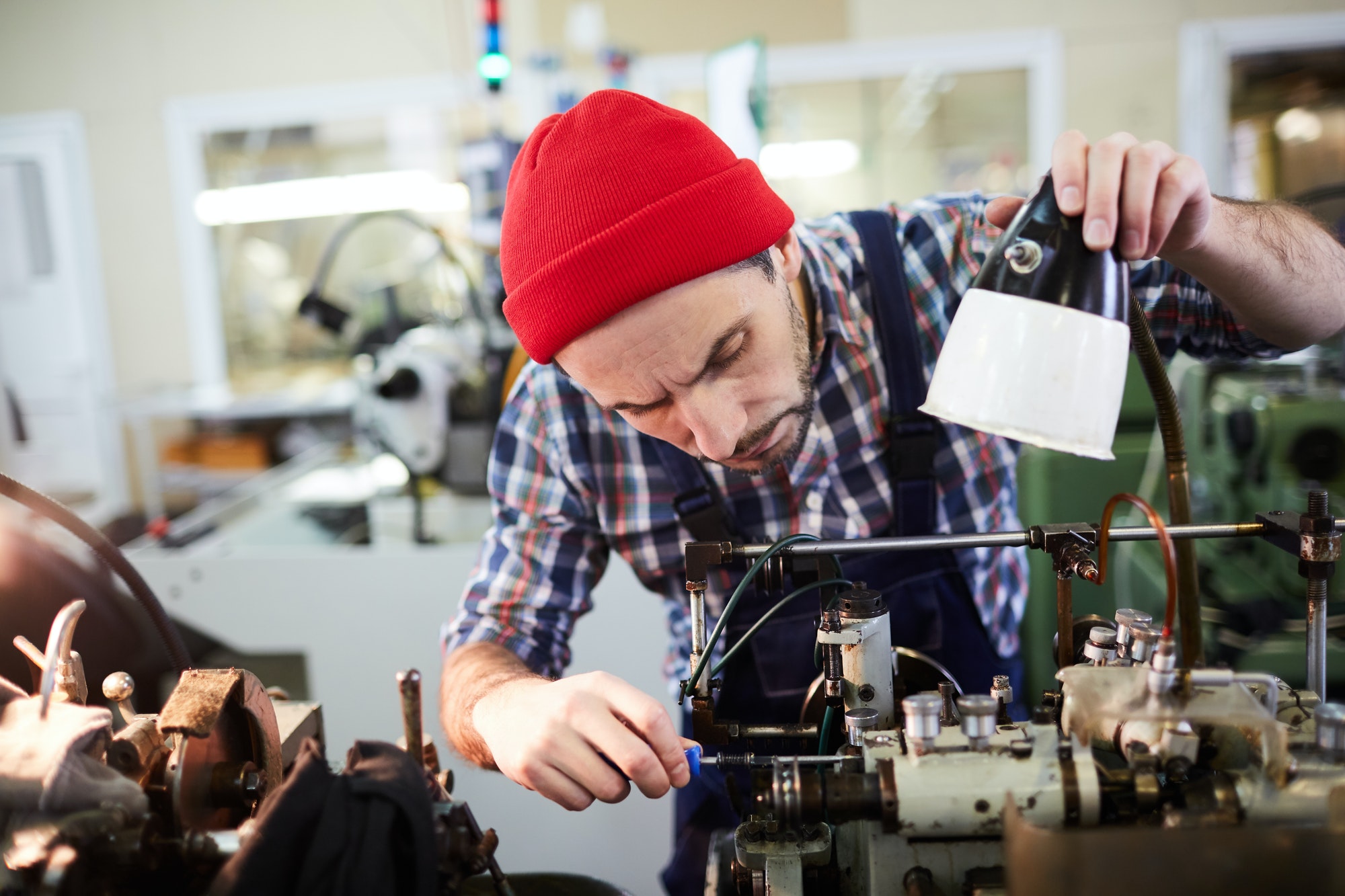
What Is the Role of a Maintenance Department?
Maintenance departments have a simple goal: keep assets running. However, as mentioned earlier, maintenance managers face several obstacles on the road to reliability. Maintenance departments must balance their priorities with those of the organization as a whole. This often means working within scheduling, budgeting, and resource constraints.
For example, say your organization aims to produce 100,000 crates of beer per week. The maintenance department must plan scheduled tasks to keep equipment running without disrupting production goals.
In addition, maintenance managers must also align with executive goals. For example, the plant may prioritize improving energy efficiency alongside reducing equipment downtime. Generally, maintenance staff is responsible for:
- Keeping comprehensive maintenance services under optimal costs.
- Engaging in corrective maintenance for unplanned issues.
- Providing maintenance support to other departments.
- Sourcing equipment parts and maintenance supplies.
- Contributing to the achievement of production goals.
- Maximizing asset uptime to avoid disruptions.
- Increasing asset life cycles with routine care.
As a rule of thumb, the more expensive the equipment involved, the more complex the maintenance department’s responsibilities will become. Industrial industries like mining, power, and oil often use advanced problem-solving methodologies to maintain equipment.
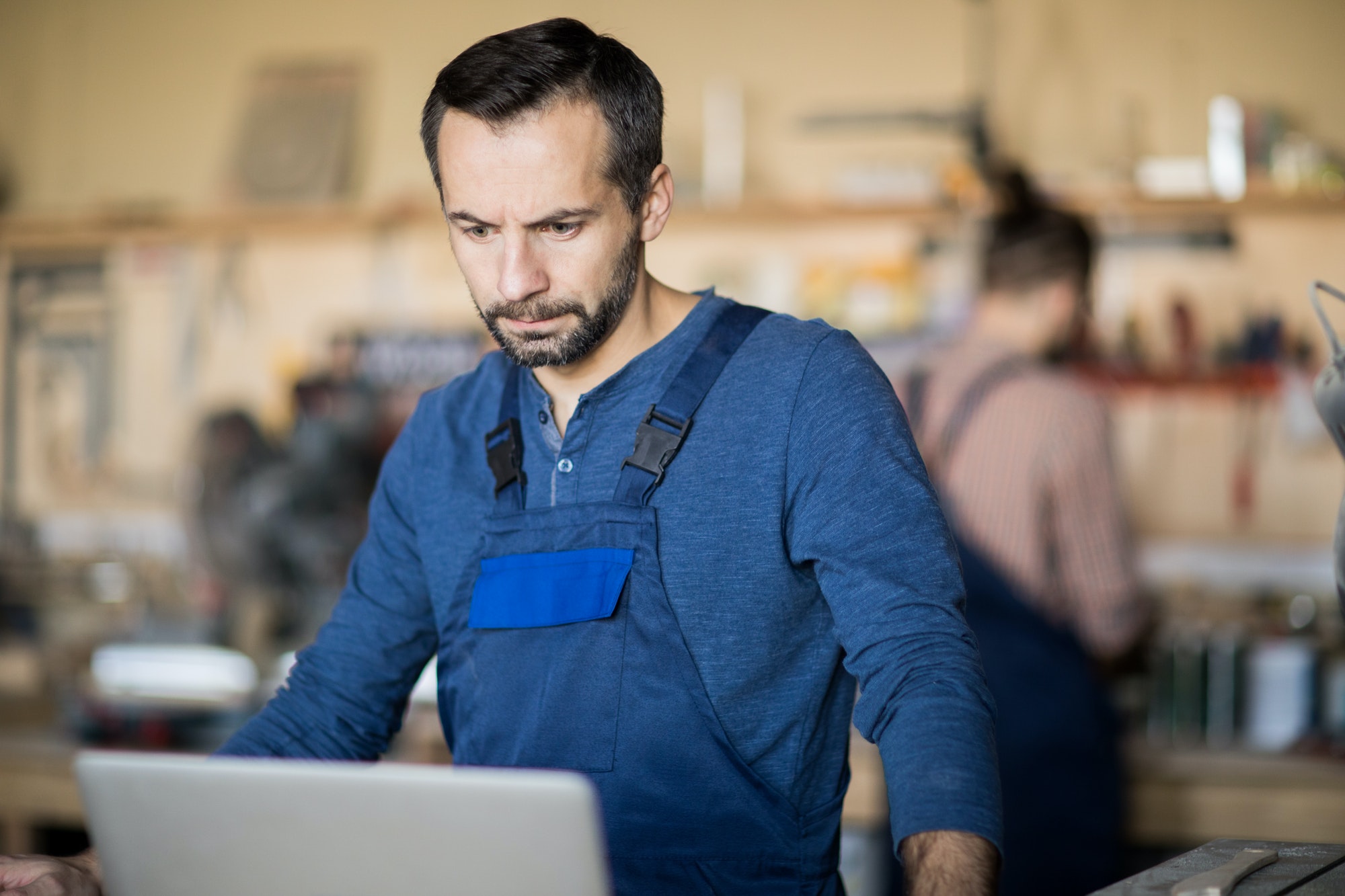
What Are the Maintenance Team Roles?
Maintenance team sizes can range from a couple of on-call maintenance technicians to dozens of full-time professionals. Factors that influence team depth include organization size, financial budget, and the number of specialty devices on site. Managers assign team members different roles based on their skills, abilities, and experiences.
Important Roles within Maintenance Teams
- Maintenance Director: Maintenance directors oversee the maintenance work of technicians. They are largely responsible for formulating maintenance goals and presenting the department’s budget to leadership.
- Maintenance Manager: Besides developing the maintenance strategy, maintenance managers are also responsible for enforcing budget controls to optimize maintenance costs. Additionally, they develop monthly maintenance workloads for the team as well as oversee maintenance inventory management.
- Maintenance Supervisors: Maintenance supervisors schedule weekly and daily maintenance activities and assign tasks to maintenance technicians. They also take part in the recruitment, training, and supervision of the technicians, besides performing regular asset inspections.
- Maintenance Technicians: They are responsible for executing the department’s maintenance program. They also carry out emergency maintenance activities.
It’s worth mentioning that for small maintenance teams, the responsibilities of the maintenance supervisor are usually handled by the maintenance manager. Larger facilities also may have a larger team consisting of maintenance planners and schedulers.
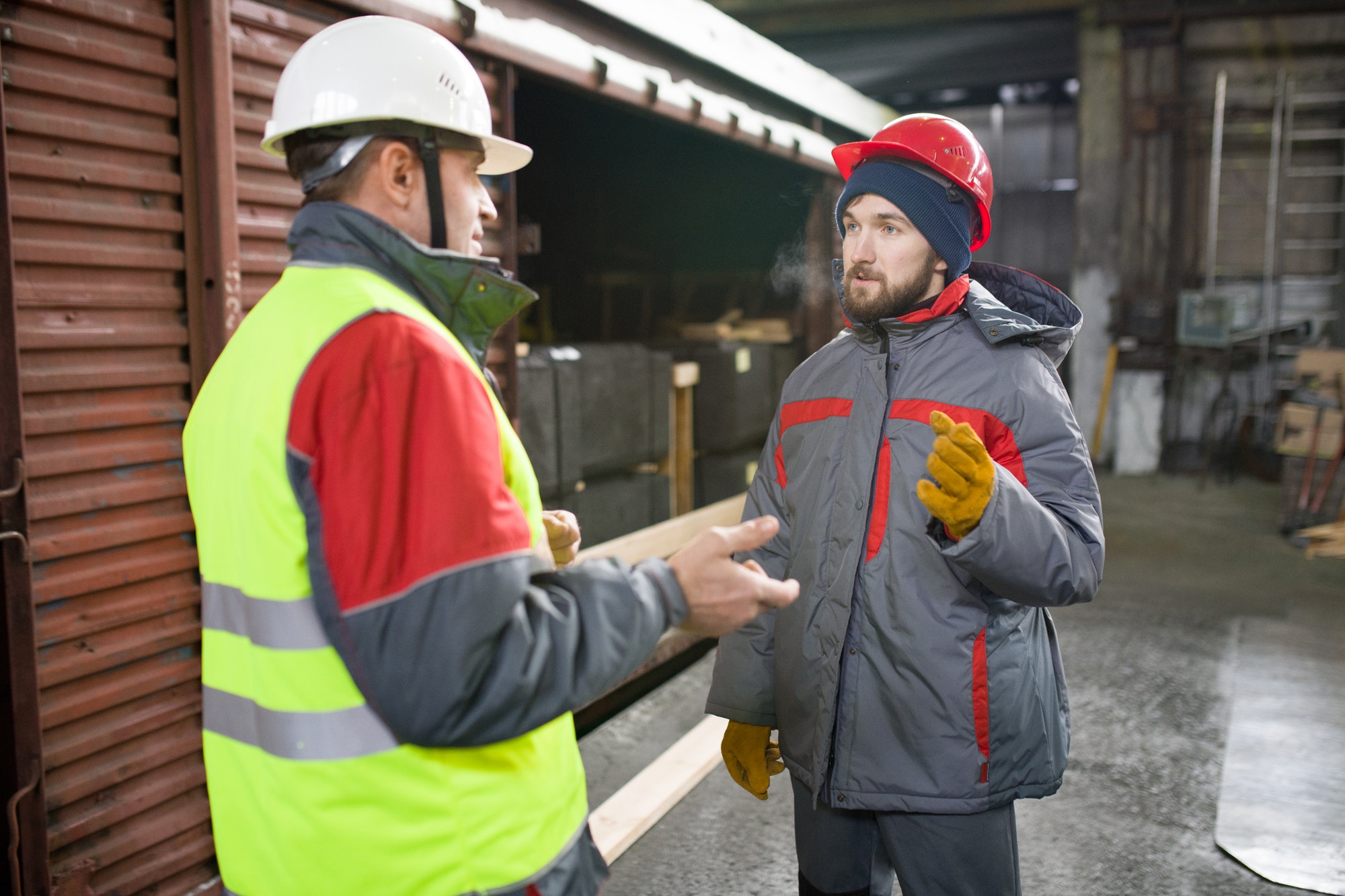
How to Start a Maintenance Team
It’s every maintenance manager’s dream to have a responsive team that completes assignments with minimal guidance. But you don’t stumble upon such workers by a stroke of luck.
You have to build “the dream team” yourself! As a maintenance manager, you’re in charge of hiring, training, and guiding competent individuals toward success. Here are a few tips that will help you to start and run an efficient maintenance team:
1. Set SMART Goals
Before you assemble your team, identify your maintenance goals. They should be specific, measurable, achievable, realistic, and timely (SMART).
Following the SMART acronym will help you set actionable objectives you can actually meet instead of vague ideas that are quickly forgotten. As a bonus, SMART goals can help identify the skills you most need before moving on to step two.
2. Hire Excellent People
To reduce extraneous spending, hire the right people. Identifying qualified professionals is crucial to avoiding equipment oversights, streamlining troubleshooting, and avoiding frequent outsourcing.
Essential skills to prioritize when recruiting maintenance technicians include:
- Working knowledge of mechanical and electrical machines.
- Comfortability working independently.
- Commitment to continued education.
- Demonstrated problem-solving skills.
- Strong communication skills.
- Time management skills.
- Attention to detail.
- Familiarity with CMMS.
- Physical strength.
In addition, look for individuals who share organizational values. Sometimes the best hires aren’t the most skilled, but they’re committed to personal excellence. These individuals will likely work hard to fill any knowledge gaps and become high performers.
If you have the capacity, consider partnering with local institutions to provide mentorship programs and internships to students taking maintenance courses. This will allow you to nurture budding talent to meet your maintenance needs.
3. Develop Standard Operating Procedures
Organize your department’s most important processes into standard operating procedures (SOPs). SOPs are documented checklists that guide employees on how to complete maintenance assignments from start to finish.
Standardizing routine maintenance procedures ensures all tasks are completed according to company standards—regardless of who is completing them. Furthermore, good SOPs simplify the onboarding of new hires. With that said, SOPS that don’t get used are useless.
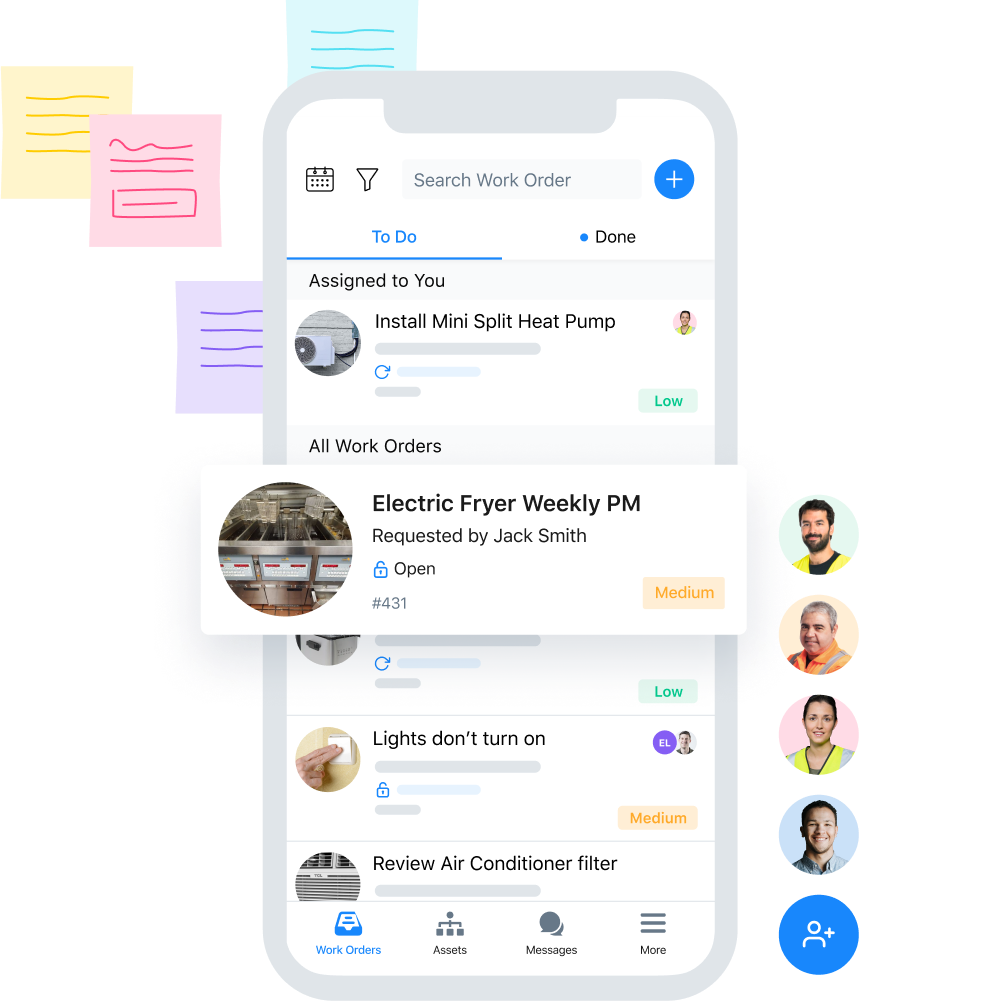
We recommend converting paper SOPs into digital checklists using a mobile CMMS; this way, busy technicians can quickly access them from their smartphones or tablets.
4. Centralize Communication with Business Messaging
For your team to be productive, you must establish a centralized communication system. Horizontal communication lines allow information to flow easily between executive leadership, upper management, and maintenance technicians.
Remaining accessible to workers ensures that conflicts are addressed before unfamiliar situations get out of hand. Additionally, it provides workers the opportunity to share feedback leadership needs to make important capital, logistical, and human resources-related decisions.
The best way to reduce miscommunication is to discourage written notes, email threads, and random text messages that often “get lost in the noise.”
While a quick phone call is often the best form of communication for emergencies, business messaging apps are ideal for typical maintenance troubleshooting.
5. Track Performance
Measuring the performance of your maintenance department is the best way to improve maintenance operations over time. Take the time to identify the maintenance metrics and key performance indicators (KPIs) most representative of your SMART goals.
Tracking data will allow you to identify frequently occurring problems, unaddressed skill gaps, and departmental systems that need improvement. Sharing metrics with your team can also improve accountability and motivate everyone to correct departmental shortcomings.
The easiest way to track, analyze, and act upon data is to use a CMMS with advanced reporting capabilities. MaintainX provides maintenance teams with a user-friendly reporting dashboard that can be filtered to illustrate mean time to repair (MTTR), planned maintenance percentage (PMP), and time vs. cost metrics.
6. Embrace Technology
As mentioned throughout this post, embracing technology makes all the difference when it comes to successfully managing a maintenance team in today’s busy world. Mobile CMMS solutions make it easier than ever to:
- Catalog company asset information in one place.
- Create, assign, and oversee work orders in real time.
- Develop editable SOP checklists for recurring tasks.
- Share individual and team messages with fellow employees.
- Automate spare parts management (and set minimum quantity alerts).
- Receive live photos, drawings, and attachments from field technicians.
The best part? MaintainX is available for scalable monthly/per-user fees. Our clients range from small shops to multi-million-dollar enterprises.
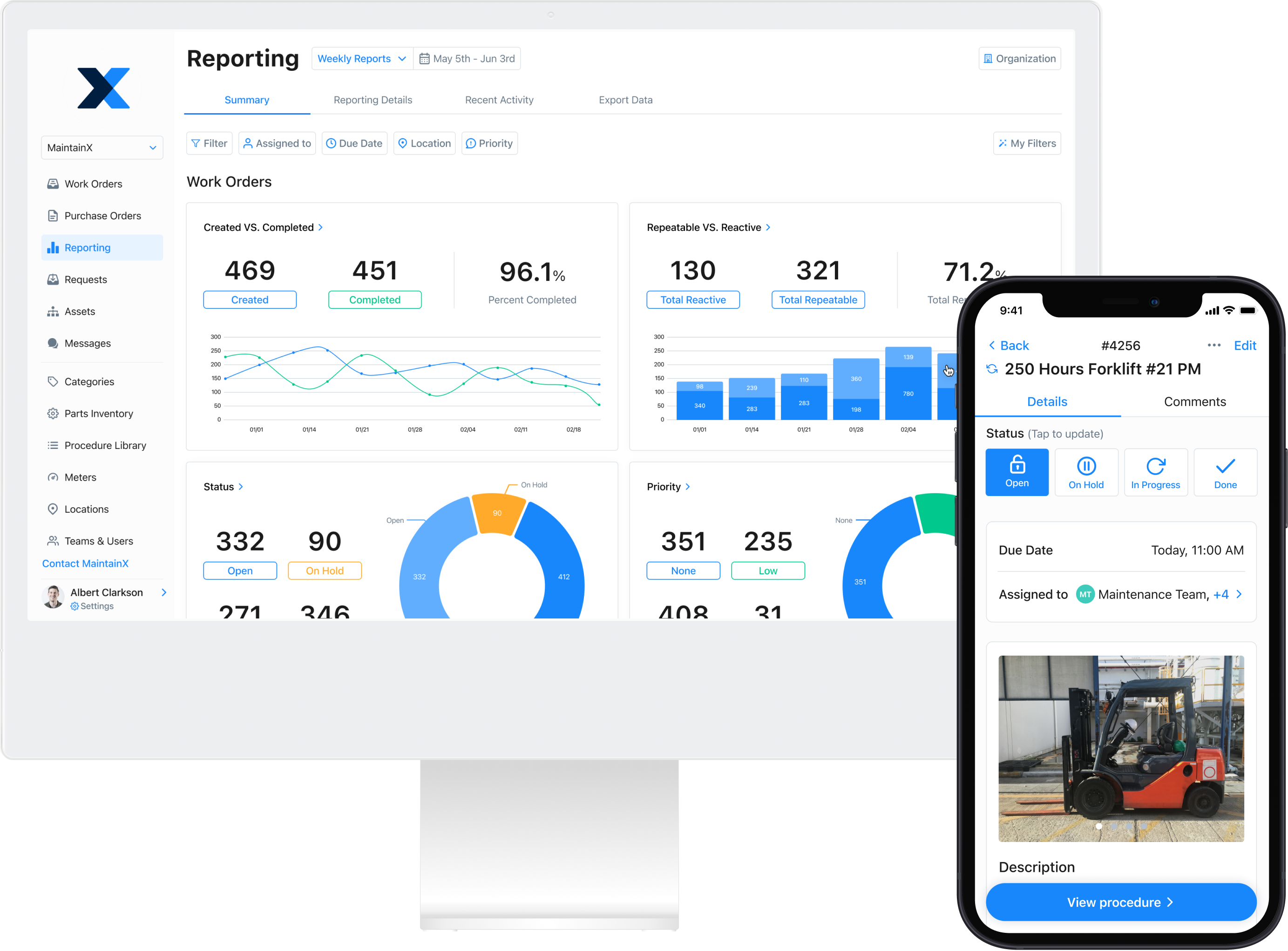
Streamline Maintenance Management with MaintainX
Leading a maintenance team, especially a large one, is a daunting job. Feelings of overwhelm can occur without the right tools, strategies, and team members in place.
MaintainX helps maintenance managers build, run, and improve world-class maintenance departments. Our CMMS automates PM scheduling, inventory management, asset management, and meter management for streamlined departmental oversight.
Get started by creating customizable work order templates for your maintenance operations today. Work orders, asset entries, and team messages are always free!
FAQs
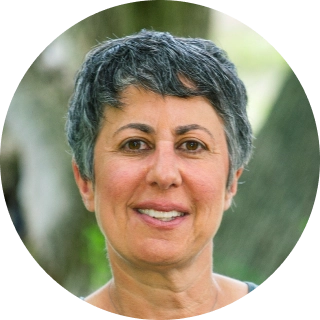
Caroline Eisner is a writer and editor with experience across the profit and nonprofit sectors, government, education, and financial organizations. She has held leadership positions in K16 institutions and has led large-scale digital projects, interactive websites, and a business writing consultancy.