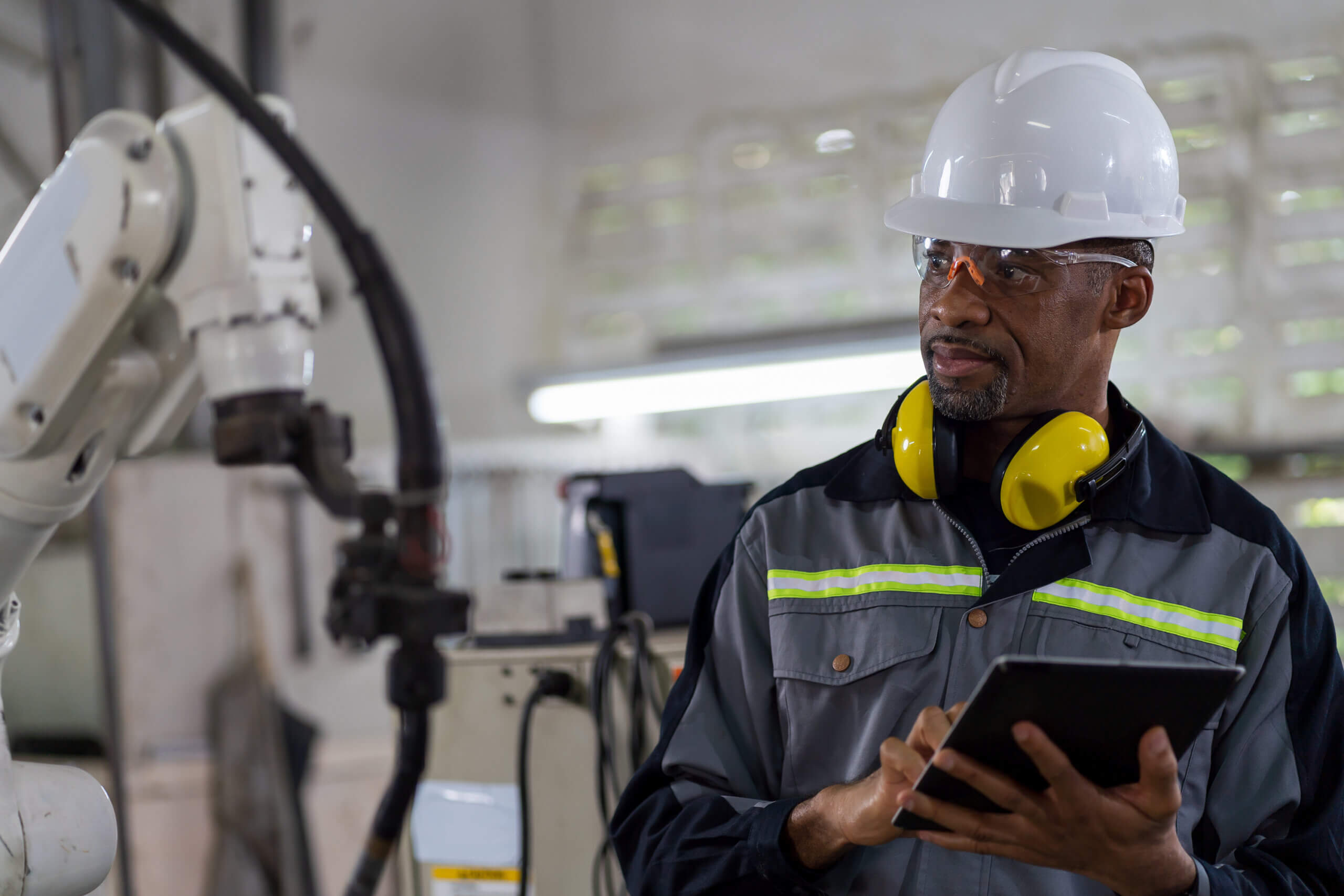
Eventually, every organization reaches a tipping point when investing in work order software becomes more than a luxury. Growing companies can only track maintenance information on paper, whiteboards, and spreadsheets for so long.
Streamlined operations (and workplace sanity) depend on the consistent execution of the following factors:
- Detailed asset tracking
- Recurring scheduling
- Resource management
- Clear communication
A good work order software program simplifies these objectives while providing managers with more time to streamline work order processes. Are you considering mobile device compatibility across Android and iOS with work order software? Conduct a quick Internet search, and you will find dozens of options to choose from. However, most computerized maintenance management software won’t be the right fit for your company or maintenance department.
In this quick guide, we’ll run through everything you need to know before making an informed purchase decision.
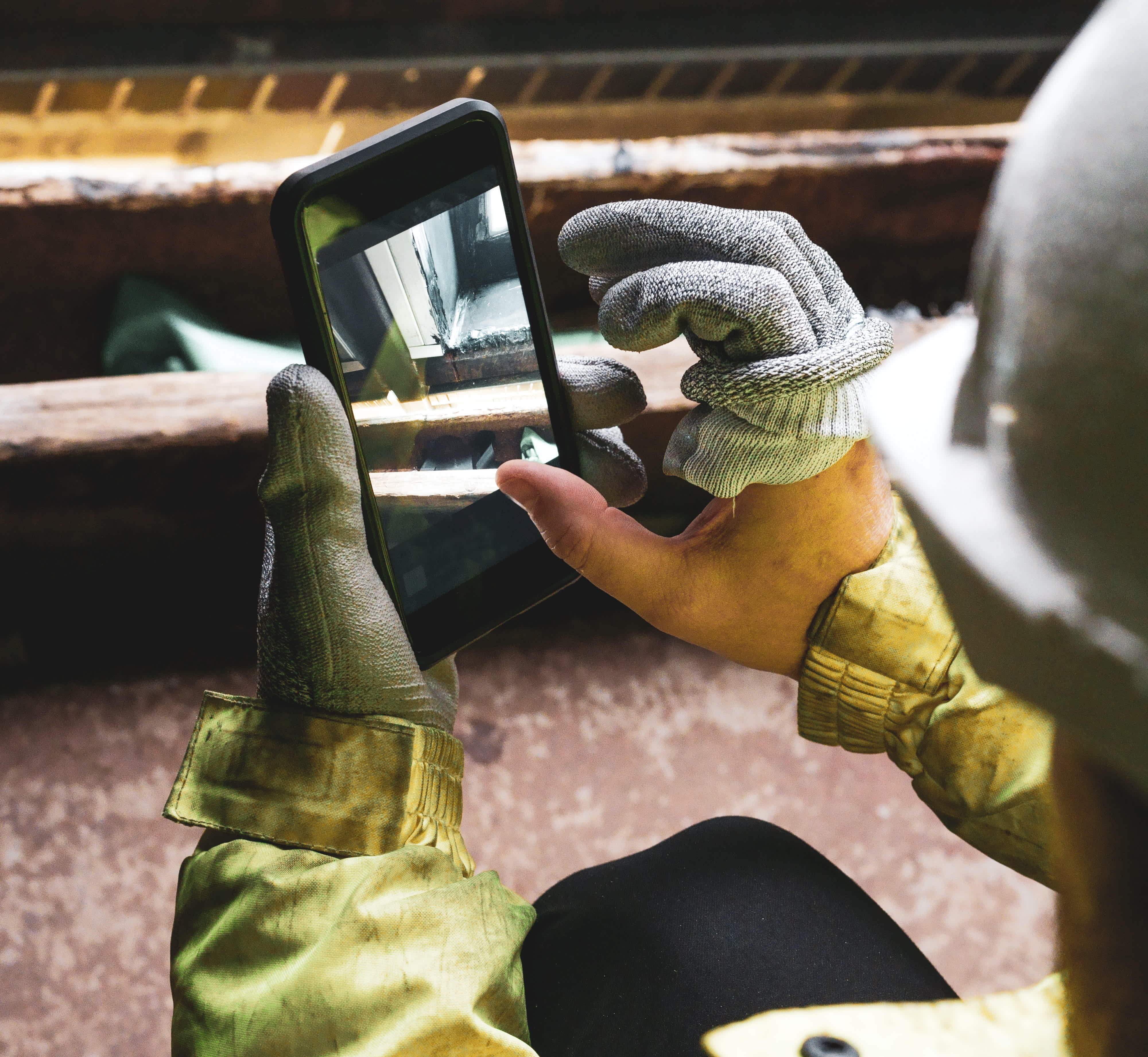
1. What Is Work Order Software?
Also referred to as a Computerized Maintenance Management System (CMMS), work order software is designed to manage maintenance-related data. In the hands of managers, these metrics can be used to increase team and department efficiency, manage work orders, reduce equipment downtime, and decrease costs.
Essentially, work order management systems are all about maintenance strategy. According to McKinsey, the strength of an organization’s maintenance strategy is the most reliable indicator of high performance. Efficient maintenance processes enable successful organizational planning and improved KPIs.
The primary function of work order management software is the automation of recurring preventive maintenance (PM) work orders. Not only do these reminders provide maintenance technicians with helpful instructions, but they also encourage greater organizational transparency. Operational managers can quickly check their CMMS software platforms to determine who completed what task and when.
Additionally, CMMS data can be used when submitting requests and verifying regulatory compliance. Today’s work order apps boast a wide range of capabilities beyond simple work order management.
2. What Does Work Order Software Include?
Most work order software programs’ functionality includes:
- Equipment data management
- Preventive maintenance
- Predictive maintenance
- Work order requests
- Task prioritization
- Vendor management
- Work Requests
- Inventory control
- Asset tracking
- Budgeting
Specialized work order packages also may include features like advanced reporting analytics, email notifications, service requests, inventory management, invoicing, collaborative workflow (chat), meter-based maintenance, photo uploading, and purchase orders.
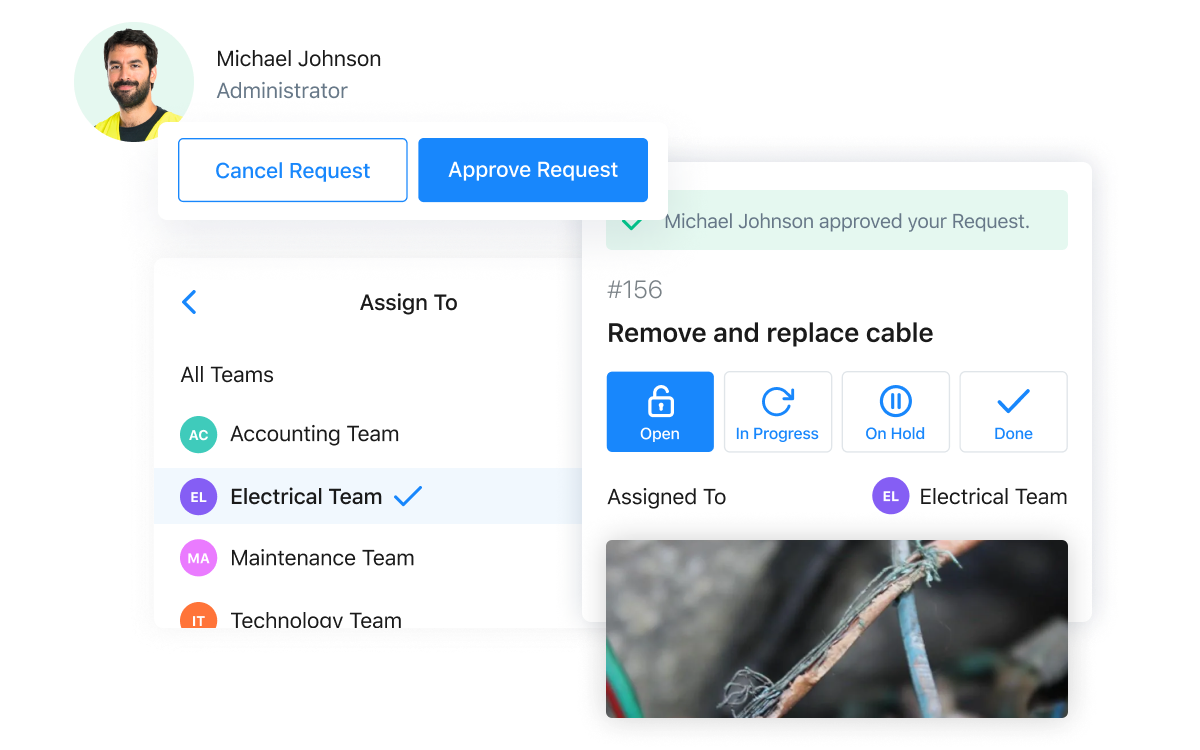
3. How Does It Work?
Most work order software platforms include four primary elements:
- Operator Interface
- Reporting Dashboards
- Administrative Tools
- Databases
Operator interfaces are screens that allow users to navigate features for recording equipment information, entering maintenance tasks, assigning work orders, and tracking asset history. Users can submit maintenance requests and receive notifications when the work is completed. Work order creation and building maintenance schedules should be easy for maintenance managers.
The information input into the work order software is then formulated into reporting dashboards to allow managers to identify opportunities for increased efficiency. For example, you might choose to generate a work order report comparing the time and cost spent repairing an asset in 2022 versus 2023 to make capital purchasing decisions.
Additionally, CMMS users can configure the software to meet their specific needs via administrative settings. Most packages can be customized with features like user settings, work order templates, and search filter specifications. Finally, most modern work order software packages include unlimited database options due to cloud storage.
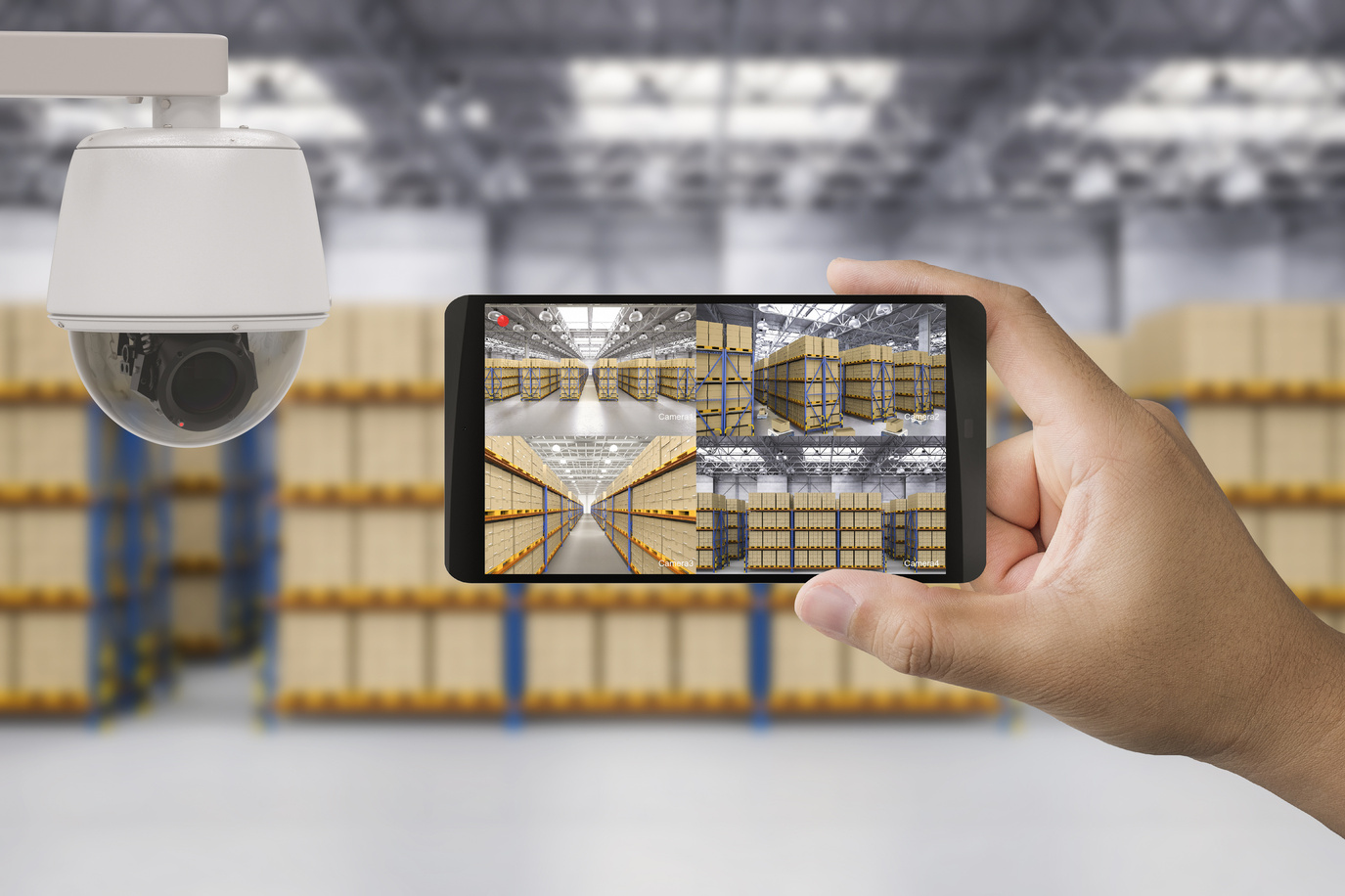
4. How Much Does Work Order Software Cost?
In recent years, work order software has become significantly more affordable thanks to newer Software as a Service (SaaS) providers. Nonetheless, the cost of programs can vary significantly depending on factors like user numbers, specialized features, deployment selection, and individual vendors. Pricing plans typically fall into one of three categories:
1. Monthly Subscription Plan by User Numbers
This option is ideal for smaller organizations with fewer users. Accounts are charged on a sliding scale according to the number of team members who use the work order software per month. Because the CMMS database is stored in the cloud, organizations can add and subtract users on the fly.
MaintainX offers a freemium starter plan with basic features and a $10 per-user, small-business plan with more premium features. Top-end subscription plans in this category can cost as much as $115 per user. Organizations can often secure monthly discounts by committing to annual subscription plans in advance.
2. Subscription Plan by Month Only
Larger organizations with more team members may benefit from a flat, monthly subscription. In this instance, the vendor typically specifies a maximum number of work order software users in exchange for a fixed fee.
Price ranges can vary quite a bit depending on factors like the number of sites, number of users, and feature specifications. Expect to pay a few hundred dollars per month for a flat subscription plan.
3. Perpetual Licensing Fees
Finally, organizations that require work order software customizations might explore procuring a “perpetual license.” This means the company pays a higher fee upfront in exchange for unlimited CMMS access. Perpetual licensing requires a sizable upfront investment, usually costing thousands of dollars. While perpetual license deals are feature-rich, they don’t always include future software upgrades.
To give you a sense of how pricing can work, check out MaintainX’s pricing model.
At this point, you probably have a fair idea as to which pricing plan is right for your organization. Let’s go a step further and calculate the potential Return on Investment (ROI) on using a CMMS.
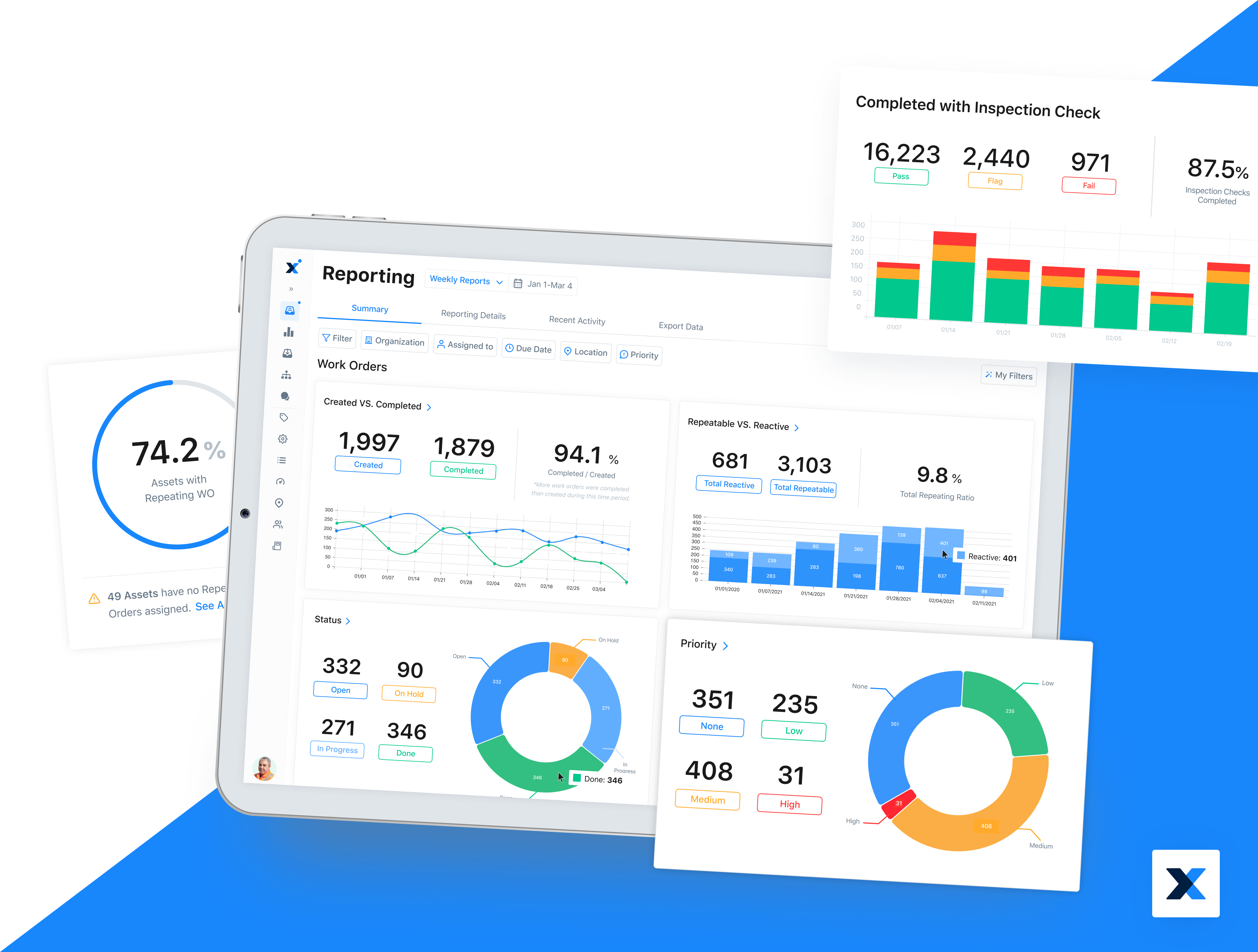
5. How to Calculate CMMS Return on Investment (ROI)
The key to obtaining an accurate calculation is having maintained accurate historical maintenance data. Understandably, not every organization has such information at their fingertips. In fact, the need for better asset management may be one of your motivating factors in finding the best work order software right now!
Understandably, many executives make CMMS purchase decisions based on initial sticker prices. Calculating an ROI on something like preventive maintenance may seem difficult, if not impossible. With so many unknown equipment variables, can you ever estimate how much a CMMS might save with a foolproof preventive maintenance program? The answer is yes. You absolutely can make an educated savings projection using a simple ROI model:
CMMS ROI = (CMMS Value – CMMS Cost)
Generally, CMMS ROI is calculated based on one-year, three-year, or five-year intervals. The longer the interval, the higher the ROI calculation you will obtain. Your CMMS Value is your expected reduction in maintenance costs as a result of implementing a CMMS system. CMMS Value is calculated based on unnecessary costs associated with five categories: Asset Life, Downtime, Inventory, Labor, and Utilities.
Calculating ROI Variables
1. Asset Lifecycle
Work order software generates preventive maintenance PM tasks, which makes it easier to follow manufacturer guidelines. If you’re still relying on spreadsheets or, even worse, paper stacks, chances are you have some PM cost savings opportunities. To calculate asset lifecycle:
- Estimate the number of years the manufacturer expects asset life extension by executing preventive maintenance.
- Translate the longevity improvement into a dollar amount by comparing it against the purchase price of a brand-new asset.
- Repeat the process for every organizational asset.
- Add your assets’ potential savings for a longevity grand total.
2. Downtime
Another major way work order software helps organizations save is through the reduction of asset downtime. Depending on the industry, downtime can have significant effects on revenue. Manufacturing organizations can lose money to scrap, facility managers lose clientele due to access interruptions, and regulated industries may suffer from poor compliance. To calculate downtime:
- Determine how much unscheduled downtime occurs per year.
- Compare daily, weekly, and monthly revenue reports to determine how asset downtime impacted revenue.
- Calculate a total downtime loss for your chosen ROI parameter (e.g., one year, three years, or five years).
3. Parts/Inventory
Every manager understands the challenge of either being understocked or overstocked at any given time. Understocked parts result in rescheduled work orders and wasted time. Conversely, overstocked parts waste capital that could be better utilized elsewhere. To calculate parts/inventory value:
- Estimate how much time your organization has lost because of emergency purchase orders.
- Estimate how much overstock inventory has cost your organization in terms of carrying costs and obsolete parts.
- Add the numbers for a total parts/inventory value.
4. Labor
Work order software also helps managers more accurately forecast both employee and contractor work hours. It’s important to examine how many labor hours per week are wasted on work order rescheduling due to inefficient work order management. To calculate labor amount:
- Determine the average hourly labor amount wasted.
- Estimate how much your organization spends on overtime hours and contract labor on average that could be avoided.
5. Utilities
Finally, many maintained assets require fewer gas, electricity, and water utilities. For example, air conditioning units that receive preventive maintenance perform more efficiently and fail less often. To calculate utility value:
- Gather your annual utility costs.
- Compare the amount with the expected yearly costs assuming your assets are operating at peak levels of efficiency.
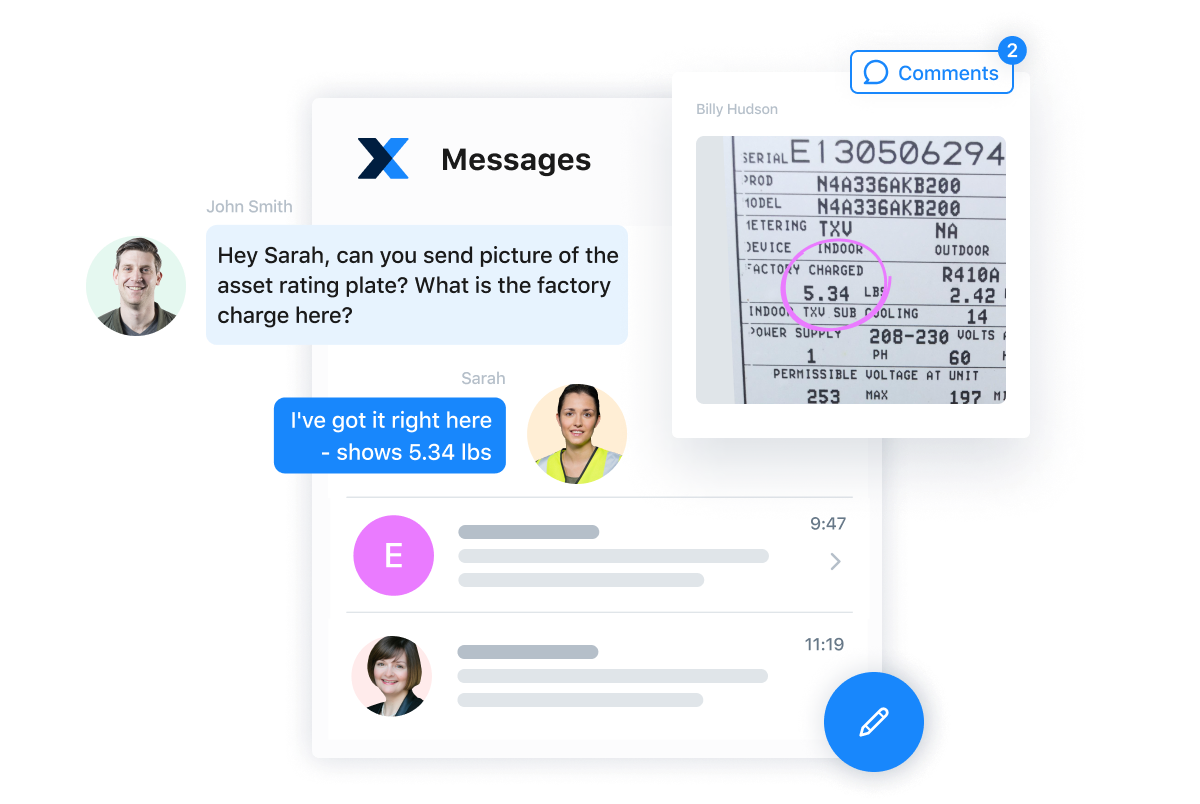
Work Order Software Costs
Once you’re finished calculating your estimated value totals–for Asset Life, Downtime, Parts/Inventory, Labor, and Utilities–evaluate projected work order software costs.
Though more modern platforms, like MaintainX, require zero to little training, many legacy programs require paid training for mastery. It’s important to consider all potential fees and costs when arriving at your total CMMS Cost. When you’re ready, plug your numbers into the formula.
Congratulations! You now have a verifiable ROI projection to present when making the case for work order software! It’s no secret that executives respond to facts, figures, and numbers. Assuming you accurately gathered your information, your leadership team will, most likely, embrace the purchasing decision with open arms.
Companies with updated CMMS solutions experience first-year ROIs of anywhere from 25 to 300 percent on average. Efficient maintenance systems also create positive chain reactions in improved customer satisfaction, less customer turnover, and greater employee accountability. Work order software is a win-win for all.
6. The History of Work Order Software
Have you ever wondered how work order tracking evolved into the smartphone apps you see today?
1960s
It may surprise you to learn the foundations of modern work order software goes back to the early 1960s. The world’s first CMMS solutions were developed by large manufacturing firms on gigantic computers.
Looking for new ways to increase efficiency, manufacturers employed computer scientists to develop systems to document, standardize, and verify their manufacturing processes.
Written in programming languages Fortran and Cobol, the first work order software programs interpreted work order cards via IBM computers. Workers input work-order data into punch cards before feeding them into computers via card readers. The system helped field technicians remember to perform simple recurring tasks, like oil changes and other preventative maintenance.
1970s
Over the next decade, manufacturers went a step further. They began printing work orders on paper and manually distributing them to team members. At the end of the day, the technicians would hand off their paperwork orders to data-entry clerks. The clerks would then input the information into mainframe computers.
Interestingly, not much has changed for many modern maintenance teams. According to the Plant Engineering Maintenance Study, 39 percent of organizations still rely on paperwork orders, and 52 percent still rely on in-house spreadsheets.
The 1980s
During the next decade, the “mini-computer” sought to even the playing field. The smaller computer made work order software available to medium-sized businesses for the first time. However, the programs themselves were still quite clunky.
The 1990s
It wasn’t until the 1990s and the emergence of the personal computer that organizations began custom-building work order software programs. Most of these interfaces ran on one server and required Microsoft Access on each terminal.
Unfortunately, these early CMMS solutions lacked many of the capabilities world-class maintenance organizations rely on today. Work order history, cost tracking, and data interrelationships weren’t previously available. And everything was still being printed on paper!
The 2000s
Eventually, CMMS vendors moved from Microsoft Access-based applications to browser-based systems. Using work order software from Internet Explorer was more convenient, but these programs still mimicked the terminal interfaces of old-school, mainframe computers. Furthermore, the work order software still ran on local servers. This required software users to perform local upgrades, typically supervising the process while vendors ran complex and time-consuming upgrades.
Organizing on-premise upgrades required substantial client interaction. Various clients could be running different software versions at any given time, which required vendors to repeatedly fix the same issues on individual platforms. While many legacy CMMS providers still offer on-premise software, the practice is becoming increasingly obsolete due to more affordable technologies.
The 2010s
In this decade, vendors began to develop convenient web-hosted applications. The technology allowed users to access for the first time work order software from anywhere with an Internet connection. Technicians could now access digital work orders from laptops, tablets, and smartphones! This unlocked the ability for field service management to automate and manage upkeep from a distance.
Now
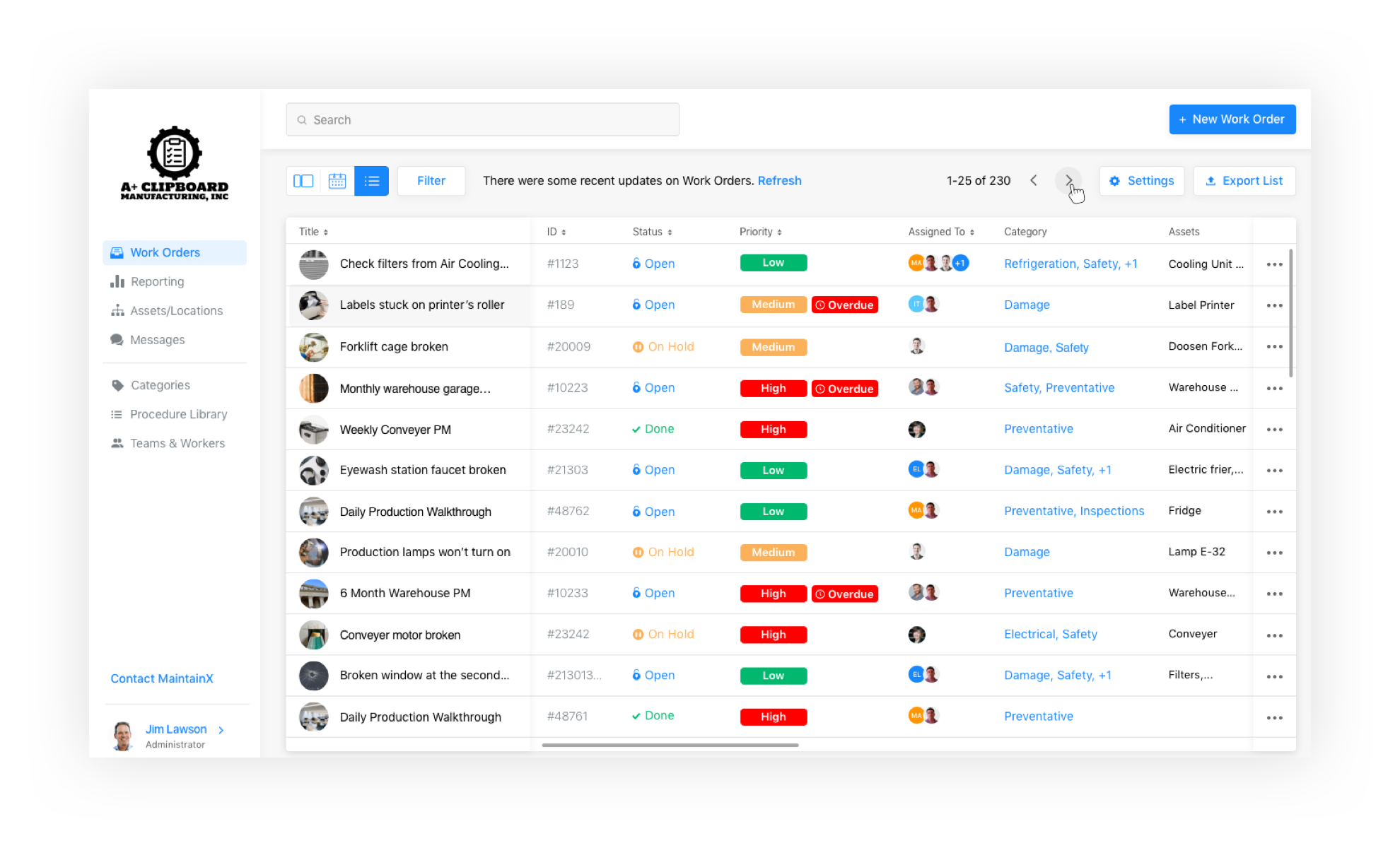
Today’s best work order software solutions are run on a cloud-based architecture, designed with convenience, affordability, and security in mind. Most importantly, modern systems can be easily operated via a mobile app with mobile work orders. Cloud-based software allows organizations to sign-up, log in, and begin creating work orders immediately.
Another bonus? These modern CMMS solutions are infinitely more reliable than their predecessors. Because the programs are stored on multiple virtual servers in the cloud, organizations will never experience CMMS downtime. If one piece of hardware fails, another turns on automatically with no loss of service
Choosing the Right Work Order Software
Choosing the right work order software program can be time consuming. However, weighing your options and conducting your due diligence will be time well spent. A user-friendly and feature-rich platform will help reduce costs, increase productivity, and enhance team member compliance.
Modern CMMS solutions are available to organizations of all sizes, budgets, and industries. Regardless of the number of initial users, multi-tenant work order software can scale as your company grows with zero loss of performance.
The best work order software programs are sleek, intuitive, and affordable. With MaintainX, users don’t have to sacrifice features for simplicity. MaintainX allows users to:
- Create reactive and preventive maintenance work orders.
- Assign recurring work orders to both teams and individuals.
- Monitor progress by maintenance category, priority level, status, etc.
- Analyze maintenance costs for greater efficiency and savings.
- Hold text conversations with team members in real time.
When we say that anyone with a smartphone can download the app and get started now, we aren’t kidding. The app is that easy to use!
FAQs
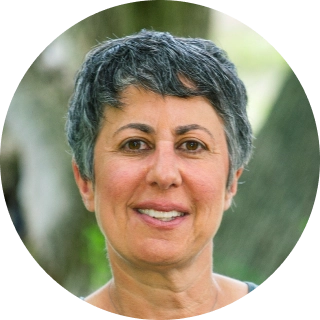
Caroline Eisner is a writer and editor with experience across the profit and nonprofit sectors, government, education, and financial organizations. She has held leadership positions in K16 institutions and has led large-scale digital projects, interactive websites, and a business writing consultancy.