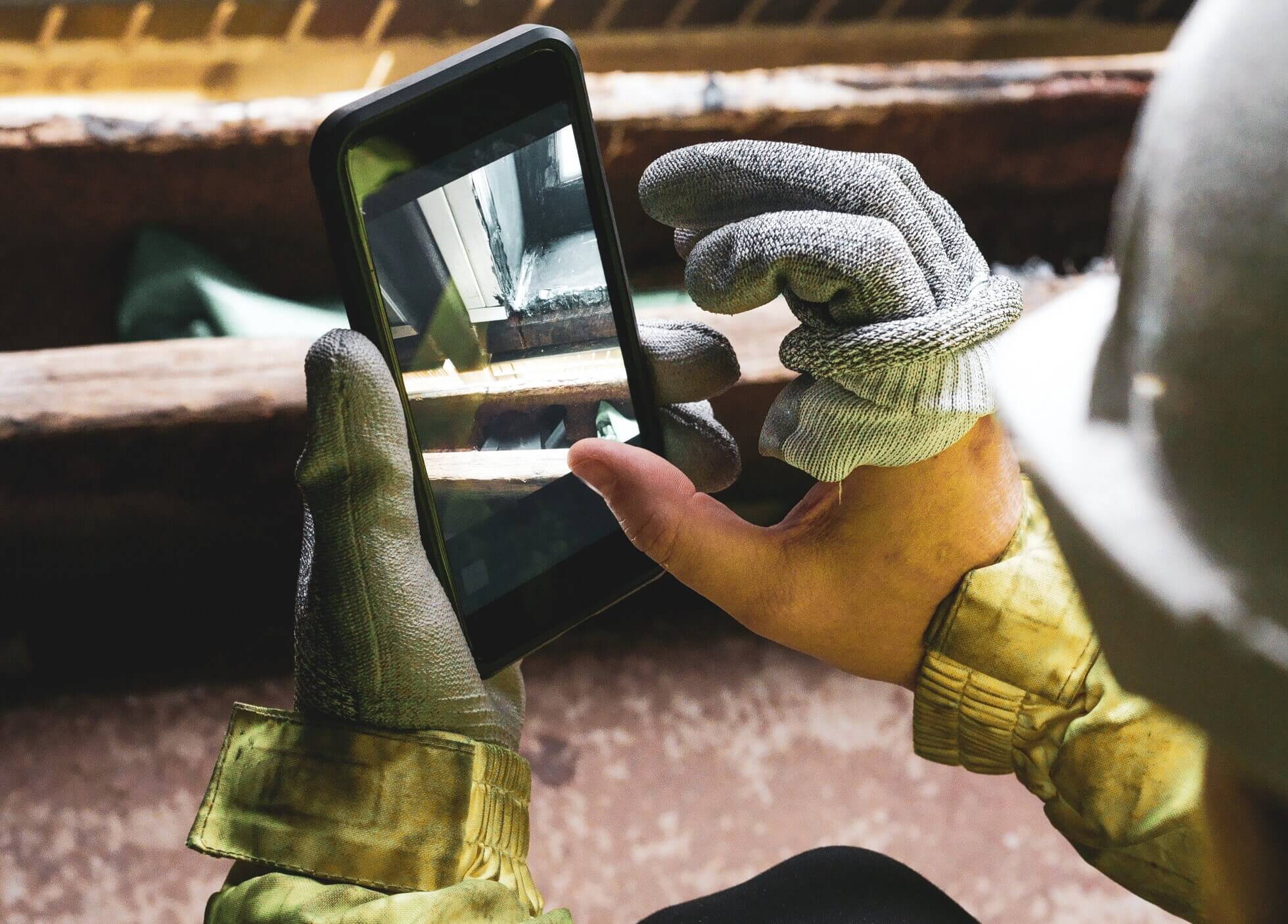
Whether the catalyst for necessary improvements is the competitive global economy, the pressure to digitize existing procedures, the role of maintenance management software has never been more important.
Each week, we speak with dozens of maintenance managers facing unprecedented operational challenges. From small- and medium-sized businesses (SMBs) to enterprise-level organizations, maintenance teams are increasingly under pressure to enhance efficiency, increase productivity, and decrease costs.
During the past two decades, advanced technologies have allowed companies to manufacture products at a stunning rate. Consequently, maintenance teams are under pressure to minimize costly equipment disruptions that halt production with minimal to no warning. In fact, the more highly automated the facility, the more important efficiently preventing, diagnosing, and solving complex asset breakdowns becomes using work order management tools.
Furthermore, studies show organizations can save an average of 12% to 18% by consistently executing preventive maintenance (PM) as part of a well-rounded, maintenance management strategy. Translation: Every dollar spent on preventive maintenance could save nearly five dollars on expenses. Unfortunately, managers, supervisors, and operators often run into several challenges when attempting to optimize maintenance programs, including the lack of process knowledge, historical data, time to complete required analyses, and top-management support.
As the title suggests, the effective use of maintenance management software can help ease these burdens. In this guide, we’ll explore the relationship between team leadership, maintenance strategies, and software. After reading, you will be more confident combining specific upkeep methods with maintenance management software.
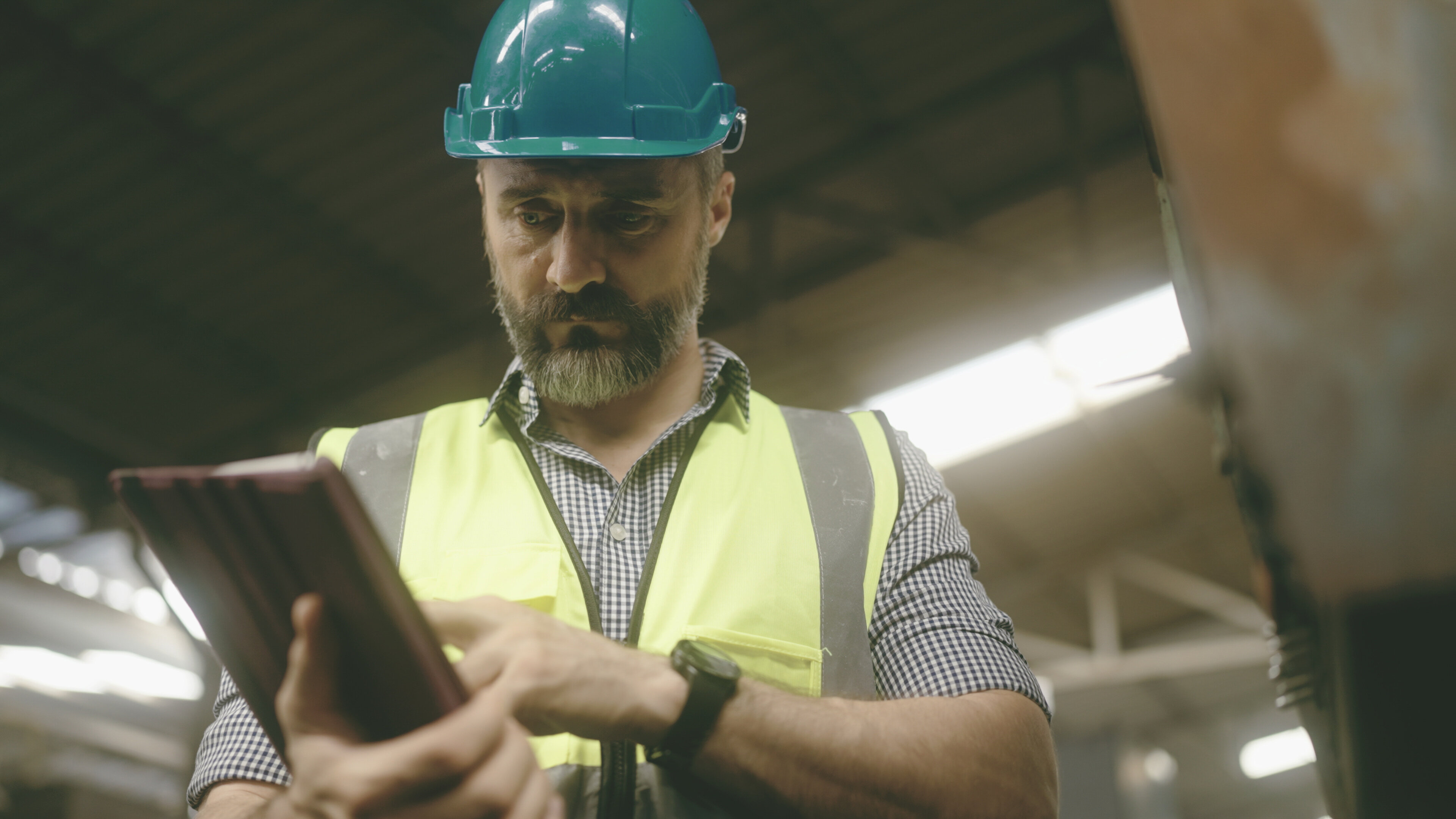
What Is Maintenance Management?
Maintenance management is defined as prioritizing, strategizing, and delegating maintenance-related objectives with the goal of maintaining company assets. Thus, it involves tracking, controlling, and maximizing equipment lifespans in order to increase profitability, increase efficiency, and reduce downtime.
Indeed, reactive and unplanned downtime negatively impacts organizations in many different ways, including unexpected repair costs (e.g., employee overtime, overpaying for spare parts, outsourced specialists), delayed shipments, customer dissatisfaction, and lost revenue.
Common Challenges
What exactly makes maintenance management so challenging? The most common maintenance management roadblocks are:
- Complexity of production process technology
- Lack of maintenance scheduling in place
- Lack of processes for Work Requests
- Low technical expertise of staff
- Lack of historical equipment data
- Lack of automation
- Lack of CMMS
- Lack of iOS or Android mobile applications
As a result. effective maintenance departments use automated software to organize both tactical and operational maintenance actions based on business priorities.
Therefore, organizational leaders must work together to identify the “critical asset targets” that most impact operational targets by conducting criticality analyses (more on that in a moment) and automating strategic maintenance workflows.
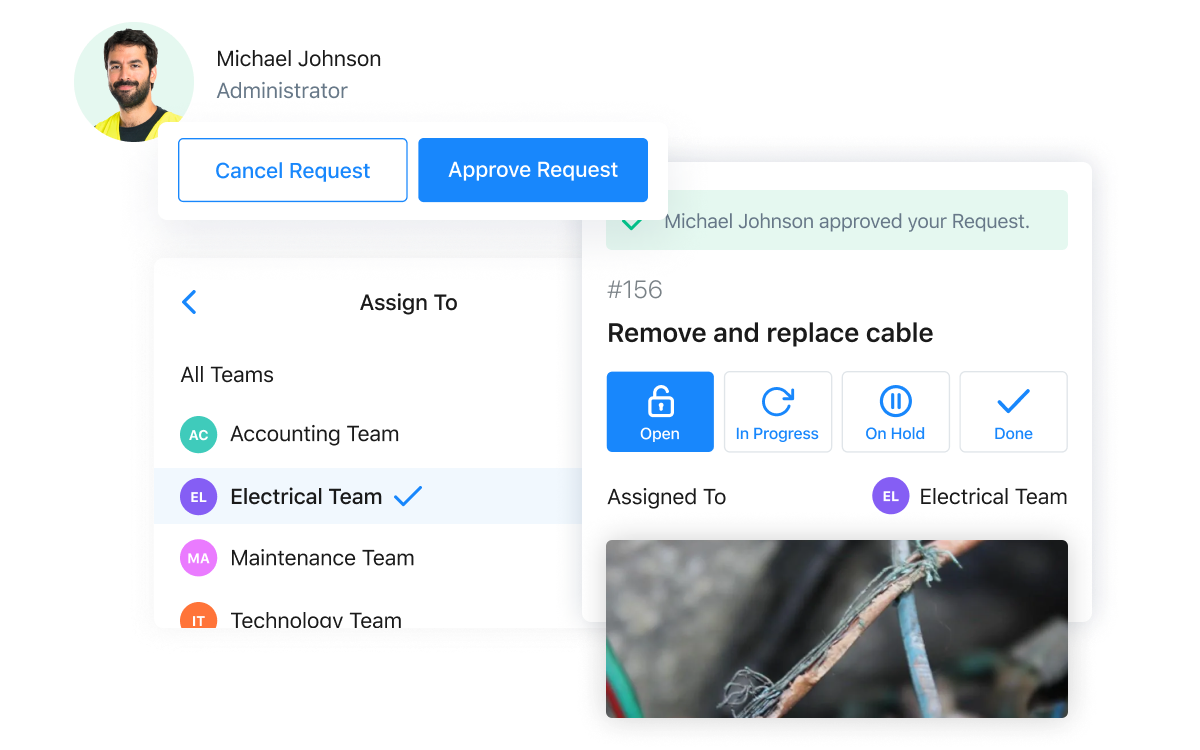
Maintenance Management vs. Enterprise Asset Management
It’s not unusual to hear the terms maintenance management and enterprise asset management (EAM) used interchangeably. However, there are key differences. Maintenance management is a holistic approach to managing facility operations. It not only covers asset and equipment maintenance, but also encompasses the overseeing of labor, parts inventory, and safety procedures.
On the other hand, asset management primarily focuses on optimizing asset performance relative to output. Asset management programs monitor equipment efficiencies and help monitor the asset lifecycle to facilitate capital decisions and provide depreciation estimates to accounting teams. While some asset management systems incorporate maintenance schedules, they are typically less focused on presenting easy-to-understand work orders. They tend to be more dependent on an administrator to manage the data entry.
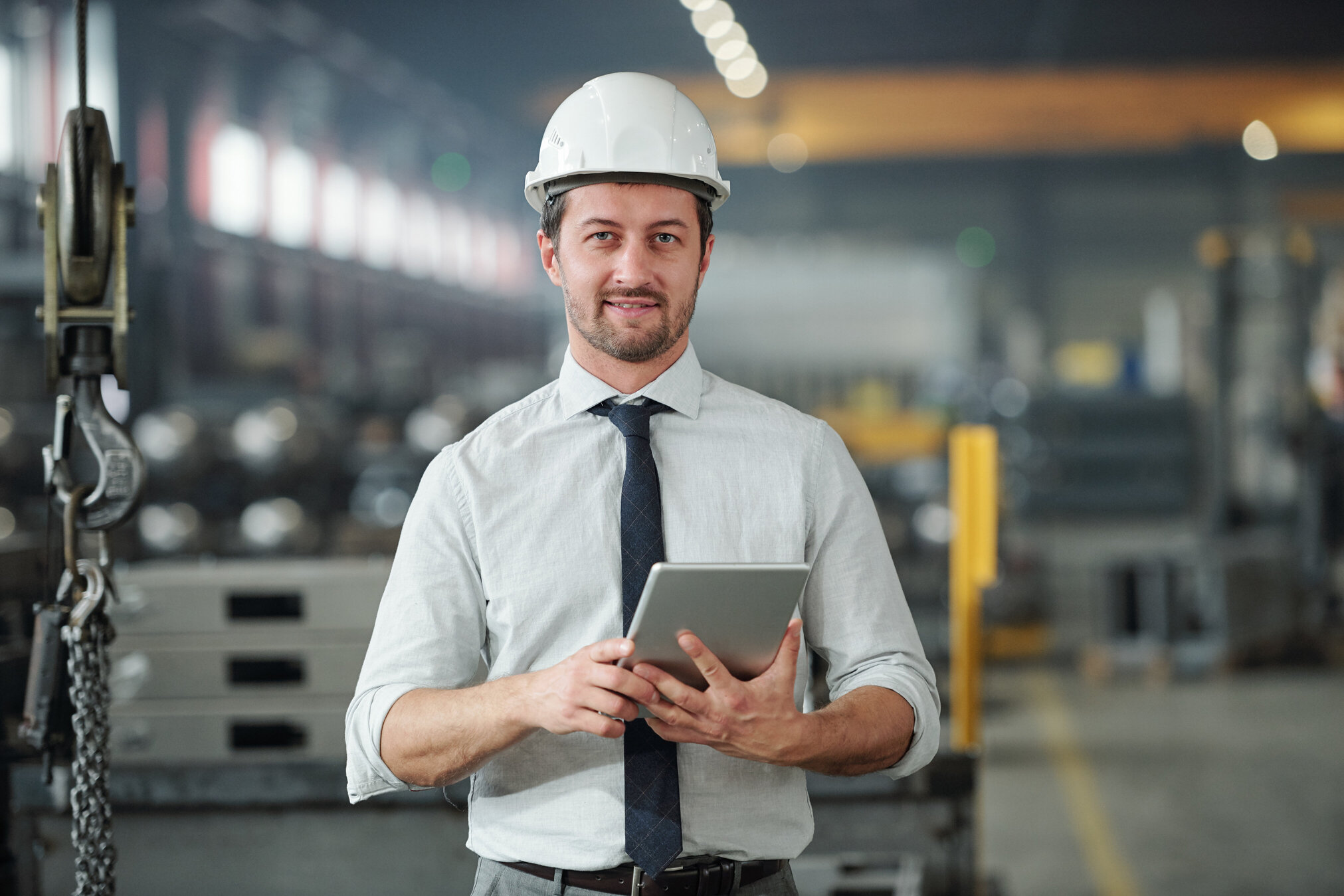
What Are the Benefits of Maintenance Management?
Budget Accurately
Well-designed maintenance management systems enable your organization to be more insightful into where your team’s resources are going.
An effective maintenance management software can identify where your team spends most of its time. This reporting can empower managers to re-prioritize their workflows or make a strong case to bring on additional help by leveraging the configurable reporting tools offered by computerized maintenance management software packages.
Schedule Work
Many organizations oversee a complex array of machinery and systems that require a well-managed preventive maintenance routine to run efficiently. Too many of these organizations depend on Excel spreadsheets or, worse, whiteboard calendars in the manager’s office, to know what needs to be done next.
Maintenance management software ensures that everyone knows what needs to be done, how to do it, and when it needs to be done. All of this comes with a digital audit trail for complete accountability.
Manage Compliance
Have you ever dealt with a surprise OSHA inspection or industry regulator inspection? If so, you have likely felt overwhelmed with the prospect of procuring appropriate documentation to prove your compliance. Maintenance management software allows you to instantly pull up that information from any connected device and produce any reports necessary to satisfy regulators.
Beyond sharing documents with regulators, maintenance management systems ensure that compliance standards are tracked and don’t fall behind on work. Digital audit trails are able to validate that the tasks were performed in a timely manner by the appropriate personnel.
Iterate and Optimize
Every organization is different, even across sites. It is unrealistic to expect that a one-size-fits-all approach will be effective for every team. Therefore, managers need to monitor the real-time data for trends that can provide actionable insights toward improvement.
Your most expensive technicians could be spending far too much time performing routine tasks that can be accomplished by less senior team members. This can result in bottlenecks of more technical maintenance tasks.
Improve Safety
In an ideal world, you could sit your team through a safety video on their first day of work, and they would execute flawlessly going forward. We all know that is unrealistic. Beyond asset optimization and time management efficiencies, maintenance management software can provide timely reminders to follow safety guidelines when performing assigned tasks.
Not every assigned task is something your team members routinely perform. Having safety instructions available on their mobile devices at their fingertips can save lives and money.
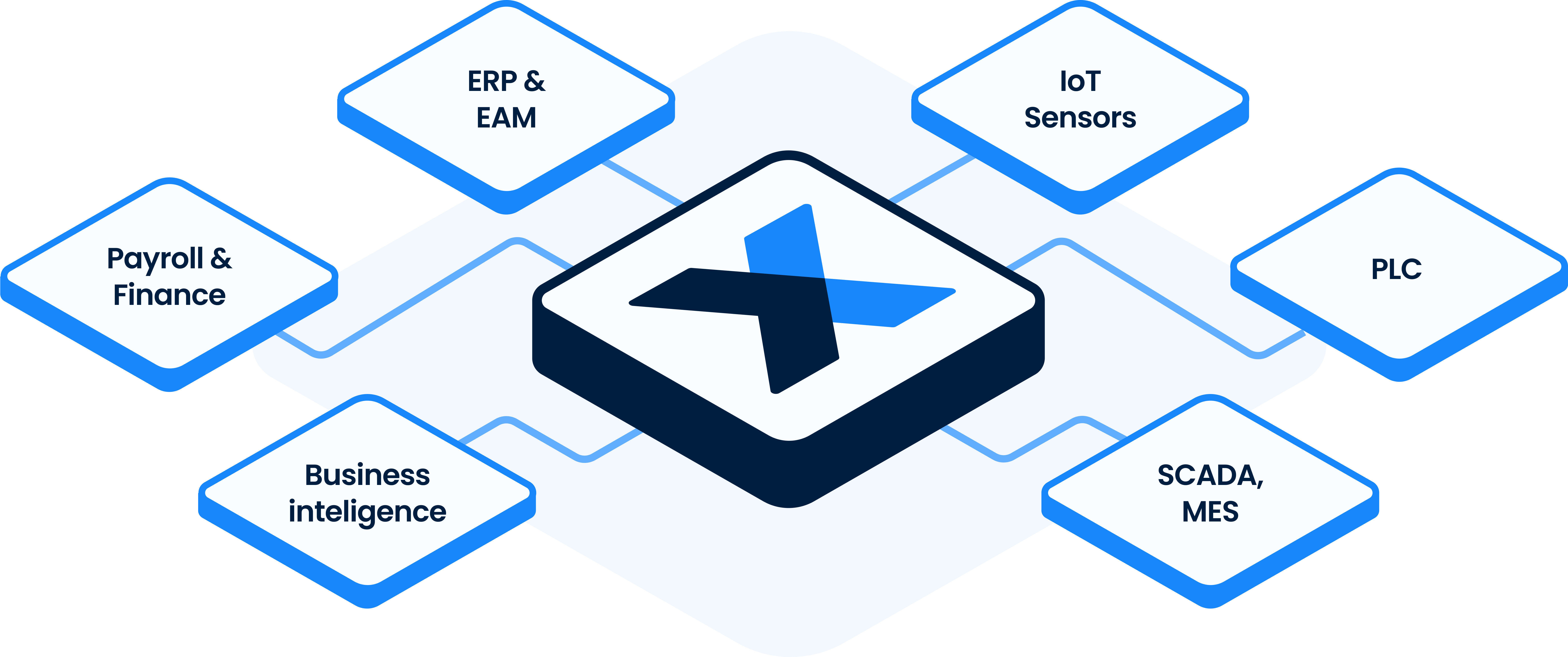
What Is Maintenance Management Software?
Monitoring dozens, if not hundreds, of assets in analog format is tedious. For this reason, high-performing organizations use maintenance management software to track everything from maintenance operations to inventory management.
Often called Computerized Maintenance Management Systems (CMMS), these platforms allow management to create, assign, and track recurring work orders; catalog facility assets by location, service date, and serial number; enhance compliance with digital audit trails; identify cost-savings opportunities with advanced reporting; and support condition-based monitoring with sensor technology.
Who Uses Maintenance Management Software?
Maintenance management software is used by the following industries:
Surprisingly, 44% of organizations still rely on paper records to plan their maintenance activities, according to a Plant Engineering Study. Why isn’t everyone running PM programs with the support of maintenance management software? Unfortunately, there is a common perception that the platforms are too complicated, expensive, and time-consuming to ever be within reach. The good news is that isn’t true—anymore.
Is a CMMS Difficult to Use?
Organizations of all sizes, with workers of varying technical skill levels, can teach themselves how to use maintenance management mobile apps within minutes. Modern maintenance management software platforms run on desktops, tablets, and smartphones.
While some providers have an outstanding reputation for desktop software, very few programs have been exclusively designed and/or adapted for mobile usage. Considering that the average worker always has a smartphone in their pocket—no matter where they are—it makes sense to choose a solution that offers on-the-go functionality. In short, MaintainX is the most user-friendly and top-rated platform on the market.
To learn more about CMMS software, check out our Ultimate Guide to CMMS: Everything You Need to Know.
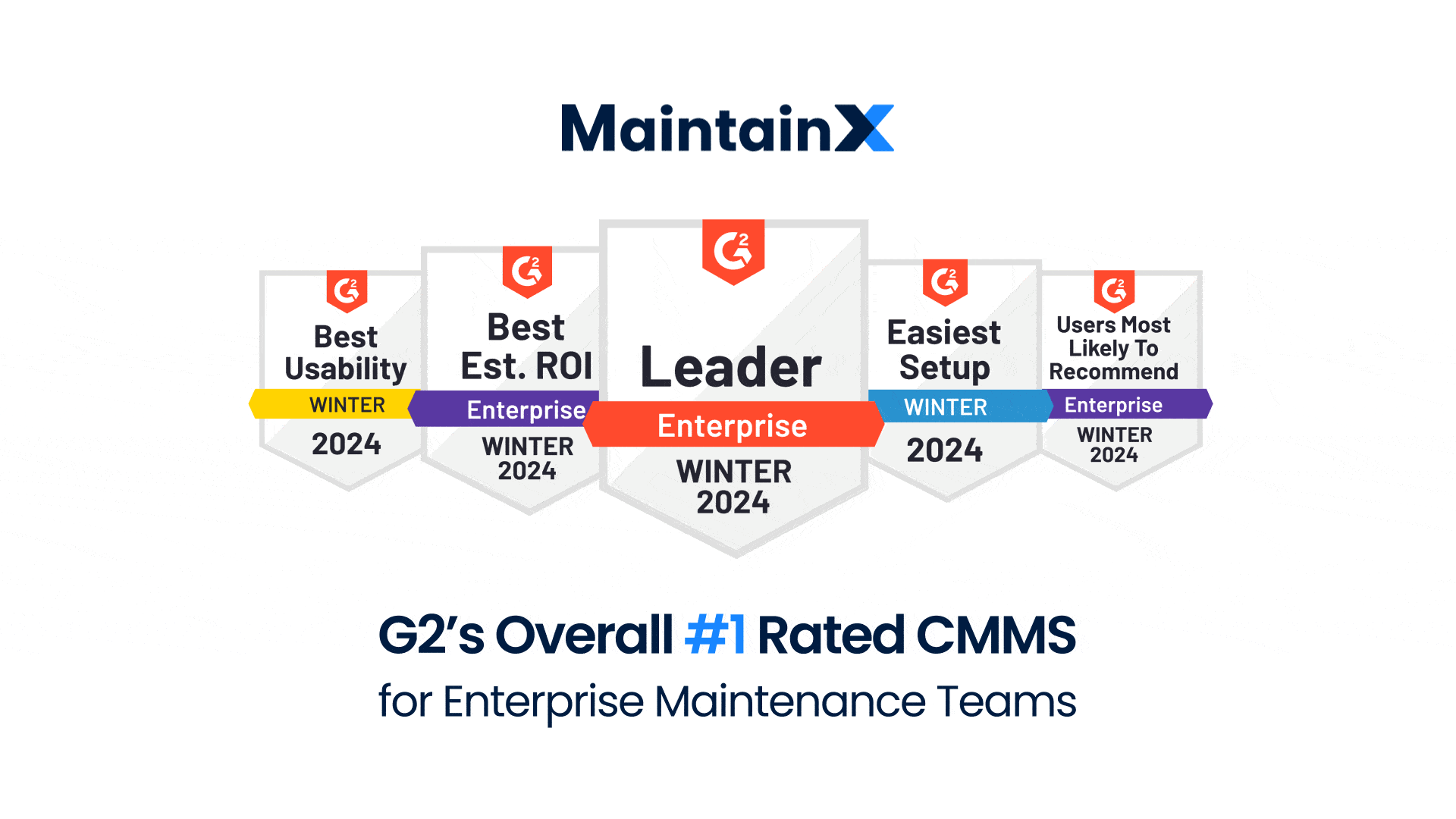
How to Choose a Maintenance Strategy
Now that you’re clear on the relationship between maintenance management and CMMS platforms, it’s time to look at maintenance strategies. Keep in mind, the best maintenance operations use a combination of strategies based on the assets they are managing.
What Is a Maintenance Strategy?
A maintenance strategy is a systematic approach that companies use to maintain their assets in prime working condition. It involves maintenance checks, data analysis—for example, of KPIs, failure rates, performance, and costs—and the repair or replacement of faulty equipment. High-level maintenance programs typically mix several different maintenance strategies based on the needs of individual equipment.
However, maintenance strategies for equipment are often adapted to meet unique needs, goals, and budgetary constraints. The optimal balance between costs and performance is, therefore, different for each company. However, in many cases, shifting from corrective to preventive maintenance can help improve the ratio between the two elements.
Choose an effective maintenance strategy in order to:
- Reduce downtime and guarantee high equipment availability
- Keep maintenance and operational costs low and predictable
- Optimize facility performance and production
- Maintain a high level of safety
- Improve customer satisfaction
- Extend equipment life
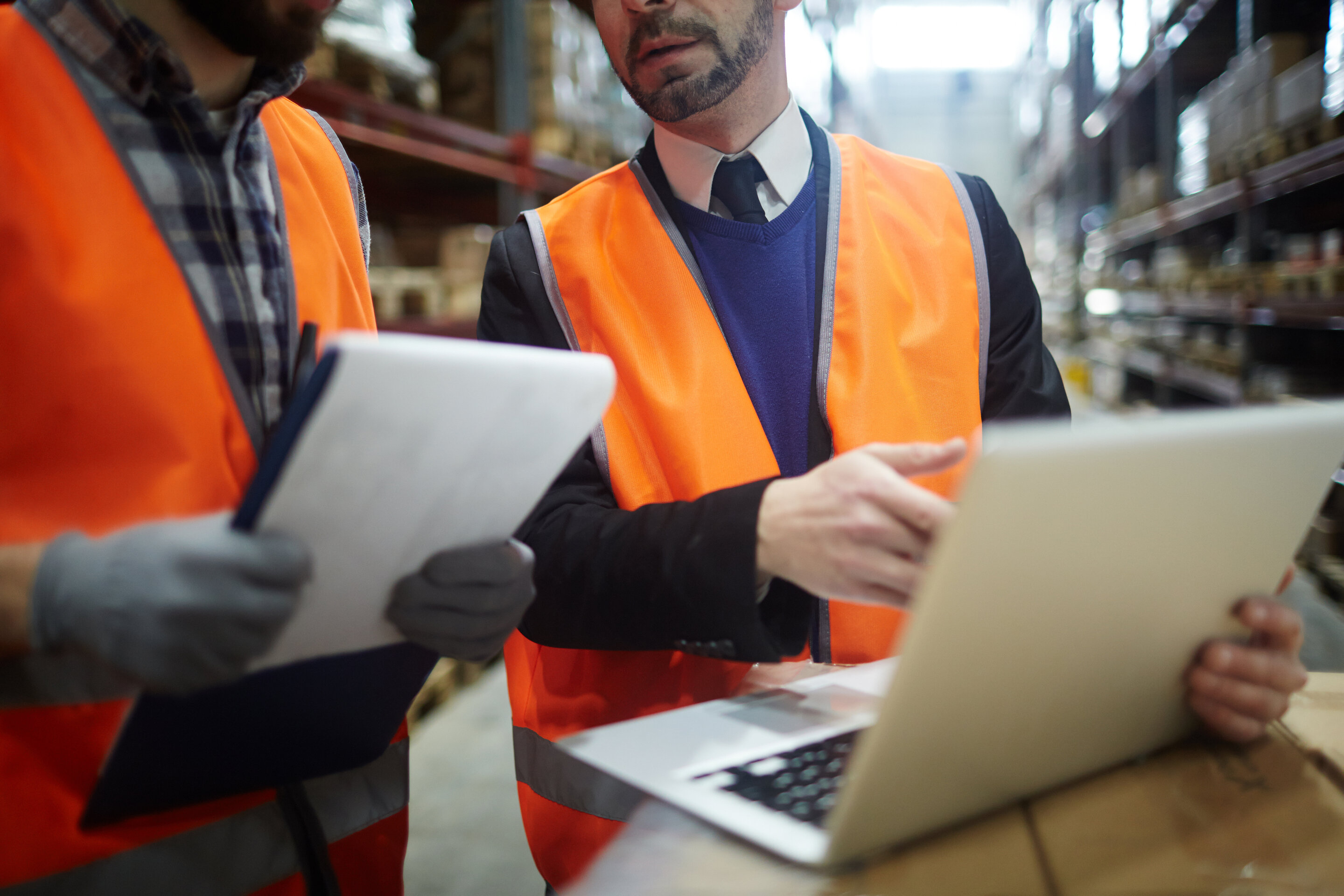
Customize Maintenance Strategies
Unfortunately, choosing the right maintenance strategy isn’t always a straightforward process. Types of equipment can vary dramatically across industries, locations, and facilities. Additionally, Return on Investment (ROI) is different for every vertical. For these reasons, a company may need to rely upon a combination of strategies for various assets within its care.
Take the mining industry, for example. In fact, 82% of mining machine failures occur at random patterns, making scheduled maintenance inefficient. For this reason, a significant number of mining organizations have invested in predictive maintenance (PdM) technologies in recent years. With PdM, modern sensors monitor machine temperature, vibration, and humidity in real-time, translating to more cost-effective maintenance actions. In this instance, studies show PdM can reduce costs by an estimated 10 to 20 percent.
However, predictive maintenance isn’t cost-effective for most facilities at this time. Being new to the market, sensor technology is still quite expensive. Thus, the majority of organizations benefit from balancing reactive and proactive maintenance strategies with the help of maintenance management software. For example, a facility might use run-to-failure maintenance on easily replaced light bulbs but practice preventive maintenance on $10,000 forklifts.
In the next section, we’ll walk through the step-by-step process of assessing values vs. costs and choosing the best maintenance strategies for your facility.
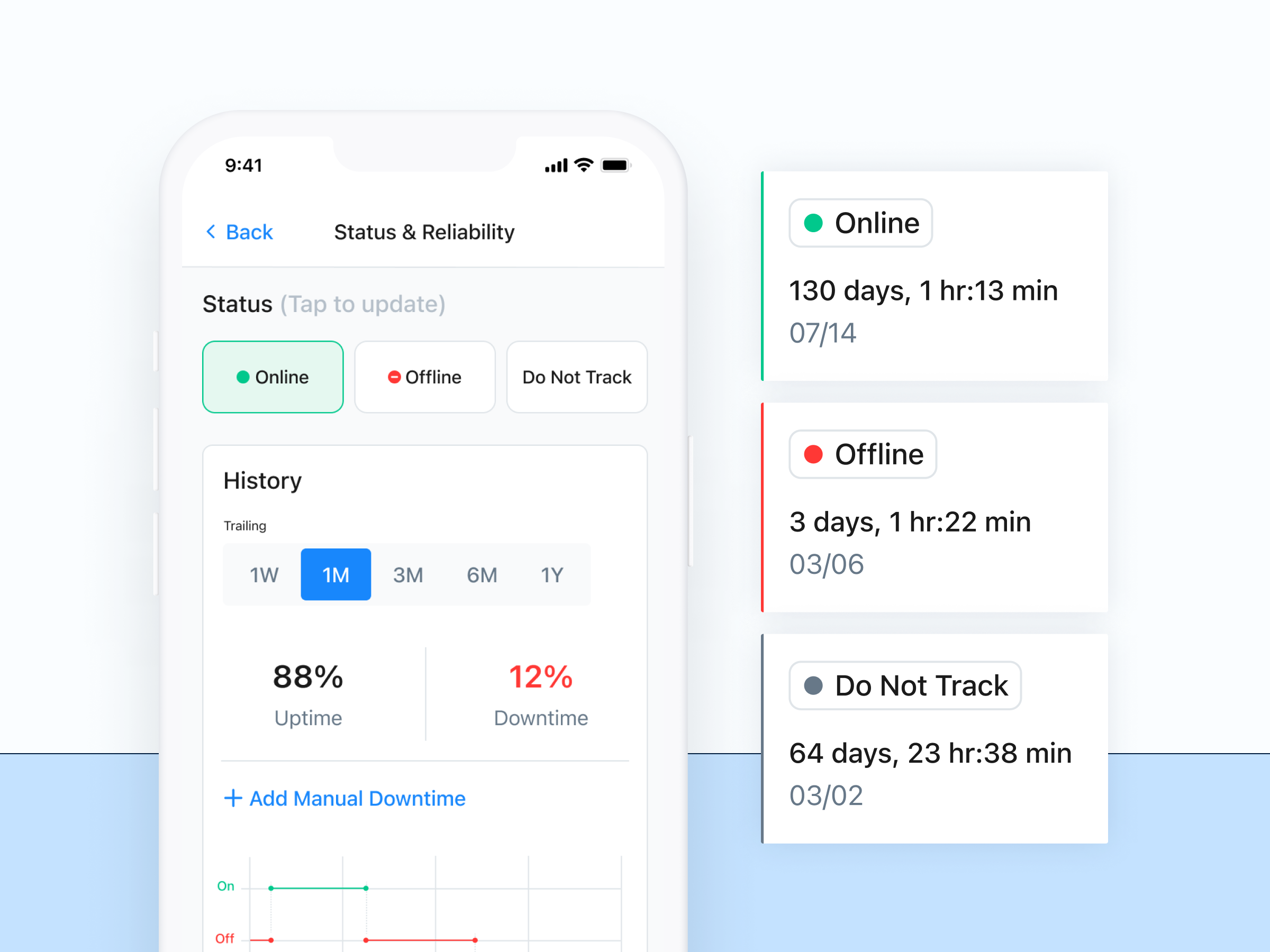
How to Build Your Ideal Maintenance Strategy
Choosing a maintenance strategy is best approached as a two-level process:
- The Maintenance Strategy for Your Entire Facility: Your global maintenance strategy is characterized by the ratio of reactive to proactive maintenance, as well as by the specific approaches you’re using.
- The Maintenance Method You Use for Each Individual Asset: Each asset is different and requires a maintenance approach that’s adapted to its criticality, cost, and the consequences of its eventual breakdown.
Therefore, it’s necessary to create an overarching maintenance strategy for your organization, as well as individual plans for different pieces of equipment. Analyze where you stand in terms of reactive vs. proactive maintenance, knowing that: a) proactive maintenance happens before a breakdown occurs and b) reactive maintenance happens after a breakdown has occurred. We can divide these two main types of maintenance further into specific maintenance approaches (more on that in a moment). When deciding on the right maintenance strategy for a given asset, both the value of equipment and the cost of failure should be considered, as related to:
- The costs of repairing or replacing equipment.
- The financial losses associated with downtime.
Note: It’s important not to try to alter existing maintenance strategies more than you’re ready to handle at the moment. If, at any time, your team struggles to keep up with procedural changes, that’s a red flag to step back and reevaluate your approach.
1. Assess Where Your Organization Stands Overall
Asset tracking should vary based on the type of equipment and how critical it is to your operational success. A lightbulb in the supply closet doesn’t need the same level of attention as a critical piece of equipment on your production line.
Operations and Maintenance managers need to identify and align on actionable KPIs:
- What percentage of maintenance is reactive to proactive?
- What is the ideal ratio of reactive to preventive maintenance?
- Are you using a CMMS platform? Is it working for you?
- What’s your biggest challenge right now as a team?
To choose the right maintenance strategy, you will need to assess existing organizational data, such as asset performance/criticality, uptime/availability, maintenance costs, and failure rates. Once you’ve obtained “the big picture” of your organization’s current maintenance and operational structure, we recommend reviewing the types of maintenance strategies before conducting FMEA and/or a criticality analysis.
2. Understand the Types of Maintenance Strategies
Corrective (Reactive) Maintenance
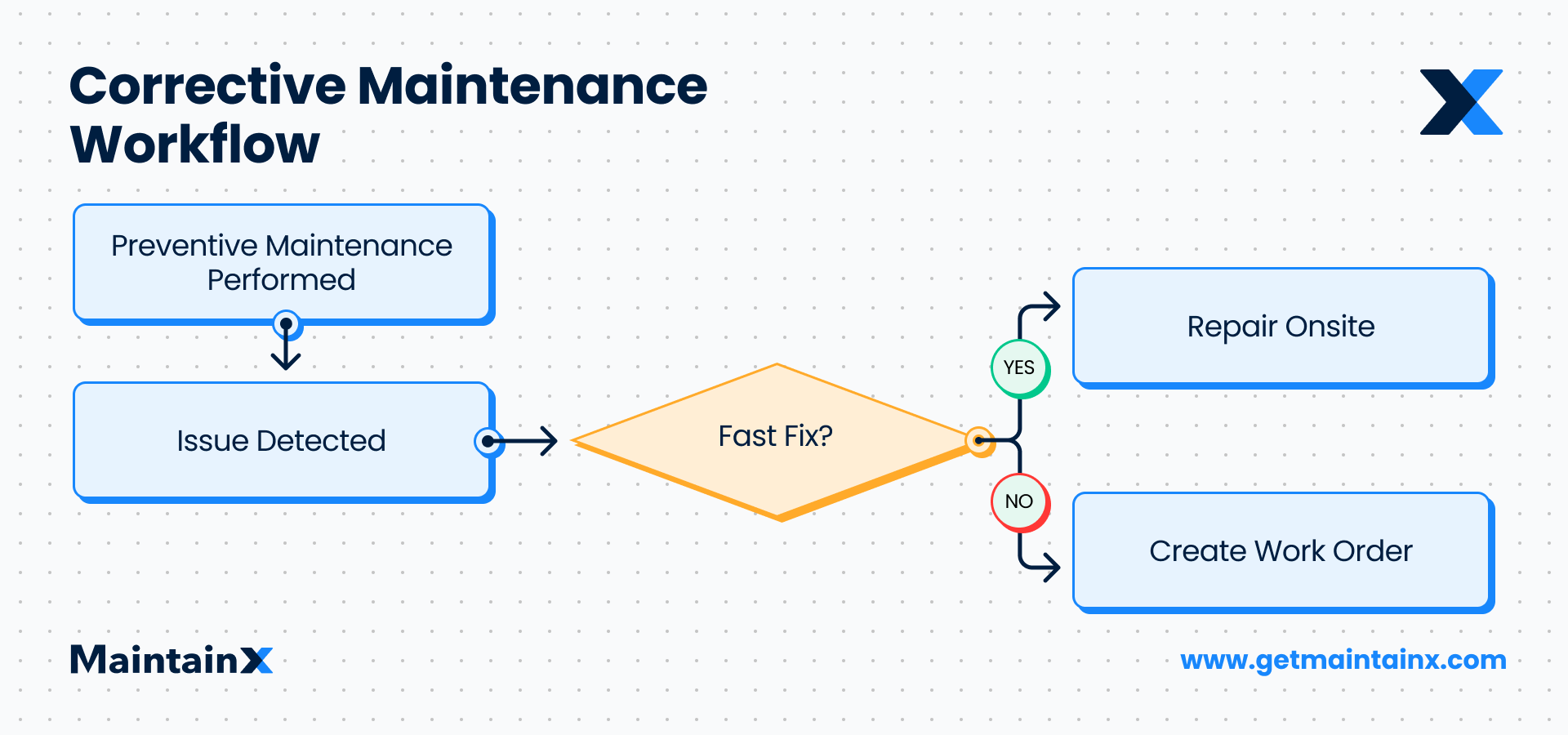
Corrective maintenance can take the form of either planned run-to-failure maintenance, unplanned run-to-failure maintenance, or breakdown maintenance. In its unplanned state, corrective maintenance is erratic in nature, with the intention of finding, isolating, and fixing a fault. Reactive maintenance requires fixing a defect that caused a malfunction of the equipment, e.g., a shutdown of the production line. For example, reactive maintenance activities will get the piece of equipment going again, but it does not guarantee that it will work optimally or sustainably.
Corrective maintenance means repairing a fault that has been found but is not (yet) causing the machine to run out of appropriate ranges. A good example of this may be the removal of an excessively sensitive sensor. In the short term, your costs are lower, and preparation is minimal. In the long term, though, downtime costs rise while the lifespan of assets decreases, and the unplanned extra costs spiral.
This does not mean that a corrective or reactive maintenance management strategy is always the wrong option. If the breakdown of a piece of equipment will not cause downtime or safety risks, the additional cost of preventive maintenance may not be worth the hassle.
Preventive Maintenance
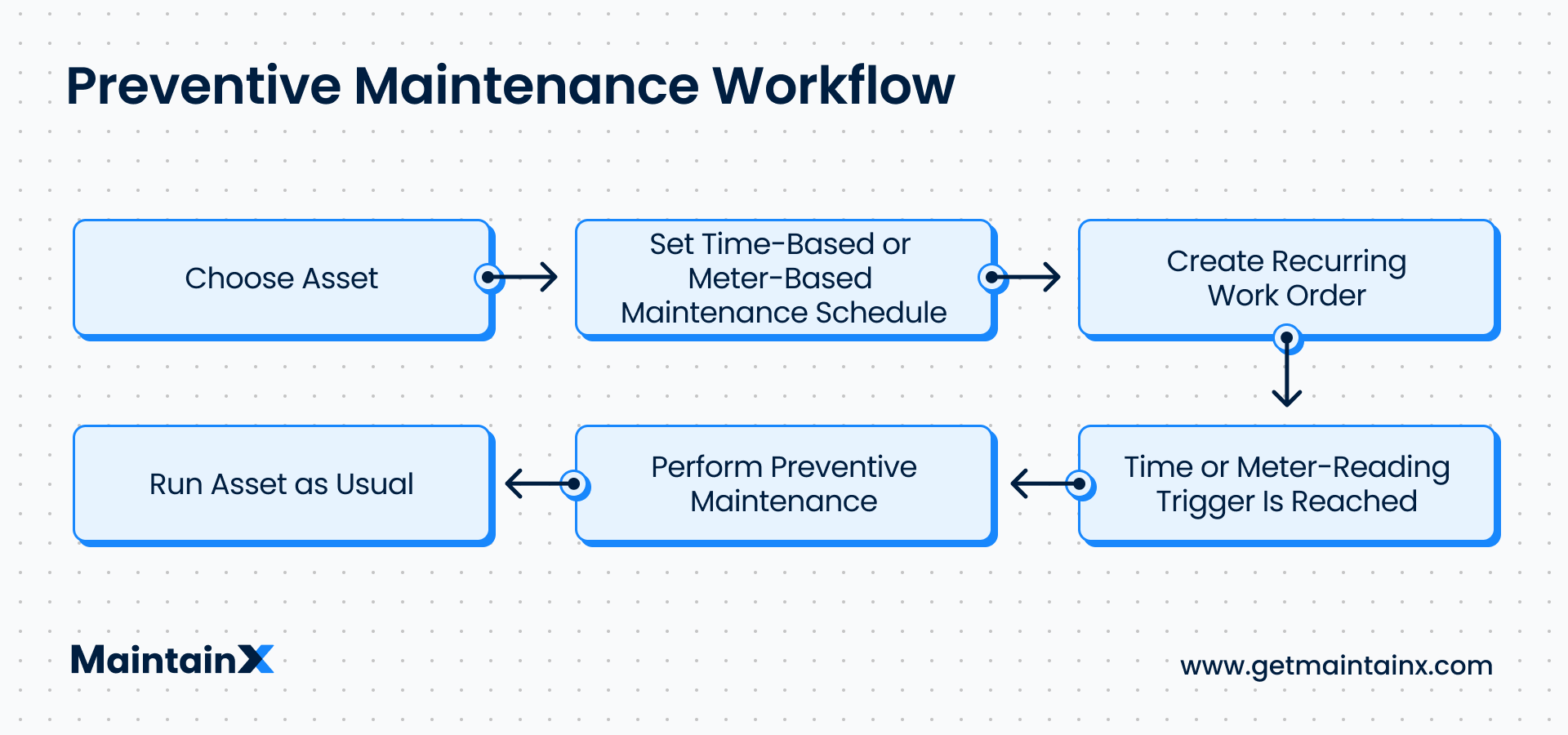
Preventive maintenance (PM) requires routine reviews with a view to avoiding problems before they occur. It can be performed over time intervals, usage metrics, conditions dependent on performance, or parameter monitoring. Preventive maintenance usually includes scheduled downtime to repair or replace a part. It is sometimes mandatory for compliance reasons. For one, preventive maintenance discovers failure points in advance and decreases reactive maintenance down the line. Work orders for preventive maintenance prevent these issues from surprising your team.
Managing time- or usage-based interval maintenance schedules only requires awareness and domain knowledge. A CMMS can help maintain preventive schedules and empower your team members to know exactly when work needs to be performed. On the other hand, such a schedule may become repetitive and expensive, leading to “over-maintenance.” As with all things in life, it’s about finding balance.
As Gupta and Marquez mention in Contemporary Maintenance Management: Process, Framework, and Supporting Pillars: “With time, and in most of the cases, PM programs can reduce reactive/corrective maintenance to a level low enough so that the other initiatives in the maintenance management process can be effective.”
Want to learn more about Preventive Maintenance? Check out our Ultimate Guide to Preventive Maintenance.
Predictive Maintenance
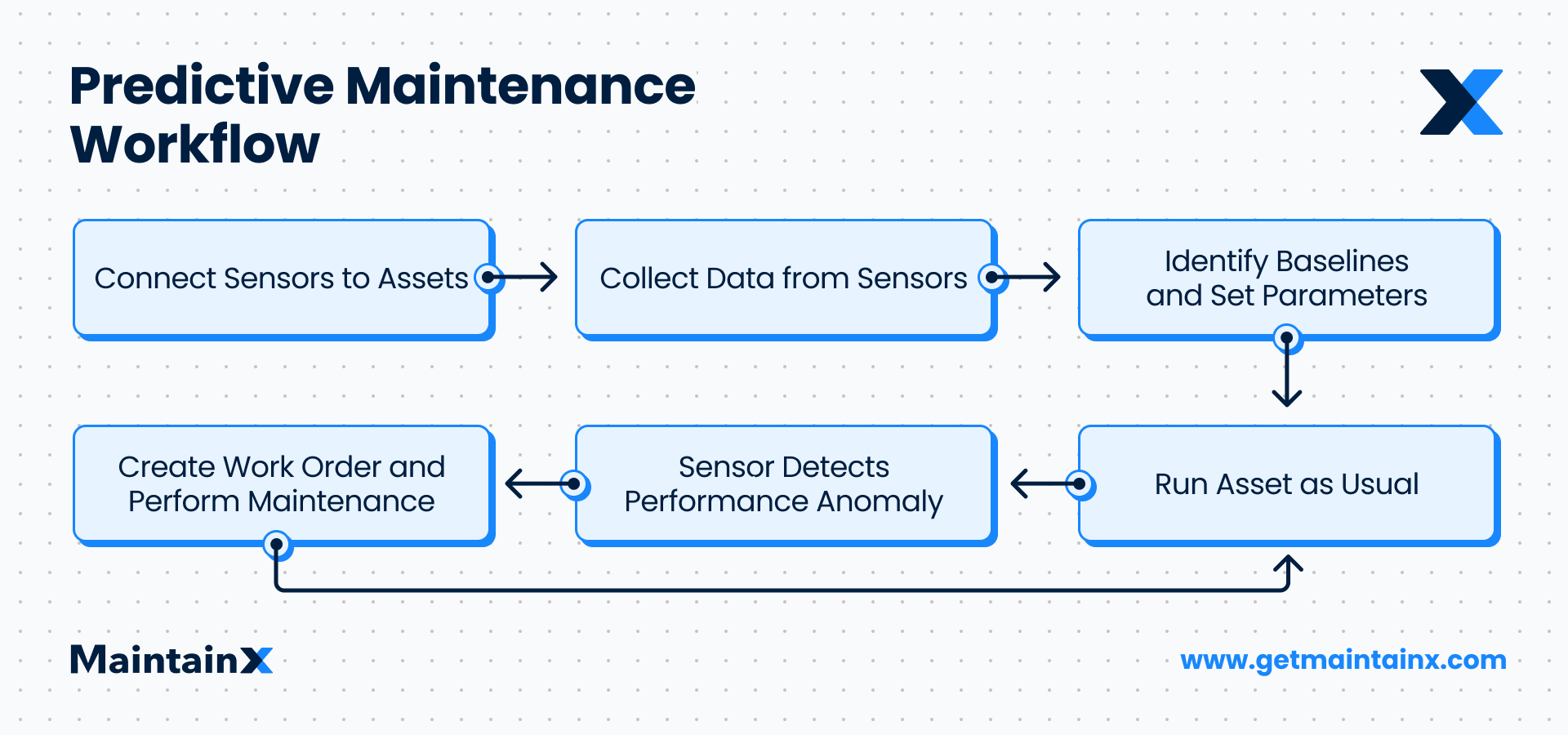
The purpose of predictive maintenance is to manage the “over maintenance” of preventive maintenance programs. Predictive maintenance is achieved by tracking the conditions of equipment with techniques such as:
Vibration Analysis: Vibration levels detect imminent failures
Oil Analysis: Oil particle size determines the state of the equipment
Thermal Sensors Analysis: Sensors monitor equipment temperature to prevent overheating
Efficient predictive maintenance leads to a “just-in-time” maintenance management strategy that maximizes equipment availability with maintenance time. This strategy is recommended for sensitive assets with intermittent or erratic failure periods. Comprehensive monitoring and control equipment is needed for your team to perform these tasks accurately. Predictive maintenance can be time-consuming and expensive for many companies. With the rapidly decreasing cost of sensors and IoT devices, however, successful predictive maintenance is more feasible than ever before.
Prescriptive Maintenance
Prescriptive maintenance is part of the new generation of maintenance techniques that uses the state of the equipment to prescribe optimum maintenance time.
Predictive maintenance will tell you when a part is likely to fail due to its temperature profile. However, a prescriptive analysis could inform you that a 10% decrease in temperature will give you 20% more time to run before failure. Prescriptive monitoring is also in its early stages. However, advanced artificial intelligence and machine learning are making strides toward prescriptive maintenance becoming more widely available.
Reliability-Centered Maintenance
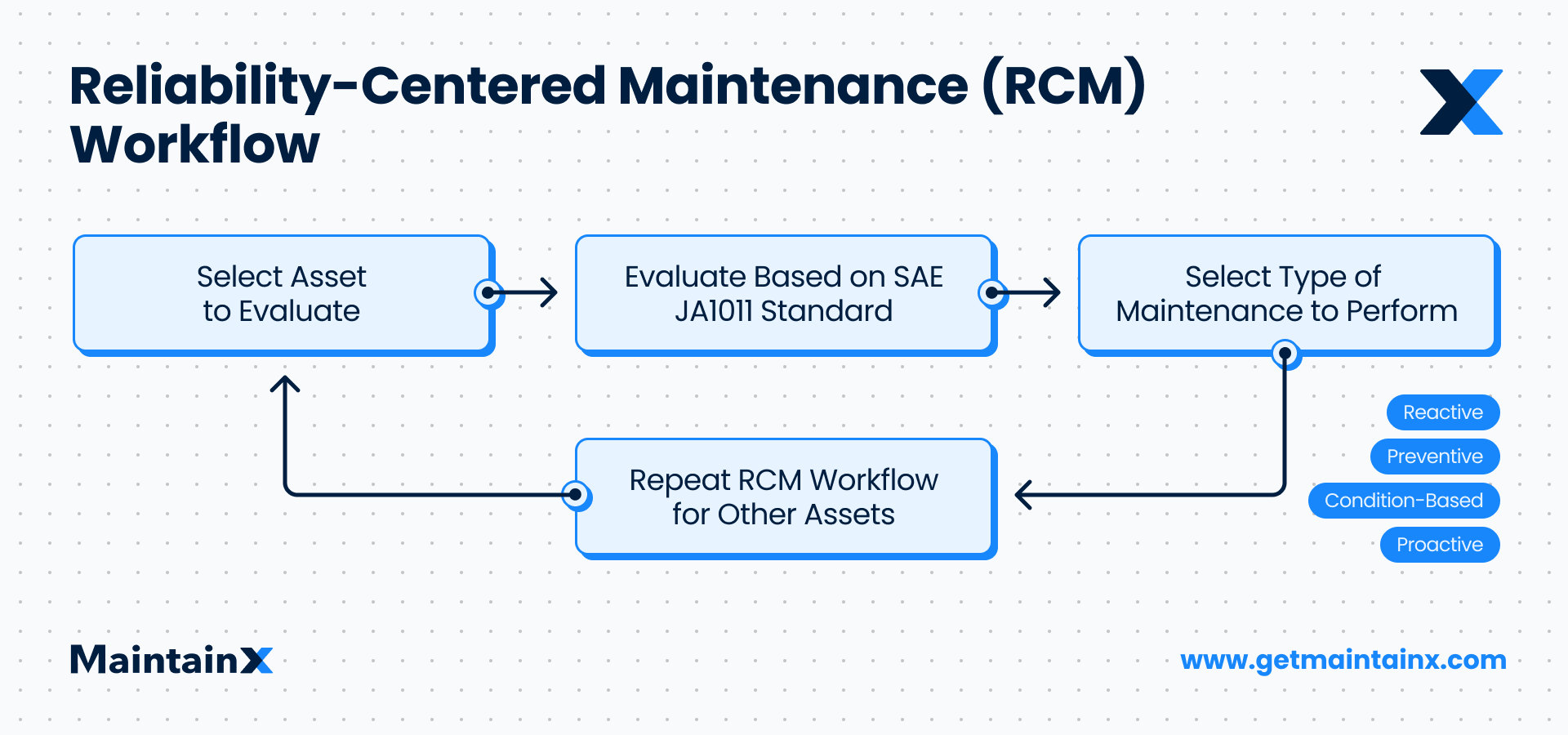
Reliability-centered maintenance is a business-wide methodology. It can encompass all of the types listed above. It aims to maximize the maintenance plan—all parts of the equipment can perform their functions most cost-effectively. This requires the continuous enhancement of the organization’s overall maintenance management plan.
3. Conduct a Criticality Analysis
A criticality analysis is an assessment process that establishes the importance of each asset for your facility’s functioning and output. Each item will fall into one of the following categories:
- Critical: Assets that are critical for the functioning of the facility.
- Vital: Assets that are important but not critical for production.
- Secondary: Assets that do not have a major role in the functioning of the facility.
Conducting a criticality analysis will help you a) manage your resources more efficiently and b) prioritize critical equipment.
Most importantly, you must clarify what is and is not a critical asset. Proactively maintaining critical assets is crucial as equipment malfunctions can have disastrous consequences in terms of safety, productivity, profits, and environmental damage—or a combination of these. Additionally, equipment with spare parts on hand is generally not considered critical. You may want to use a criticality matrix to stay organized.
4. Match Each Asset to a Maintenance Strategy
Once you have established your criticality analysis, it’s time to evaluate individual pieces of equipment based on two factors—the cost of failure and the ease of monitoring—in order to match each asset with its ideal maintenance strategy.
Examine the cost of failure through multiple perspectives:
- How much will the resulting downtime impact your business?
- Will your team’s health and safety be at risk?
- Are replacement parts easily available?
Ask similar questions about the ease of monitoring:
- Are you able to identify leading indicators to help prevent downtime?
- Does the cost of failure justify allocating resources to monitor the asset?
- Do you have the resources to monitor this asset over other assets in your operation?
This secondary evaluation will help determine the most appropriate maintenance program for each asset. For example, some assets that are hard to monitor may have a low cost of failure. Because these pieces are easy to replace or repair, run-to-failure maintenance is most appropriate. Likewise, critical equipment that is easy to monitor will benefit most from a predictive maintenance approach. You can find preventive maintenance information through your manufacturer guides or directly from your vendor. Once you’ve identified which assets need to be prioritized, make sure you implement the most up-to-date guidelines for each asset.
5. Access Real-Time Data
Use You also need to have up-to-date maintenance information on how to service and care for assets and make it easily available for your maintenance team.
Manufacturers’ data and guidelines, historical internal data, and industry best practices are all important sources of information. On the basis of this information, you can create standard operating procedures (SOPs) for your maintenance team to make sure that they execute maintenance correctly. Consider additional training if necessary.
Manufacturers’ data and guidelines, historical internal data, and industry best practices are all important sources of information. On the basis of this information, you can create standard operating procedures (SOPs) for your maintenance team to make sure that they execute maintenance correctly. Consider additional training if necessary.
6. Consider Availability of Resources
When updating your maintenance strategy, it’s equally important to consider the availability of maintenance resources. Most companies allocate fairly limited resources for maintenance. Managers may need to rally for the following additional resources to successfully implement new maintenance strategies:
- Budget
- Manpower
- Tools
- Inventory
- Software
Nearly all industries are facing growing pressure to do more with less. Budgets are tight, while the amount of work is increasing. Translation: the prioritization of maintenance resources based on assets’ criticality is crucial for success!
If you’re relying primarily on reactive maintenance, you may be unknowingly wasting efforts and resources. If so, shifting from reactive to proactive maintenance can help you save money and time and improve efficiency. If most of your maintenance is proactive, you can still fine tune it to achieve a better ROI.
You may also discover that you’re performing excessive maintenance on some assets. This can happen with equipment that is rarely used but is still serviced regularly, or with low-risk, easy-to-replace parts that may be best left on a run-to-failure maintenance program. It’s not realistic—or doable—to change every asset’s maintenance plan at once. You may risk overwhelming your maintenance team, or you may not have all the necessary resources you need.
Do an ROI analysis of your assets’ maintenance to see which equipment is the most critical and which would incur the highest breakdown and maintenance costs if not serviced correctly. Prioritize high-risk and high-value assets first, and add equipment to your new maintenance strategy progressively.
7. Get Everyone on Board
The most successful maintenance strategies for plants and equipment are the result of teamwork and good communication. That’s why, when planning a new maintenance strategy, it’s important to keep your entire maintenance team involved. This will guarantee that:
- You’re not missing critical pieces of information
- The team is fully invested in the changes you’re making
- The team understands the scope of the maintenance work
- The entire implementation process is smooth
Additionally, you may want to create a separate team or committee to help you implement the overall maintenance strategy’s most significant changes. For this, it’s best to involve maintenance, engineering, and operations staff to benefit from each department’s skill sets and expertise and guarantee a high level of acceptance and adoption across your organization.
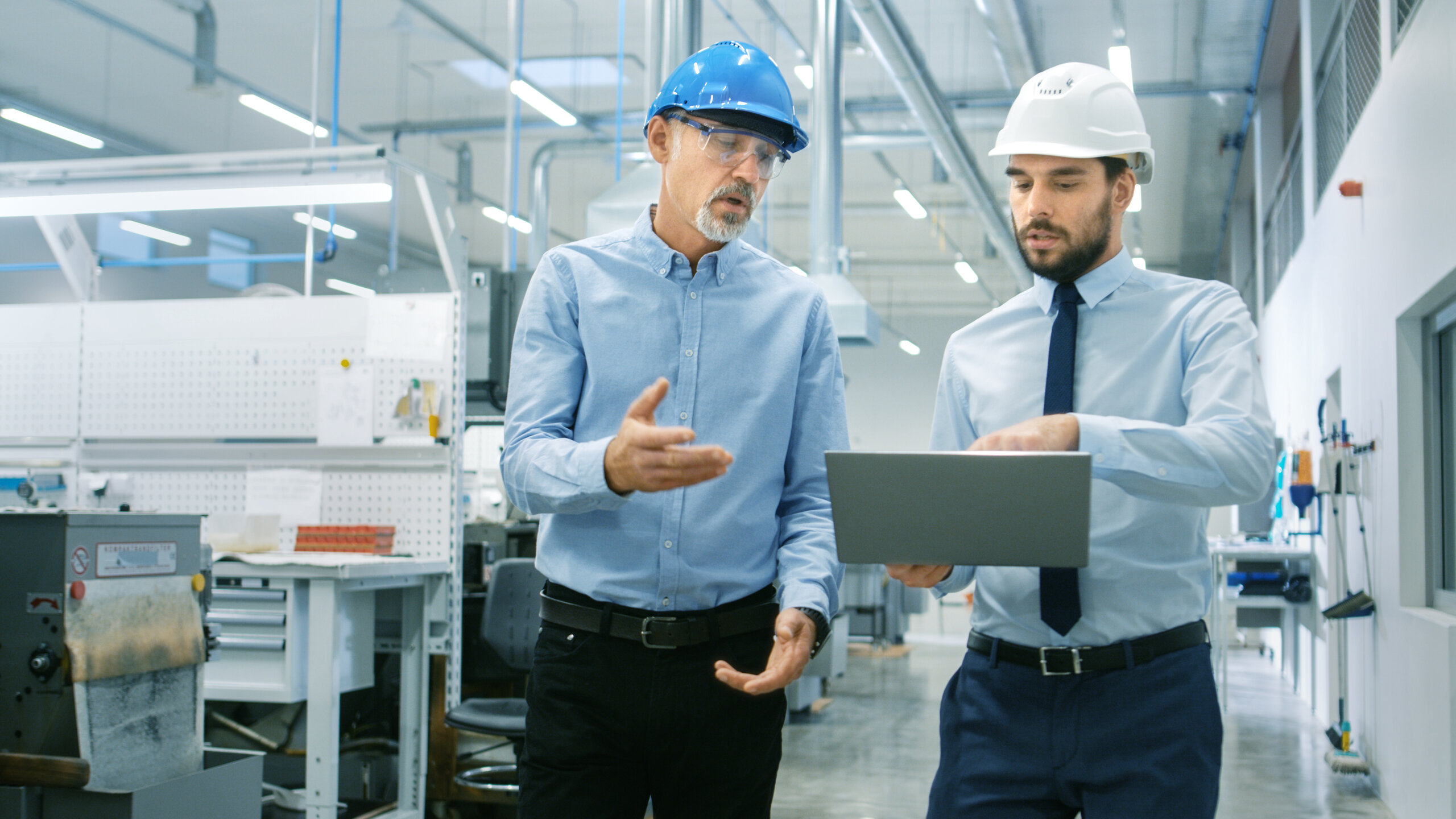
8. Track Your Progress with Maintenance Management Software
Finally, monitor and measure your progress over time. Determine what is or isn’t working as expected and adjust accordingly. For example, you may realize your team needs additional training to properly execute your chosen maintenance strategies. Or, you may identify the need for new materials, tools, and spare parts.
Use a Computerized Maintenance Management System (CMMS) to track your progress, analyze key performance indicators (KPIs), and generate meaningful data reports. SaaS products offer different CMMS features and customization that vary based on the company and pricing plan. Gather benchmark data on your facility’s performance before changing strategies. Your most useful KPIs will most likely be:
- Equipment Performance
- Mean Time Between Failure (MTBF)
- Mean Time to Repair (MTTR)
- Maintenance Costs
Collect benchmark data for both individual assets and collective asset holdings. This preliminary work will enable you to draw meaningful conclusions from your new KPIs post-launch. Review your strategy’s performance frequently and prioritize realistic improvements that are achievable in the short to medium term.
Preventive vs. Reactive Maintenance: Practical Considerations
Many organizations rely 100% on reactive maintenance, especially when starting. Most maintenance experts propose an ideal maintenance ratio of 80% preventive to 20% reactive maintenance. However, this is difficult for most organizations to achieve from the get-go because of limited resources. You can gradually move toward a PM-heavy strategy through the following actions:
- Catalog each asset, from high-priority to low-priority
- Research manufacturer maintenance recommendations
- Implement condition-based strategies, where applicable
- Schedule recurring work orders
Again, start with your most important assets and slowly work toward scheduling the majority of your equipment for preventive maintenance. Remember that this is a long-term goal, which takes time, resources, and dedication to achieve.
Once you’ve achieved, or come close to, an 80/20 ratio, you might explore the benefits of predictive maintenance (PdM). PdM involves using newer technology, such as sensors, to conduct vibrational analyses and determine ideal servicing times. Put simply, PdM helps facilities find the sweet spot between efficiency and costs.
Maintenance Strategy Examples
Let’s analyze the maintenance strategies of three hypothetical organizations—each one using a different preventive-to-reactive maintenance ratio.
Example 1: A small hotel that operates in reactive mode nearly 100% of the time
Bob, the hotel’s general manager, oversees a team of three technicians on a limited budget. He’s relying on paper work orders and a whiteboard to keep track of tasks. Unfortunately, his team is often running behind schedule, as they need to handle whatever is most urgent first, and there is always something seemingly urgent competing for their attention. Consequently, other maintenance requests fall through the cracks—more than a fluke. Everyone is working under pressure, and people blame one another for failures and unfinished tasks. The team occasionally needs to outsource expensive repairs, and the hotel is losing customers because of bad Yelp reviews.
Example 2: A fleet management company that is successfully applying the 80/20 rule
Jerry is an operational manager charged with maintaining a 100-vehicle fleet, managing eight technicians, and identifying opportunities to lower costs. Five years ago, he implemented a preventive maintenance program with the help of mobile-first CMMS software. Jerry’s workers are always busy, but tasks are nearly always completed on time. All critical equipment functions smoothly and is regularly serviced. In the rare event of an unplanned breakdown, the maintenance team is quick and efficient in fixing the problem. Jerry analyzes all issues with the help of the CMMS and fine tunes the company’s approach to the maintenance of each asset.
Example 3: An automobile manufacturing plant experimenting with PdM technology
John, the plant manager, has years of experience with PdM, and the company’s management fully supports his efforts. He manages a team of 15 maintenance technicians and invests in their training and professional development. The company uses sensors to detect anomalies in the performance of assets and addresses them right away. Most issues are tackled before they turn into problems. Also, the company has a detailed maintenance schedule logged in its CMMS and the necessary resources to work according to the industry’s best practices.
Choose the Best Maintenance Management Software for Your Maintenance Strategy
Do You Need Maintenance Management Software?
As previously mentioned, CMMS solutions are a cost-efficient and easy way to streamline your operations and improve maintenance efficiency. CMMS help:
- Shift from reactive to proactive maintenance
- Optimize your maintenance schedule
- Handle both recurring tasks and urgent issues on time
- Reduce maintenance costs
- Improve the visibility into your immediate, mid-term, and long-term maintenance needs
User-friendly manufacturing maintenance management software can make the difference between constantly running behind schedule, fixing urgent issues, and making the most out of your maintenance resources in the most efficient way possible. Case in point: one of MaintainX’s facility management clients increased its annual revenue by $1 million after using our software to assign, track, and manage work orders.
Do you need a CMMS? Maybe not, but having a good one can make meeting your goals substantially easier!
Factors to Consider
When evaluating CMMS options, consider the following factors:
- Available Functionalities: Choose a CMMS with the right functionalities for your company. Key features to consider include scheduling, reporting, workflow optimization, barcodes, meter readings, and instant messaging. A flexible work order creation tool is also a must-have to track work orders and preventive maintenance tasks. If you are looking into facility management software, be sure that it includes vendor management and purchase order functionality.
- Training Needs: Unless you’re using a mobile-first platform like MaintainX, personnel may require training to confidently begin using the CMMS. Check with the CMMS provider whether they have training materials, such as videos, how-to guides, and manuals. A company representative should help your team get up and running.
- Technical Support: You may not need to contact technical support often, but when you do, its availability is crucial. Check that the company has good tech support and that customers are happy with it.
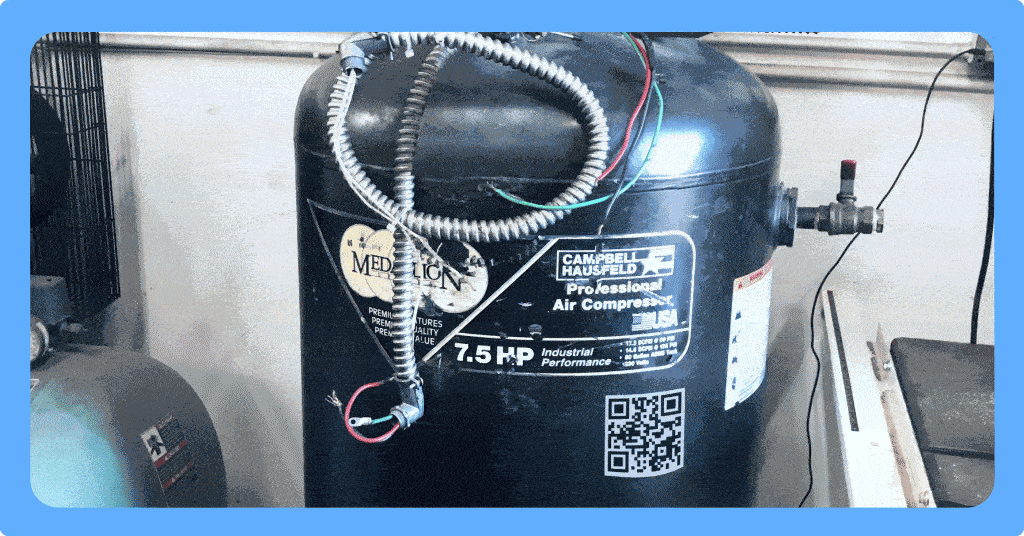
MaintainX Is Your Maintenance Management Software
Maintenance management is a multifaceted discipline involving many moving parts—both figuratively and literally. The right maintenance strategy will be different for each business and for each asset. There is no one-size-fits-all solution.
You can leverage the information provided in this guide, in combination with maintenance management solutions, to help save your organization money and time, and prevent workplace accidents. Understand that, as with any change, it will take deliberate action and reinforcement with your team for you to realize the benefits. Choosing user-friendly software makes maintenance care much easier for everyone involved.
MaintainX is one of the top-rated maintenance management software solutions on the market. Not only for its robust maintenance management functionality but also because it typically requires zero training.
FAQs
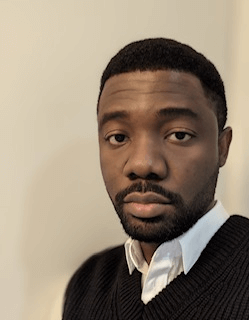
Lekan Olanrewaju is a content writer with years of experience in media and content creation. He has held positions at various media organizations, working with and leading teams at print magazines, digital publications, and television productions.