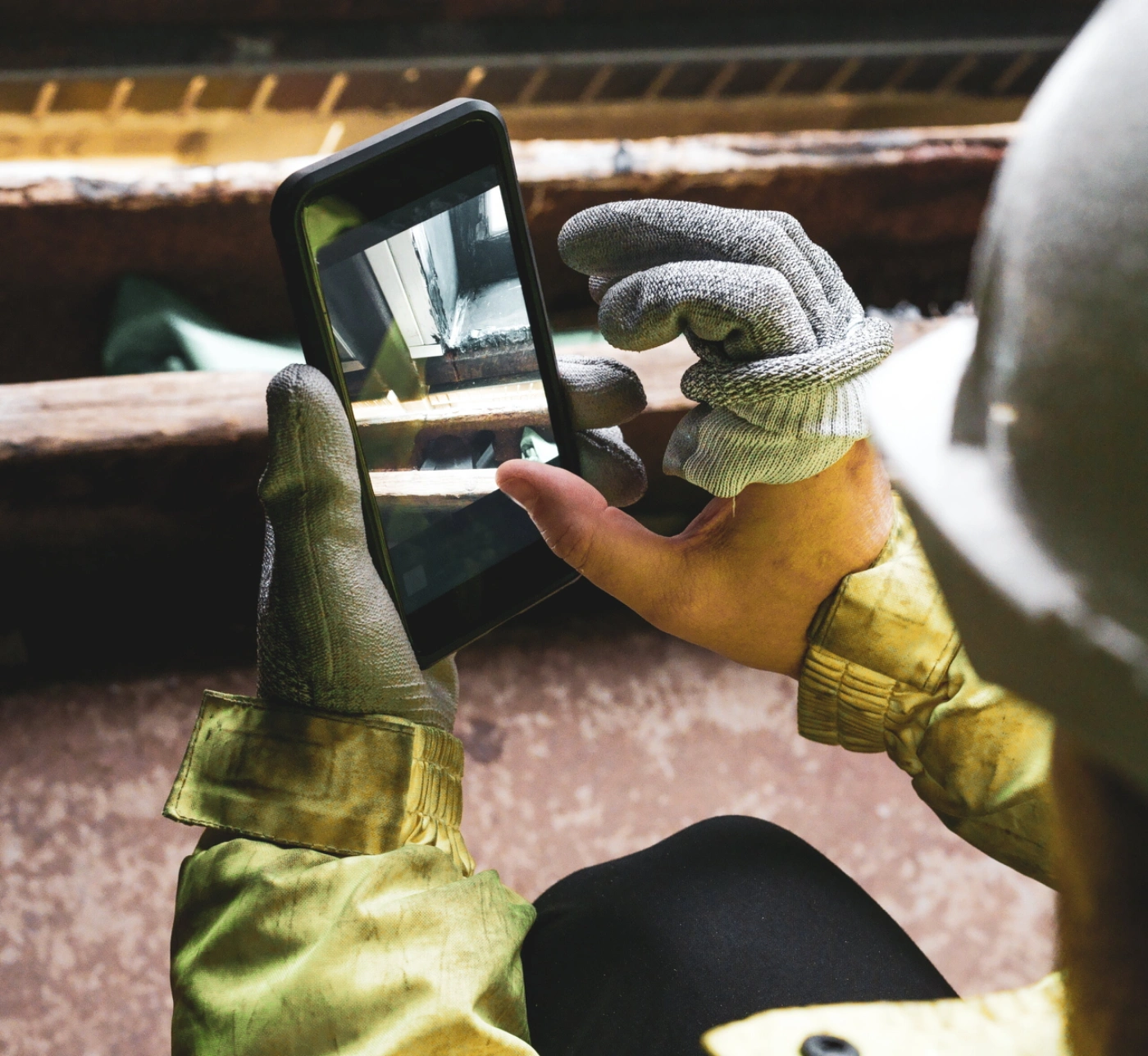
Work order software can dramatically improve business operations, decrease downtime, automate complex workflows, and simplify preventative maintenance (PM). For decades, platform providers almost exclusively partnered with large organizations within the fleet, manufacturing, and facility maintenance industries. Why?
Not all that long ago, the customized nature of software solutions required substantial resources to create, install, and maintain. Not surprisingly, dropping thousands of dollars on a work order software program, or a Computerized Maintenance Management System (CMMS), was a wise investment for a company that had already invested millions in assets.
Conversely, maintenance departments with small budgets saw work order management software as a luxury they could do without.
But that’s all changing thanks to modern cloud infrastructure. Today’s best maintenance platforms are scalable, affordable, and sometimes even free.
What is Work Order Software?
Work order software is a management system designed to streamline maintenance, inventory, and operational tasks across organizations from a centralized app. Work order management software typically facilitates the execution of standard operating procedures (SOPs), production workflows, quality control, and safety inspections.
Maintenance managers can maintain full visibility of the work performed across their organizations at all times while creating, assigning, and tracking work orders from both mobile apps and desktops. However, more than 75 percent of companies still use spreadsheets, paper, clipboards, or nothing at all for maintenance management, according to the Maintenance Management Buyer Report.
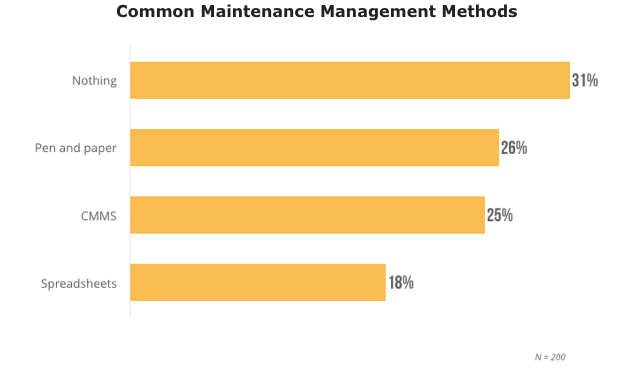
The Best Free Work Order Management Software Apps
In this work order software app review, we’ve compiled information on the best free work order software based on customer reviews, user experience, and functionality. We included 3 of the top work order software solutions that include simple Work Order software, CMMS software, and field service management software. Though each option offers premium paid plans that come with more advanced features, the freemium versions are capable of a surprising amount of heavy lifting for small maintenance teams.
1. MaintainX

Not surprisingly, MaintainX is the world’s first work order software solution designed with real-time chat functionality and one of the world’s first platforms designed specifically for smartphone usage. Furthermore, the app provides an integrated CMMS solution, including everything you need to create, assign, and track maintenance and work orders; execute preventive maintenance programs; document Standard Operating Procedures (SOPs); manage inventory; maintain asset logs; track work requests and maintenance requests; create invoices; and track KPIs.
In addition, MaintainX also includes API integration capabilities that allow external sensors to trigger Work Orders and can push data back to ERP systems. Indeed, the CMMS stands as the most comprehensive maintenance management software platform for mobile devices, tablets, and desktop devices. As a result, MaintainX has acquired a substantial amount of positive reviews from customers in both the Apple App and Google Play stores.
Noteworthy Features:
- Instant Messaging: Segment chat conversations by individuals, groups and teams, departments, topics, and more.
- Work Order Commenting: Chat with technicians directly within individual work orders to troubleshoot in real time.
- Photo Uploading: Workers can upload (and mark up) photos of equipment failures, parts issues, or maintenance quandaries to better illustrate to management what is happening.
- User-Friendly Interface: The MaintainX mobile app is one of the most intuitive, user-friendly work order systems on the market right now. The interface is sleek, quick, and easy to navigate.
- Seamless Integration: Switch back and forth between desktop and smartphone use in real-time without losing progress.
- E-Signatures: Technicians can sign off on completed jobs for additional accountability, in addition to the app’s time stamp feature.
- Work Order Templates: Create routine or recurring work orders faster with templates that have procedures, locations, or parts pre-attached.
Free Plan Includes:
- Unlimited work orders
- Unlimited team messages
- Unlimited assets and locations
- Unlimited web-based and mobile access
- Purchase Order feature
- 5 work orders with photos per month
- 2 work orders with forms per month
- 1 month’s worth of reporting and analytics
Potential Drawbacks:
- No custom user permissions on the free plan
- No API access on the free plan
Industries Using MaintainX:
Manufacturing, Industrial, Facilities Management, Property Management, Government, Schools, Hospitality, Car Wash, Fleet Management, Quick-Serve Restaurants, Warehouses, Churches, Retail, Safety/EHS, Building Maintenance, SMB to Enterprise.
Best Suited For:
- Organizations of all sizes needing a user-friendly work order app that workers can quickly navigate without extensive training.
- Teams wanting to adopt a centralized instant messaging system to improve communication.
2. UpKeep
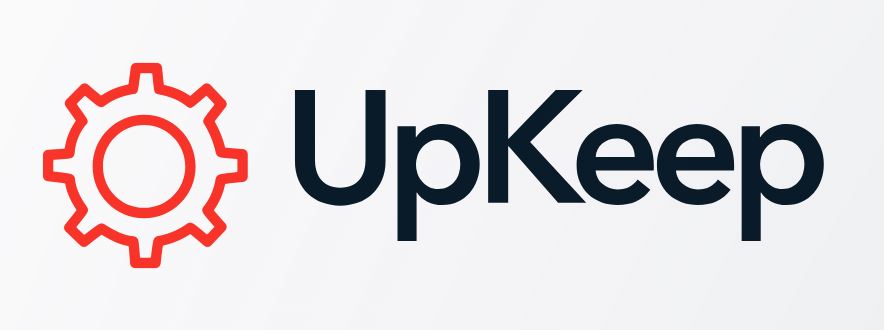
Another maintenance software mobile app, UpKeep, allows maintenance teams to create and manage recurring maintenance tasks, track inventory, run billing/invoicing, manage calibrations, control keys/locks, and more.
Additionally, UpKeep allows managers to assign work order processes with varying priority levels so tasks can be completed from most important to least important. However, many of UpKeep’s most compelling features are only available to paying customers. Consequently, the starting price point for the basic plan is $35 per user per month.
Importantly, UpKeep’s freemium version was created with the goal of allowing users to “try before they buy” and isn’t meant to be a complete CMMS solution. In fact, the work order software app is best suited for individual technicians wanting to organize their daily tasks.
Noteworthy Features:
- User-friendly interface
- Asset management
Free Plan Includes:
- Unlimited work orders
- Unlimited assets and locations
- Unlimited web and mobile access
Potential Drawbacks:
- No instant messaging functionality
- Inflexible procedures without conditional logic or scoring
- Learning curve for building reports
Industries Using UpKeep:
Property Management, Fleet, Hotels, Oil & Gas, Construction, Municipalities, Warehousing, Restaurants, Churches, Education, Food Processing, Packaging
Best Suited For:
Individuals who don’t need to assign work orders to others simply want to better organize their daily tasks and don’t need to refer to them once they are completed.
3. Jobber
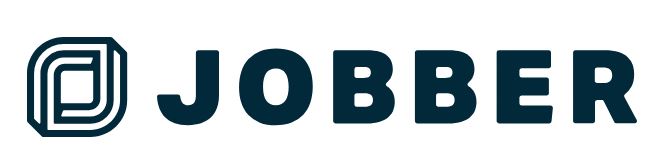
Jobber is ranked as our top field service management app (FSM). As a result, the app has a work request and scheduling platform tailored for service providers. Founded in 2011, Jobber focuses on helping small businesses with dispatch-related work.
In brief, the app makes it easy to build and delegate work orders by offering a drag-and-drop calendar. The app also helps with client work request intake by automatically creating new work orders that can be assigned to a team member. Consequently, customers who have the highest level of satisfaction are those who need to be able to manage employee schedules and client invoices.
Noteworthy Features:
- Dedicated Mobile App
- Built-In Client/Customer Relationship Manager (CRM)
- Invoice Management
Paid Plan Includes:
- Client/Customer Relationship Manager (CRM)
- Quotes
- Invoicing
Potential Drawbacks:
- No free plan
- No asset management
- No parts or inventory management
Industries Using Jobber:
Carpet Cleaning, Chimney Sweep Services, Elevator Services, Garage Door Services, Janitorial Services, Junk Removal, Locksmith Services, Pest Control, Pool & Spa Services, Pressure Washing, Snow Removal, Tree Care, Window Cleaning
Best-Suited For:
Commercial service businesses that need to dispatch work and send invoices.
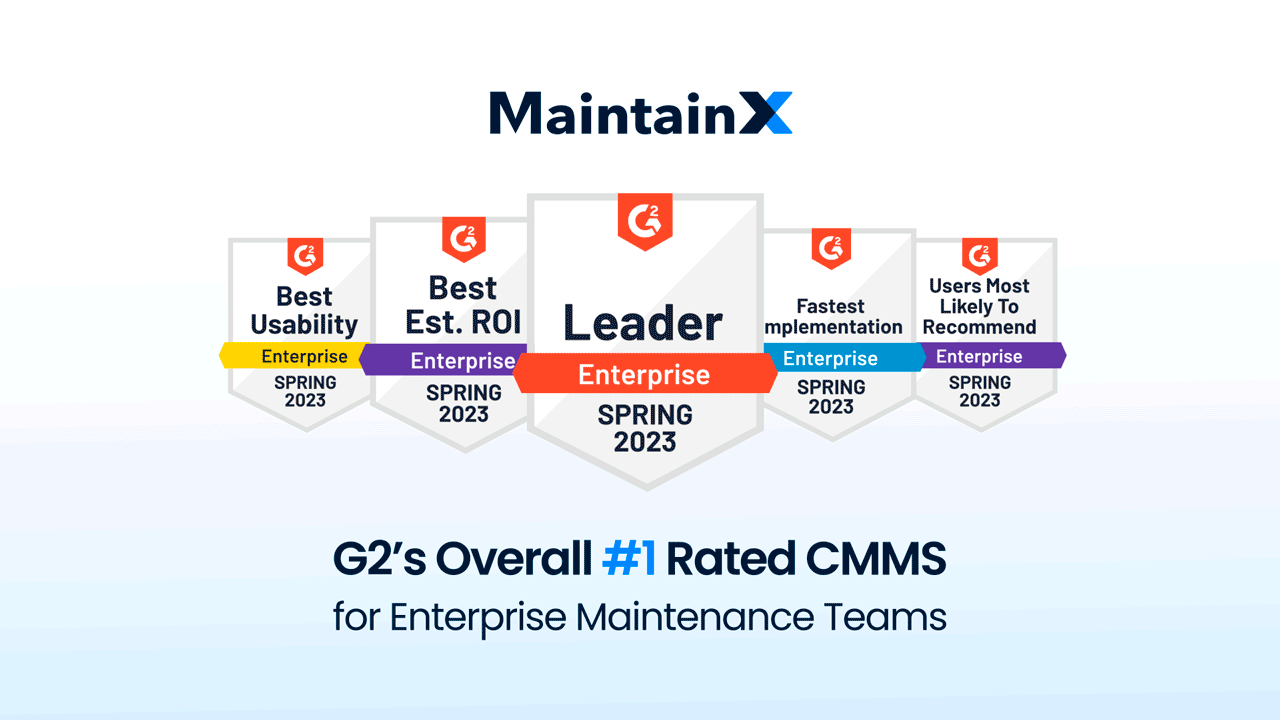
Top 6 Benefits of Work Order Management Software
Work order software plays a crucial role in business management, particularly for organizations involved in services or manufacturing. The software helps streamline processes, improve efficiency, and increase productivity. Here are the top six benefits of using work order software:
1. Enhanced Operational Efficiency
Implementing work order management software can greatly enhance your organization's efficiency. By automating service requests, maintenance tasks, and work schedules, this robust software saves valuable time and significantly reduces manual workload, streamlining your day-to-day operations.
2. Improved Communication and Collaboration
Work order systems facilitate superior communication across various departments and teams. By offering a centralized hub for information storage and retrieval, the software reduces the chances of miscommunication, ensuring smoother workflows and increased productivity.
3. Increased Work Order Standardization
Adopting digital work order solutions minimizes the risk of human errors inherent in manual tracking and documentation. The automated process ensures accurate task assignment and tracking, improving the precision of your service management processes.
4. Improved Inventory Management
Digitizing your parts inventory can go a long way to mitigating these delays. A detailed parts inventory lets your team know what’s on hand, monitors quantities, and automates purchase orders.
We know that an unplanned repair can amplify these interruptions and leave your team scrambling to find the critical parts needed to prevent costly production delays. In the auto industry, for example, downtime can cost up to $50,000 per minute, putting a lot of pressure on maintenance departments to work more strategically.
With efficient work order software at your disposal, you can optimize resource utilization. The tool provides detailed insights into available resources and their deployment, enabling managers to plan effectively, minimize waste, and cut down on costs.
But don’t take it from us. We spoke with Navistar Maintenance Technician Ronald Gibson to walk us through the benefits of digitizing and automating your parts inventory, especially as we face long lead times and limited supplies.
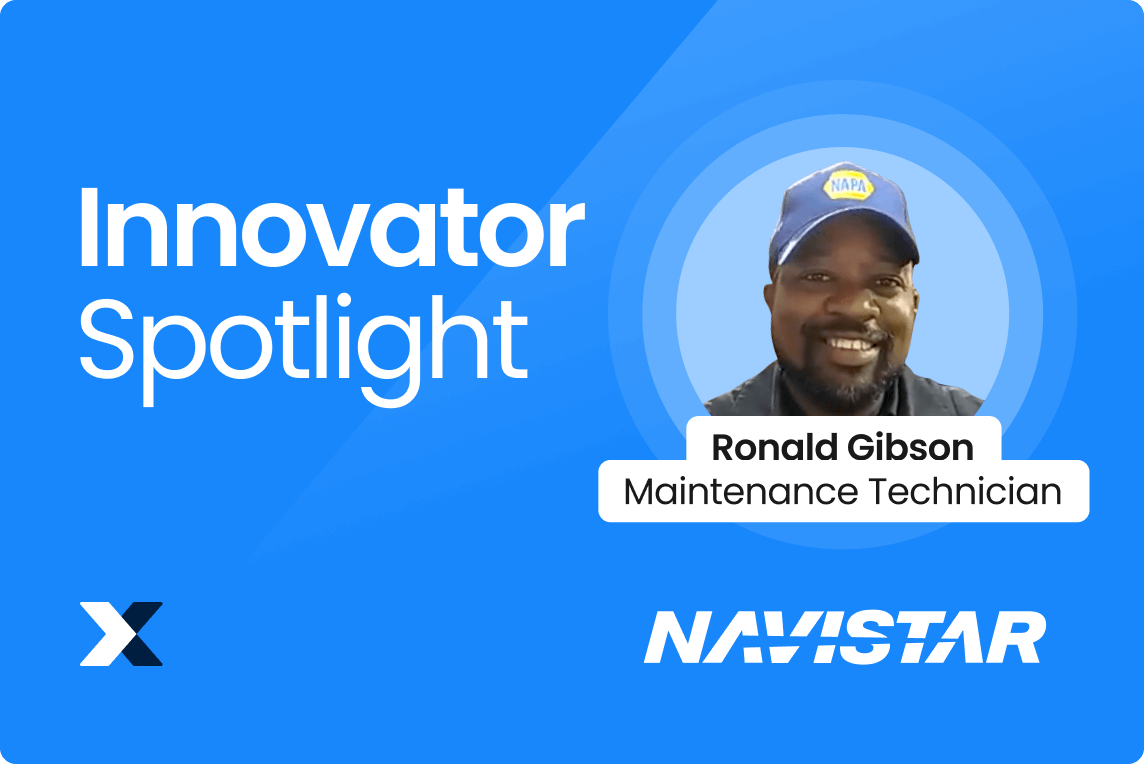
5. Real-Time Data-Driven Insights and Reporting
A work order tracking system offers comprehensive data collection on all aspects of your operations. By helping you identify performance trends and bottlenecks, the software facilitates data-driven decision-making and strategic planning.
6. Significant Cost Savings
Work order software can be a game-changer in achieving significant cost savings. By increasing operational efficiency, reducing manual errors, optimizing resource utilization, and facilitating data-driven decisions, this software helps cut operational costs and boosts profitability.
Types of Work Order Management Software Systems
To determine which type of work order management software system is best for your organization, it’s helpful to understand their differences. Consequently. companies with heavy, on-premise maintenance requirements most benefit from CMMS solutions. On the other hand, commercial service companies may require service order software capable of GPS tracking. Below are the three main types of work order management systems.
1. Basic Work Order Software Systems
Maintenance work order systems are designed with a simple mandate: assign, track, and record work orders. This allows for both work order creation and real-time progress updates through one centralized platform. These work order management solutions are specifically designed for small businesses with simple management processes.
However, in recent years, some Software as a Service (SaaS) providers have taken on a revolutionary challenge: designing work order software that perfectly balances ease of use with advanced feature functionality. These cloud-based platforms are blurring the lines between basic work order software systems appropriate for small businesses and our next category: Computerized Maintenance Management Systems (CMMS), which are ideal for both SMBs and enterprise companies.
2. Computerized Maintenance Management System (CMMS)
In brief, CMMS software was originally designed for organizations responsible for maintaining large numbers of critical equipment and assets. Industrial plants, manufacturing facilities, and mining companies are longstanding users of CMMS. However, in recent years, facility management, food service, hospitality franchises, and more have also implemented CMMS programs.
The platforms are complete maintenance management systems that include capabilities for organizing strategic preventive maintenance, predictive maintenance, and reactive maintenance programs. The software also provides labor time tracking, historical metric reporting, and real-time insights that can translate into O&M cost-saving opportunities. From preventive maintenance schedules to parts inventory, CMMS systems are invaluable for operations that depend on critical assets. As previously mentioned, today’s cloud-based CMMS solutions are more versatile than their predecessors.
The cloud-based software is stored on multiple servers that allow providers to deliver more affordable, scalable, and reliable user experiences than ever before. Translation: Monthly, per-user pricing plans that don’t break the bank. The best CMMS programs are available for mobile users on both iOS and Android.
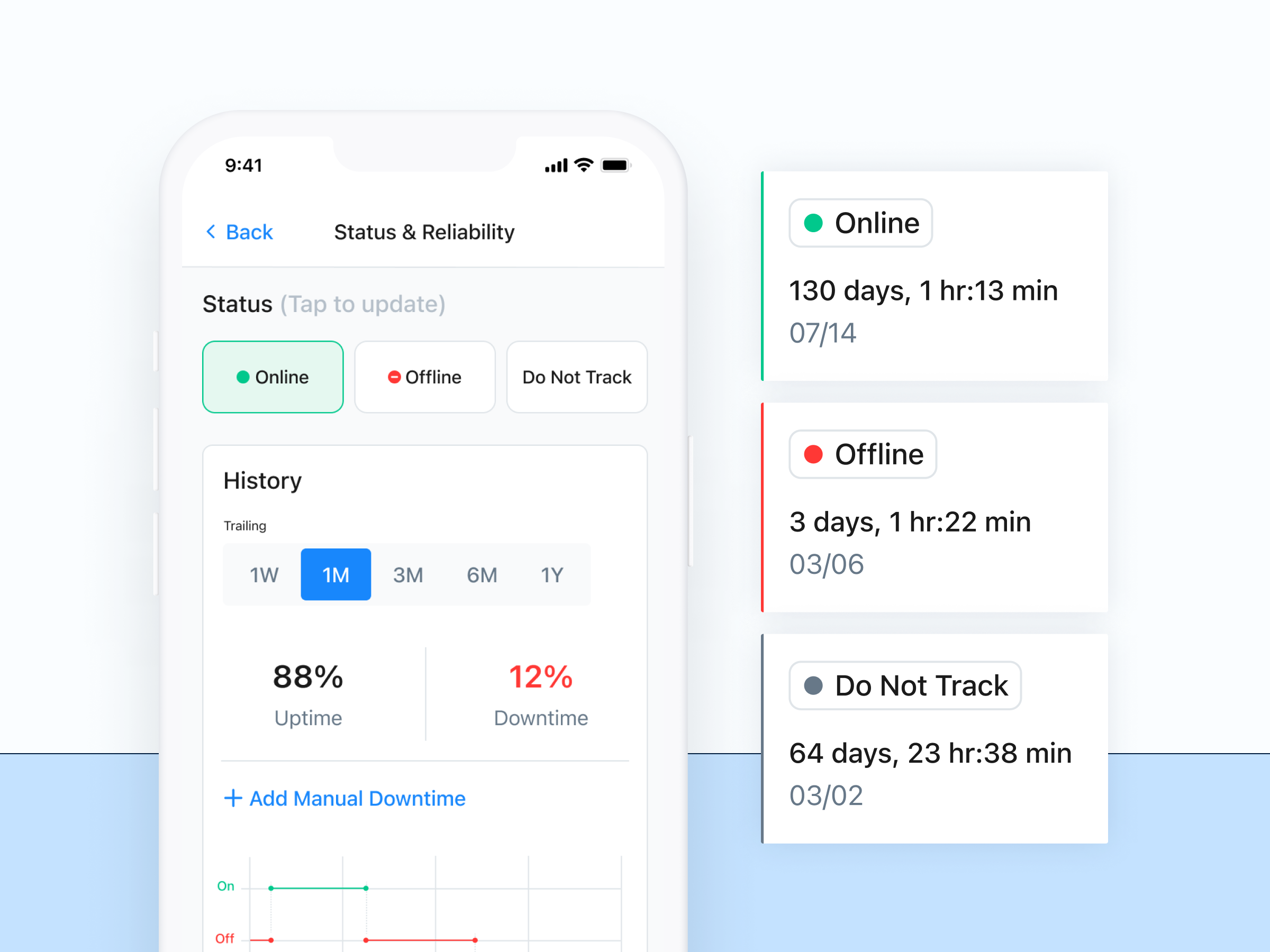
3. Field Service Management (FSM)
FSM systems are designed for companies with field teams. If your organization needs to assign and track field technicians, salespeople, or other dispatch team members, FSM might be the right choice for you. Many of these systems include invoice management features that help convert your work order tickets into billable invoices once completed. They also help plan routes and share any relevant information, files, etc., on the fly. However, FSM software does not offer the full range of features that CMMS, like MaintainX, offers.
Features to Look for in Work Order Software
1. Mobile User Experience Tailored to Frontline Teams
- Maintenance managers say one of their top challenges is getting people to use their software correctly. If the system is not easy-to-use, it won’t be adopted, and you will not realize the benefits of the software (faster response times, data capture, increase planned maintenance, etc)
- If the system looks complicated to you, it’s likely to be too complex for your technicians as well
- Legacy solutions and ERP modules are known to have bad mobile experience and were not designed for today’s mobile workers
- The ability to add photos and annotate them is an example of a work order software feature that meets the needs of today’s mobile teams
2. Modern Communication Features
- Many work order software solutions make it easier to create and complete work orders but don’t include fast and streamlined ways to communicate as a team
- Maintenance is a collaborative process, and technicians should be able to quickly lend the expertise of others on the team without resulting in long delays
- If communication is not centralized within your work order software, valuable information is swapping hands outside of the system and not being recorded
3. Built-In Asset and Inventory Management
- Having asset and parts records connected to your work order management streamlines work further for technicians by giving them more context
- It also gives a fuller picture to managers about where resources are going
4. Reporting Dashboards
- The best work order software provides robust reporting that allows you to quickly see how many work orders were completed on time, how many were planned vs unplanned, and what costs were associated with each work order
- This helps you to become more efficient as a team and reduce bottlenecks that you would otherwise not be aware of
- It also helps you to better plan your resources and understand where you might need more headcount or to replace machinery
5. Advanced Customization
- Although it’s important to provide your team with a simple and easy-to-use solution, it should also be customizable so that you can tailor it to your unique needs
- Useful customization includes:
- The ability to add custom fields to capture specific data that are useful to your organization
- Making certain data fields or signatures mandatory to ensure that important details are captured, and people are held accountable
- Ensuring that work orders can be triggered automatically by certain events specific to your operation, such as a pressure sensor hitting a certain reading
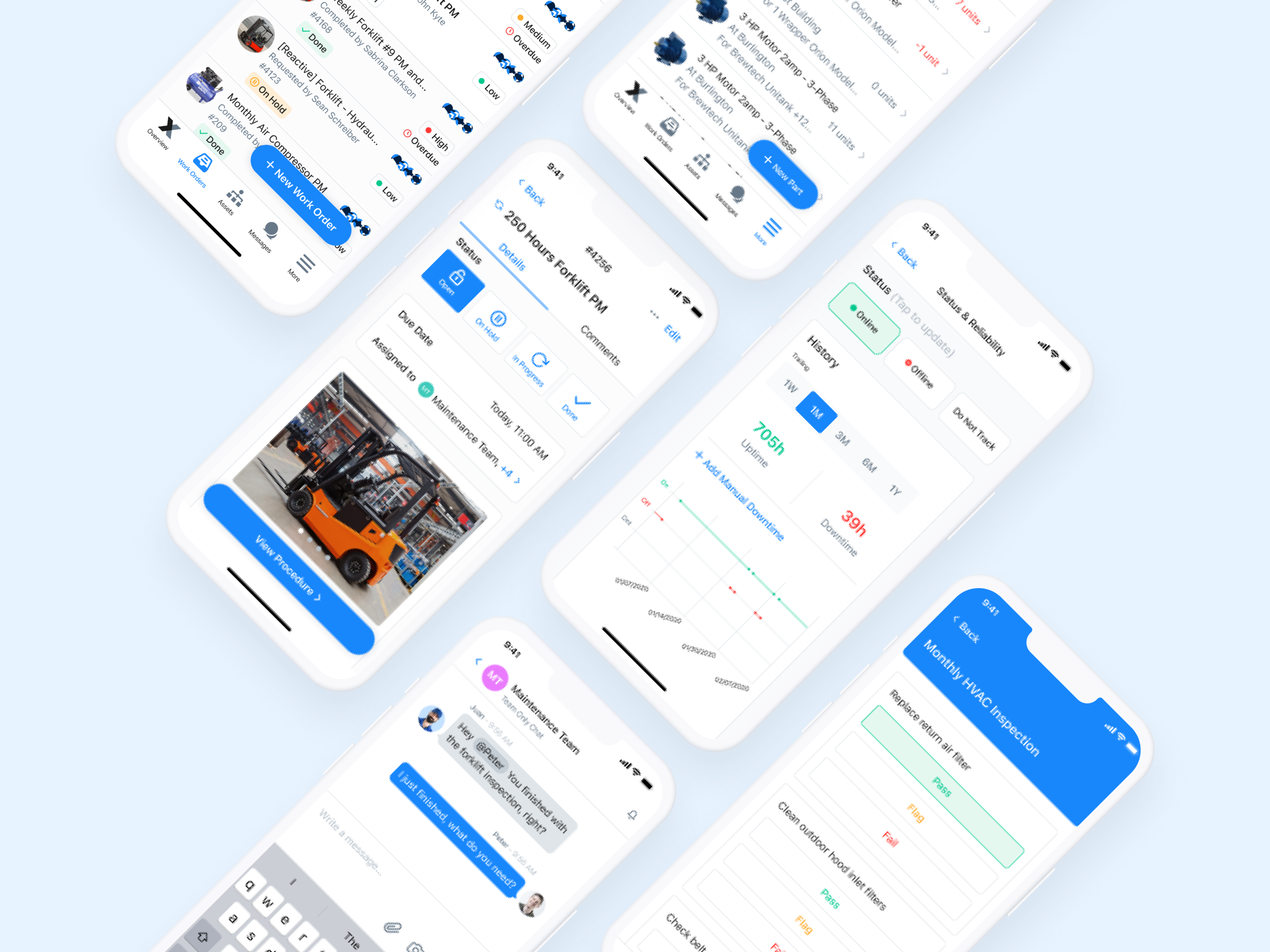
Choosing the Best Work Order Software App for Mobile
We hope you have enjoyed our work order software app review. As you can see, work order software is now more affordable, functional, and accessible than ever before. Unless your organization has uniquely complex maintenance needs, choosing the best CMMS often comes down to personal preference: What features do you absolutely need? And which ones can you live without?
Look for work order software that offers at least the following key capabilities:
- Native-first mobile access
- Automatic routing of work orders to assigned teams
- Real-time inventory supply management for assets and parts
- Barcode and QR code tagging and scanning
- Fully configurable work order request forms
We know that delays can happen—from when a person first identifies an issue to when a tech resolves the issue to when the resolution is communicated back to the person who reported it.
Without an efficient process to manage maintenance requests, requests can sit around for hours or even days before they’re picked up and actioned. As a result, supervisors can get bombarded with irrelevant requests, and requesters can be left in the dark as to why their request isn’t being fulfilled.
MaintainX’s new Request Routing allows requests to be assigned to specific teams, accelerating the approval process. Approvers are notified when a request has been assigned to their team and can quickly distinguish these requests from others they’ve submitted. Request Routing helps supervisors focus on the requests that matter to them while minimizing distractions.
With Request Routing, requesters receive automatic push notifications when their request is declined, minimizing back-and-forth and helping to reduce frustration.
In addition, to help technicians connect faster with key people and information, we’ve introduced @Mentions on Work Order comments and instant messages. This allows you to tag other MaintainX users in your message, notifying them immediately of something you want to ask them or bring to their attention.
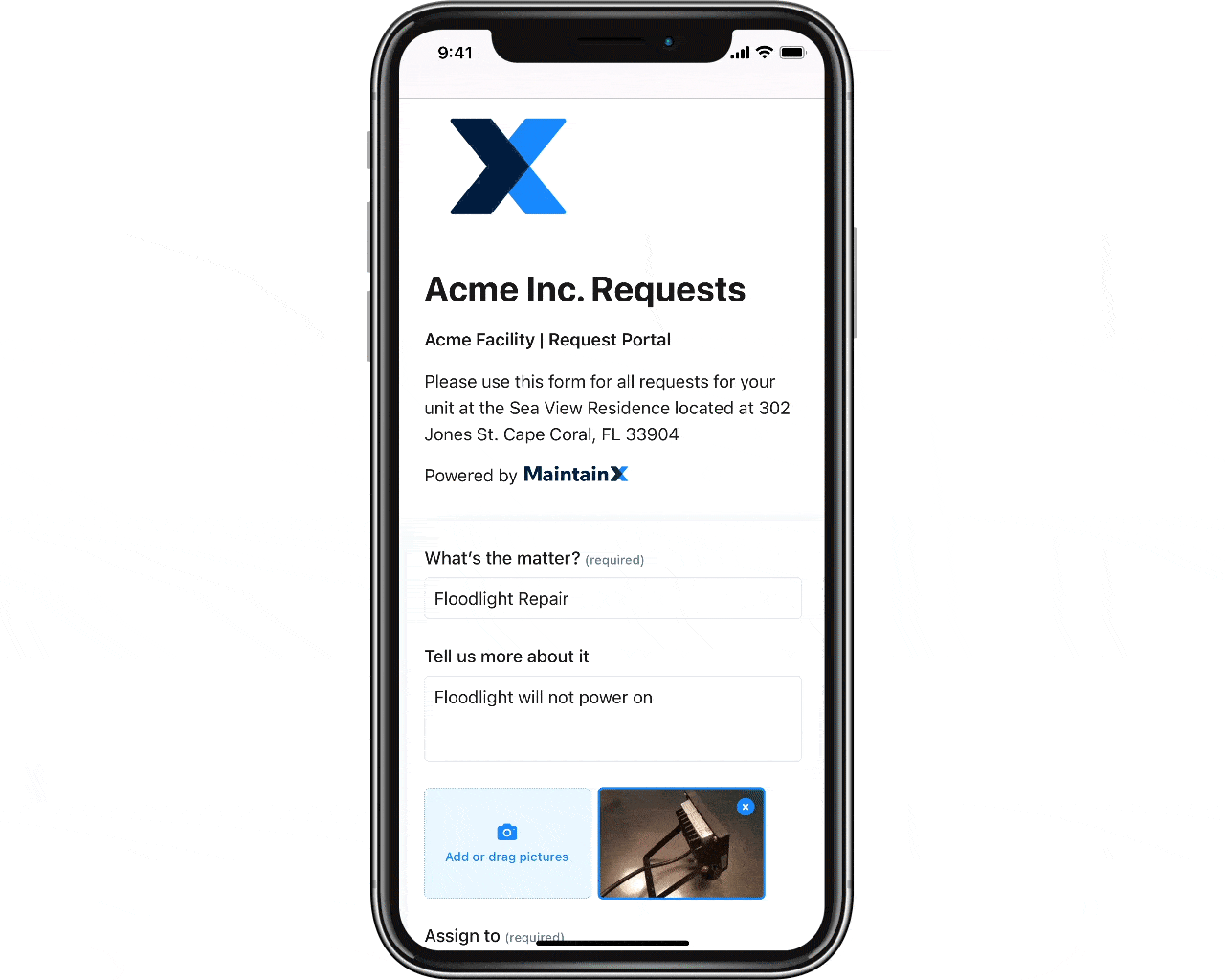
The thing is, you often don’t know until you begin creating and managing your own procedures, checklists, and templates. For this reason, we recommend downloading the apps that appeal the most and making the decision based on what you would most enjoy using every day.
Best Work Order Software FAQs
Can Work Order Management Software Be Customized to Specific Industries or Business Needs?
Yes, many work order software solutions offer customization options to adapt to diverse industry requirements. They can be tailored to suit specific workflows, industry compliance standards, and unique business processes.
Can Work Order Software Integrate With Existing Systems Within an Organization?
Many work order software options offer integration capabilities with other systems like ERP (Enterprise Resource Planning), CMMS, accounting software, and asset management systems. This integration streamlines data flow and prioritizes seamless communication between different departments or functions.
Is Training Required to Use Work Order Software Effectively?
While some training might be necessary for initial setup and understanding functionalities, most modern work order software systems are designed with user-friendly interfaces and intuitive features to ensure ease of use for employees across various skill levels, not just the tech pros.
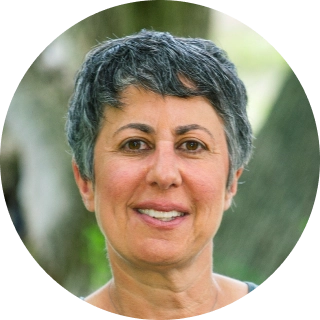
Caroline Eisner is a writer and editor with experience across the profit and nonprofit sectors, government, education, and financial organizations. She has held leadership positions in K16 institutions and has led large-scale digital projects, interactive websites, and a business writing consultancy.