Preventive vs. Predictive Maintenance
Preventive maintenance and predictive maintenance represent types of maintenance management plans. Often referred to as proactive maintenance, they are strategies that avoid equipment failure and unplanned downtime, reduce the need for repair and replacement, and schedule machine maintenance in advance. In this article, we’ll delve into the differences between preventive vs. predictive maintenance.
Preventive Maintenance
Preventive maintenance (PM) is routine maintenance to keep equipment running by preventing unplanned downtime and costs from unanticipated equipment failure. Here maintenance is triggered by time thresholds, meters, or events. Think of PM in terms of the tires on your car. The NHTSA recommends “replacing tires that are 6 to 10 years old, regardless of tread wear.” Additionally, we don’t wait for our brakes to fail—which, in maintenance terms, we call run-to-failure maintenance. We practice proactive maintenance to keep everyone on the road safe. Preventive maintenance is performed based on time and usage benchmarks.
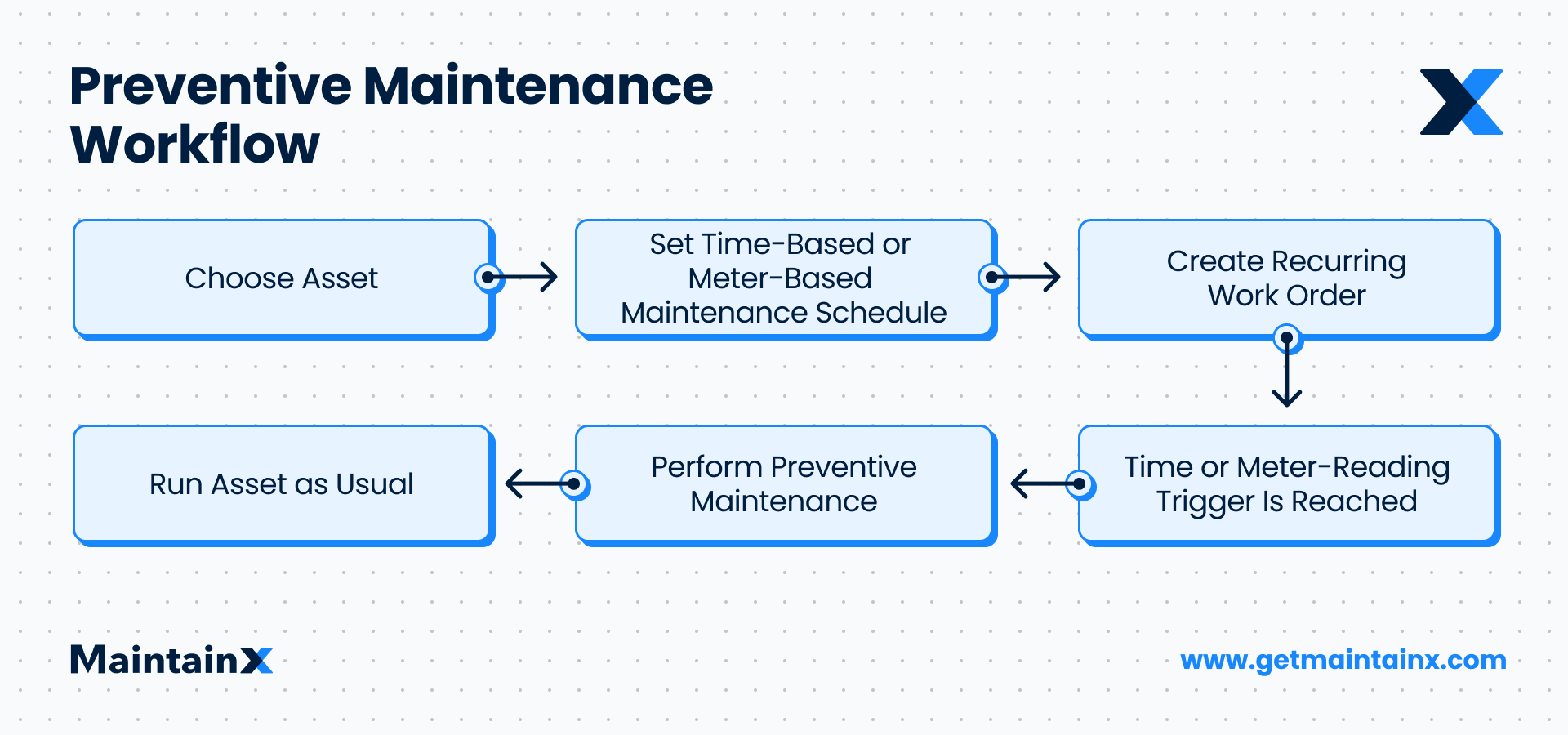
Preventive Maintenance Work Orders (PMs)
Preventive maintenance work orders (PMs) are often scheduled by date—a week, month, or year, depending on the asset or manufacturer guidelines. Manufacturing floor PMs include parts cleaning and adjustments, lubrication, increased air pressure, battery checks, and parts replacements, such as belts and valves.
PM plans also involve maintaining accurate records of inspections and servicing and knowing the lifespan of each part to understand the replacement frequency. These records help maintenance teams anticipate the appropriate time to change parts and diagnose problems.
CMMS software, also referred to as enterprise asset management systems, can act as preventive maintenance software to collect and organize this information for maintenance technicians. This type of management software also provides leaders with key performance indicators to track maintenance work order completion, time on task, downtime, and supply-chain inventory. Now, let’s delve deeper into preventive vs. predictive maintenance.
Benefits of Preventive Maintenance
Preventive maintenance offers companies several essential benefits, including:
- Increased Equipment Reliability and Asset Lifespan: Preventive maintenance schedules ensure that critical assets are running according to manufacturer and consumer guidelines. When poorly performing parts are updated, assets will run at a steady productivity level throughout the year. This reduces the frequency of capital expenditures needed to purchase new equipment.
- Decreased Downtime: Failure often equals reduced productivity. Poor maintenance strategies can reduce production capacity by 20 percent. Modern PM solutions allow operational managers to digitize essential equipment details, assign recurring work orders, and review asset history in real time from their mobile devices.
- Reduced Costs: Decreased equipment failures and fixes translate to less incurred emergency maintenance costs. Using equipment to the point of failure can cost 10X more than performing periodic maintenance.
- Increased Employee and Customer Safety: The more often assets are checked, the less likely dangerous problems will occur. Businesses that follow preventive maintenance schedules reduce unexpected breakdowns, health hazards, and liability lawsuits.
Ideally, preventive maintenance checklists and schedules will prevent equipment failure before it occurs. PM saves time, reduces unnecessary maintenance costs, and keeps businesses running efficiently and productively.
Does Preventive Maintenance Eliminate All Breakdowns?
While preventive maintenance cannot eliminate all breakdowns—because stuff does happen—successful preventive maintenance programs significantly reduce the occurrence of costly equipment failure, unplanned downtime, and dangerous safety hazards
What Is Predictive Maintenance?
Predictive Maintenance (PdM) is also proactive maintenance and involves using a form of measurement to schedule maintenance. Predictive maintenance uses condition-monitoring equipment to determine an asset’s condition and performance in real-time to determine when maintenance should be scheduled and performed. Predictive maintenance relies on conditions or measurements to signal when it is time to perform maintenance.
Measurements often include sensor data on asset temperature, noise level, and vibrations out of the normal. Only when a sensor reaches a specified level will technicians perform predictive maintenance to restore the asset to its proper condition.
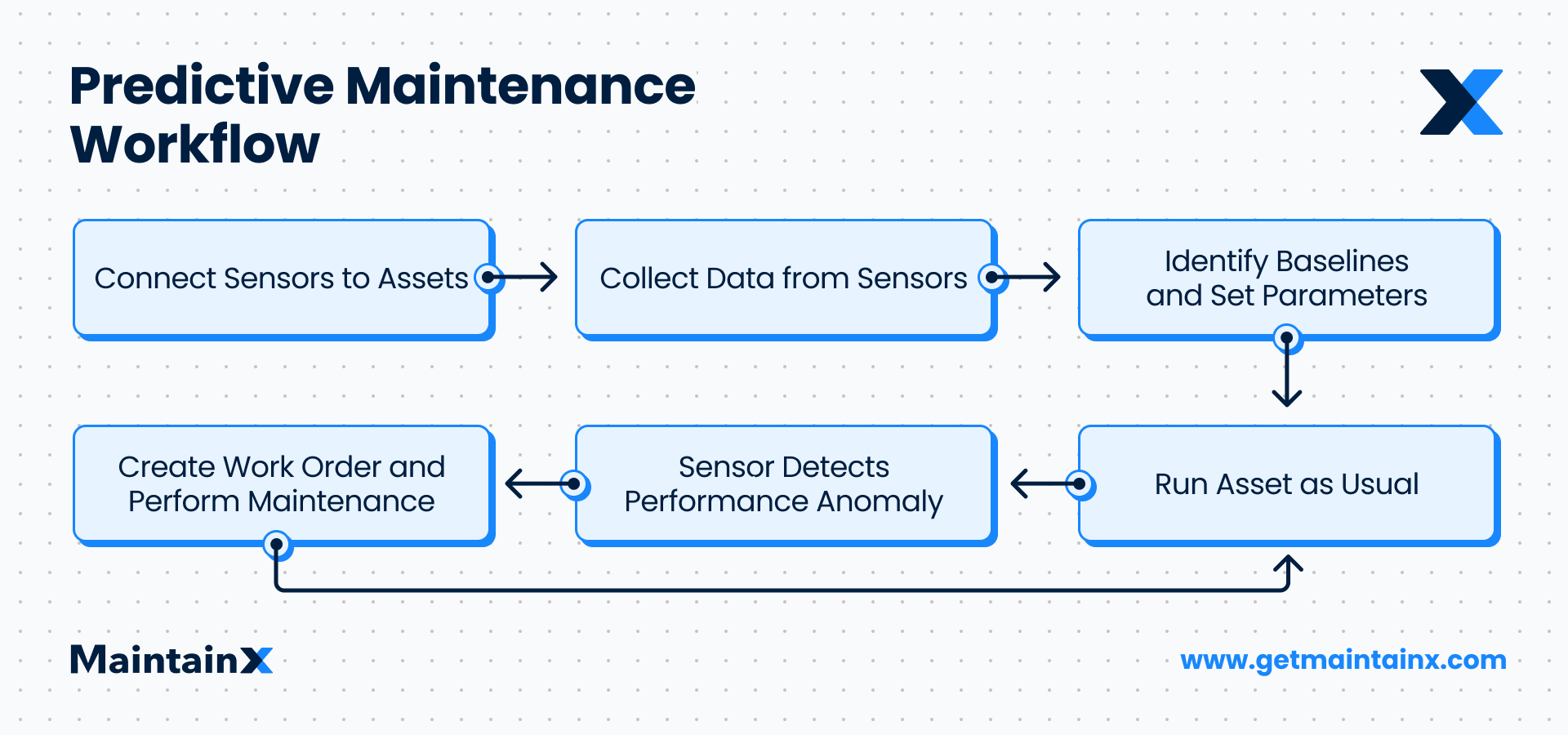
How Does PM Work?
Predictive maintenance programs rely on condition sensors to monitor equipment performance during regular operation to identify and fix possible defects or weaknesses before the machine breaks down or fails.
Predictive maintenance can decrease maintenance frequency to prevent costly and inefficient reactive and run-to-failure maintenance, without incurring costs associated with doing too much preventive maintenance.
Predictive maintenance uses sensors (often referred to as condition-monitoring equipment) to capture information. Equipment condition sensors can provide information on, for example, machine vibrations, oil use, and quality, and thermal imaging, to determine when to perform maintenance to prevent equipment failure.
Benefits of Predictive Maintenance
When sensors work effectively, predictive maintenance occurs only when required, with cost savings on parts and employee hours. However, sensors and other condition-monitoring devices can be expensive and need more skilled employees to analyze the device data.
Effective PdM lowers maintenance costs, extends equipment life, reduces downtime, and improves production quality by addressing problems before equipment failures. However, to realize these benefits, a robust digital infrastructure needs to be in place.
Using past data, predictive analytics anticipate future outcomes. Data preparation and data quality are critical inputs for any predictive model. The more high-quality data we can feed into a predictive model, the better its accuracy.
Predictive maintenance strategies ensure that workers only take equipment offline for necessary maintenance to prevent failure. This creates a reduction in the total time and cost spent maintaining equipment.
Examples of Predictive Maintenance
- Utility departments use drones to find trees too close to power and utility lines.
- Fleet vehicles that include “drowsiness detection systems” to monitor steering wheel angle, lane deviation, driving time, and road conditions.
- Restaurants use thermometers to check that the kitchen cooks meat according to FDA guidelines, and thermostats to ensure that food storage meets regulatory guidelines.
Though none of these tasks is rocket science, effective PdM can reduce failure, increase safety, and extend asset life by up to 60 percent. Predictive maintenance strategies work best with a) Assets critical to a company’s operations and b) Equipment with condition-monitoring sensors to detect failure modes.
Frequently Asked Questions
What Are the Disadvantages of Predictive Maintenance?
Technical experience is needed to interpret real-time condition-monitoring data accurately, and condition-monitoring equipment may have a high upfront cost for organizations.
What Is the Difference between Preventive Maintenance and Routine Maintenance?
Although we may use the terms “preventive” and “routine” interchangeably, they are different. Routine maintenance involves small maintenance tasks requiring only minimal skills or job training and regular equipment inspections for everyday wear and tear.
Alternatively, preventative maintenance is more systematic, involving inspection and corrections to prevent failures. Preventive maintenance generally takes longer than routine maintenance and may require higher maintenance costs and more expertise. However, both routine and preventive maintenance work proactively to avoid costly and inefficient breakdowns and potentially dangerous failures.
Why Is Preventive Maintenance Better than Breakdown Maintenance?
The primary goal of a PM program is to prevent equipment failure before it happens. Regular preventive maintenance increases the lifetime of assets and reduces repairs and replacement. As previously mentioned, unplanned breakdown maintenance can be hazardous. Blown-out tires and failed brakes are dangerous, and inconvenient, and may not allow optimal repairs. Thus, preventive maintenance can be better than breakdown maintenance from a safety standpoint.
Preventive maintenance tasks also keep machines running efficiently, safely, and according to manufacturer guidelines. Running a machine without regular inspections is like riding a bicycle without checking its tires. Riding the bike will get harder and harder as its tires lose pressure over time. Eventually, the cyclist will be riding on nothing but the rims! At the very least, the bicycle will not operate as smoothly as it can. Similarly, the usual wear and tear of facility equipment, without regular maintenance, can lower machine efficiency over time. Preventive maintenance conserves asset lifespans.
Which Is It? Preventive vs. Predictive Maintenance
What is the difference between preventive vs. predictive maintenance? Though PM and PdM aim to achieve similar goals, they involve substantially different, budgets, resources, and technologies. Maintenance managers must understand the real-time performance implications of the different maintenance strategies they choose and implement the practices necessary to support each plan.
Get a CMMS for Your Work Order Management
For example, in a proactive program, preventive and predictive maintenance activities should be accompanied by equipment monitoring and analysis. Modern computerized maintenance management systems (CMMS) collect data to provide real-time dashboards and report on equipment costs, equipment failures, mean-time-to-repair, work order status, and more. MaintainX, provide peace of mind for businesses wanting to improve their overall maintenance operations with user-friendly work order software.
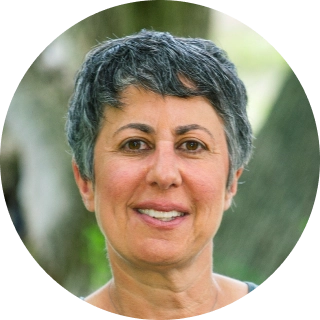
Caroline Eisner
Caroline Eisner is a writer and editor with experience across the profit and nonprofit sectors, government, education, and financial organizations. She has held leadership positions in K16 institutions and has led large-scale digital projects, interactive websites, and a business writing consultancy.
See MaintainX in action