WORK ORDER MANAGEMENT
Modern workflows for more efficient frontline teams
Streamline maintenance, safety, and operations with the world’s most intuitive work order system.
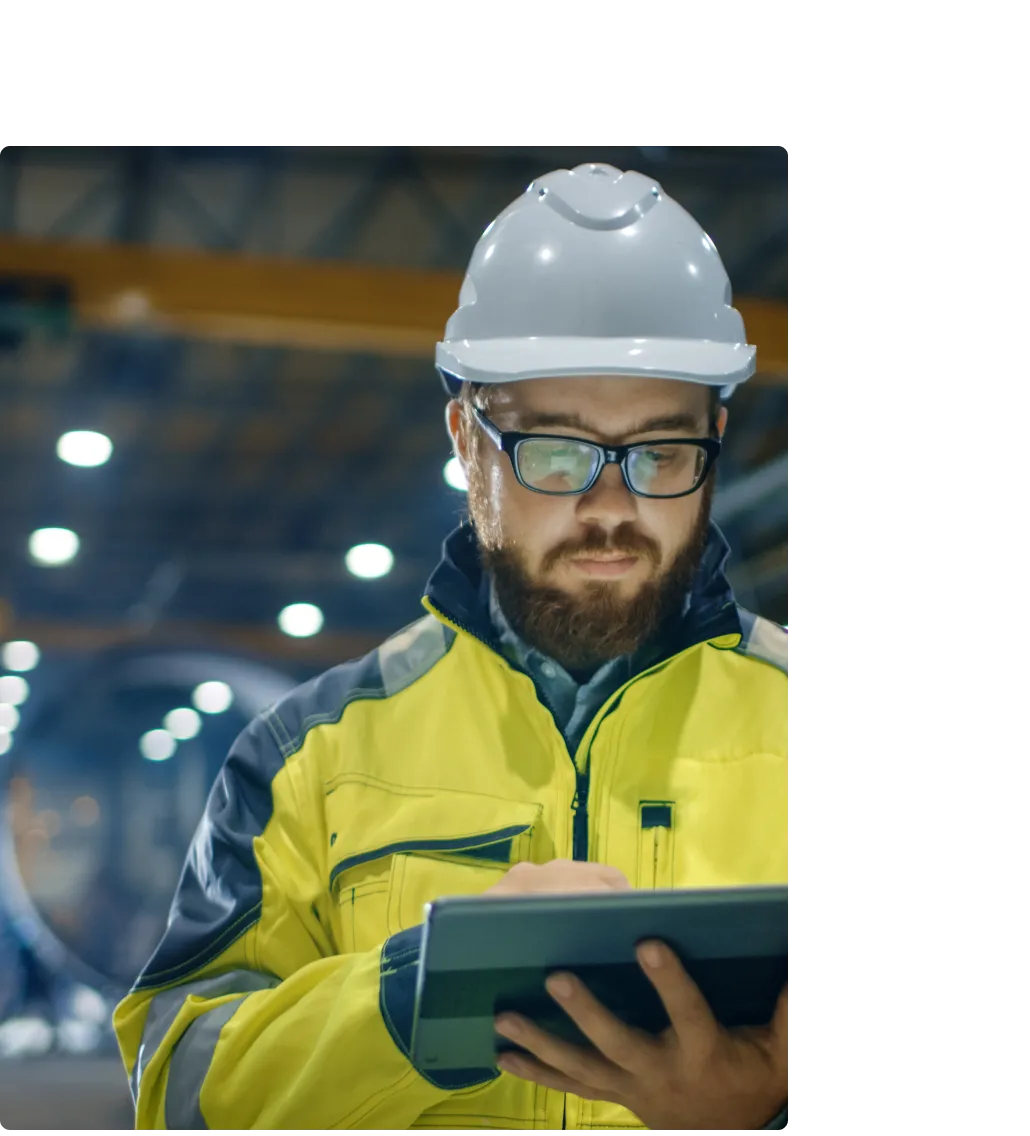

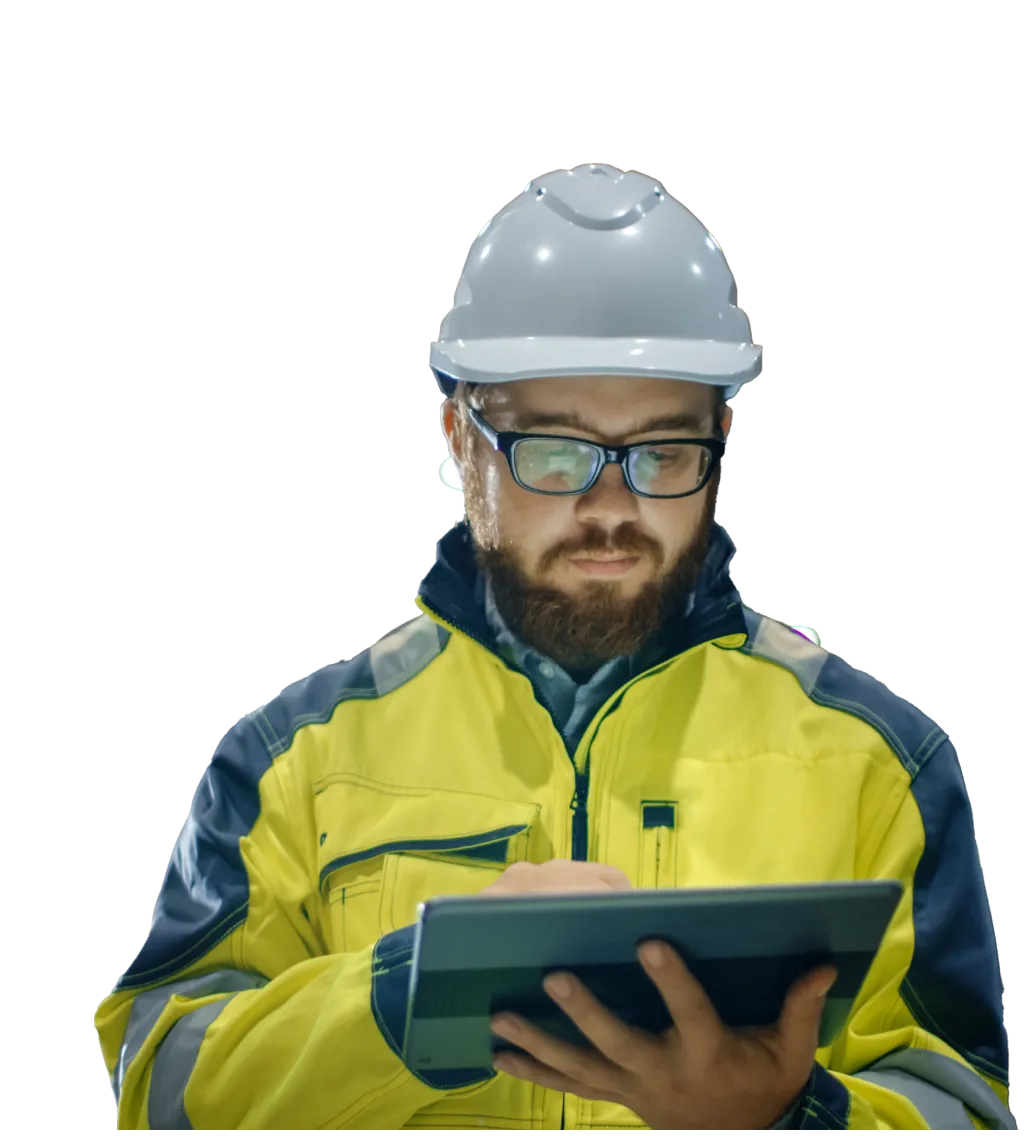
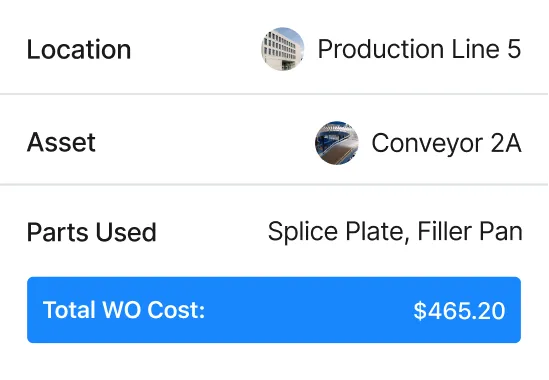
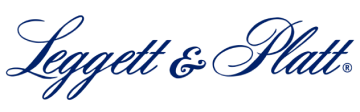
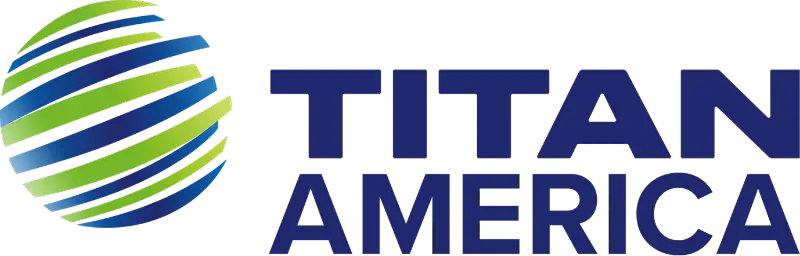
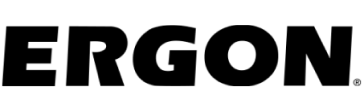

Our clients using MaintainX report
(mean time to repair)
Plan, schedule, and record work all in one place
Create, assign, and prioritize digital work orders for one or many asset, and track everything in one place to keep teams aligned from start to finish.
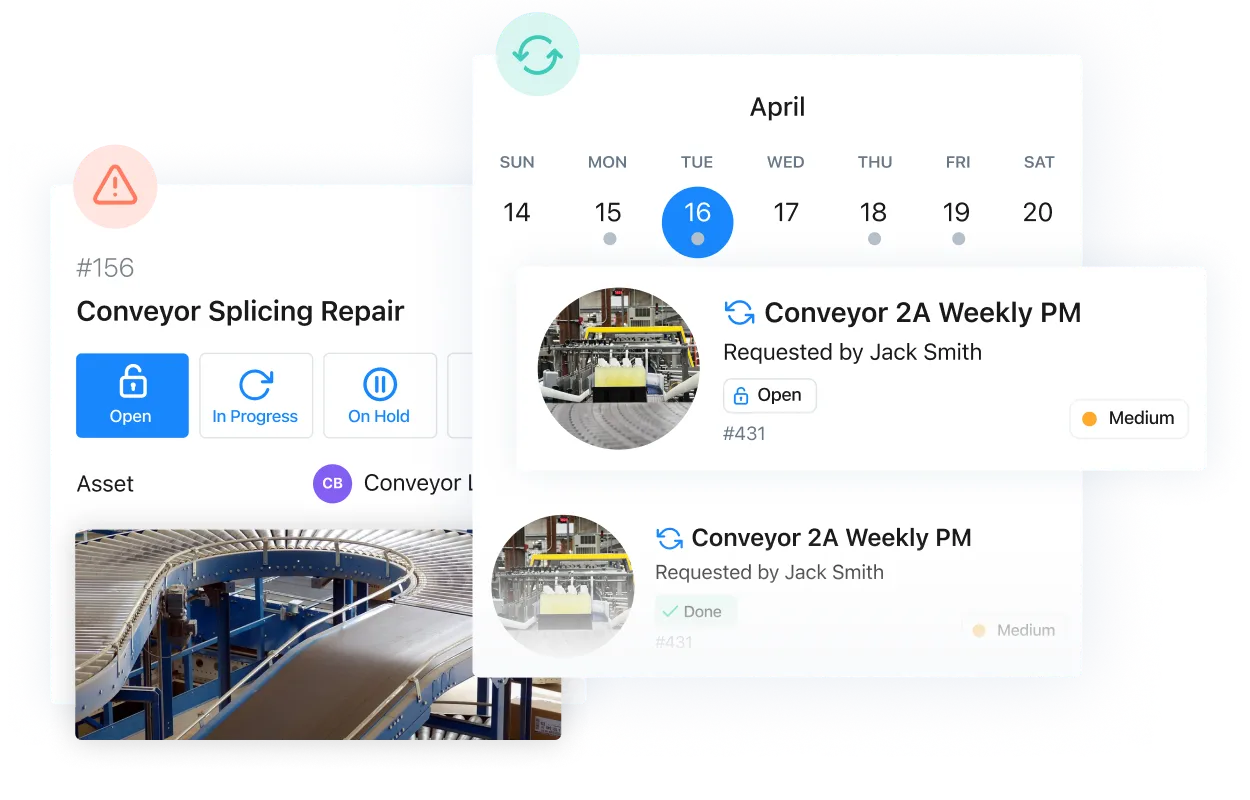
Capture work order data more easily
Make it ridiculously easy for technicians to log work on their mobile devices. Capture the right data every time using pre-filled templates, time tracking, signatures, and required fields.
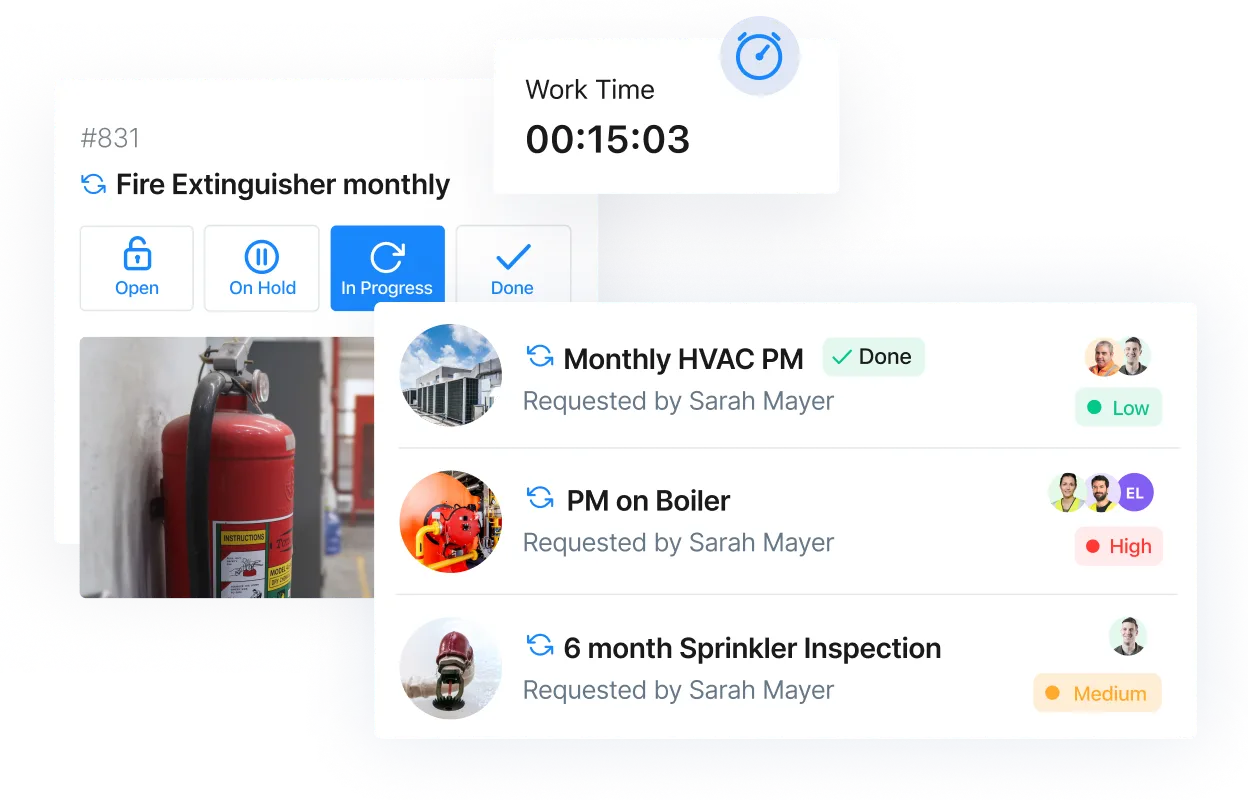
Share work and collaborate seamlessly with vendors
Boost productivity and vendor efficiency with External Work Orders. Collaborate with shared work orders, communicate with comments and files, and track progress and activity — all in MaintainX.
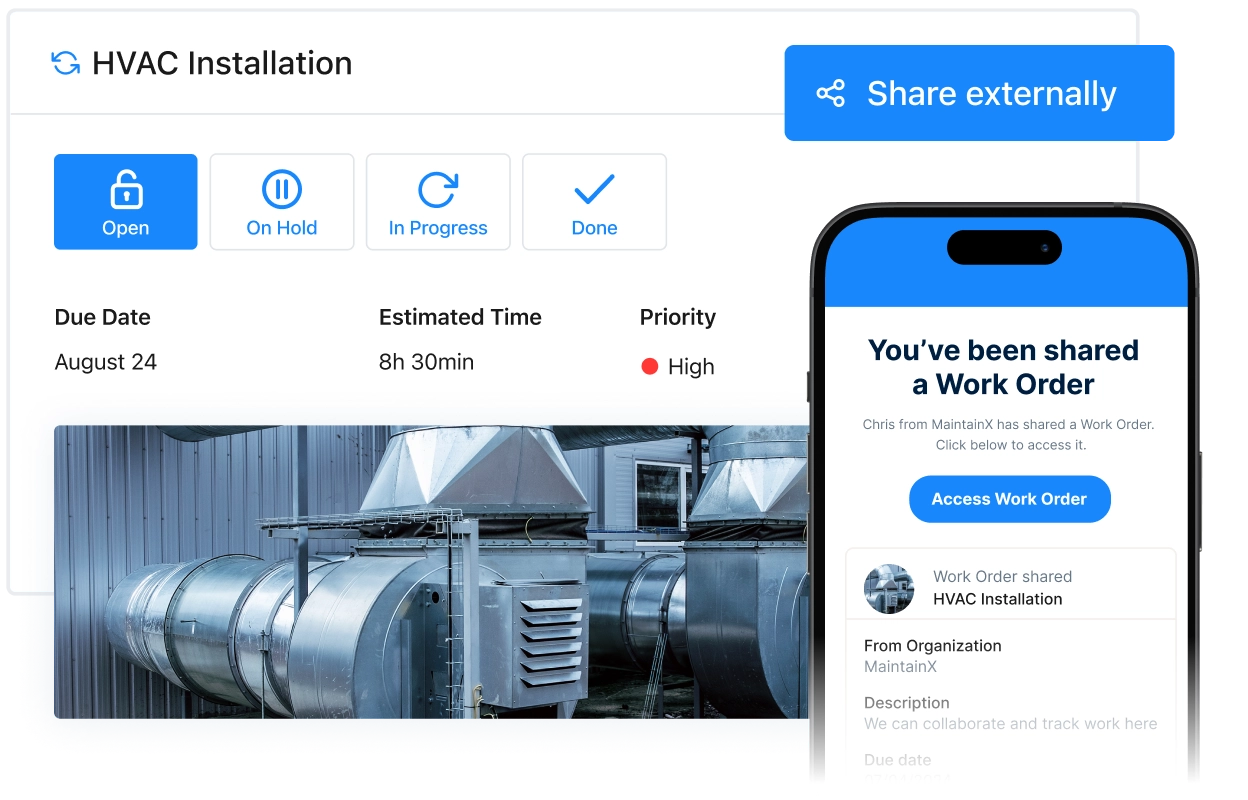
Work smarter with data-driven insights
Get more done using labor hour insights to schedule work more effectively. Report on PM compliance, on-time completion, inspection failures and more to drive continuous improvement.
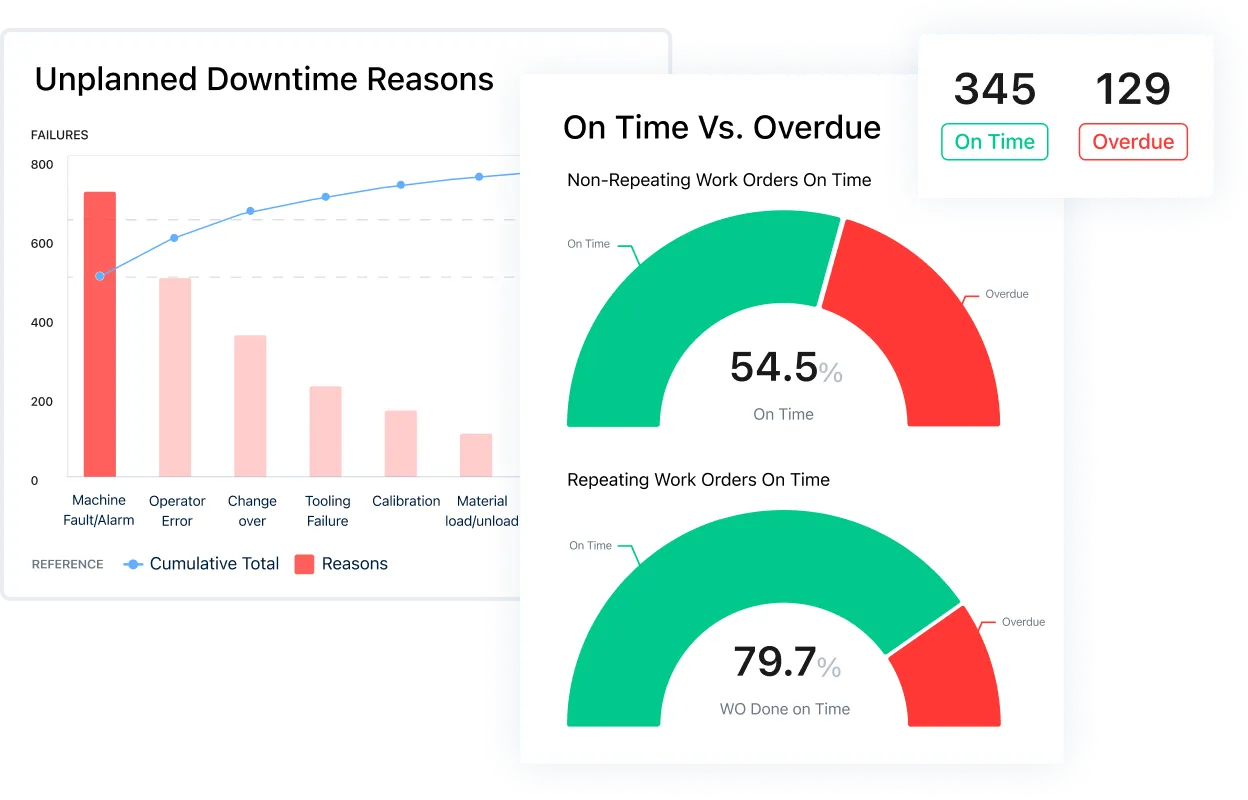
Improve your data quality with standardized templates
Enable your teams to fill out work orders accurately with minimal training using pre-filled templates. Streamline routine or recurring jobs, ensure only the right users perform and approve work, and capture the right data every time.
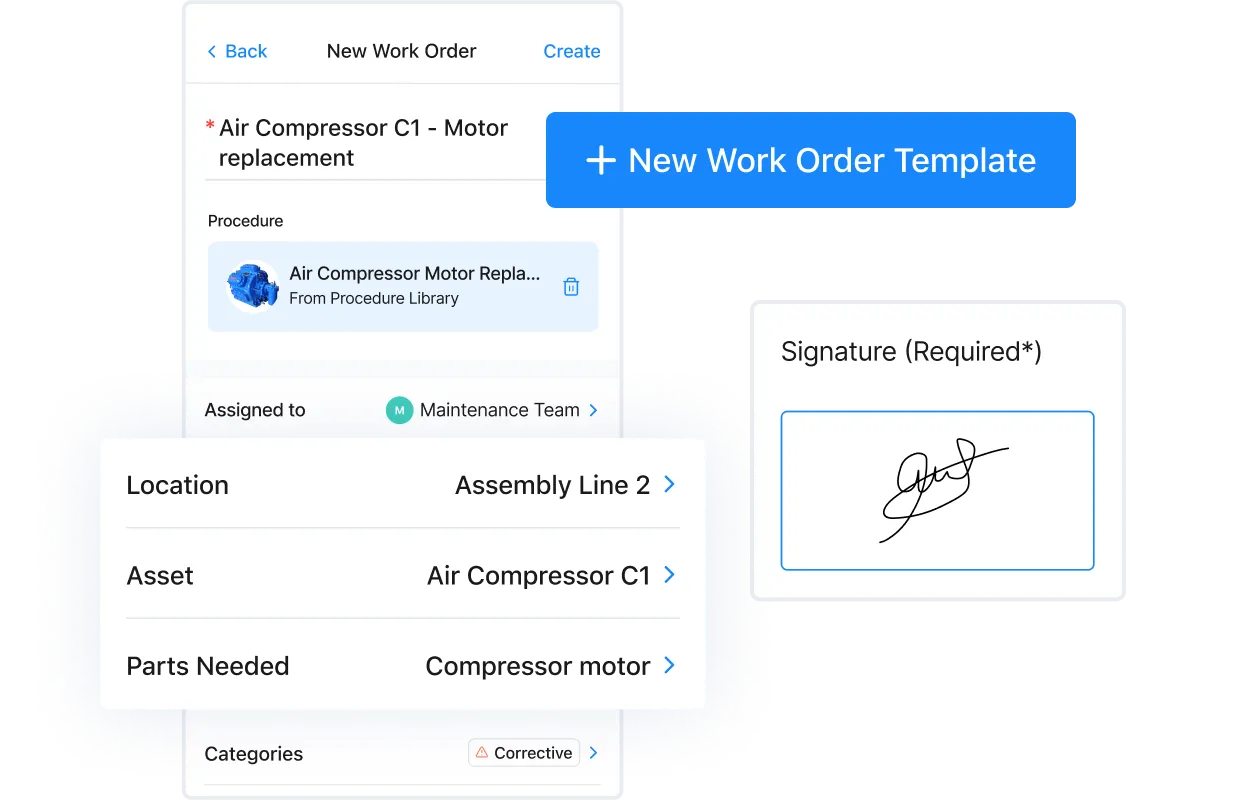
Get AI-powered estimates on time to complete work orders
Improve your workload planning accuracy and efficiency with Smart Time Estimates. Instantly see data-driven estimates on how long a new work order should take to complete – informed by historical data and powered by AI.
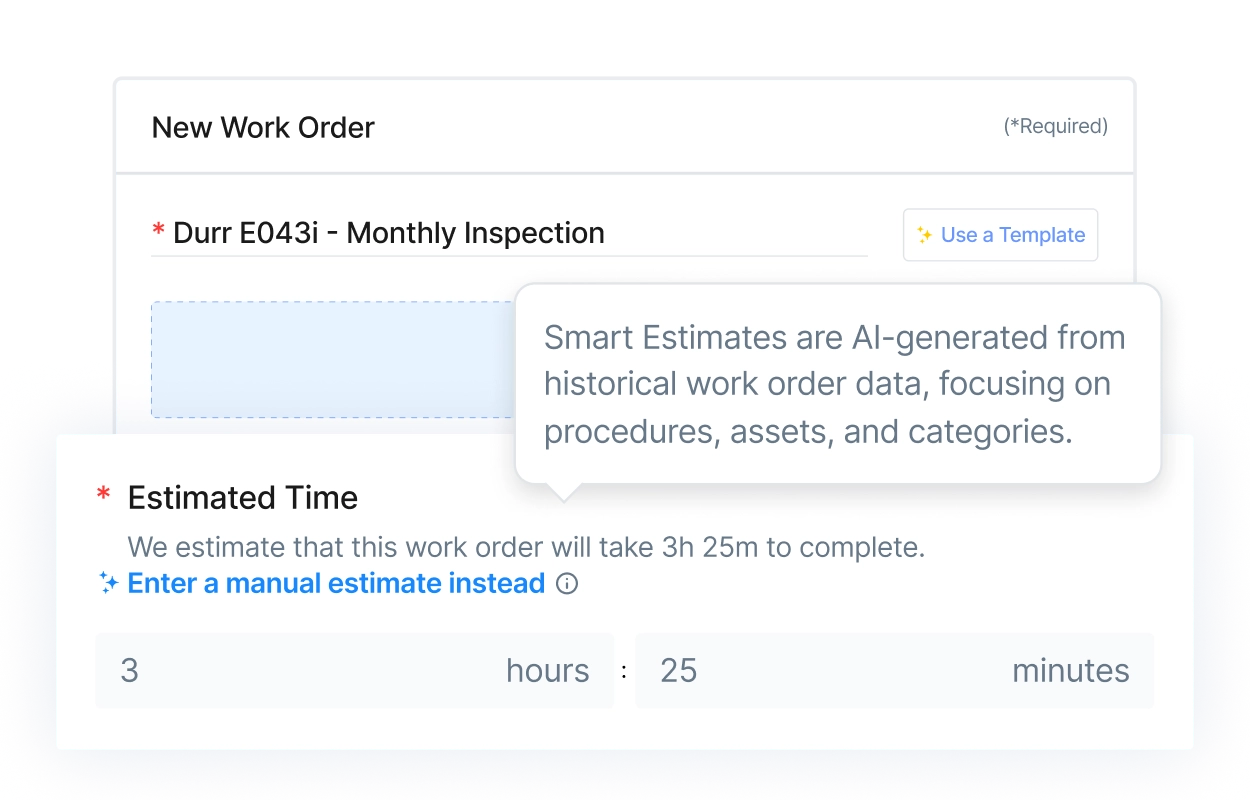
Share photos, comments, and more
Snap photos, annotate them, and save them to each work order to quickly illustrate problems. Add comments and tag other users to collaborate across teams and fix faster.
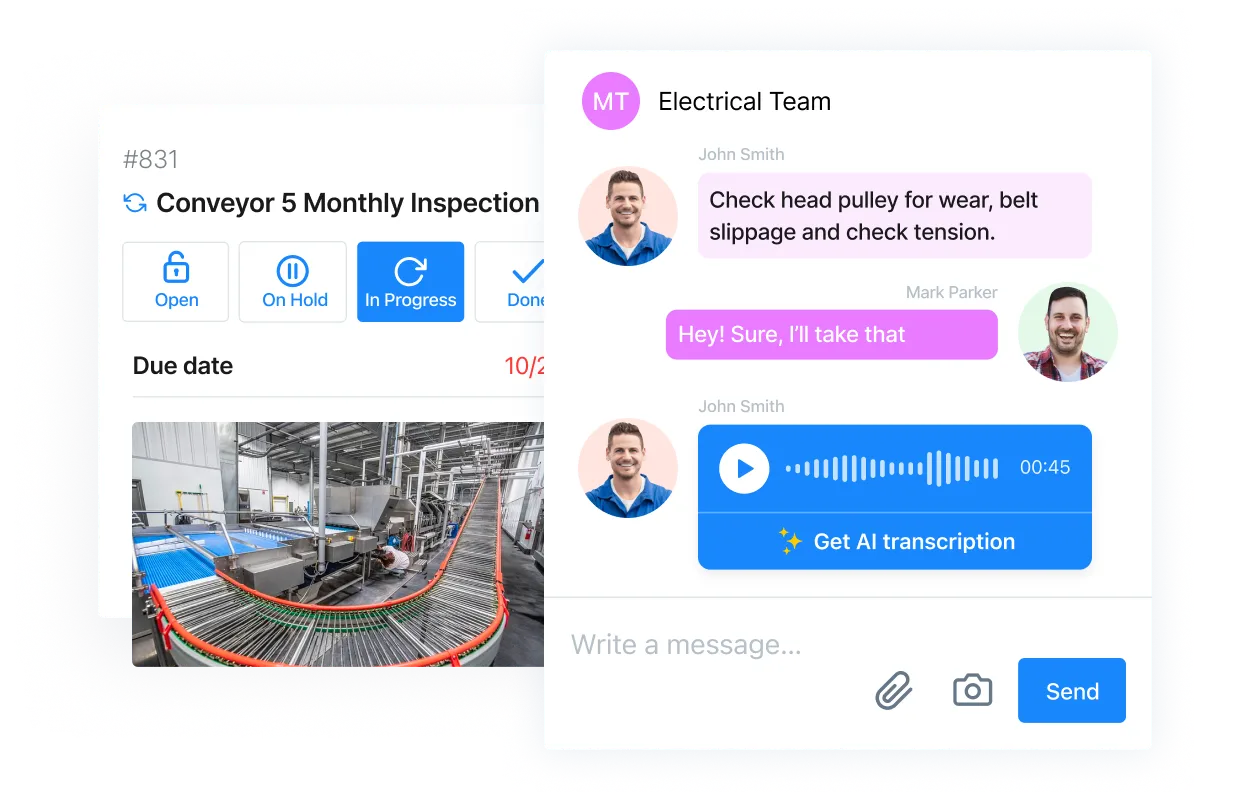
MaintainX is the best software for maintenance and operations across third-party review sites
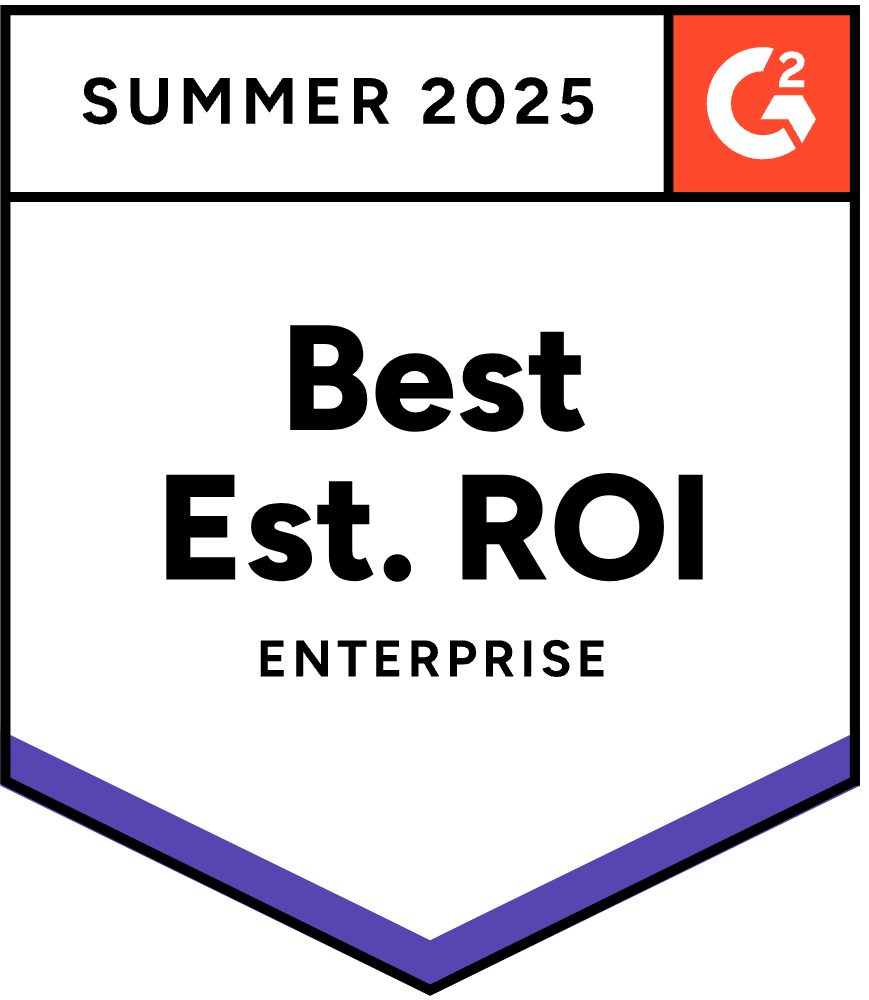
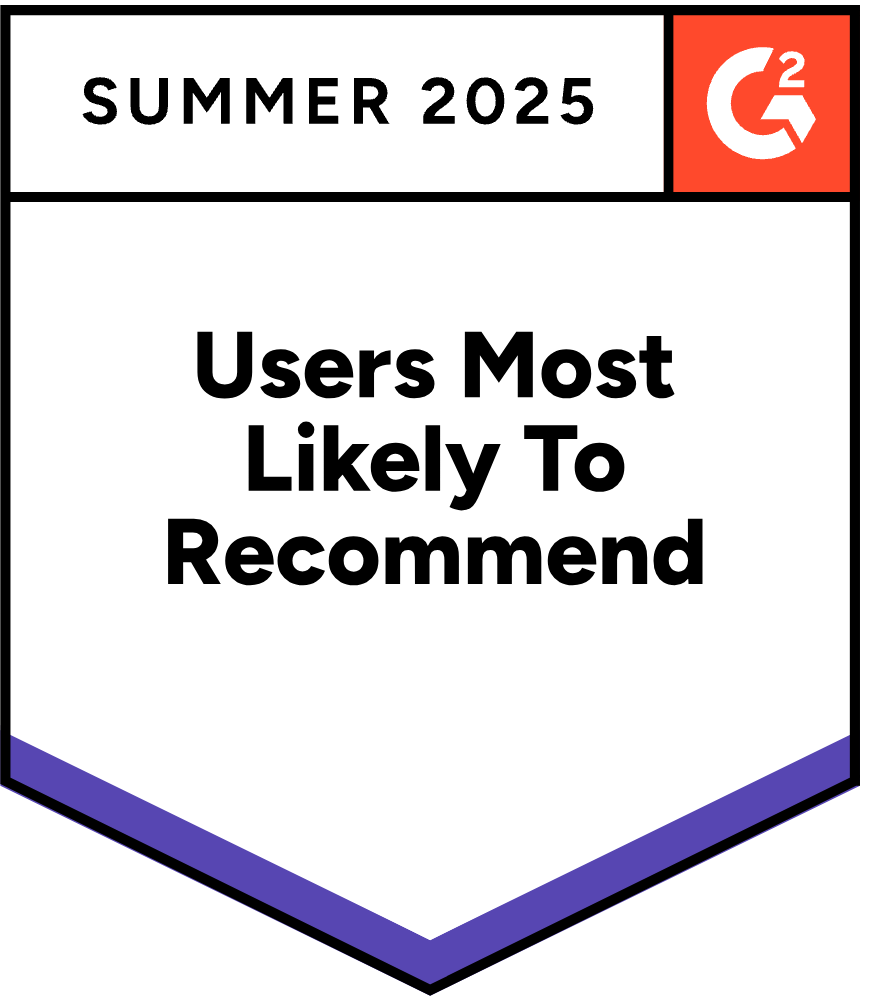
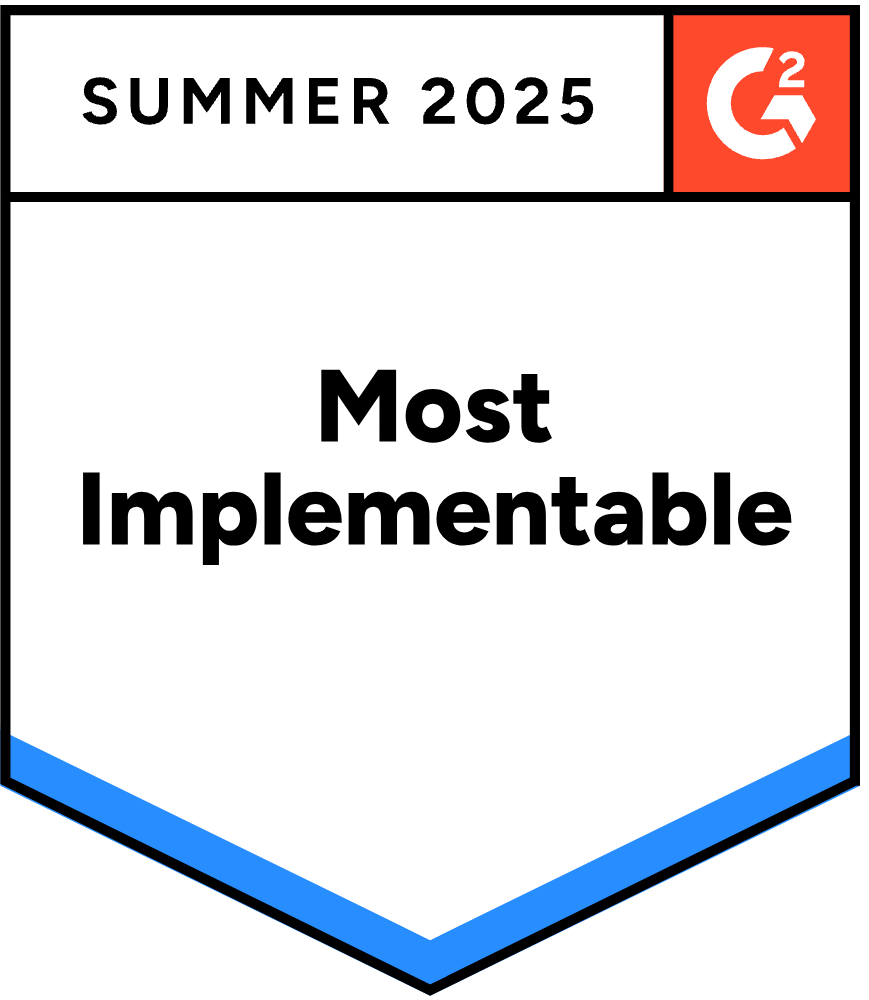
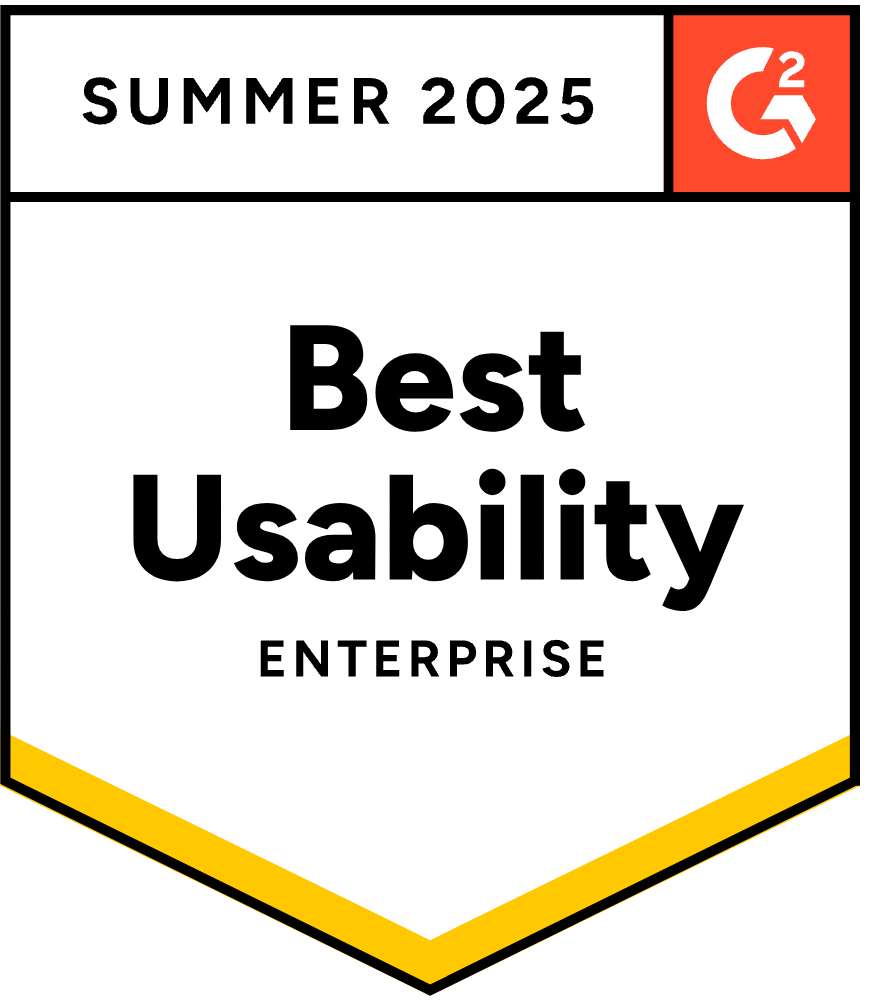
See what customers have to say
Get more done with MaintainX
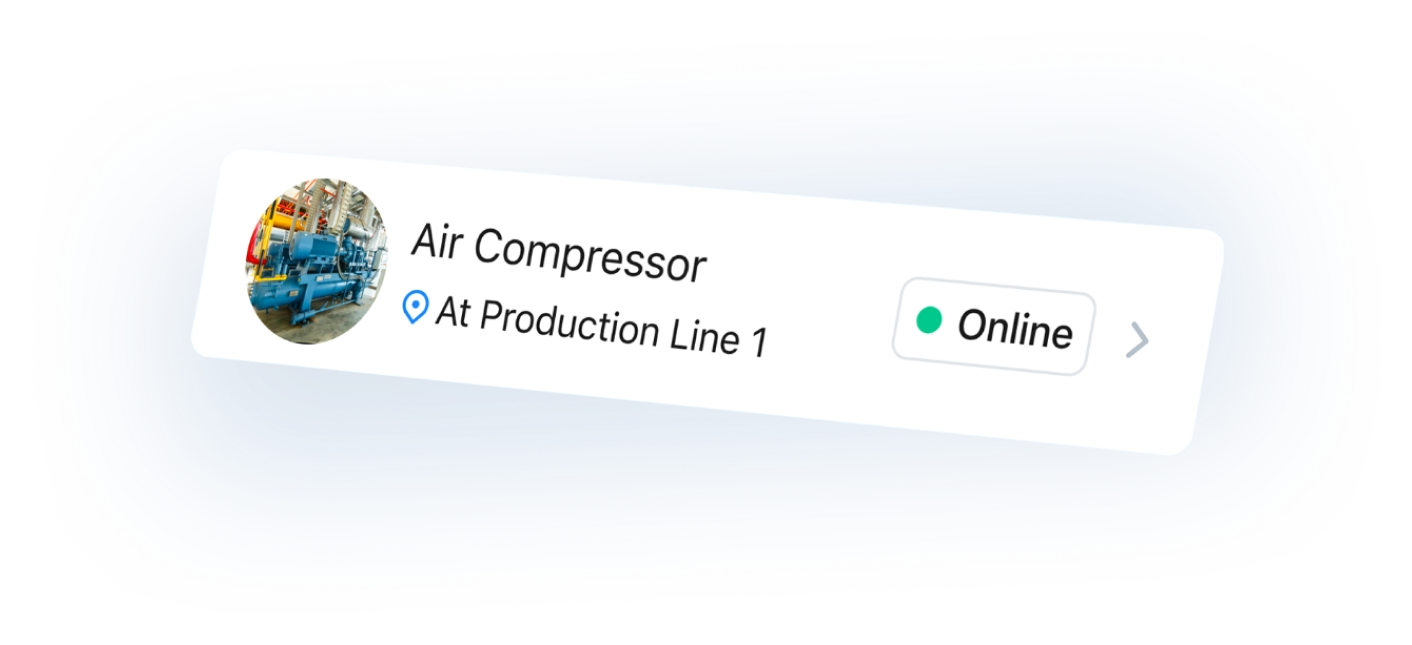
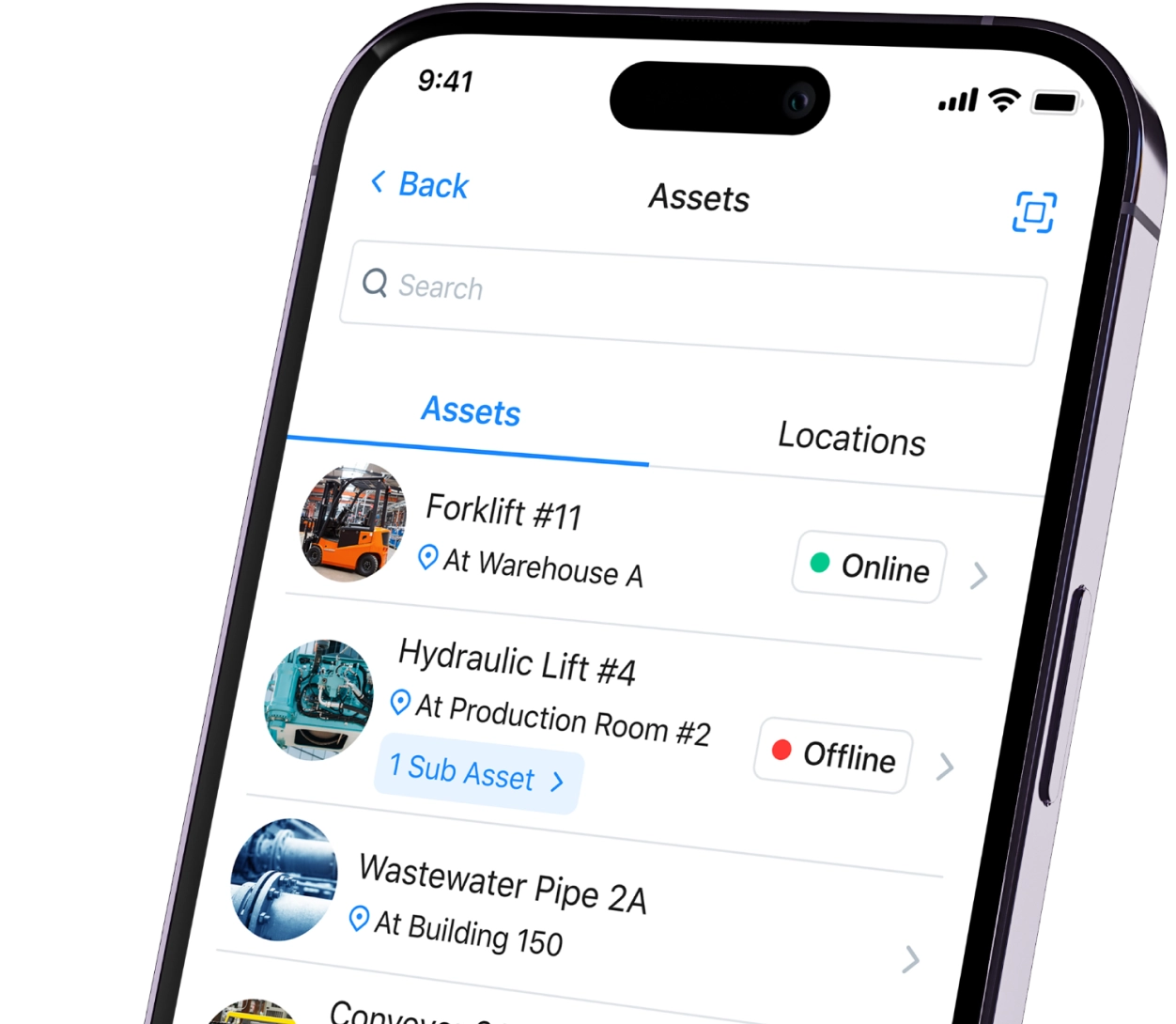