CMMS
Empower your workforce with a CMMS built for the frontline
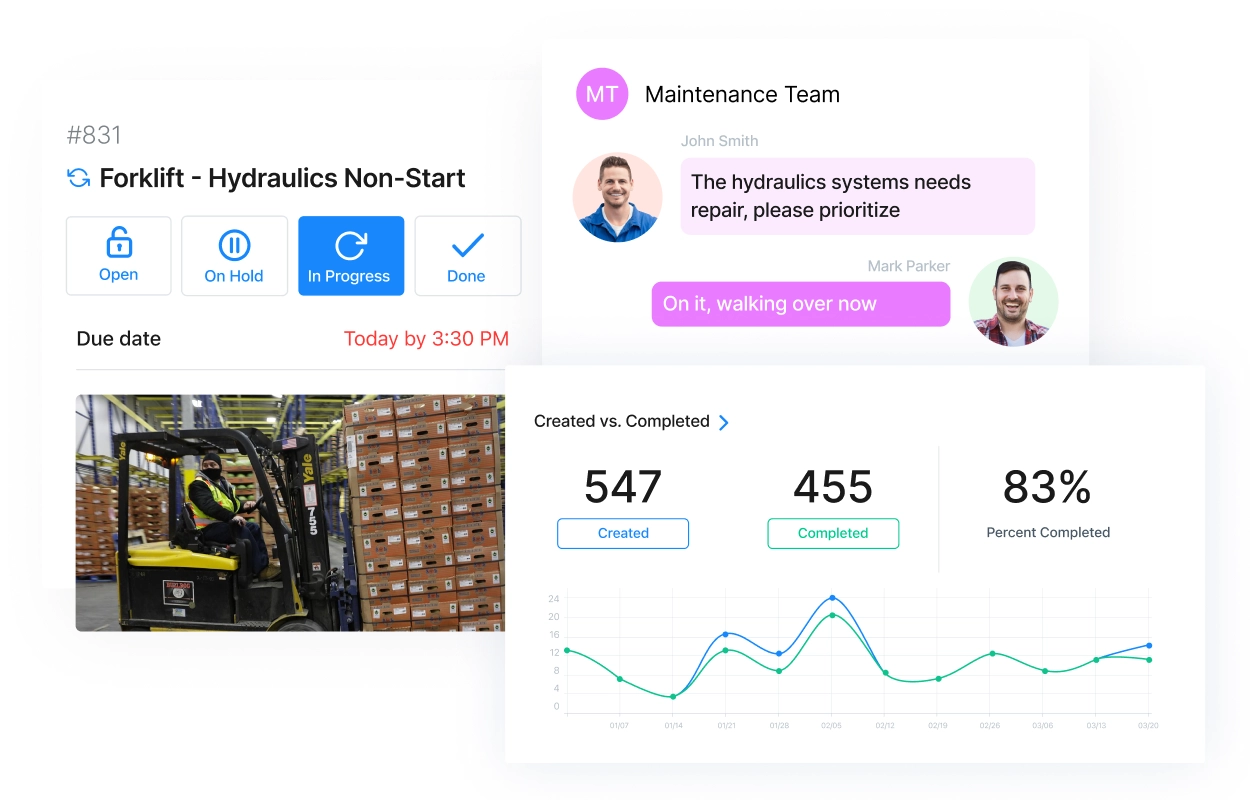
Trusted by leading companies
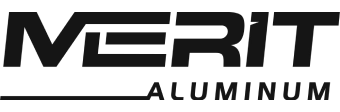
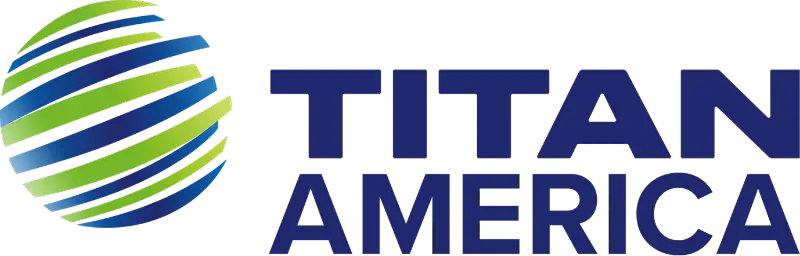
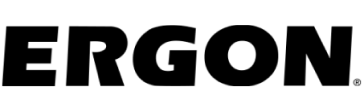
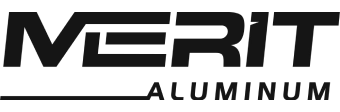
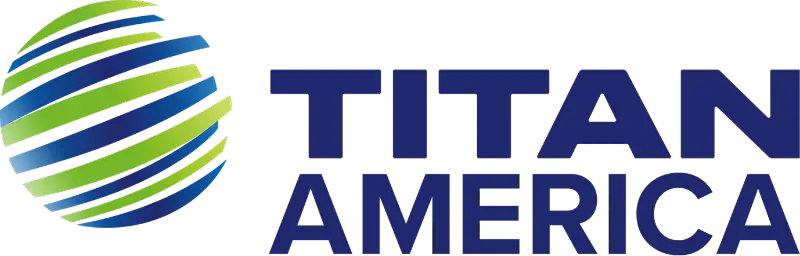
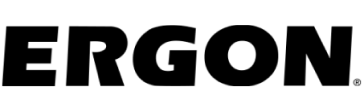
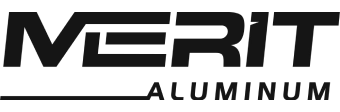
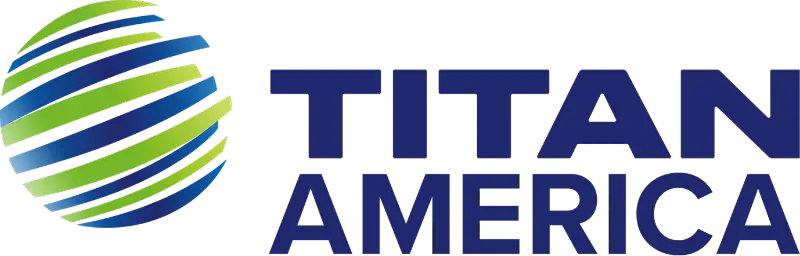
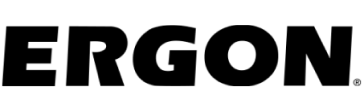
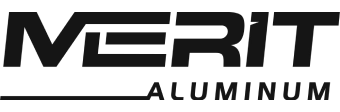
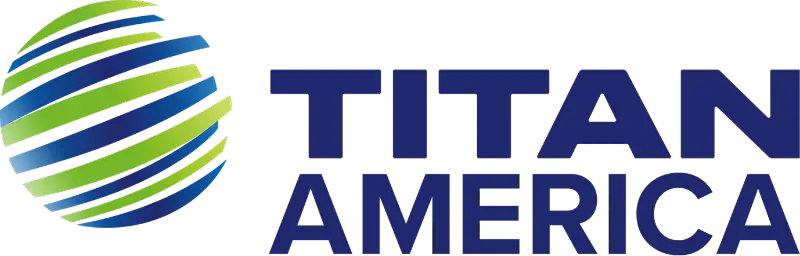
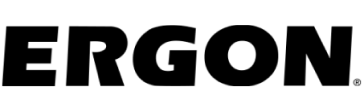
What is a CMMS?
A Computerized Maintenance Management System (CMMS) enables organizations to manage assets, schedule and track work orders, and gain visibility into the process end-to-end. A CMMS helps companies reduce maintenance costs and minimize asset downtime, while increasing safety and work order completion rates.
What MaintainX delivers
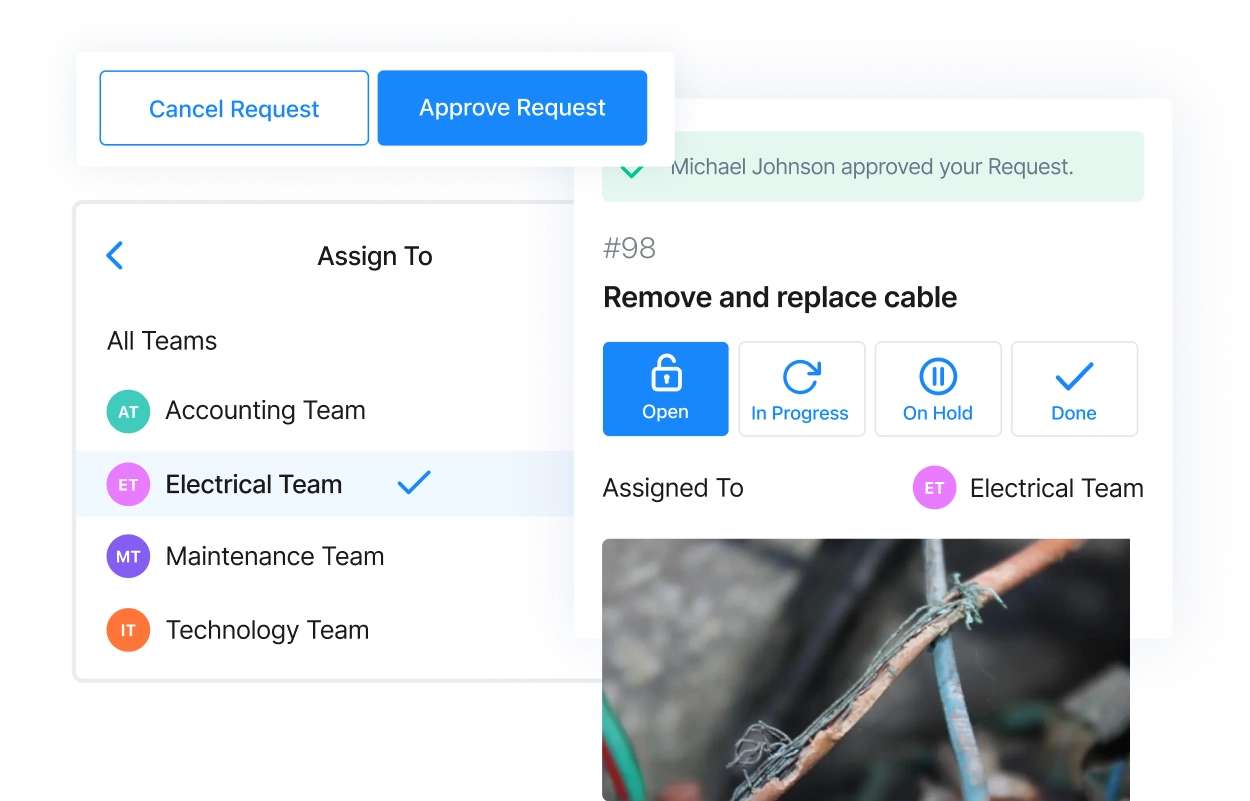
Schedule and track maintenance
Modernize how teams handle all types of maintenance and gain visibility across the process.
Flexible workforce planning
Give frontline and back-office workers an intuitive, easy-to-use platform to manage their work.
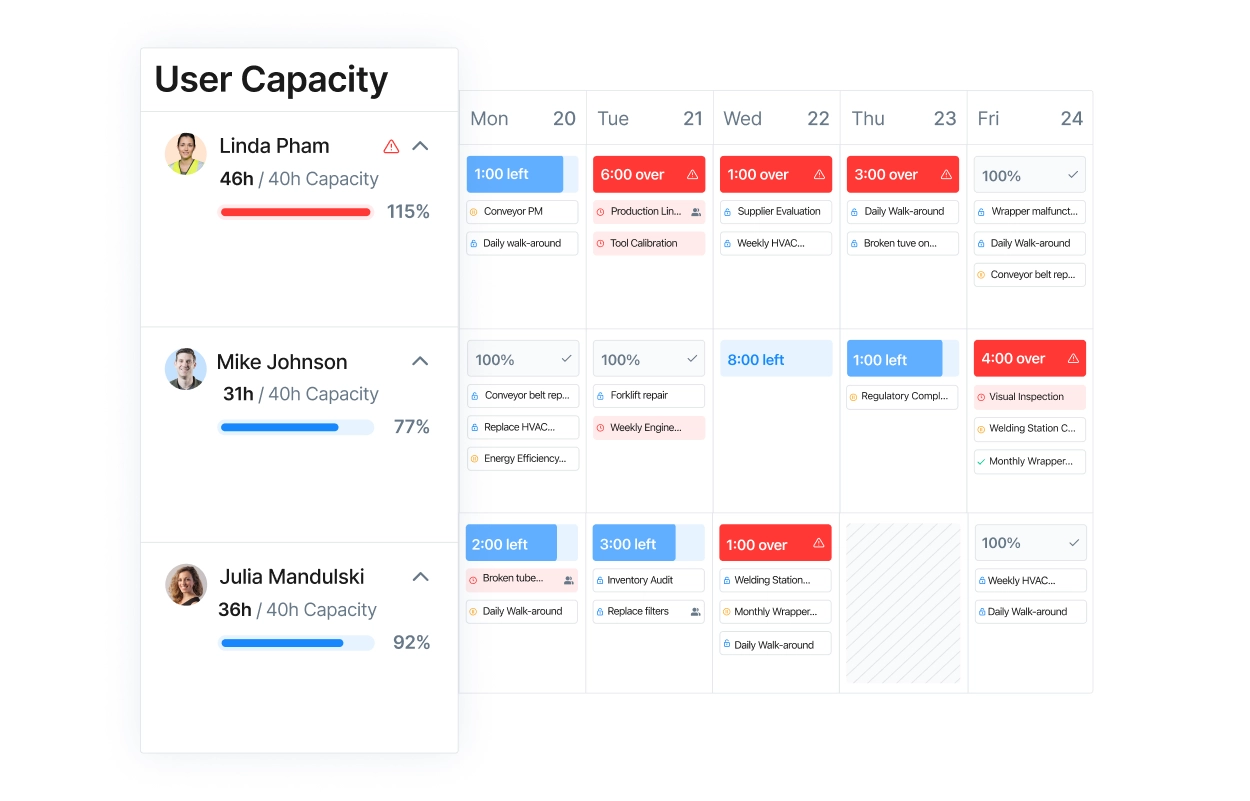
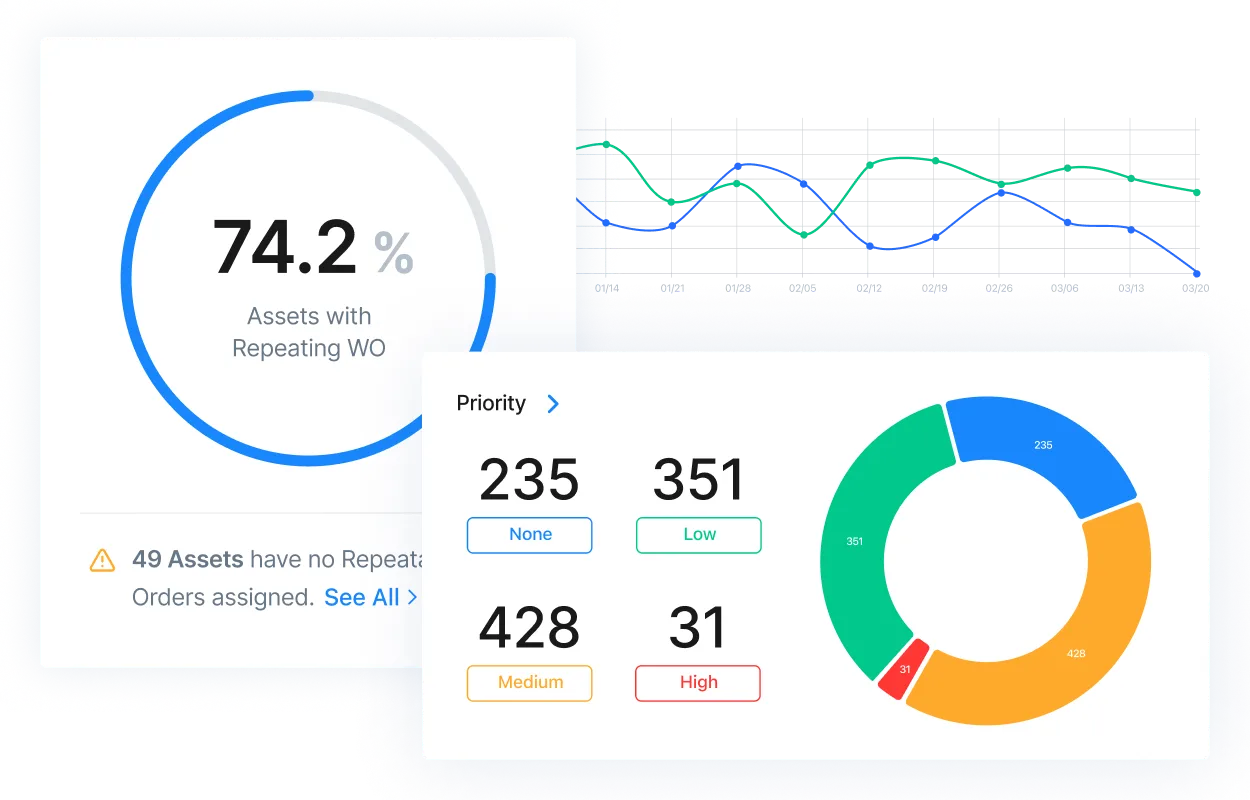
Gain actionable insights from data
Optimize decision making with maintenance data without needing a data analysis background.
Streamline parts management
Save costs and take the hassle out of inventory management. Connect to your ERP system for a complete view of your parts inventory across sites.
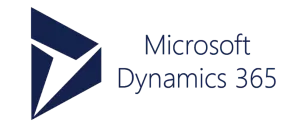
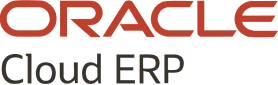
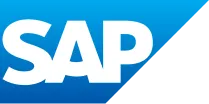
Automate
Save time and avoid downtime by automatically tracking parts inventory and triggering alerts when stock is low.
Monitor
Leverage built-in reports to monitor critical metrics like cost of labor and parts.
Synchronize
Connect to critical ERP systems to synchronize data and purchase orders, and streamline part reordering.
NEW
State of Industrial Maintenance 2025
Tackle 2025’s top challenges with strategies from 1,000+ maintenance leaders. Plus, see which trends and technologies are reshaping industrial maintenance.
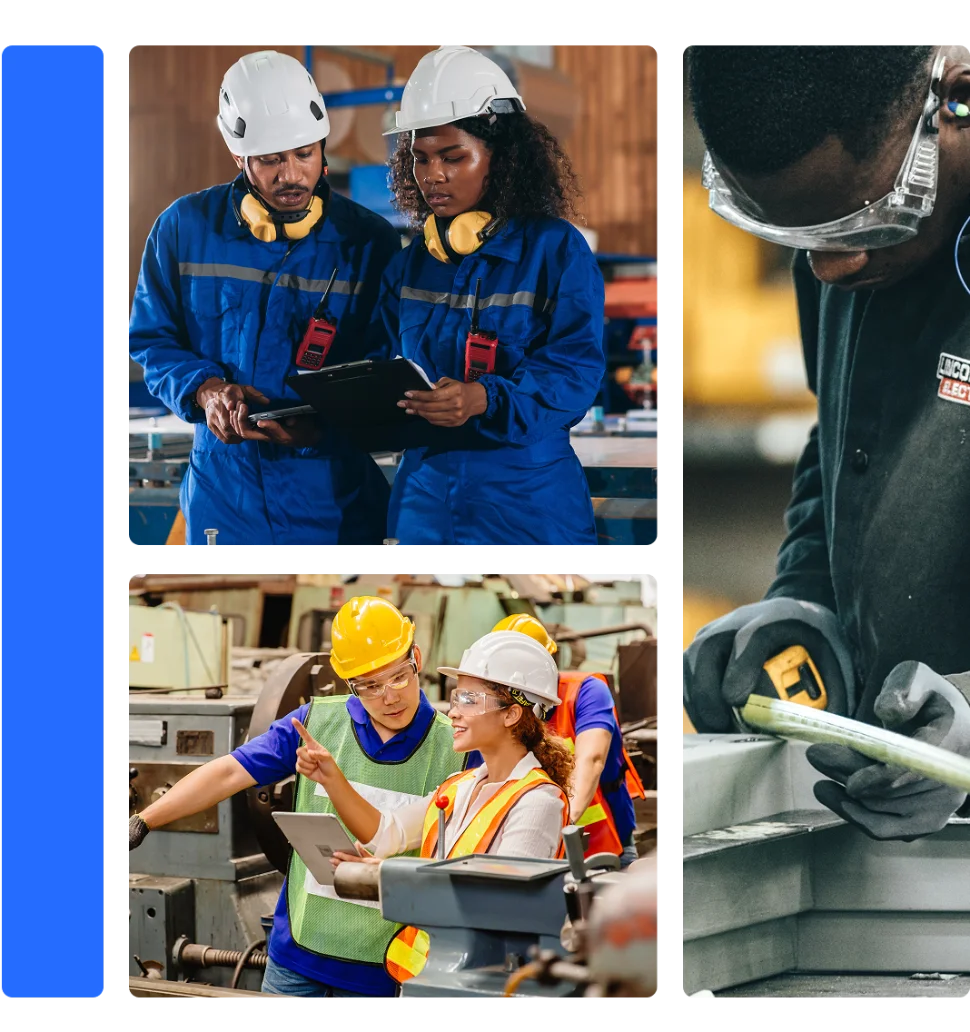
Keep your teams connected
Share knowledge, answer questions, and provide clarification anytime.
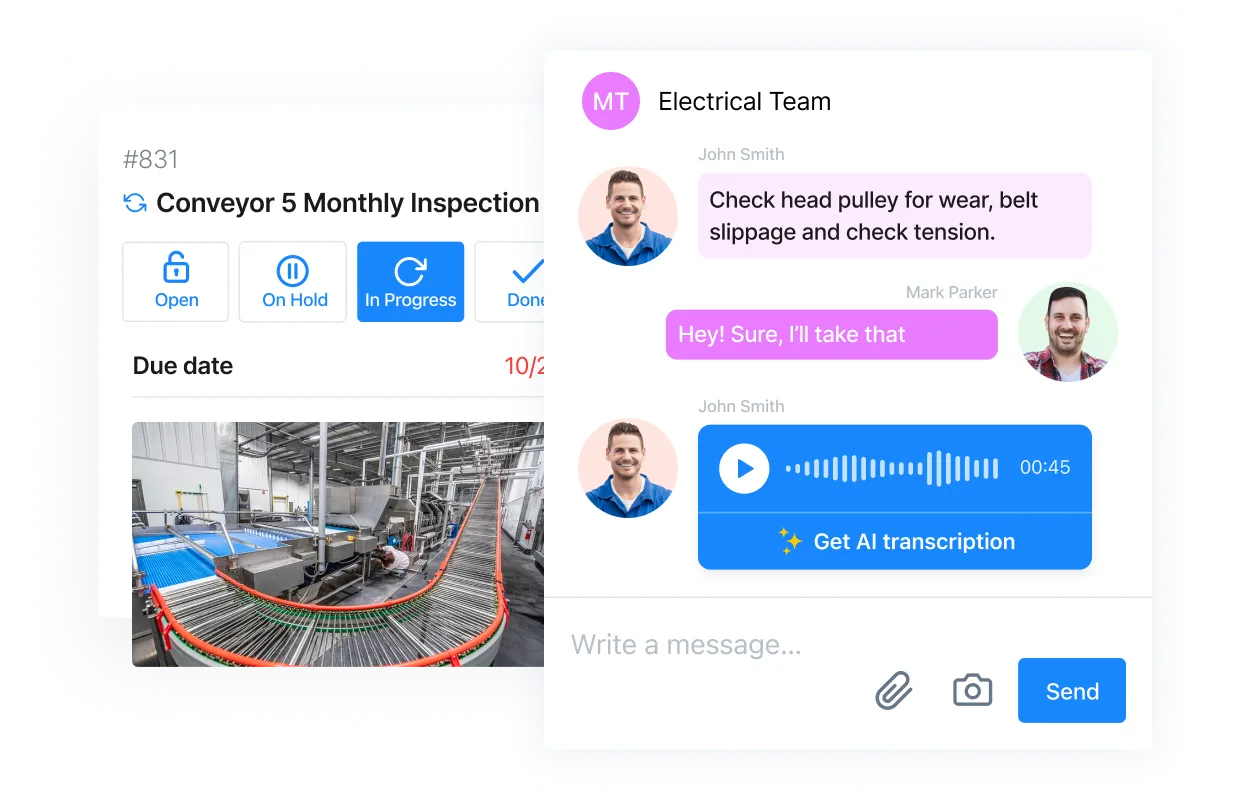
Companies using MaintainX as their CMMS have found:
49%
Increase in inspections completed on time
53%
Improvement in work order completion rates
250h
Saved per year for maintenance managers
55%
Improvement in customer response times
Get more done with MaintainX
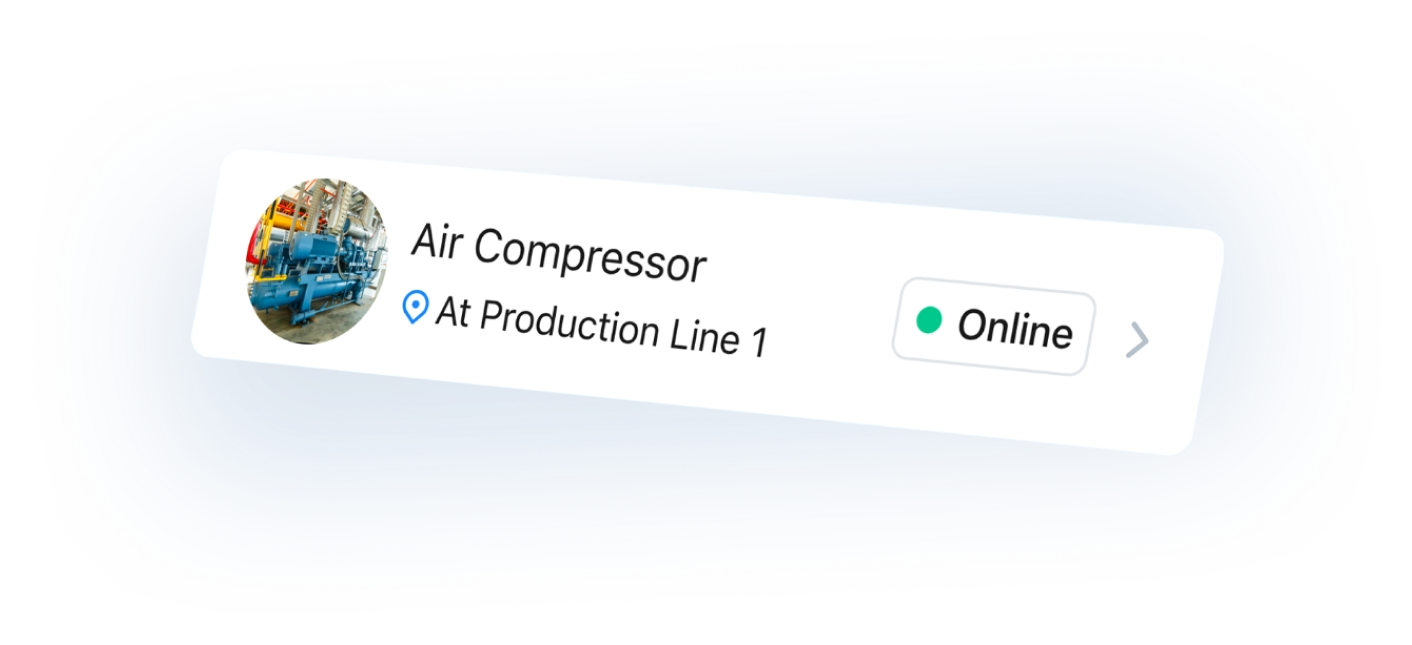
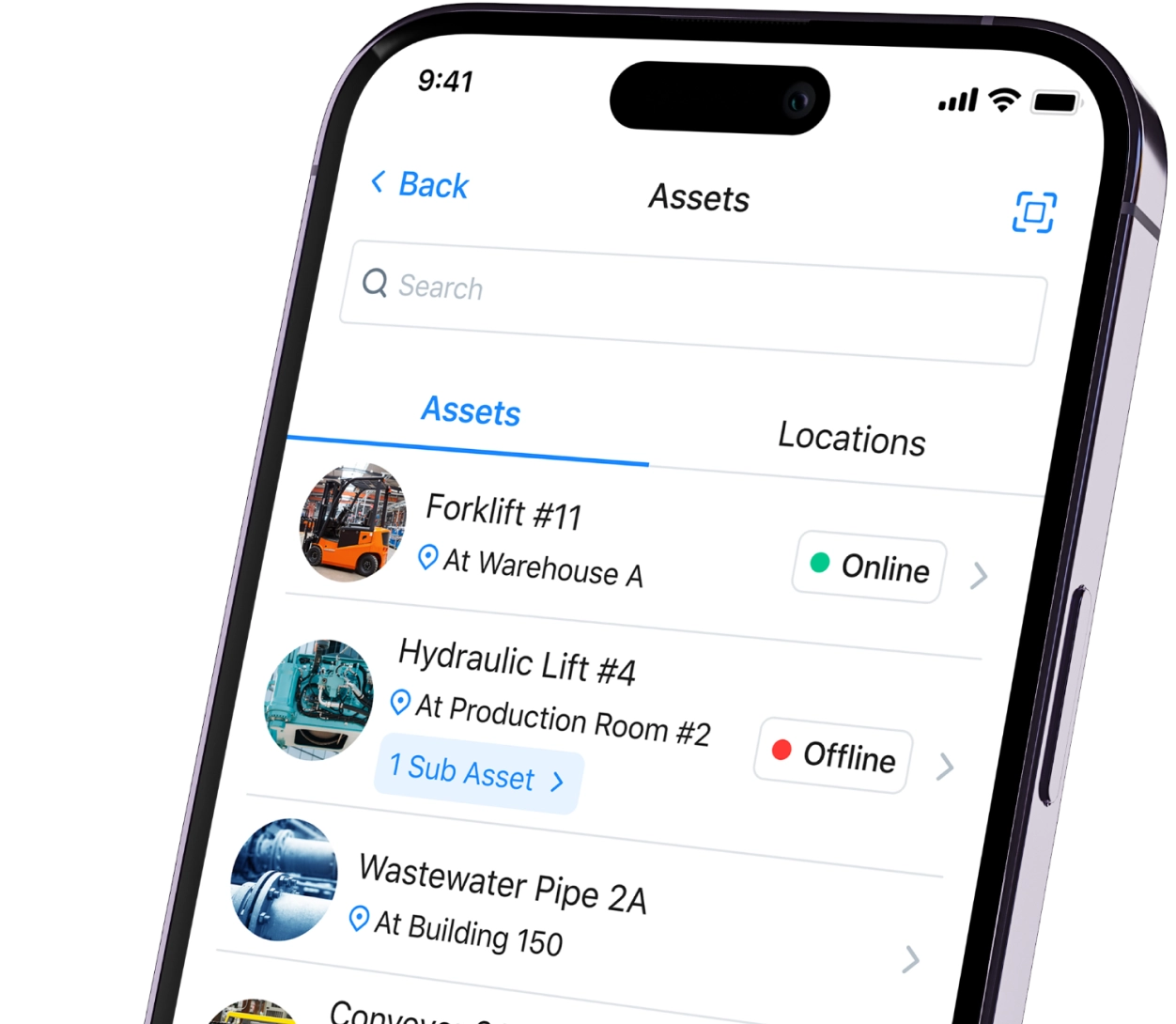