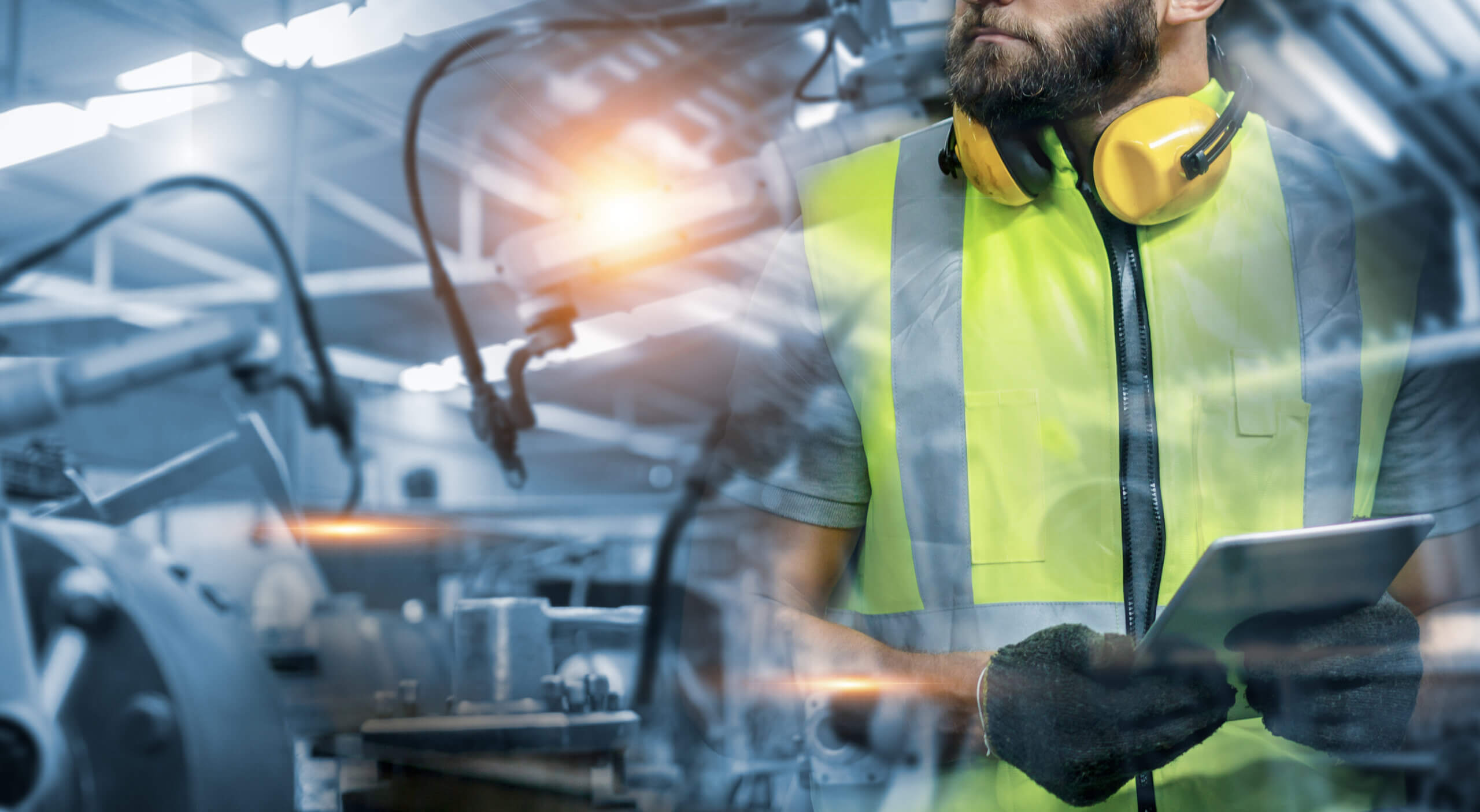
Maintenance departments are encountering increasing pressure from several angles, driving the rapid uptake of efficient cloud-based maintenance management software.
Economic forces such as an aging workforce, sluggish growth in the US labor market, and a complicated global political landscape have converged to create a complex operational environment.
This has left many industrial and manufacturing businesses unsure about making strategic decisions that will serve them well in the coming years. However, despite this volatile landscape, one thing is sure: the uptake of technology needs to be swift and decisive to ensure manufacturers don’t get left behind.
Manufacturers looking to increase efficiency and eliminate waste in their operations are turning to digital maintenance management solutions for their maintenance activities, such as:
- Work Order Software
- Enterprise Asset Management (EAM) software
- Computerized Maintenance Management Systems (CMMS)
These user-friendly platforms offer similar functionality, replacing static Excel spreadsheets and automating outdated paper-based processes.
Using technology to tighten up maintenance schedules and eliminate downtime and wasted money ensures that manufacturers can keep pace with the rapid changes in the industry.
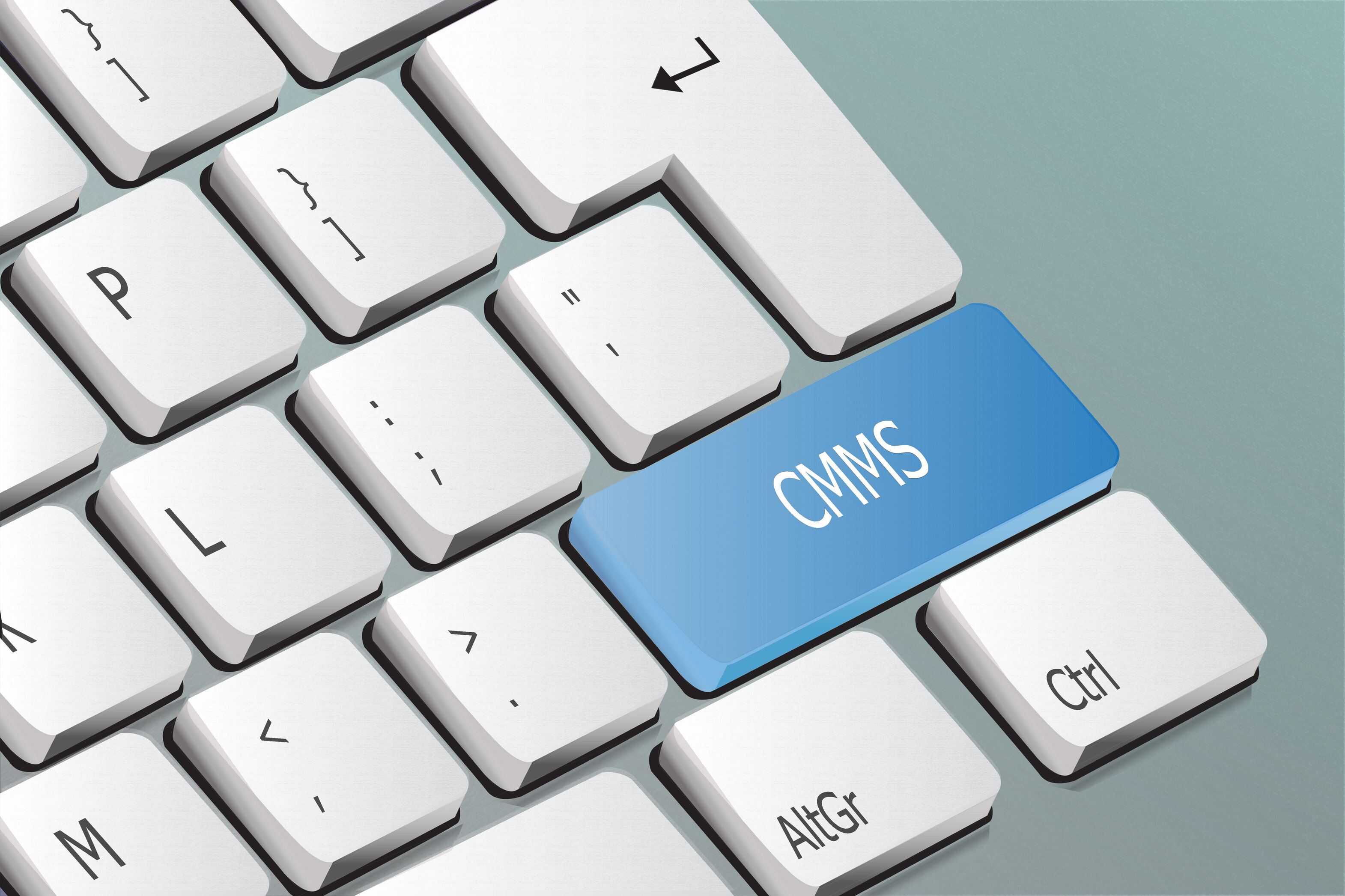
What Is CMMS Software?
A CMMS system is a type of work order management software that helps businesses simplify and streamline their maintenance operations. The best CMMS platforms centralize essential information for facility managers and technicians, allowing maintenance teams to efficiently track, assign, and monitor preventive maintenance tasks, respond to facilities requests, and strategize action plans.
Here are five ways a CMMS solution can help you deliver an efficient maintenance program, mitigate labor shortages, reduce maintenance costs, support better managerial decision-making, and set your business up for future growth.
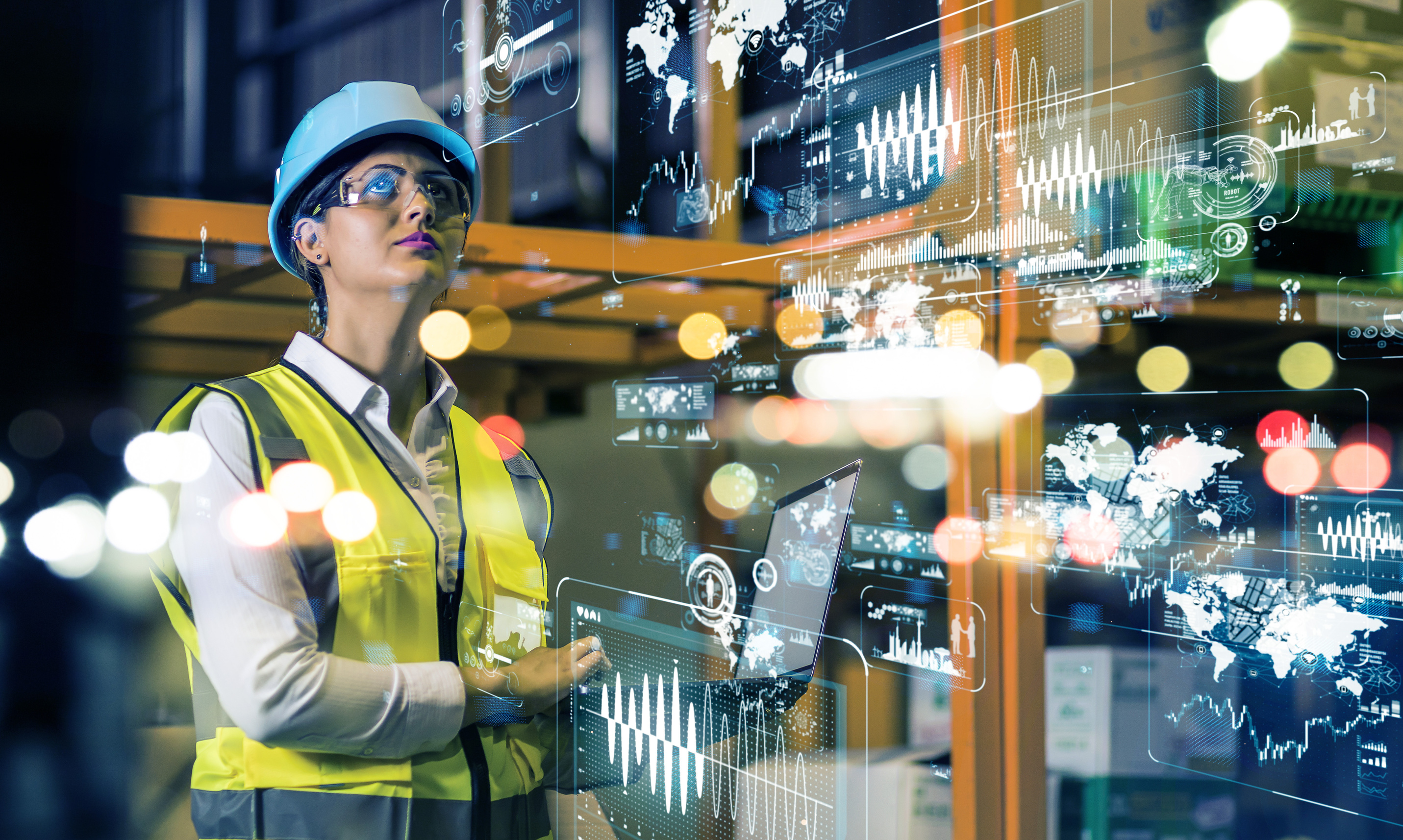
CMMS Features That Drive Efficiency
1. Automate Workflows to Deliver an Efficient Maintenance Program
Preventive maintenance schedules are cyclical, making it simple to take the time-consuming admin out of maintenance work.
Automating job scheduling by setting up maintenance tasks in a CMMS means your team can get notifications for upcoming work requests, take care of preventive, rather than reactive, maintenance tasks, track work orders, and keep equipment downtime at a minimum.
Your maintenance technicians can access a library of standard maintenance processes, ensuring you stay on top of safety and regulatory compliance. The best part is that once you’ve set up standard operating maintenance procedures, templates, and checklists for your team, you can “set and forget” and let your team of maintenance professionals get on with their equipment maintenance work.
2. Mitigate Labor Shortage Issues with Better Staff Utilization
It may be challenging to find new skilled technicians to join your team, but one way to circumvent this is to ensure the talents of your current employees aren’t being wasted. Getting all your maintenance information into a single platform means you can see who is doing what and when.
This gives supervisors better insight into how staff are responding to maintenance needs and helps you better utilize your skilled workers–arguably your biggest asset. Basic administrative tasks and your project management can be automated by making your CMMS work for you, which frees up talented technicians to solve complex problems.
Metrics related to staff utilization can also be reported using your CMMS, and KPIs can be allocated to encourage employees to deliver their best work and achieve individual and company-wide goals.
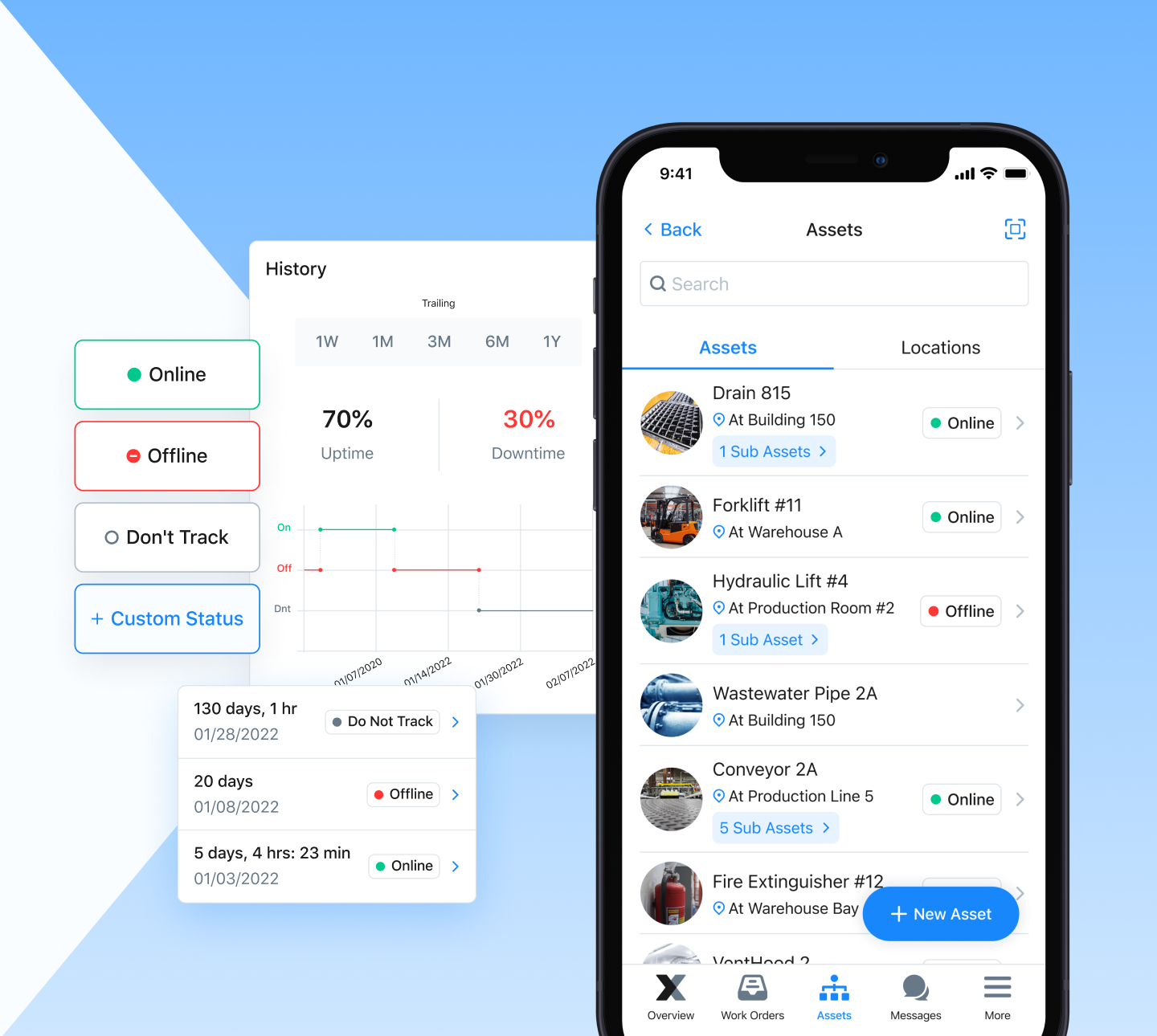
3. Get Asset Lifecycle Data to Inform Purchasing Decisions
Asset performance has traditionally been difficult to track, but the Internet of Things (IoT) has made reams of asset data available to facility management teams. Despite this prevalence of metrics, it can still be hard to understand which assets are performing well, which are experiencing repetitive breakdowns, and where all your asset maintenance dollars are going.
A CMMS collates and clarifies equipment downtime and uptime data from all your assets, showing performance across the entire equipment lifecycle. This transparency allows you to use real-time parts and inventory management to make informed decisions about capital purchases or adjust predictive maintenance schedules to mitigate downtime by increasing asset lifespan for your current fleet of equipment.
Maintenance history information is easy to access, and constant real-time equipment monitoring helps you predict maintenance requirements, schedule audits, order spare parts, send purchase orders, manage inventory, and keep track of costs for each asset.
Assets and parts inventory, connected via QR codes and barcodes, on a user-friendly CMMS (Computerized Maintenance Management System) has several benefits, including:
- Time-saving: QR codes enable teams to quickly and easily access asset information without having to search for this information manually.
- Improved accuracy: With the codes, teams can be confident that they are accessing the correct information for a specific asset.
- Enhanced asset tracking: The codes allow for improved tracking of assets by helping teams quickly scan the code to access information about the asset.
- Improved safety: The codes can provide access to safety procedures and protocols.
- Reduced costs: By enabling maintenance teams to access parts and asset information quickly and accurately, the codes can help reduce costs and downtime.
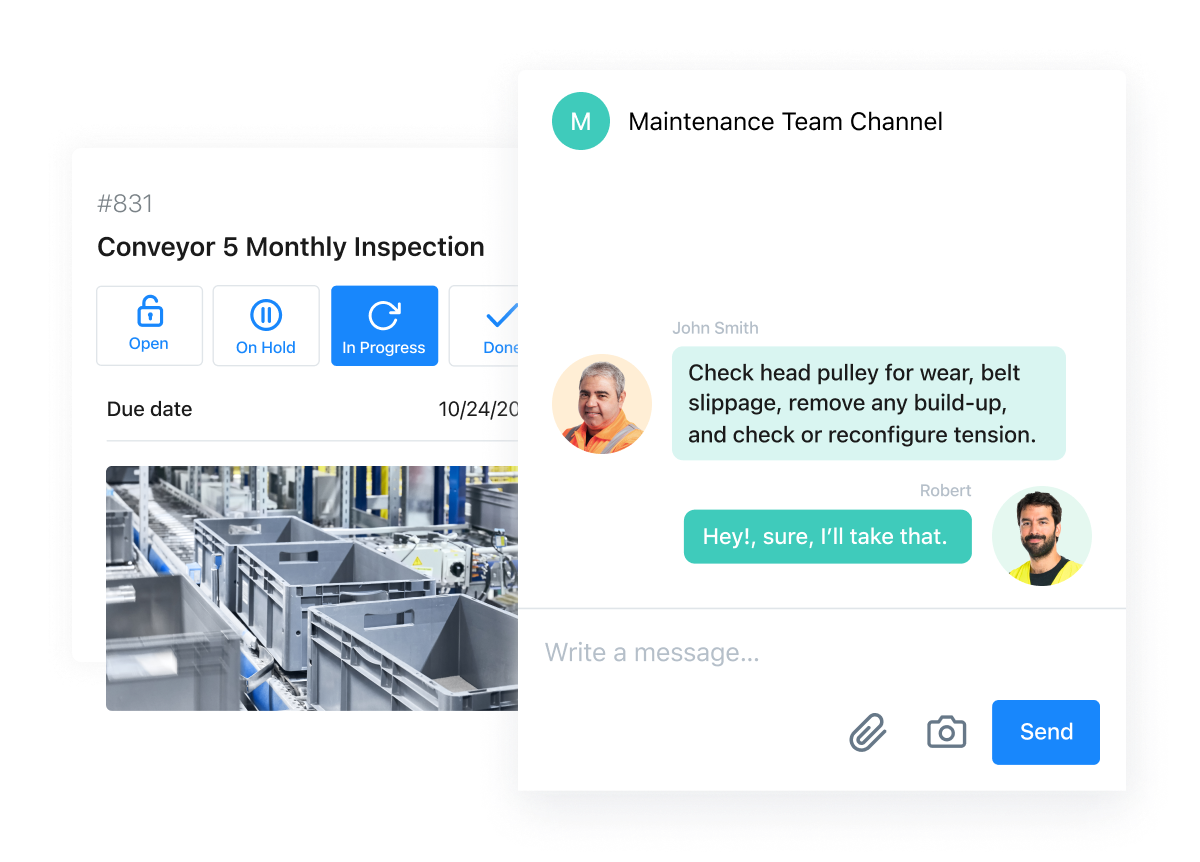
4. Chat and Collaborate in Real-Time without Confusion
Inefficient, disconnected communication can have a tangible impact on efficiency, slowing down the progress of tasks through your workflow and leading to miscommunications and misunderstandings.
A cloud-based CMMS can help bridge the gap between on-premise, in-person conversations and remote communication with disparate teams. Most workers are familiar with chat functions on their mobile devices, lowering the barrier to entry when integrating new software into your business.
Today’s technicians are generally comfortable with a mobile app, and even those not as tech-savvy will easily pick up on using online chat features, provided the platform is user-friendly and simple to navigate.
Real-time chat helps save time and avoid mistakes when it comes to carrying out maintenance activities. Not all software solutions have this feature, so when weighing CMMS providers, look for a mobile CMMS with chat functionality to facilitate real-time, productive conversations.
5. Connect Disparate Systems for Better Visibility
It’s easy to get excited about integrating a new CMMS platform into your business. Still, your CMMS implementation should always be considered in the context of your existing system infrastructure and organizational goals.
SaaS providers allow integrations between their proprietary ERP systems and independent software like MaintainX CMMS. This integration is vital to the success of your CMMS implementation, enabling you to link up siloed systems and gain a new holistic view of your business’s maintenance operations. In addition, you can integrate system data with MaintainX through our REST API.
Dashboards provide instant insights, critical reports, and essential real-time data to help you easily identify and fix inefficiencies across your business.
Get the Best CMMS Software with MaintainX
MaintainX is a customizable web-based CMMS software solution that simplifies how maintenance teams interact with large sets of information daily. It’s an interactive CMMS tool that helps you prioritize the most critical maintenance tasks, automates recurring work orders, simplifies preventive maintenance, enhances team communication, and provides meaningful insights into improving your maintenance strategy.
For any maintenance software, ease of use is key, especially for software meant to make your team’s work easier. Navigating the software to discover insights should be simple and intuitive. The features can be used to your advantage as you work to improve efficiency across your organization. Check out our pricing (we offer a free basic plan) and book a demo today to get a closer look at the insights you can discover with MaintainX.
FAQs
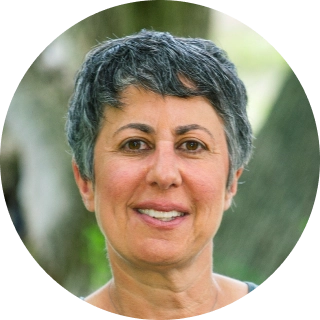
Caroline Eisner is a writer and editor with experience across the profit and nonprofit sectors, government, education, and financial organizations. She has held leadership positions in K16 institutions and has led large-scale digital projects, interactive websites, and a business writing consultancy.