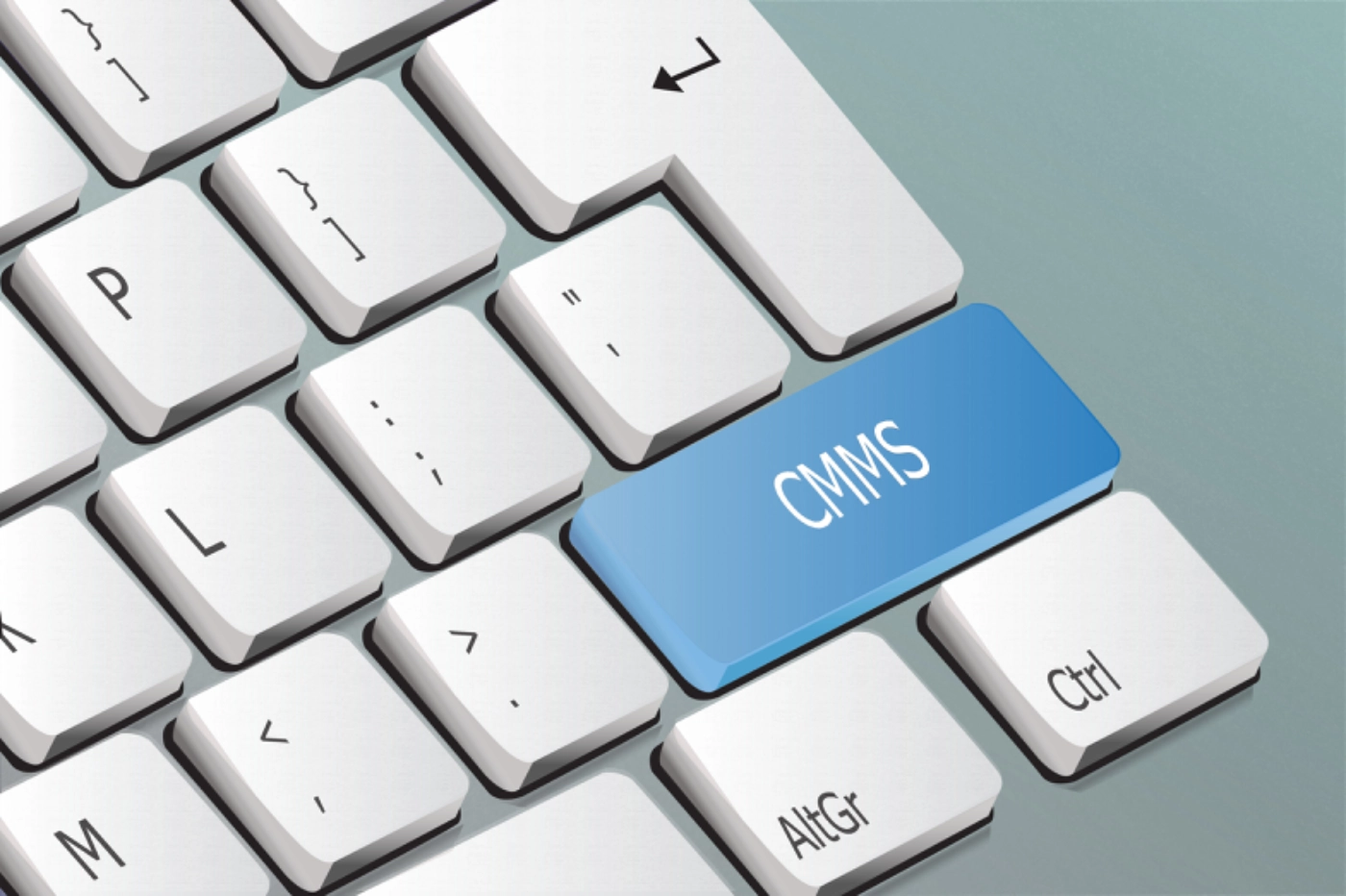
We use software every day, whether that means drafting spreadsheets in Excel, ordering food from smartphones, or posting on social media. Simple CMMS software should be available these days.
But how comfortable are we picking up unfamiliar technology with no training? According to a survey commissioned by Arbor Networks, two-thirds of Americans see themselves as “tech-savvy,” despite conflicting data suggesting otherwise. Even millennials aren’t as technologically proficient as once assumed: 6 out of 10 American individuals born between 1981 and 1996 “lack basic tech knowledge and cannot fulfill tasks such as search, sort, or email data from a spreadsheet.”
Which begs the question: Why do operational leaders expect maintenance technicians with zero to low digital training to quickly adapt to complex Computerized Maintenance Management Systems (CMMS)? Below are three reasons why maintenance managers should prioritize usability when evaluating CMMS software options:
3 Reasons Why CMMS Software Should Be Simple
1. Team members often lack the advanced tech skills needed for success
Unfortunately, it happens all the time. Organizational executives approve preventive maintenance programs designed to cut costs, and enthusiastic managers rush into CMMS purchases without understanding their options.
The user interfaces are so cumbersome that maintenance technicians never really master their usage. They either incorrectly input work order data or rely on upper management to digitize work order progress. The result? An inaccurate database of asset history, an abandoned CMMS software program, and money down the drain. As previously mentioned, most individuals are not truly tech-savvy.
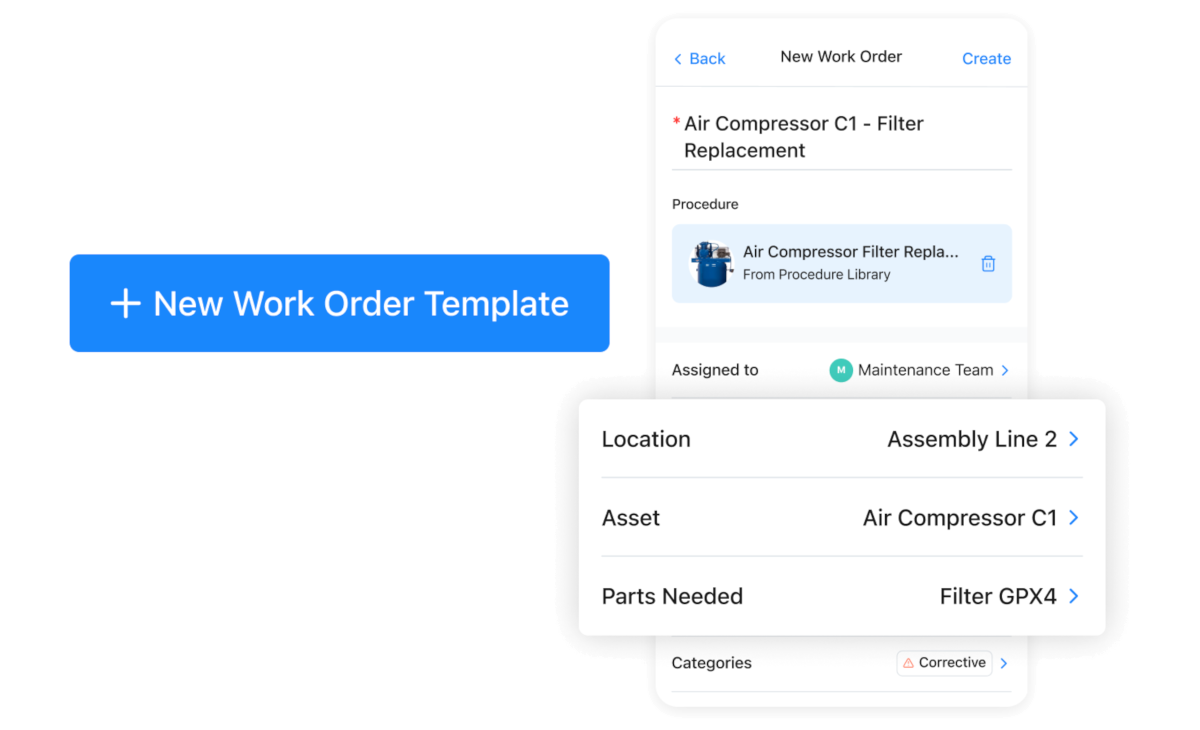
A report by Change The Equation shows that 58 percent of millennials have failed to master tech skills that help increase workplace productivity yet spend more than 20 hours per week consuming smartphone media.
This suggests that most of us are better at using software programs designed for smartphone usage than desktop usage. Translation: Modern software engineers have become extremely adept at developing user-friendly programs that make us feel tech-savvy.
While maintenance technicians are brilliant at troubleshooting complex equipment issues, their problem-solving skills don’t always translate to unfamiliar technological interfaces. This brings us to our next point:
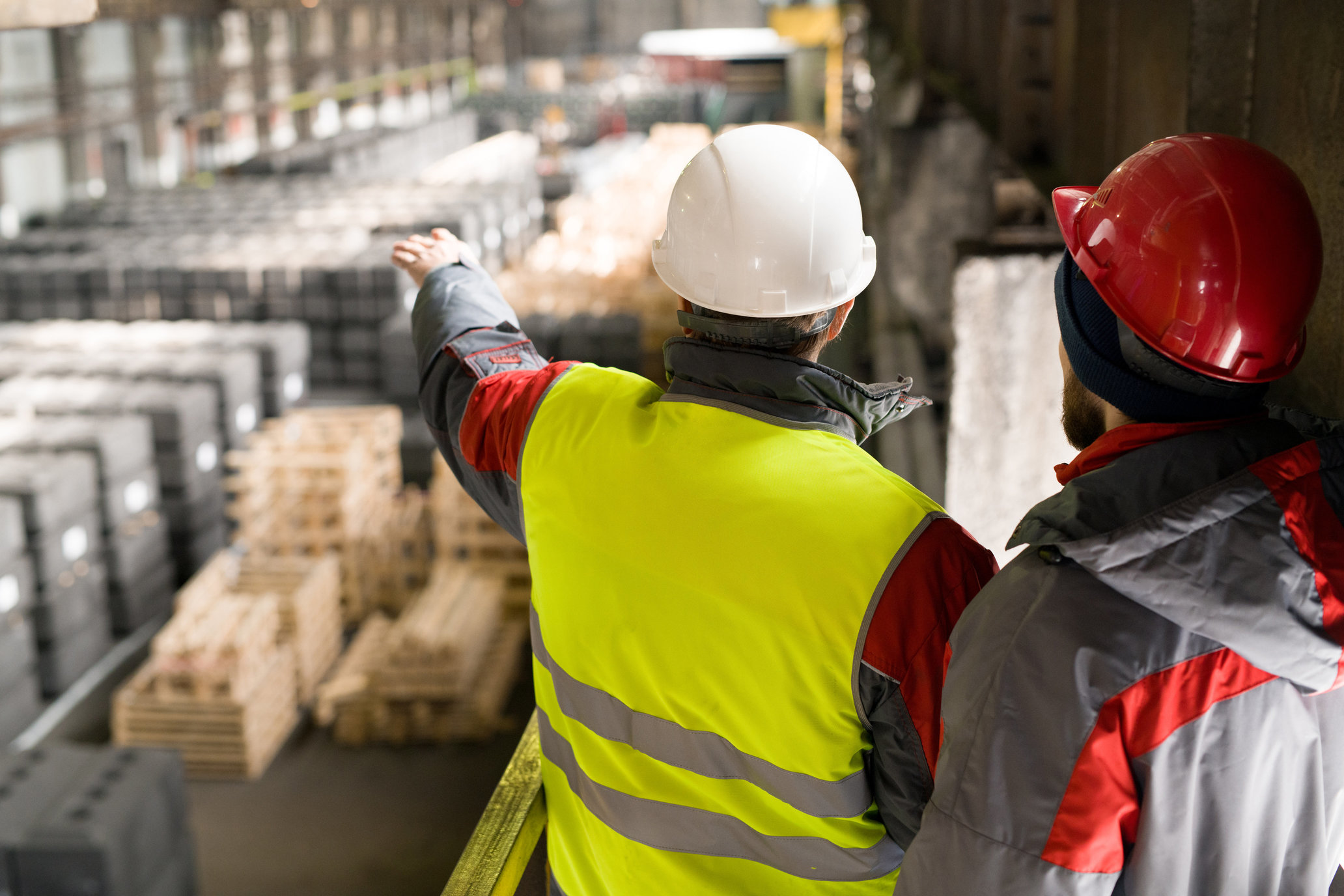
2. Software training takes time away from maintenance priorities
OK, let’s be honest: Most operational managers and CMMS providers are aware of the need for software training. It’s not unusual for legacy providers to offer paid training packages in conjunction with CMMS purchases.
Whether technicians are initially taught by expert instructors or are later trained by operational managers, technical training presents an obvious challenge: It takes time away from important maintenance tasks. Managers must either redirect employees from daily work orders or request their participation after hours in exchange for overtime. Neither option is ideal for resource-strapped maintenance teams.
Furthermore, most CMMS software training programs don’t offer money-back guarantees. This is bad news for the large number of technicians who report still feeling uncomfortable navigating advanced features after purchasing CMMS platforms. According to Reliable Plant, as many as 80 percent of CMMS implementations have failed. While we’re skeptical the statistics are that high for industries across the board, the data suggests many maintenance departments often “bite off more than they can chew” with CMMS. We suggest CMMS that promises robust training for technicians, managers, and owners that covers everything from work orders to global procedures to real-time inventories to metric reporting.
Considering that more than half of maintenance managers cite a “lack of resources” as their primary maintenance challenge, most organizations cannot afford to waste time on questionably effective CMMS training programs. At this point, you may be wondering if we suggest forgoing CMMS solutions altogether! Nope, we are simply suggesting the selection of a CMMS platform specifically designed for mobile usage.
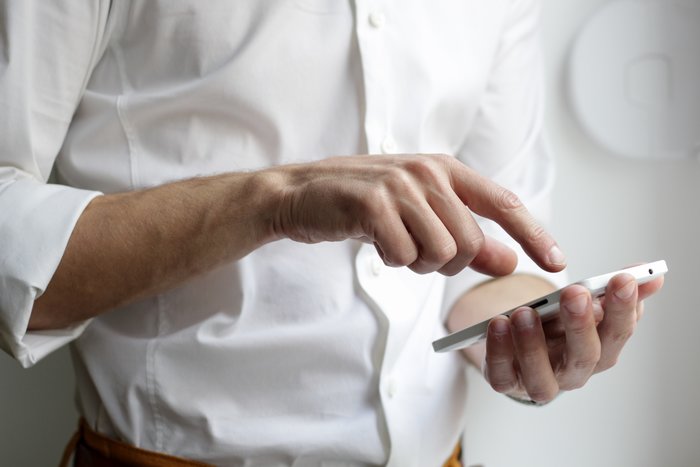
3. Most people heavily rely on smartphones
The majority of Americans—96 percent—now own a cellphone, and many of these mobile devices are smartphones. Smartphones run operating systems that support mobile and web applications. In addition to text messaging capabilities, smartphones allow users to download a variety of software applications for both personal and professional use.
In other words, maintenance technicians are walking around with tiny computers in their pockets every day! These “tiny computers” can and should be used to streamline organizational processes wherever possible. Most existing CMMS solutions were not built for mobile. However, that hasn’t stopped some legacy providers from adapting their software applications for smartphone usage. Unfortunately, without almost completely rewriting the existing software code from scratch, these CMMS programs don’t seamlessly translate to a friendly mobile-user experience.
Conversely, a CMMS designed for mobile-first will feel like your technician’s familiar consumer apps. The best CMMS software programs are easy to use. Navigational menus are positioned in logical locations, functionalities are clearly illustrated, and screen interfaces remain uncluttered despite housing more advanced features.
However, only a handful of CMMS options are designed exclusively for mobile at this point. Why? Because the level of software engineering required to accomplish intuitive smartphone functionality is exceedingly high. Though every provider will eventually be forced to move toward mobile-friendly CMMS, not everyone is there yet.
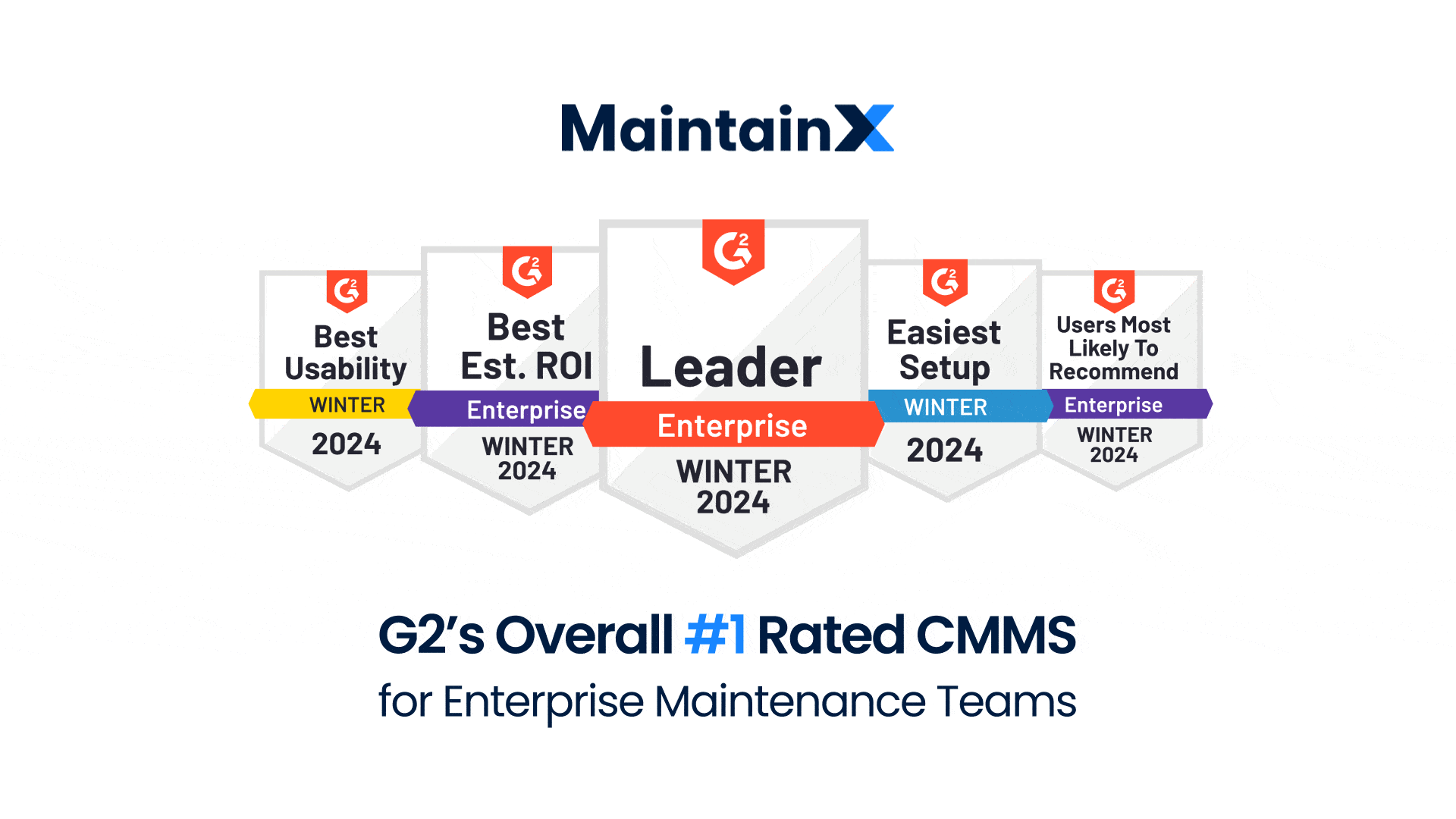
MaintainX Simplifies CMMS Software
MaintainX is the world’s first digital maintenance and operations app designed with collaborative workflow functionality. The work order platform eliminates the problem of lost email threads, undocumented phone calls, and disorganized text messages with in-app messaging and work order commenting.
Operational managers can also track reactive maintenance, organize preventive maintenance work orders, and control daily business operations–all with a digital audit trail. Are you ready to manage your company’s maintenance and operations without the paper stacks? Global organizations like McDonald’s, Marriott, and Hilton have already switched to the convenience of MaintainX.
FAQs
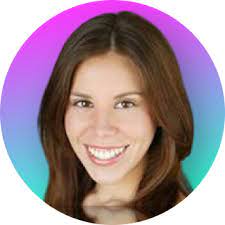