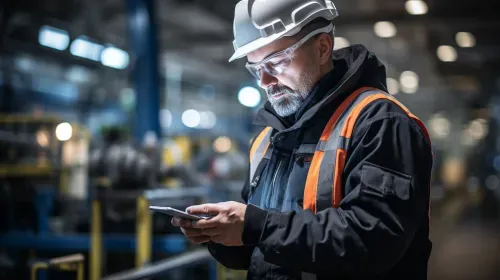
There’s a reason most employment contracts include a probation period: the first few months of any job are the most critical. During this time, a new employee learns the challenges they’ll be facing every day and proves that they’ll be able to conquer them. In other words, it’s when a new employee can make or break their chances of long-term success within the company.
The first few weeks of introducing a Computerized Maintenance Management System (CMMS) are similar. But in this case, the software has to prove itself to the team (and the maintenance manager responsible for that success). A well-planned CMMS software implementation is just as important as the first 90 days for a new employee. In fact, getting this period right is the most critical factor in ensuring long-term success.
In this guide, we’ll show you how to ensure a successful CMMS implementation—both for your team and for the company as a whole.
Benefits of implementing a CMMS
Implementing a CMMS helps teams improve maintenance operations by empowering them to evolve their maintenance strategies. Our 2024 State of Industrial Maintenance Report showed that respondents who evolve their maintenance strategy:
- Increase efficiency, saving 250 hours a year and increasing work order completion rate by 53%.
- Reduce costs through better resource management owing to data-based insights.
- Reduce unplanned downtime by 32%.
- Improve asset lifecycle management by proactively maintaining equipment.
- Control inventory better. 59% of teams reduced costs by improving their parts inventory management.
Now that you know what to look forward to, let’s start planning your implementation.
Want an even deeper dive? Get the full guide now.
How to plan a successful CMMS implementation
To reap the full benefits of a CMMS, you have to implement it properly. And a successful CMMS implementation requires thorough planning. Here are the five CMMS implementation steps we recommend:
Accurately assess current maintenance practices
Before you know where you’re going, you have to know where you’re starting from. Take stock of your current state of affairs. What does your current maintenance strategy look like? Is it mostly reactive, or do you have preventive maintenance schedules in place? What’s your work order completion rate? How are work orders recorded and executed?
Set clear objectives and key performance indicators (KPIs)
You can transform your entire maintenance operation with a CMMS, but choosing a few clear objectives (and tying them to clearly-defined KPIs) will help you stay focused. If your biggest worry is unplanned downtime, for example, your objective could be introducing a proactive maintenance strategy for your most at-risk equipment. In this case, your KPIs would be preventive maintenance (PM) completion rates and equipment failures for those assets.
Create a detailed implementation timeline
Without a timeline, even the best intentions can get swallowed up by reactive cycles. Create a specific, time-bound plan that clearly outlines key milestones in your CMMS implementation plan. Include items like “completing onboarding training” and “completing and executing 100% of work orders through the CMMS.” This will help everyone stay accountable.
Form a dedicated CMMS implementation team
CMMS implementations fail without a village to drive the process. Beyond maintenance managers, there should be champions within each team to drive CMMS usage forward.
Secure management commitment
You’ll need executive suite support to keep a CMMS implementation moving along. Having someone on your side who can tolerate growing pains and support process changes is essential. Learning curves are unavoidable, but real progress awaits on the other side.
How to choose the right CMMS software
No two CMMS offerings are created equal, but there are standard features you should keep an eye out for in your search for the right solution. At a bare minimum, a CMMS should provide:
- Preventive maintenance scheduling. Being able to schedule and complete preventive maintenance tasks on aging equipment should be a cornerstone of evolving your maintenance and asset management strategy.
- Work order management. A good CMMS will allow you to easily create, assign, prioritize, and complete work orders.
- Asset tracking and management. When you can access asset information and data easily, you can improve reliability and uptime. A CMMS that includes asset management and tracking features is essential.
- Inventory management. A CMMS should let you easily manage, track, and purchase spare parts so that you’re never caught without them.
- Reporting and analytics. Being able to access reports and easily track KPIs allows you to assess your maintenance strategy and improve it over time.
- Mobile accessibility. An app-based CMMS lets maintenance workers access asset and work order information in the field, which skyrockets productivity and work order completion.
Finding the right CMMS vendor is a process. Your ultimate decision will depend on factors like your company size, software ease of use, the objectives you want to achieve with a CMMS, and whether you want a cloud-based or on-premise solution.
Syracuse Glass Company tried 15 different CMMS solutions before deciding on MaintainX. It was the best solution to help them curb inventory spending, reduce reactive maintenance, and improve their maintenance operations and processes.
The CMMS implementation process
The great news about implementing a CMMS? If you find the right solution, you only have to do it once. With the right implementation process in place, it can be done in as little as three weeks, so it’s important to find a vendor that can guide you through each step.
Here’s what the CMMS software implementation process typically looks like:
1. Data gathering and migration
First, you’ll need to gather all the asset and maintenance data you currently have, whether it’s in Excel or .csv files, a different CMMS software, or stacks of paperwork. You can then standardize, map, and begin the data migration process. Ensuring accurate data that’s consistent and error-free is essential.
2. System configuration and customization
Each team will have slightly different needs with their CMMS. Working closely with an implementation specialist to configure and customize your CMMS will ensure you get a solution that helps your maintenance team do their best work, every day.
3. Integration with existing software
A CMMS becomes much more powerful when it’s connected to the systems you use to run your business. Integrating with ERP software, fleet maintenance software, accounting systems, and other automation tools will help maximize your capabilities. A major part of Duracell’s CMMS implementation with MaintainX was connecting it to SAP, their system of record.
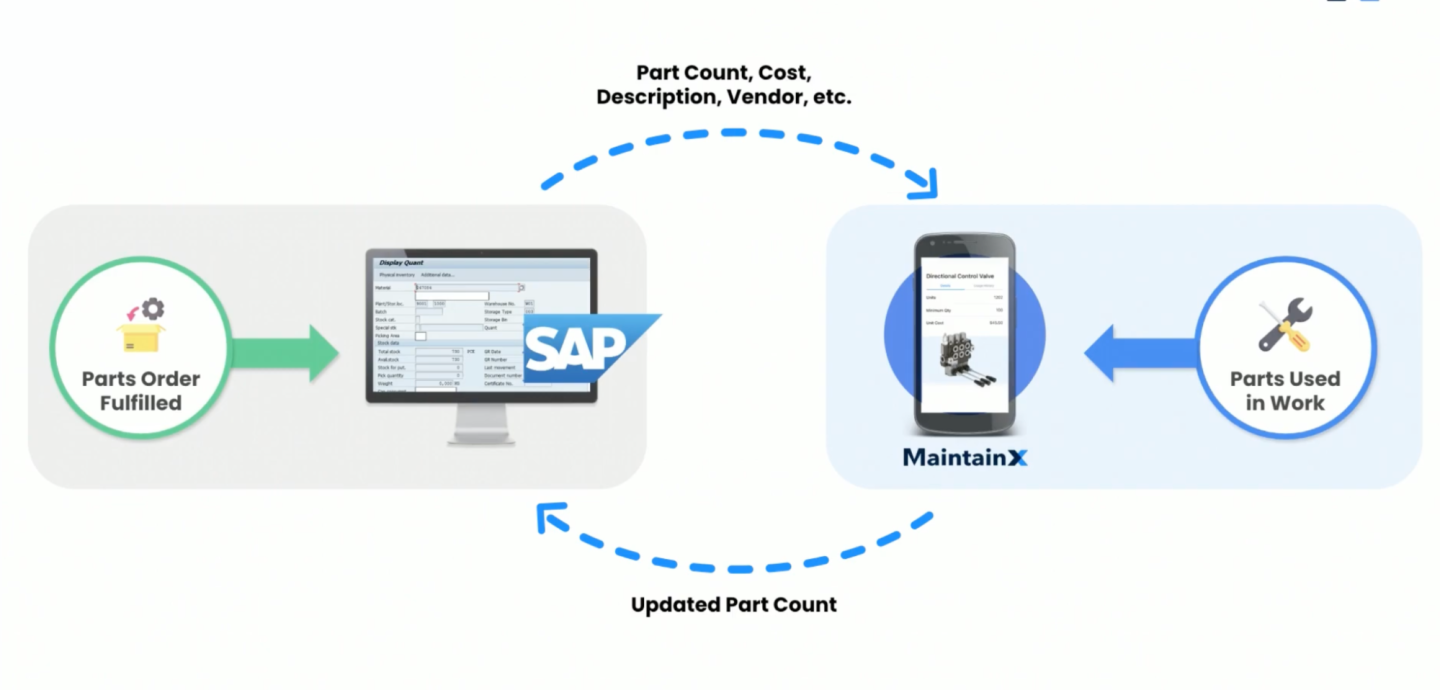
4. User training and adoption strategies
Once your CMMS is configured and connected, you’ll start training your team to use it. A robust training plan and user adoption strategy is your best bet. Change can be difficult, but providing your team with the information and accountability systems they need is the only way to guarantee success and continuous improvement.
5. Testing and quality assurance
The road to widespread implementation throughout your facility or organization should have many necessary checkpoints. Building testing and quality assurance into your rollout strategy will ensure that data, tasks, workflows, and analytics are all being captured properly.
Overcoming common CMMS implementation challenges
It’s a hard pill to swallow when CMMS implementations struggle. No team wants to encounter obstacles in the CMMS implementation process, not to mention having to abandon the process altogether. Here are some common roadblocks to look out for—and how to avoid them.
Inaccurate data
Like we mentioned earlier, it’s very important to ensure your data is consistent and error-free before you begin the data migration process. While it can be a pain, it’s worth going through everything with a fine-tooth comb to make sure things like naming conventions and asset history are accurate. Going back and fixing these issues retroactively will be a much bigger headache than getting it right the first time.
Resistance to change
It can be difficult to get everyone on board with a sweeping change—even one that’s going to improve their day-to-day lives. Being very communicative about what’s changing when, and what it means for each team is the key. Ensuring that your CMMS champions are well-trained and enthusiastic about your CMMS is also important—they can address resistance within their team directly.
High implementation costs
Any major plan that impacts daily workflows will become costly if it’s not executed well. It’s important to set up an implementation plan with clear milestones that are tied to dates and accountable people. Partnering with an implementation specialist can also help if you run into any technical hiccups, ensuring you have as little downtime as possible during the implementation process.
Losing momentum
We’ve all been in situations where a plan everyone was excited about loses steam over time. Building accountability into your plan is your best bet. That means clearly communicating what needs to be completed by which dates, and sticking to that plan. Comprehensive training for employees will also ensure that people use the CMMS in the way it’s intended.
Best practices for successful implementation
Of course, nobody wants to encounter any of the challenges we mentioned above. These tips can help you stay on the right path throughout your implementation:
- Start with a pilot program. We know you’re eager to roll out a CMMS as quickly as possible, but always start with a pilot program first. A smaller-scale test run will help you identify any issues, plan for contingencies, and tailor your training plan when it’s time for the big rollout.
- Focus on user engagement and training. An enthusiastic and well-trained workforce is the secret weapon that will carry your implementation over the finish line. Provide comprehensive training that focuses on usability, and ensure your CMMS champions are checking in with their teams regularly.
- Continuously gather feedback. A CMMS should be easy to use. Check in with your staff regularly to gather feedback, then use that feedback to continuously improve processes.
- Regularly update and maintain the system. Just like your equipment, your CMMS needs maintenance and attention to keep everyone productive. Regularly check in to make sure the systems you set up are functioning as intended, and everything’s being captured well.
Measuring CMMS success
How do you know if your CMMS is increasing reliability and productivity while reducing maintenance costs and unplanned downtime? You build those goals into your implementation plan.
Your KPIs should be directly attached to the goals and objectives you defined at the start of your implementation (which should be informed by the main challenges you had before you adopted a CMMS). For example, Wauseon Machine knew they were overspending on inventory before they found MaintainX. By focusing on inventory management in their implementation, they’re now closely tracking inventory spend—and saving $60,000 a year.
No matter what your goals are, there are KPIs you can track through your CMMS to ensure you’re achieving them. Your implementation specialist can help you define these goals at the outset of your implementation and show you how to track them over time.
Long-term strategies for CMMS success
A great implementation sets the stage for CMMS success, but extending that success requires a long-term commitment. We recommend a few strategies to ensure your CMMS keeps delivering value.
Continuously improve your maintenance processes
As your organization uses your CMMS, you’ll begin to evolve your maintenance management process. This journey should be ongoing. In the first few weeks, you may set up a PM program for your most at-risk assets. As time goes on, you’ll have the insights and the resources to keep expanding your horizons.
For example, Wauseon Machine has continued to evolve its maintenance strategy since implementing MaintainX. They’ve moved from a reactive model to a preventive strategy, and PM completion rates have increased from 60% to 100% over time.
Regular software updates and feature utilization
If you’ve chosen a modern CMMS vendor, there should be regular software updates and new features to keep up with. Make sure you do—these upgrades ensure that your team can do their best work as the industry continues to evolve. Your Customer Success representative should keep you informed when new features drop and show you how to maximize them.
Expand CMMS usage across the organization
The more you can weave your CMMS into the fabric of your organization, the better your results will be long-term. Once your maintenance team and technicians are well-versed in the solution, consider rolling it out to other teams such as Operations, Facility Management, or Inventory Management. A CMMS can help these teams work smarter, both within their own team and across the organization.
A successful implementation leads to a successful organization
Your journey with a CMMS should be a long and fruitful one, but the implementation phase is truly what will set your organization up for long-term success. Making sure you find a CMMS vendor that will guide you through the process and partner with your team throughout the implementation is essential.
At MaintainX, we support our customers on their implementation journey and help them improve their maintenance management processes. To learn more, get in touch with an implementation specialist today or download our guide for a seamless implementation.
FAQs about CMMS implementation
How long does a typical CMMS implementation take?
Implementation time will vary depending on the size and needs of your organization. If you partner with a CMMS vendor that offers a robust implementation program along with comprehensive training, you can get the system effectively running in as little as three weeks.
What are the key factors for successful CMMS adoption?
Successful CMMS software adoptions are driven by a number of factors. At a minimum, you need clear goals and objectives, accurate data, comprehensive training, clear and open communication, and a detailed timeline that includes critical milestones. In addition to working with a dedicated implementation team, these factors will help you avoid an implementation failure.
Can CMMS be implemented in small-scale operations?
Yes, a CMMS can be implemented for operations as small as single-site teams of less than 10 (and as large as global, multi-site enterprises). Finding a software solution that can meet your organizational needs is the most important aspect of a successful CMMS implementation for any size of organization.
How does mobile CMMS differ from traditional desktop solutions?
A mobile CMMS includes a technician app that frontline workers can use to access asset information and complete work orders in the field. It enables technicians to be much more efficient and informed while completing their daily tasks, which drives productivity across the organization.
What ROI can be expected from CMMS implementation?
A CMMS drives ROI by reducing unplanned downtime and unproductive work hours. It also allows maintenance teams to evolve their maintenance strategies, from reactive to preventive maintenance. As a CMMS software solution is widely adopted across a team, ROI will increase. Many teams realize a positive ROI on their CMMS within weeks of implementing it.
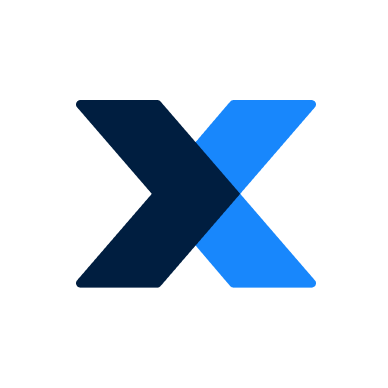
The MaintainX team is made up of maintenance and manufacturing experts. They’re here to share industry knowledge, explain product features, and help workers get more done with MaintainX!