Machine maintenance includes activities undertaken to keep a facility’s mechanical equipment in good working condition. It includes maintaining both simple hand-operated pieces of equipment and heavy-duty machinery. Companies perform routine inspections, equipment servicing, parts replacement, and repairs as part of machine maintenance.
What Is Machine Maintenance?
Machine maintenance is critical for business continuity and profitability. It contributes to a company’s meeting production timelines, minimizing downtimes, and improving workplace safety. Companies can choose to perform machine maintenance after a breakdown or through proactive maintenance programs.
Proactive maintenance approaches include preventive, predictive, and condition-based maintenance. Undertaking machine maintenance after a breakdown is known as reactive maintenance.
What Is the Purpose of Maintenance?
According to Aberdeen, businesses lose an average of $260,000 for every hour of downtime. Equipment failure can disrupt the entire production process in addition to posing a safety risk. This is what maintenance looks to solve. Maintenance aims to keep assets in optimal working order to reduce downtimes. Facilities rely on maintenance to keep equipment running to meet their operational needs.
Examples of Machine Maintenance
Large manufacturing facilities often connect infrared cameras to software; these tools deliver real-time warnings that alert maintenance managers when pieces of equipment are in danger of overheating if parts aren’t soon replaced or remedied. Maintenance is then planned and scheduled before failure occurs.
Companies that manufacture car parts implement proactive maintenance strategies to prevent automated machines from breaking down. When a machine malfunctions, the entire manufacturing process is disrupted, and there’s also the likelihood of producing faulty car parts. Problems, therefore, need to be detected and corrected early.
Industries That Practice Machine Maintenance
In many industries, heavy machinery makes up the core of production and business processes. Such industries rely on machine maintenance to avoid costly downtimes. These industries include:
- Automotive Manufacturing: Automakers and car-part manufacturers rely on automated machines such as pneumatic grippers, conveyor systems, and robotic welders for production. Without proper maintenance, there’s the risk of producing faulty vehicles that pose safety risks to road users.
- Apparel Production: Knitting, pressing, and sewing machines need maintenance to work well.
- Plastic Products Manufacturing: Equipment used to manufacture plastic products include extrusion machines, trim presses, plastic granulators, and injection molds. They need regular maintenance to work optimally.
- Food Production: Machines, such as ovens, fryers, and decorating equipment critical to food production, storage, and packaging, need to be in good condition to avoid compromising food safety.
- Refineries: Reactors, heat exchangers, compressors, and furnaces, among other equipment used in refineries, require maintenance.
Types of Machine Maintenance Workers
Machine maintenance requires a team to oversee the planning and execution of maintenance programs. The most common personnel involved in machine maintenance include:
- Machinery Mechanics: Mechanics perform maintenance activities to ensure equipment is operating at full capacity. For work orders that involve advanced diagnostics, they only execute visual inspections.
- Maintenance Technicians: Technicians perform the advanced diagnostics. They rely on device sensors and maintenance software, such as a CMMS, to identify problems and prescribe solutions. In rare cases, maintenance technicians can perform repairs even though they are primarily left to mechanics.
- Millwrights: Millwrights dismantle and install equipment in a facility. They also perform maintenance tasks.
How to Enhance Machine Maintenance
As businesses grow, companies should scale their machinery maintenance to meet growing productivity demands. Companies should focus on the following four areas when improving their machine maintenance:
- Planning: Planning ensures that all maintenance resources are available when needed. These include replacement parts and labor. Maintenance planning also helps to optimize maintenance costs.
- Precision: Maintenance activities should be performed accurately and consistently. The company and maintenance personnel should also adhere to industry best practices. Precision requires well-trained maintenance workers, availability of tools and equipment, high-quality materials, and easy-to-follow maintenance plans.
- Protection: Employee safety is paramount to any machine maintenance program. Workers should be equipped with protective equipment. Safety procedures should also be regularly reviewed to determine their effectiveness.
- Measurement: Proactive maintenance requires data and analytics. This enables an organization to settle on the right maintenance strategy for more reliable asset performance.
Machine Maintenance Certifications and Training
Several community colleges, universities, and trade schools offer machine maintenance training. The programs cover different types of maintenance and prepare individuals for industrial machine maintenance. The institutions award certification to individuals who complete the programs.
The Society for Maintenance & Reliability Professionals (SMRP) also provides exam-based certifications for maintenance personnel. Its programs include Certified Maintenance & Reliability Professional (CMRP), Certified Maintenance & Reliability Technician (CMRT), and Certified Asset Management Assessor (CAMA). The CMRP program is accredited by the American National Standards Institute (ANSI).
Frequently Asked Questions
What Are the Four Types of Maintenance?
Most organizations practice a combination of different types of maintenance. The four most commonly practiced types of maintenance are:
- Corrective Maintenance: A maintenance strategy that involves taking planned or unplanned corrective actions after equipment issues occur. The goal is to return broken assets to operational capacity.
- Preventive Maintenance (PM): A maintenance strategy that involves completing scheduled maintenance tasks before failure occurs to keep assets in optimal working condition, curb unplanned downtime, extend life cycles, and reduce costs associated with equipment failure.
- Condition-Based Maintenance (CBM): An advanced form of PM that uses condition-based diagnostic measurements (e.g., vibrations, temperature, ultrasounds) to predict equipment failure. Operational managers use CBM intervals to make more reliable, efficient, and cost-effective decisions about when to perform maintenance tasks.
- Predictive Maintenance (PdM): An advanced form of PM, and an even more advanced form of CBM, that relies on sensors to relay real-time data in combination with predictive algorithms to precisely predict future breakdown times. Though many resources use the terms PdM and CBM interchangeably, they are not the same. While CBM often includes the same sensor-based technology as PdM, it doesn’t utilize predictive technology.
What Are Maintenance Procedures?
Maintenance procedures refer to documented instructions, or standard operating procedures, on how maintenance should be performed to ensure that assets operate within safety limits. They identify existing conditions, outline precautions, and provide clear instructions on performing maintenance according to maintenance strategies and policies in place.
Designers, equipment suppliers, and maintenance personnel are usually involved in the preparation of maintenance procedures. This ensures accuracy, validation, and verification of the document. Maintenance procedures should be periodically reviewed.
What Is the First Step to Creating a Maintenance Schedule?
Maintenance personnel should first make an inventory of available personnel, finances, and organizational systems before scheduling maintenance. This helps to identify resource constraints that may impact the performance of the scheduled maintenance activities. After that, they should develop a maintenance checklist of the activities to be performed.
What Is a Maintenance Checklist?
A maintenance checklist is a list of maintenance tasks prepared by equipment manufacturers or inspectors to be completed by maintenance personnel. They make the backbone of any proactive maintenance program. Maintenance checklists help ensure workflow standardization, increased productivity, workplace safety, faster troubleshooting, and efficient maintenance planning.
How to Create a Maintenance Checklist?
To create an effective maintenance checklist, organizations should first list all assets that need maintenance and review each asset’s history, such as unique working conditions, failure modes, and probable frequency of breakdowns. In some instances, there may be a need also to review manufacturer guidelines when developing a checklist.
Get a CMMS for Your Machine Maintenance
Machine maintenance is critical to both production and workplace safety. It’s essential to develop an effective strategy that keeps equipment in good working order. In some cases, certain assets will require different types of maintenance approaches. Organizations should find the perfect balance that improves productivity, promotes employee safety, and reduces maintenance costs.
Planned machine maintenance ensures increased asset efficiency, reduces the need for equipment replacement, and increases ROI. It’s a straightforward strategy that’s easy to implement regardless of maintenance skill level.
Thinking about implementing scheduled machine maintenance? Try MaintainX for free!
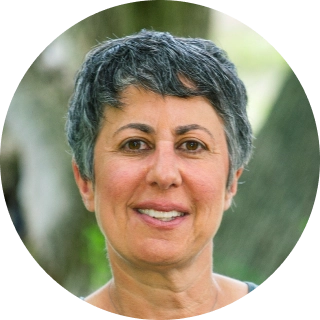
Caroline Eisner
Caroline Eisner is a writer and editor with experience across the profit and nonprofit sectors, government, education, and financial organizations. She has held leadership positions in K16 institutions and has led large-scale digital projects, interactive websites, and a business writing consultancy.
See MaintainX in action