How Electro Cycle Increased Planned Maintenance 30% with MaintainX
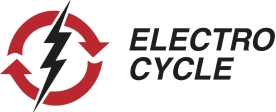
After a brief hiatus, Tom Resch rejoined Syracuse Glass Company in July 2020. The company brought Resch back as a Process Improvement Project Lead and tasked him with forging operational improvements to meet new business goals.
Upon his return, one of Resch’s first business priorities was to implement a modern computerized maintenance management system (CMMS). His goal was to help Syracuse's maintenance department track assets, streamline parts management, simplify preventive maintenance (PM) scheduling, and foolproof procedures with greater efficiency.
Most project leaders have settled for “good enough” at one point or another. However, Tom Resch was determined to find the perfect CMMS solution. After tinkering with 15 different platforms, Resch still hadn’t found the robust, yet user-friendly CMMS of his dreams.
Fortunately for his team, Resch is not a quitter. He came across an ad for MaintainX, a CMMS that checked every box.
Resch’s team now feels confident its three most critical forklifts will never unexpectedly fail due to meter-alert integrations. Thanks to his process-improvement implementations, Syracuse continues to expand throughout New England.
“It's always nice to make a decision after testing 15 solutions—although, it felt like 1000—and feel confident you've made the correct one. The seamless transition between MaintainX’s desktop and mobile apps makes it a nice solution. The software’s advanced reporting, asset filtering, and work order scheduling capabilities are also easy to use. I’m looking forward to continuing our partnership with MaintainX in the future.”
Since implementing MaintainX, Resch has cataloged 64 vendors, 372 assets, and 924 parts. At all times, the company now houses cost-optimized levels of essential spare parts like water filters, suction cups, and float switches.
Syracuse Glass Company is an independent distributor and fabricator of flat glass and aluminum products. Since opening its doors in 1909, the family-owned business has prioritized maintaining extraordinary customer relationships.
Syracuse Glass serves glass shops, commercial glazing contractors, home improvement contractors, and select manufacturers. Syracuse Glass is an involved member of the Glass Association of North America (GANA), the National Glass Association (NGA), and the Manufacturing Association of Central New York (MACNY).
Get more done with MaintainX