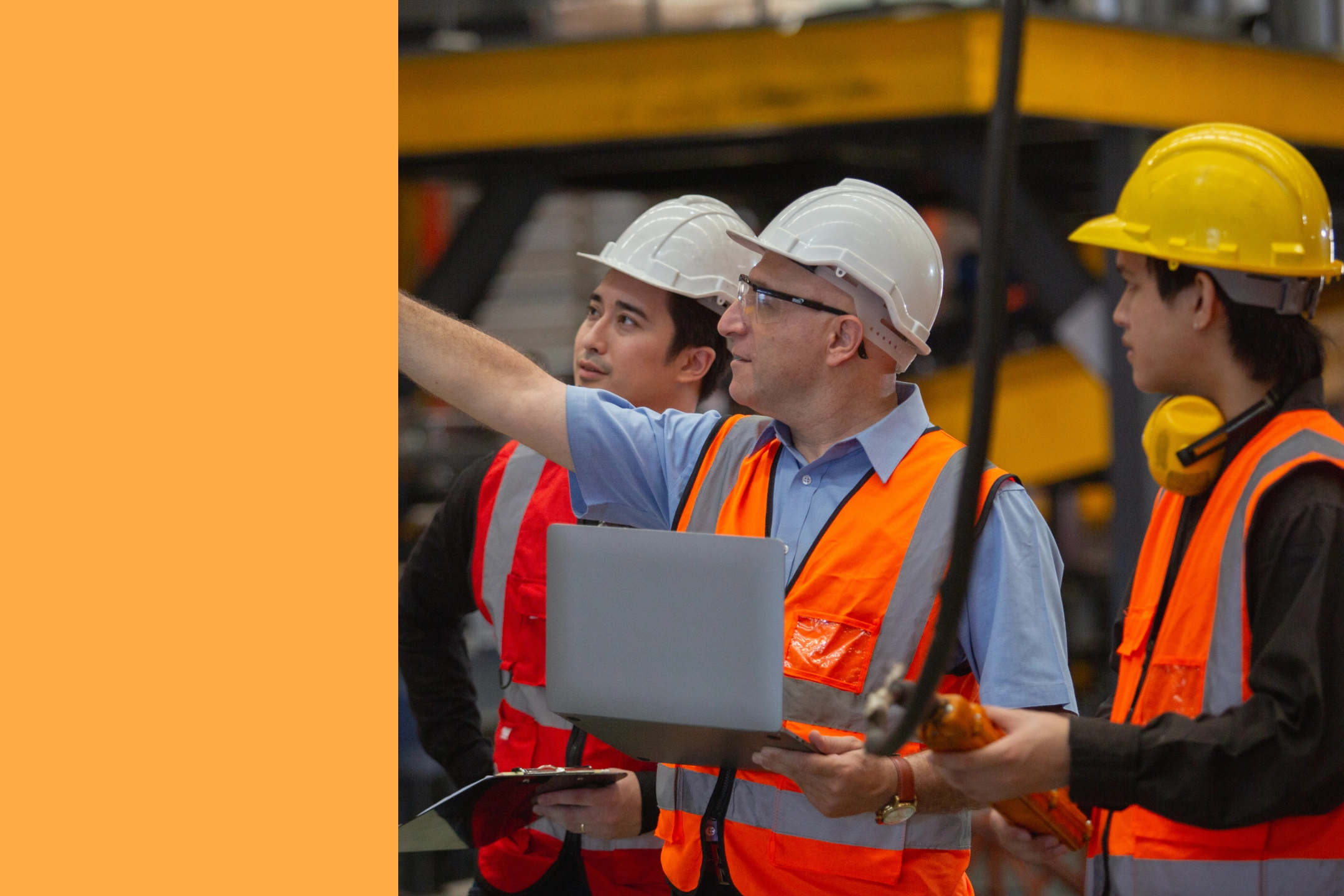
Quer aprimorar sua estratégia de manutenção ou implementá-la do zero? Escolher a estratégia de manutenção correta pode significar a diferença entre um sistema de operações otimizado e um com interrupções e tempo de inatividade.
Embora certos princípios possam ajudar qualquer pessoa a melhorar sua manutenção, uma abordagem única para todos não é a solução mais eficiente ou econômica, pois nem todo ativo precisa do mesmo tipo ou nível de manutenção.
Neste guia, explicaremos cinco tipos diferentes de estratégias de manutenção, como escolher a melhor estratégia de manutenção para seus ativos e como implementar cada estratégia em sua empresa.
Quais são os 5 tipos diferentes de estratégias de manutenção?
Os cinco tipos diferentes de estratégias de manutenção incluem:
- Manutenção reativa
- Manutenção preventiva
- Manutenção baseada em condições
- Manutenção centrada na confiabilidade
- Manutenção preditiva
Manutenção reativa (manutenção de avarias)
O que é manutenção reativa?
UM manutenção reativa A estratégia, também conhecida como manutenção contínua até a falha, envolve atrasar todo o trabalho de manutenção até que os ativos funcionem mal ou quebrem.
Esse programa de gerenciamento de manutenção exige pouco trabalho proativo por parte da equipe e, em muitos aspectos, parece ser a abordagem mais óbvia. Afinal, por que consertar o que não está quebrado?
Digamos que você tenha um orçamento de manutenção limitado e uma pequena equipe dedicada ao trabalho de manutenção e confiabilidade. Tirar várias horas do cronograma de produção para ajustar equipamentos e máquinas que parecem estar funcionando bem pode não ser uma abordagem viável ou intuitiva.
No entanto, você precisa ter cuidado, pois uma estratégia de manutenção puramente reativa pode levar ao caos. Como uma geleira submersa na água, as aparências enganam: não é inédito que máquinas e equipamentos que funcionam perfeitamente bem quebrem sem aviso prévio. E, se você estiver administrando uma instalação com equipe de manutenção limitada, o tempo de inatividade não planejado pode causar sérias perdas de receita e produtividade.
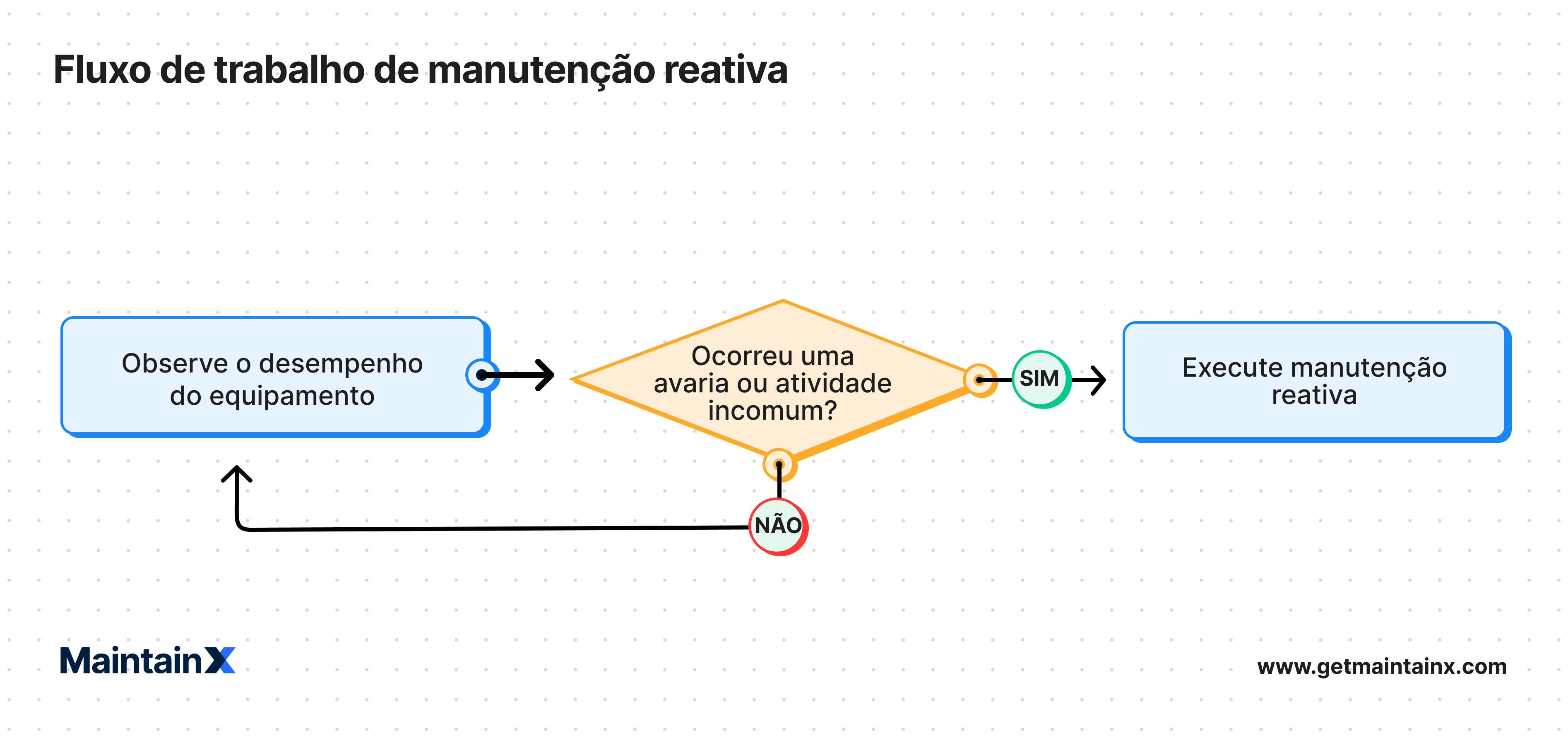
Qual é a quantidade perfeita de manutenção reativa?
Com que frequência você deve planejar deixar o equipamento falhar? Embora não haja uma quantidade “perfeita” de manutenção reativa, especialistas recomendar a adoção de uma abordagem 80/20 (baseado vagamente no Princípio de Pareto), em que 80% das atividades de manutenção se concentram no trabalho proativo e os 20% restantes no trabalho reativo.
Por que se preocupar com a manutenção reativa?
Se a manutenção proativa ocupar 80% do seu tempo, provavelmente parece uma abordagem mais benéfica do que reativa. E embora seja aconselhável evitar avarias na maioria dos casos (falaremos mais sobre isso em breve), você não deve abandonar completamente o trabalho reativo. A manutenção reativa é inevitável; apesar de seus melhores esforços, falhas e avarias acontecerão.
Embora você queira limitar a quantidade de manutenção reativa que você executa, você deve ter um robusto manutenção corretiva plano estabelecido para quando as coisas falharem. A manutenção corretiva se refere às ações tomadas para corrigir um defeito ou restaurar a funcionalidade de um equipamento. Ter um plano de ação corretiva em vigor significa que, quando o equipamento fica inativo, você não perde tempo tentando descobrir como restaurar a funcionalidade. Sem um plano estabelecido, você enfrentará obstáculos, incluindo montar a equipe de manutenção certa, entender o problema e determinar como resolvê-lo. Como resultado, você pode ter dificuldades para que as operações voltem a funcionar o mais rápido possível.
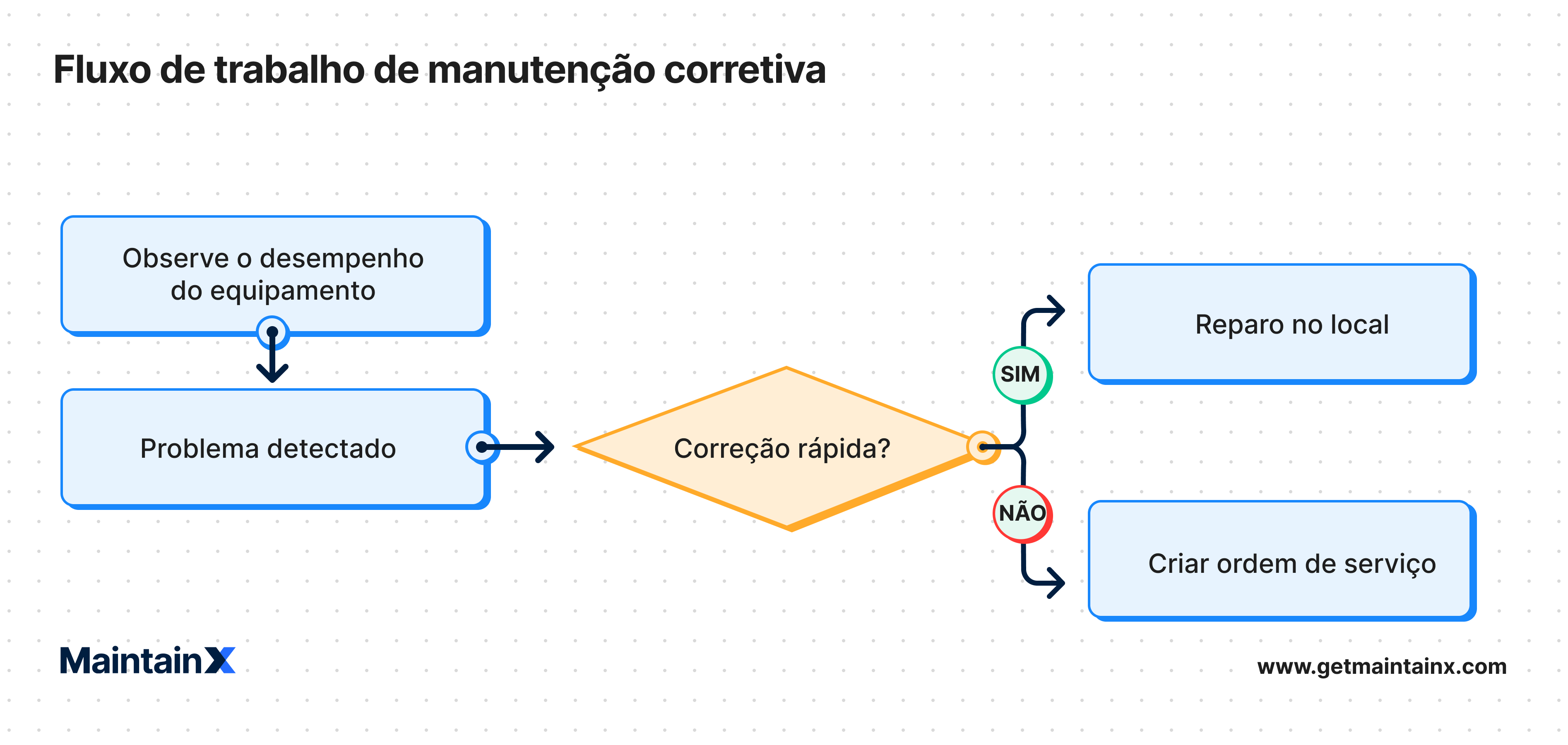
Quando escolher a manutenção reativa
Ao considerar a implementação de uma estratégia de manutenção reativa, pondere o custo de realizar a manutenção regular em relação ao custo da falha do ativo. Se o custo da manutenção proativa contínua superar o custo do tempo de inatividade, reparo e substituição, a manutenção reativa é o programa de manutenção certo para esse ativo. Os custos de manutenção nunca devem exceder os decorrentes de uma avaria.
Limitações da manutenção reativa
Embora um dos principais atrativos da manutenção reativa seja seu baixo custo, os ganhos de curto prazo decorrentes da limitação das atividades apenas aos ativos que quebram geralmente podem ser compensados por perdas significativas no longo prazo decorrentes do aumento do tempo de inatividade e das interrupções na produção.
E, em alguns casos, fixando ativos depois eles quebram podem ser mais caros do que prevenção eles pararam de se decompor em primeiro lugar. Reparos de emergência e peças de reposição podem ser mais caros do que trabalhos de manutenção regulares, pois tendem a exigir tempo e recursos para restaurar a disponibilidade.
Na maioria das vezes, porém, com a manutenção reativa, você simplesmente não sabe. Você não sabe que tipo de dia vai ter, que tipo de cronograma esperar de forma realista, qual produção esperar e como fazer planos sérios. Você entra todos os dias sabendo que existe a possibilidade de alguém te pegar no corredor e te impedir de almoçar porque algo precisa ser consertado imediatamente.
Como gerente de manutenção, você quer poder planejar seu dia sabendo que, na maioria das vezes, as coisas seguirão um cronograma definido. Você pode fazer pausas em determinados horários, conversar com os funcionários em outros horários e agendar reuniões quando for conveniente. Apoiar-se inteiramente em uma estratégia reativa significa que tudo está no ar, o que coloca muita pressão sobre os líderes.
Como diz Sara Ghali, gerente de produto da MaintainX: “Imagine que você está dirigindo um carro e ele quebra no meio da estrada. Seus passageiros estão agitados e confusos com o que está acontecendo. Você deveria saber o que fazer, e todo mundo está procurando uma solução para você. O que você está sentindo naquele momento é estresse, que não é a abordagem lúcida de que você precisa ao decidir como consertar o equipamento.”
Confiar apenas em um programa de manutenção reativa também apresenta riscos desnecessários às suas operações. Avarias inesperadas do equipamento representam um risco de segurança para os operadores e funcionários no chão de fábrica. A falta de manutenção e inspeção regulares pode levar a violações regulatórias e de conformidade e multas. E a imprevisibilidade da quebra de ativos torna difícil orçar e alocar recursos adequadamente, colocando uma pressão sobre os recursos da empresa.
Manutenção preventiva (manutenção planejada ou programada)
O que é manutenção preventiva?
Ao contrário da manutenção reativa, manutenção preventiva (PM) visa evitar que avarias ocorram em primeiro lugar. É uma estratégia de manutenção proativa baseada em atividades regulares e recorrentes que protegem os ativos, mantêm os equipamentos em boas condições de funcionamento e evitam paradas não planejadas.

A manutenção preventiva pode seguir um cronograma baseado no uso, calendário e período de tempo. Esses tipos de manutenção programada se enquadram em manutenção periódica.
Quando escolher a manutenção preventiva
O PM é mais eficaz quando o desgaste de equipamentos e peças segue um padrão previsível, permitindo que você agende a manutenção com base em intervalos de tempo ou uso. Além disso, seguir as diretrizes do fabricante para manutenção garante a conformidade com as condições da garantia e se alinha às melhores práticas estabelecidas com base em testes extensivos.
A manutenção preventiva faz muito mais do que apenas manter os ativos disponíveis para produção. Ao manter o equipamento em boas condições de funcionamento, você pode garantir a eliminação de possíveis problemas de qualidade devido ao mau funcionamento do equipamento. O equipamento ideal fornecerá produtos ideais.
Em última análise, a manutenção é colaborativa e, embora reduzir o tempo de inatividade não planejado seja um dos principais benefícios da manutenção preventiva, essa estratégia de manutenção trabalha lado a lado com o gerenciamento de qualidade e segurança.
Além disso, com uma estratégia reativa, você não só não tem ideia de quando seus ativos falharão, mas também de como. É sempre um sorteio entre pequenas falhas e avarias com graves consequências para a saúde e a segurança. Assumir o controle com a manutenção preventiva significa que você pode reduzir significativamente o risco de falhas catastróficas que comprometem a segurança de sua equipe e de suas instalações.
Para criar uma estratégia eficaz de implementação de PM, comece com um inventário completo dos ativos. Em seguida, determine as prioridades definindo os equipamentos que exigem manutenção regular e são essenciais para a produção e a segurança.
Determine seus intervalos de PM ideais com base na capacidade de sua força de trabalho, nos requisitos de ativos individuais e nos requisitos do regulador. Depois de programar e implementar ordens de serviço recorrentes, certifique-se de avaliar constantemente seu progresso para identificar áreas para melhorar e ajustar seus planos de manutenção quando necessário.
Exemplos de PM incluem:
- Realizar verificações rotineiras de lubrificação e alinhamento em motores elétricos para evitar superaquecimento e garantir uma operação eficiente, seguindo um cronograma baseado nas horas de operação.
- Substituir filtros e inspecionar dutos em intervalos regulares para manter a qualidade do ar e a eficiência do sistema, evitando avarias inesperadas e prolongando a vida útil do equipamento.
Considere quanto tempo um ativo durará sem manutenção e quanto custará substituí-lo e, em seguida, compare isso com o custo potencial de operar PMs regulares por esse período. Além disso, determine se esses ativos têm modos de falha que a manutenção regular pode evitar. Se um ativo só apresentar falhas devido a erros aleatórios que a manutenção preventiva não consegue resolver, a manutenção preventiva desperdiça tempo e dinheiro e se torna redundante.
Limitações da manutenção preventiva
A manutenção preventiva é uma abordagem econômica que economiza dinheiro ao evitar avarias e quaisquer perdas de produção consequentes. O princípio orientador é que as horas e os recursos gastos em atividades rotineiras serão menos do que aqueles que, de outra forma, seriam usados para restaurar a funcionalidade dos ativos durante o tempo de inatividade.
No entanto, encontrar esse equilíbrio pode ser um desafio. A manutenção preventiva mal planejada pode levar a trabalhos de manutenção redundantes ou desnecessários, ocupando ativos e recursos humanos que poderiam ser úteis em outros lugares. E gerenciar várias programações de PM para uma variedade de ativos pode se tornar cada vez mais complicado.
Além disso, uma estratégia de manutenção preventiva é redundante para ativos não reparáveis ou de uso único. Geralmente, é melhor substituir ativos que estão chegando ao fim de seus ciclos de vida ou que não podem ser reparados, em vez de investir tempo e esforço para prolongar suas vidas já limitadas.
Manutenção baseada em condições (CBM)
O que é manutenção baseada em condições?
A Manutenção Baseada em Condições (CBM) é uma estratégia de manutenção proativa focada em monitorar e avaliar a condição real de equipamentos e ativos para determinar quando você deve realizar a manutenção. O CBM depende do monitoramento contínuo ou periódico da condição do equipamento usando várias ferramentas e técnicas de diagnóstico. Os métodos comuns incluem análise de vibração, termografia, análise de óleo e testes ultrassônicos.
O CBM pode minimizar o tempo de inatividade e reduzir os custos gerais de manutenção. Com essa estratégia, você inicia tarefas de manutenção quando determinados indicadores sugerem uma diminuição no desempenho ou uma falha iminente. O CBM é uma abordagem reativa que pode ser menos complexa e cara em comparação com a manutenção preditiva, que discutiremos abaixo.
Por exemplo, uma aplicação comum de manutenção baseada em condições envolve o uso de leituras de pressão em sistemas de tubulação. A equipe de manutenção monitora constantemente os níveis de pressão, permitindo identificar quando possíveis vazamentos podem ocorrer. Organizações que dependem de sistemas de tubos ou líquidos, como produtores de alimentos e bebidas, usam o CBM para rastrear a pressão e diagnosticar problemas.

6 técnicas primárias de monitoramento baseado em condições
As tecnologias CBM coletam dados continuamente enquanto o equipamento opera. Esses dispositivos registram números em determinados intervalos ou continuamente por meio de inspeções visuais, sensores e testes programados. As seis técnicas primárias de monitoramento baseadas em condições incluem o seguinte:
Análise de vibração: Esse tipo de sistema de monitoramento baseado em condições mede as frequências e os níveis de vibração do maquinário. As equipes de manutenção então usam essas informações para analisar a integridade do equipamento e de seus componentes para detectar problemas, como eixos curvados, ressonância, folga, falha de rolamento e desequilíbrio. Por exemplo, um ventilador danificado produzirá mais sinais de vibração.
Termografia infravermelha: A termografia infravermelha é um sistema de monitoramento baseado em condições que usa termovisores para detectar a radiação de um objeto. Os imageadores convertem a radiação em temperatura e exibem sua distribuição em tempo real. Esse processo ajuda a detectar quando um equipamento está superaquecendo. Exemplos de ferramentas de infravermelho incluem câmeras de imagem térmica infravermelha, sistemas de escaneamento infravermelho e termógrafos infravermelhos. As equipes de manutenção os usam principalmente para verificar os níveis de gás, líquidos e lodo; inspecionar rolamentos; examinar o isolamento refratário; e monitorar as condições mecânicas e elétricas dos motores.
Análise ultrassônica: A análise ultrassônica detecta e converte sons de alta frequência em dados digitais e de áudio para ajudar a identificar ativos potencialmente falhos. Esse sistema de monitoramento baseado em condições usa métodos de coleta de dados com e sem contato para determinar diferentes tipos de falhas detectáveis. Os métodos de contato (baseados na estrutura) geralmente detectam falhas que geram ruído de alta frequência, como problemas de lubrificação, falhas nos rolamentos, barras de rotor quebradas e danos na engrenagem. Os métodos sem contato (aéreos), por outro lado, ajudam a detectar vazamentos de pressão e vácuo em sistemas de gás comprimido, além de várias aplicações elétricas.
Análise de óleo: As equipes de manutenção analisam a integridade do óleo, a contaminação e o desgaste da máquina. Eles podem determinar se os aditivos estão ativos ou esgotados e se a viscosidade está correta, entre outras propriedades do fluido de óleo. Um programa de análise de óleo ajudará a confirmar se um equipamento está funcionando como deveria.
Análise elétrica: Aqui, o foco está na qualidade da energia de entrada dos ativos. A corrente do circuito é medida usando leituras de corrente do motor de amperímetros de fixação. A análise elétrica ajuda a determinar se um ativo tem um fornecimento de eletricidade anormal.
Análise de pressão: É importante que os equipamentos que transportam ar, gás ou fluido mantenham a pressão correta. As equipes de manutenção usam a análise de pressão para monitorar continuamente os níveis de pressão em tempo real. Eles recebem alertas sobre quedas ou picos repentinos e podem responder antes que se tornem mais graves.
Quando escolher a manutenção baseada em condições
A manutenção baseada em condições é mais eficaz quando aplicada a equipamentos e ativos críticos que poderiam impactar significativamente a produção, a segurança ou as operações em caso de falha ou ter altos custos de manutenção e reparo. O CBM funciona melhor com ativos que têm modos de falha bem definidos e sofrem desgaste gradual e previsível ao longo do tempo. Antes de escolher o CBM, certifique-se de ter acesso imediato às tecnologias de monitoramento, como sensores, que sejam compatíveis com seu equipamento.
Limitações da manutenção baseada em condições
O CBM oferece várias vantagens, mas também é importante reconhecer suas limitações. Em primeiro lugar, os custos iniciais da implementação de sistemas de monitoramento baseados em condições podem ser altos devido à necessidade de investir em sensores, medidores e outros instrumentos de monitoramento.
A manutenção baseada em condições também pode ser menos eficaz em condições de trabalho severas, nas quais os sensores são vulneráveis a danos ou expostos a ruídos. Além disso, o CBM é mais eficaz para ativos críticos que têm modos de falha bem documentados, nos quais a detecção precoce de problemas pode evitar quebras de custos. Para equipamentos menos críticos ou mais simples, o custo e o esforço da implementação do CBM podem ser difíceis de justificar.
Manutenção centrada na confiabilidade (RCM)
O que é manutenção centrada na confiabilidade?
Manutenção centrada na confiabilidade (RCM) concentra-se na criação de abordagens sistemáticas e estruturadas para manter ativos individuais. Seu objetivo principal é garantir que os esforços de manutenção se concentrem em atividades que maximizem a confiabilidade e o desempenho dos ativos e, ao mesmo tempo, minimizem os custos e os riscos operacionais. O RCM envolve primeiro realizar uma análise detalhada dos possíveis modos de falha e seu impacto potencial e, em seguida, criar planos personalizados para evitá-los.
O RCM visa responder a quatro perguntas críticas sobre a manutenção de ativos individuais:
- Quais são as funções do ativo? Como isso funcionou no passado?
- Quais são os possíveis modos de falha e as causas de cada ativo?
- Quais são as consequências dessas falhas em termos de segurança, impacto ambiental e perdas financeiras?
- Quais tarefas de manutenção, sejam proativas (preventivas) ou corretivas, as equipes devem aplicar para mitigar essas consequências?
Você quer avaliar as possíveis consequências das falhas para descobrir como evitá-las. Repita isso para todos os ativos, criando uma abordagem de manutenção personalizada para cada equipamento, melhorando a confiabilidade e garantindo que os ativos permaneçam disponíveis o tempo todo.

Quando escolher a manutenção centrada na confiabilidade
Se você precisar atribuir estratégias de manutenção com base nas necessidades específicas do equipamento, o RCM é uma ótima ideia. Em vez de aplicar uma estratégia de manutenção (preventiva, reativa ou preditiva) em toda a instalação, o RCM otimiza os dados para personalizar as soluções classificando os ativos de acordo com a criticidade. Dessa forma, o RCM é uma boa opção para instalações com ativos que variam significativamente em termos de criticidade e ajuda as equipes a otimizar os recursos com base na prioridade.
Limitações da manutenção centrada na confiabilidade
Ao fornecer soluções personalizadas para diferentes ativos, o RCM pode ser incrivelmente poderoso ao lidar com equipamentos cujo mau funcionamento pode ter impactos desastrosos na receita, na produção e na segurança. No entanto, a criação dessas soluções exige dados de manutenção detalhados, um processo de integração elaborado e muito tempo e recursos.
Se você tem os recursos para dedicar uma equipe para integrar o RCM em seus ativos ou está disposto a trabalhar com um parceiro experiente nesse campo, isso pode ser para você.
Da mesma forma, se você tiver registros de manutenção detalhados e claros, será mais fácil implementar o RCM. Sem os dados adequados, o RCM pode ser mais desafiador do que vale a pena.
Manutenção preditiva (PdM)
O que é manutenção preditiva?
Ao contrário da manutenção baseada em condições reativas, manutenção preditiva (PdM) é uma forma de manutenção proativa que funciona usando informações sobre as condições do equipamento (como temperatura, pressão e outros fatores de integridade do ativo) para prever uma falha iminente.
Ao contrário da manutenção baseada em condições, o baseado em condições os dados coletados incorporam algoritmos avançados de análise, mineração de dados e aprendizado de máquina, que buscam padrões e tendências para prever o estado futuro do ativo. As equipes de manutenção podem usar as previsões de tempo de inatividade do equipamento para isolar as tarefas de manutenção apenas nos ativos mais necessários para reduzir qualquer trabalho de manutenção redundante.
A principal distinção entre CBM e PdM é que o PdM se concentra na previsão de condições futuras para otimizar o planejamento de manutenção, enquanto o CBM reage principalmente às condições atuais do equipamento.
IIoT e manutenção preditiva
O PdM usa sensores de monitoramento de condições para rastrear as condições do equipamento em tempo real. Esses sensores funcionam por meio do IIoT (Internet industrial das coisas), que são dispositivos e instrumentos interconectados em rede com aplicativos de computador para aprimorar a fabricação, a manutenção e outras atividades industriais.
Exemplos de dispositivos sensores de PdM são equipamentos de análise de vibração, tecnologia acústica ultrassônica e outros equipamentos que monitoram fatores relacionados à integridade do equipamento.
O PdM alimenta os dados coletados por meio dos sensores em algoritmos de aprendizado de máquina para prever possíveis falhas comparando o comportamento atual de um ativo com o comportamento esperado. Nesse caso, a detecção de anomalias (comportamento anormal) aciona o PdM.
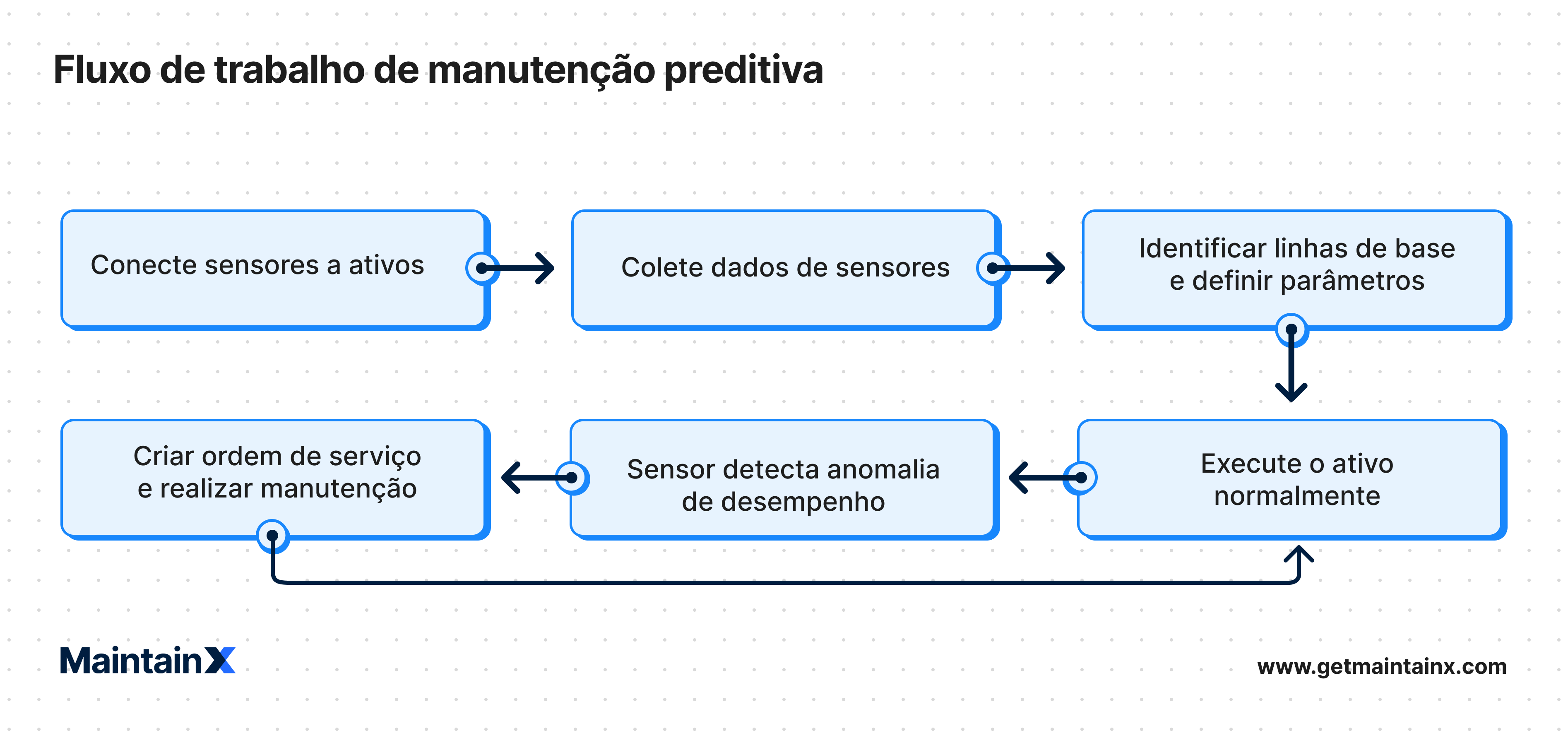
Quando escolher a manutenção preditiva
A implementação da manutenção preditiva só faz sentido quando você tem os recursos necessários de coleta e análise de dados, pois ela depende muito do monitoramento e da análise em tempo real das condições do equipamento por meio de algoritmos preditivos complexos. Sem a infraestrutura necessária instalada ou a vontade de investir na infraestrutura necessária, é difícil implementar uma estratégia de manutenção preditiva com sucesso. No entanto, para equipes de manutenção prontas ou dispostas a investir em manutenção preditiva, você pode aumentar a confiabilidade dos ativos, diminuir os custos de manutenção e reduzir o tempo de inatividade não planejado.
Gráfico resumido das estratégias de manutenção
Escolhendo a estratégia de manutenção certa para sua instalação
Na prática, será difícil encontrar uma instalação que dependa exclusivamente de uma estratégia. Por mais que um programa de manutenção preventiva ajude a reduzir custos, manter o tempo de atividade e evitar paradas de emergência, um plano de manutenção reativo é necessário para lidar com emergências quando elas ocorrem. Considere esses fatores ao criar seu programa de manutenção:
- Os ativos em questão: examine minuciosamente seu registro de ativos para determinar qual tipo de manutenção cada ativo exige. O que dizem as diretrizes do fabricante sobre como e quando abordar a manutenção? Alguma regulamentação de conformidade se aplica a equipamentos específicos? O que você e sua equipe de manutenção notam sobre esses ativos e como eles funcionam quando usados? Considere os custos potenciais da falha do equipamento para cada ativo e o custo do monitoramento do equipamento para priorizar a manutenção em ativos específicos.
- Capacidades e recursos internos: Por mais robustos que sejam seus recursos, você não quer desperdiçar nenhum deles. Pense em maneiras de otimizar sua equipe de manutenção e peças de reposição ao criar uma estratégia de manutenção. Você tem equipe suficiente para implementar cada uma de suas estratégias de manutenção? E quanto custaria confiar estritamente na manutenção reativa?
- Dados, dados, dados: Ao implementar qualquer estratégia, certifique-se de coletar, registrar e analisar dados constantemente. Use esses dados para identificar quais ações produzem os resultados desejados e quais não. “Dados robustos evitam o trabalho e a energia de lembrar coisas”, diz Sara Ghali. “Mesmo na ausência de um especialista, o conhecimento está dentro do sistema. Você não apenas terá acesso ao conhecimento sobre como lidou com problemas no passado, mas também poderá identificar tendências, instituir melhorias incrementais e otimizar seu gerenciamento de tempo.” Com isso em mente, continue reiterando e ajustando sua abordagem de manutenção para melhoria constante.
Leve sua manutenção para o próximo nível
A escolha do tipo certo de manutenção é específica para sua empresa e para cada ativo. Embora estratégias específicas possam parecer perfeitas no papel, a estratégia certa para você sempre será aquela que você pode implementar com sucesso.
Ao começar a implementar a estratégia escolhida, lembre-se de que você não precisa fazer isso sozinho. Reserve um passeio com MaintainX para descubra como nosso sistema computadorizado de gerenciamento de manutenção (CMMS) pode ajudá-lo a criar ou melhorar sua estratégia de manutenção.
Perguntas frequentes
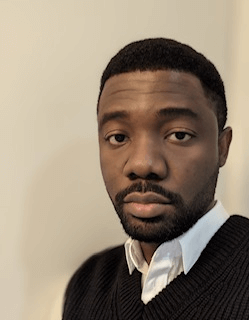
Lekan Olanrewaju é redator de conteúdo com anos de experiência em mídia e criação de conteúdo. Ele ocupou cargos em várias organizações de mídia, trabalhando e liderando equipes em revistas impressas, publicações digitais e produções televisivas.