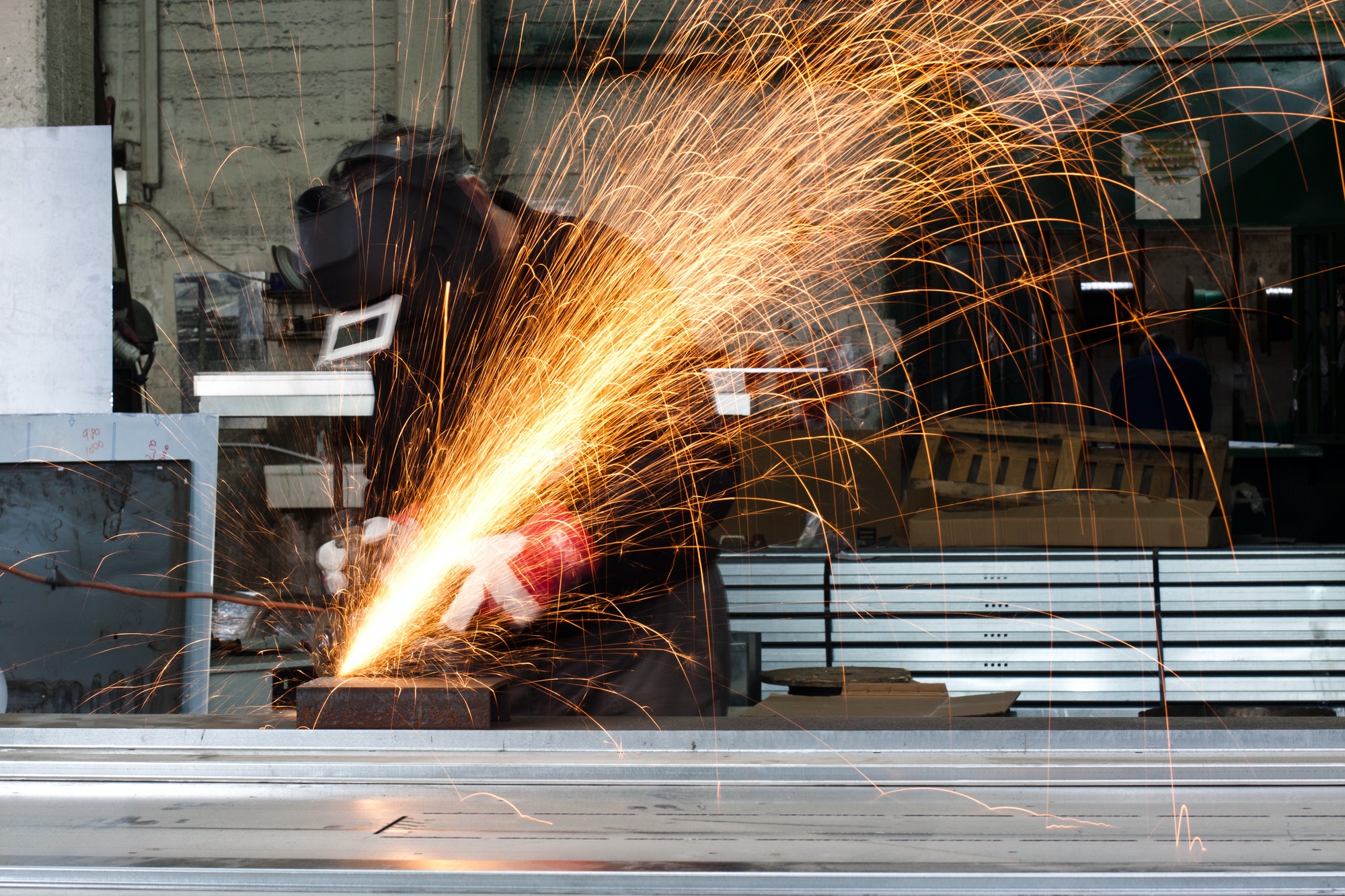
Todos os equipamentos comerciais, desde uma fritadeira em uma cozinha comercial até uma correia transportadora em uma fábrica, acabarão falhando. Embora um plano de manutenção proativo possa mitigar algumas falhas, avarias inesperadas ainda pode acontecer, paralisando a produção, distraindo os técnicos das tarefas rotineiras de manutenção preventiva e custando muito dinheiro à sua organização.
Por esses motivos, O&M (Operação e Manutenção) os gerentes devem tomar medidas proativas para manter o maquinário funcionando de forma ideal, e entender por que o equipamento falha é o primeiro passo para gerenciar o tempo de inatividade imprevisto.
Felizmente, usando sistemas robustos de gerenciamento de manutenção, empregando técnicos qualificados e aproveitando as tecnologias e o software conectados, você pode reduzir consideravelmente as consequências da falha do equipamento em sua organização.
Neste artigo, discutiremos as quatro causas mais comuns de falhas em equipamentos e como evitá-las. A realidade é que você provavelmente não conseguirá eliminar 100% das falhas, mas saberá como começar a reduzir sua ocorrência e impacto nas operações.
O que é falha de equipamento?
Antes de nos aprofundarmos no que causa a falha do equipamento, vamos entrar na mesma página sobre o que é.
Falha no equipamento é uma condição na qual um ativo ou uma máquina não funciona como deveria, ou seja, algo está quebrado. Falhas inesperadas podem ter um impacto significativo nos cronogramas de produção, nos níveis de satisfação do cliente e na qualidade do produto.
A falha do equipamento é mais cara do que você pensa
Embora a perda de tempo de produção seja o problema mais óbvio, as consequências da falha do equipamento são abrangentes:
- O custo de horas extras não planejadas para técnicos
- Custos reduzidos para operadores de máquinas
- O aumento do custo do envio urgente de peças de reposição de fornecedores
- Matérias-primas desperdiçadas, como ingredientes de produção de alimentos perecidos que precisam ser descartados
- Produtos defeituosos ou um aumento acentuado nas falhas de controle de qualidade quando o equipamento está com baixo desempenho
- Redução nos níveis de satisfação do cliente e na percepção da qualidade
- Perda de negócios devido ao não cumprimento das metas do DIFOT ou das datas prometidas
- Custo de oportunidade devido ao excesso de recursos focados na reparação do ativo
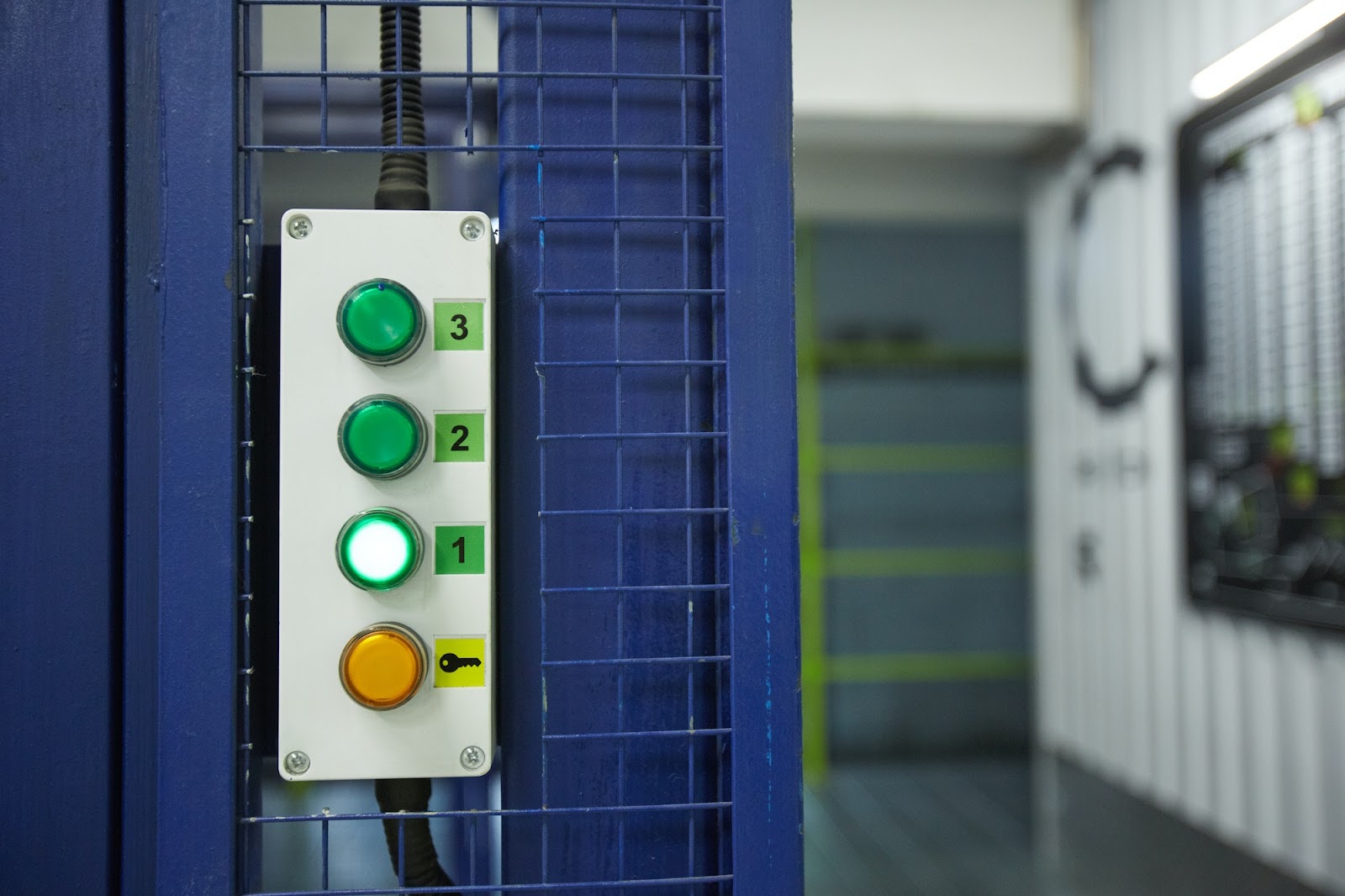
3 tipos de equipamentos que falham
Independentemente do setor — agrícola, manufatura, armazenamento, energia e gás ou serviço de alimentação — falhas no equipamento podem ocorrer em todos os tipos de ativos. A falha em qualquer uma dessas categorias pode impactar fortemente as operações:
- Equipamento alimentado: Essas máquinas dependem de combustível ou motores elétricos para operar. Também conhecida como equipamento pesado, essa categoria inclui tratores, guindastes e empilhadeiras.
- Equipamento mecânico: O equipamento mecânico geralmente inclui componentes móveis que trabalham juntos para realizar uma tarefa específica. Unidades de refrigeração, condensadores, extrusoras, correias transportadoras e compressores de ar são exemplos de equipamentos mecânicos.
- Equipamento não mecânico: O equipamento não mecânico geralmente é menor e não possui partes móveis. A maioria das ferramentas manuais se enquadra nessa categoria, incluindo tubos, linhas de gás, painéis elétricos e ferramentas do sistema HVAC.
Agora, vamos analisar as causas mais frequentes de avarias nas máquinas.
As 4 causas comuns de falha do equipamento
A maioria dos tipos de falha de equipamento é causada por um dos quatro motivos mais comuns:
- Equipamento de envelhecimento
- Erro do operador
- Falta de manutenção preventiva
- Manutenção excessiva
Felizmente, tudo isso pode ser evitado com os processos, procedimentos e tecnologia corretos.
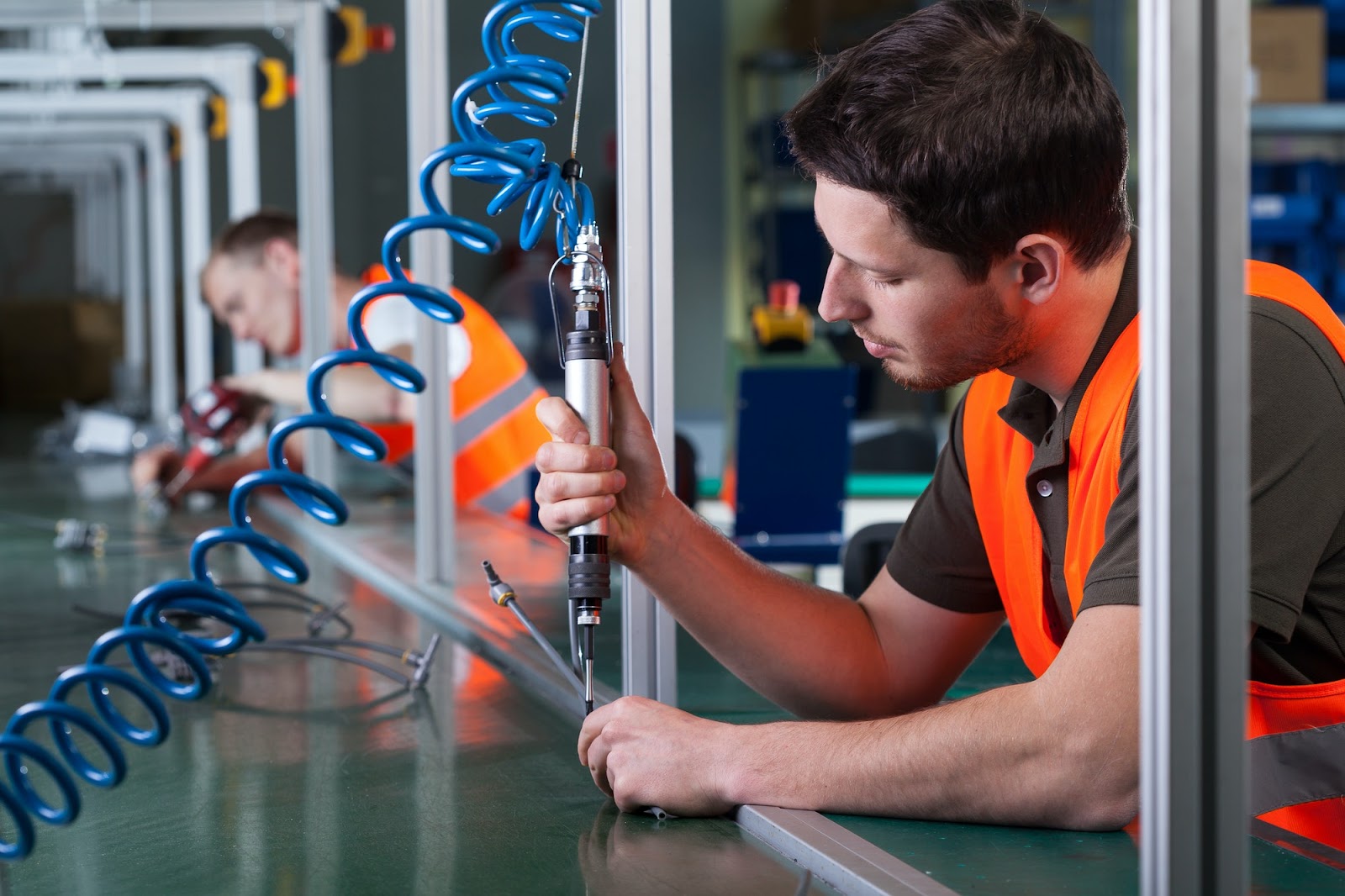
1. Equipamento de envelhecimento
De acordo com o Estudo de Manutenção de Engenharia de Fábrica, equipamentos envelhecidos são a principal causa de falhas de equipamentos, representando 40 por cento dos equipamentos não planejados tempo de inatividade em plantas.
Os ativos que funcionam de forma consistente ano após ano exigem reparos mais frequentes ao longo do tempo.
Infelizmente, essa deterioração natural se traduz em mais dinheiro gasto em peças, taxas de envio de estoque e interrupções na produção. Também exige que os técnicos mudem de manutenção preventiva (PM) para manutenção reativa com mais frequência.
Além disso, quanto mais desatualizado um ativo se torna, mais difícil é adquirir peças de reposição. Como os fabricantes geralmente produzem quantidades menores de peças de reposição antigas, os gerentes de equipamentos antigos geralmente têm dificuldade em garantir o que precisam, quando precisam.
Por esses motivos, as plantas devem considerar a possibilidade de permitir ativos que tenham ultrapassado seus vida útil para corra até o fracasso. Embora a compra de novas máquinas seja, sem dúvida, cara, a maioria das organizações economizará dinheiro a longo prazo por meio de despesas de reparo menos frequentes, aumento da produção e maior eficiência gerenciamento de peças.
2. Erro do operador
Outra causa comum de falha do equipamento é o erro do operador — às vezes, os operadores de máquinas cometem erros devido à fadiga, esquecimento, inexperiência ou falta de treinamento. De acordo com o Estado da Manutenção Industrial 2024 relatório, 12% dos entrevistados previram que o erro do operador seria a principal causa de tempo de inatividade não planejado nos próximos doze meses.
A maioria das fábricas prepara os operadores de máquinas para operar adequadamente equipamentos complexos com treinamento adequado e de fácil acesso procedimentos operacionais padrão (SOPs)e diretrizes de segurança claras. No entanto, não é incomum que os trabalhadores trabalhem ocasionalmente em máquinas desconhecidas ao substituir outras.
Um operador não treinado pode não ter o conhecimento especializado necessário para operar a máquina com confiança. Isso pode resultar em uma avaria do equipamento ou em um acidente de trabalho, bem como em uma violação Requisitos de treinamento de operadores da OSHA,
3. Falta de manutenção preventiva
Há uma razão pela qual os programas de manutenção de equipamentos de classe mundial praticam predominantemente a manutenção preventiva: está comprovado que ela diminui o dispendioso tempo de inatividade do equipamento. Estudos sugerem que os programas de PM podem reduzir a falha do equipamento em até 45 por cento.
No entanto, muitos gerentes ainda usam o ditado: “Se não está quebrado, não conserte”.
Embora a manutenção até a falha geralmente seja a estratégia ideal para equipamentos mais antigos e não essenciais, a falta de inspeções planejadas pode levar à perda de sinais precoces de falha iminente e à depreciação do desempenho.
Manutenção contínua versus manutenção preventiva
A manutenção executada até a falha é uma estratégia de manutenção na qual as atividades de manutenção são executadas após a ocorrência de uma falha. É uma estratégia reativa que permite que um ativo se quebre antes de decidir se deve repará-lo ou substituí-lo.
Também conhecido como”manutenção de avarias”, essa estratégia é mais adequada para ativos não críticos, ativos baratos e aqueles com vida útil mais curta. Às vezes, também é usado para equipamentos remotos, como satélites, nos quais é difícil realizar manutenção regular.
No entanto, a manutenção executada até a falha nunca deve ser usada para ativos críticos que afetam a produção e a segurança.
A abordagem alternativa—manutenção preventiva (PM)—envolve o agendamento e a execução da manutenção recomendada de acordo com o tempo ou os intervalos baseados no uso. É uma estratégia proativa mais adequada para equipamentos caros, ativos essenciais e componentes essenciais para a segurança dos funcionários.
Em última análise, as organizações que praticam apenas a corrida até o fracasso perdem a oportunidade de resolver problemas menores antes que eles se tornem grandes problemas. Além disso, tarefas de manutenção frequentemente perdidas ou atrasadas, como lubrificação periódica de peças de equipamentos, podem reduzir a vida útil de um ativo e provocar a necessidade de novas compras de capital.
4. Manutenção excessiva
Pode parecer contra-intuitivo, mas realizar muita manutenção também pode ser prejudicial.
A manutenção excessiva pode acelerar a depreciação de um ativo ao desmontar e reconfigurar constantemente os componentes do equipamento. Essa abordagem excessivamente zelosa pode interromper até mesmo os sistemas mais estáveis, fazendo com que eles se tornem menos eficazes.
Além disso, é mais provável que os técnicos de manutenção “sigam em frente”, vendo as tarefas frequentes como mais um item a ser verificado.
A manutenção excessiva também consome um tempo desnecessário que os técnicos poderiam usar melhor em outros equipamentos.
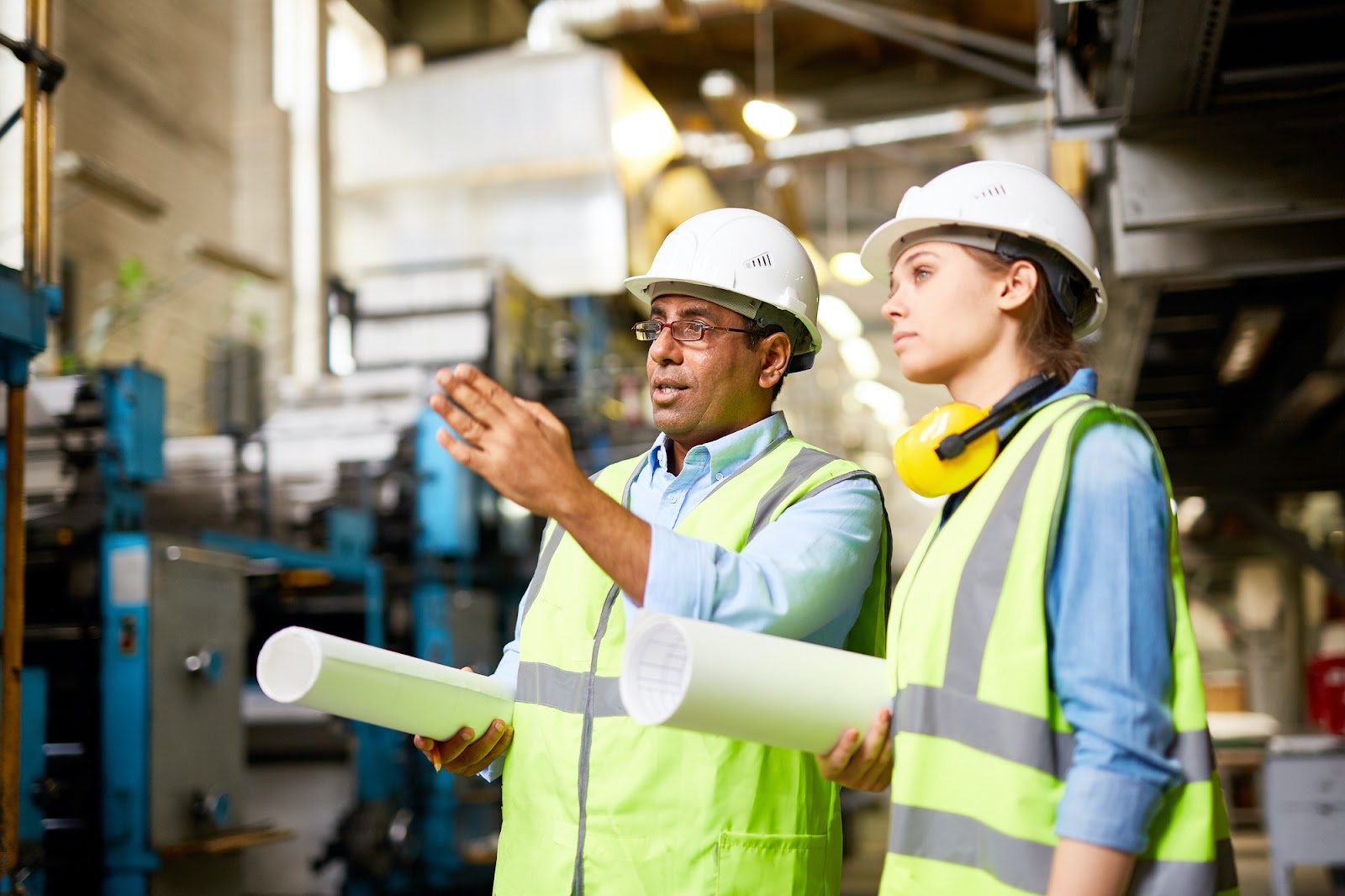
5 maneiras de evitar falhas no equipamento
Conforme mencionado anteriormente, a falha do equipamento pode ser extremamente caro, dependendo do setor. O Estado da Manutenção Industrial 2024 descobriu que “em 2024, o custo médio de uma hora de inatividade não planejada gira em torno de $25.000 e pode subir para mais de $500.000 para organizações maiores”.
Se uma falha no equipamento é gradual, intermitente ou repentina, ela geralmente pode ser atribuída a uma causa raiz. Descobrir o “dominó em queda” original deve ser o objetivo final de todo gerente que deseja aumentar a confiabilidade operacional e reduzir o dispendioso tempo de inatividade.
Os gerentes de manutenção podem usar uma variedade de métodos de análise para ajudar a identificar as causas principais. Os 5 porquês, diagramas de espinha de peixe, e análise de causa raiz são apenas algumas das técnicas dedutivas comumente usadas em manutenção industrial departamentos.
Encontrar a causa raiz, no entanto, é apenas parte da solução. Aqui estão algumas dicas sobre como evitar falhas no equipamento para minimizar o impacto em sua organização e em seus resultados.
Forneça treinamento completo do operador e mantenha a conformidade
Garantir que os operadores de equipamentos recebam treinamento adequado pode ajudar a minimizar as falhas decorrentes de erro humano. Os gerentes também devem criar redundância em suas operações treinando os trabalhadores sobre como usar máquinas que normalmente não operam. Dessa forma, alguém que tenha sido devidamente treinado de acordo com os padrões da OSHA estará sempre disponível.
Da mesma forma, a gerência deve aplicar rigorosamente políticas que impeçam funcionários não treinados de operar máquinas.
Monitore e analise equipamentos digitalmente
Monitorar a integridade dos ativos e garantir contra falhas se torna significativamente mais fácil quando você investe em sistemas conectados e prontos para IoT. Ao conectar medidores e sensores de equipamentos ao seu sistema computadorizado de gerenciamento de manutenção (CMMS), você pode automatizar o rastreamento de ativos e obter uma visão de alto nível de todos os seus ativos em um único painel.
Esse monitoramento remoto de condições permite que sua organização aproveite a economia de tempo e custos por meio da detecção precoce de condições operacionais incomuns antes que um ativo quebre.
Equilibre a manutenção preventiva com a manutenção baseada em condições
As atividades regulares de manutenção preventiva (PM) ajudam a evitar falhas e a prolongar a vida útil dos ativos. Por outro lado, manutenção baseada em condições (CBM) permite ajustes oportunos com base nas condições do ativo (e antes que ocorra uma falha).
A execução simultânea de programas de PM e CBM exige um banco de dados robusto que garanta que todos os equipamentos recebam a quantidade exata de atenção de que precisam no momento certo. Um sistema computadorizado de gerenciamento de manutenção (CMMS) compatível com dispositivos móveis, como o MaintainX, fornece insights, agendamento, gerenciamento de dados e rastreamento de ativos com tecnologia de inteligência artificial para oferecer aos gerentes de manutenção uma visão de 360 graus de seu programa de manutenção.
Anexe SOPs às ordens de serviço
Os procedimentos operacionais padrão (SOPs) garantem que o equipamento seja mantido e reparado adequadamente da mesma maneira todas as vezes.
Ao alocar ordens de serviço para técnicos com um SOP pré-preparado anexado, os gerentes de manutenção podem ter certeza de que reparos, substituição de peças e outras tarefas de manutenção sejam realizadas de forma eficaz para reduzir a ocorrência de avarias futuras.
Execute inspeções de manutenção de rotina
SOPs e listas de verificação também são vitais para atividades de manutenção de rotina e gerenciamento eficaz de ativos. As listas de verificação criadas no MaintainX ajudam os técnicos a realizar inspeções de rotina com facilidade, bem como a criar uma “trilha em papel” para que os gerentes de manutenção analisem a integridade dos ativos e detectem evidências precoces de anomalias — tudo com a conveniência de um aplicativo.
Economize tempo e dinheiro com o Maintain X
Nem sempre é possível superar as falhas do equipamento, mas é possível minimizar seu impacto. CMMS do MaintainX pode ajudar a manter sua equipe de manutenção um passo à frente de avarias inconvenientes e a colocar as máquinas on-line rapidamente quando ocorrerem falhas.
O MaintainX ajuda sua organização a mitigar falhas caras de equipamentos com ferramentas e sistemas para gerenciar a manutenção proativa e reativa. Minimize o tempo de inatividade e maximize a produtividade com um CMMS fácil de usar que permite monitorar a integridade dos ativos em tempo real, atribuir ordens de serviço com rapidez e rastrear o histórico do equipamento para se manter à frente dos problemas.
Perguntas frequentes sobre falhas de equipamentos
Quanto tempo leva para implementar o MaintainX?
Para o cliente médio, leva três semanas para implementar um site. Para clientes dos planos Premium e Enterprise, nossa equipe garante uma transição suave para o MaintainX dentro da sua organização. Trabalhe com um especialista dedicado de implementação por meio de nosso processo estruturado de onboarding de três semanas. Saiba mais sobre nossos serviços de implementação aqui.
O MaintainX é seguro?
O MaintainX está em conformidade com padrões de segurança, incluindo SOC 2, ISO 27001 e GDPR. Ele também oferece suporte a login único (SSO), autenticação multifator (MFA) e permissões e funções personalizadas. Para mais informações, visite nossa página do trust center.
O MaintainX oferece suporte a vários sites?
Sim, o MaintainX Enterprise permite que você gerencie várias plantas ou instalações na mesma plataforma. Você também pode criar painéis de relatórios personalizados para rastrear KPIs em vários sites na mesma tela.
Quais indústrias são mais impactadas por falhas em equipamentos?
Quase todos os setores — da produção de alimentos à indústria automotiva — podem sofrer falhas críticas de ativos. Um sistema de refrigeração em supermercado é tão essencial quanto um robô de solda em uma montadora.
Quais são os sinais de alerta de falha iminente em equipamentos?
Falhas intermitentes, degradação física como carcaças rachadas, vibração excessiva, vazamentos de fluido, acúmulo de contaminantes e temperaturas anormalmente altas são sinais comuns de que há algo errado com equipamentos mecânicos. Ruídos incomuns e aumento inesperado no tempo de produção também são indícios de que é necessário realizar inspeção ou manutenção.
O que deve estar incluído em um plano de resposta a falhas de equipamentos?
O planejamento para falhas de equipamentos começa pela segurança, então certifique-se de que o equipamento esteja isolado, bloqueado ou sinalizado, e que os operadores estejam cientes da falha. Técnicos de reparo podem responder rapidamente se houver procedimentos pré-definidos para lidar com falhas. Procedimentos operacionais padrão devem incluir etapas para inspecionar o equipamento, um processo claro de reparo, como agilizar a obtenção de peças sobressalentes e como mitigar o impacto na produção diária.
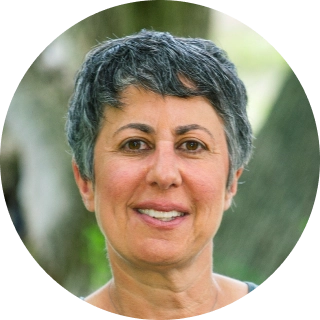
Caroline Eisner é escritora e editora com experiência nos setores de fins lucrativos e sem fins lucrativos, governo, educação e organizações financeiras. Ela ocupou posições de liderança em instituições de ensino fundamental e médio e liderou projetos digitais de grande escala, sites interativos e uma consultoria de redação comercial.