
O que é o FMEA?
FMEA significa Análise de efeitos e modos de falha. É uma análise de engenharia realizada para avaliar as possíveis causas de falhas operacionais relacionadas ao design do produto, à produção da linha de montagem e às avarias dos equipamentos de fabricação.
Não importa o negócio, o objetivo final do FMEA é simples: manter a produção de produtos de alta qualidade em andamento! Para esse fim, o processo de FMEA envolve a adoção de ações baseadas em dados para evitar que qualquer contratempo concebível aconteça desde o projeto até o envio.
De acordo com a Sociedade Americana de Qualidade, o FMEA exige que uma equipe multifuncional de especialistas no assunto discuta como o equipamento pode falhar e seus efeitos. As equipes do FMEA analisam os processos atuais de sistemas, subsistemas e montagens organizacionais passo a passo para conceber cada resultado potencial.
Além de apoiar a confiabilidade do equipamento, os dados do FMEA também podem fornecer informações que ajudam a promover melhores estratégias de manutenção, medidas de segurança e conformidade regulatória.
FMEA versus FMECA
Em algum momento, você também pode ter se deparado com o termo Modos de Falha, Efeitos e Análise de Criticalidade (FMECA). Tanto o FMEA quanto o FMECA são metodologias que os profissionais de manutenção usam para identificar, avaliar e abordar possíveis modos de falha.
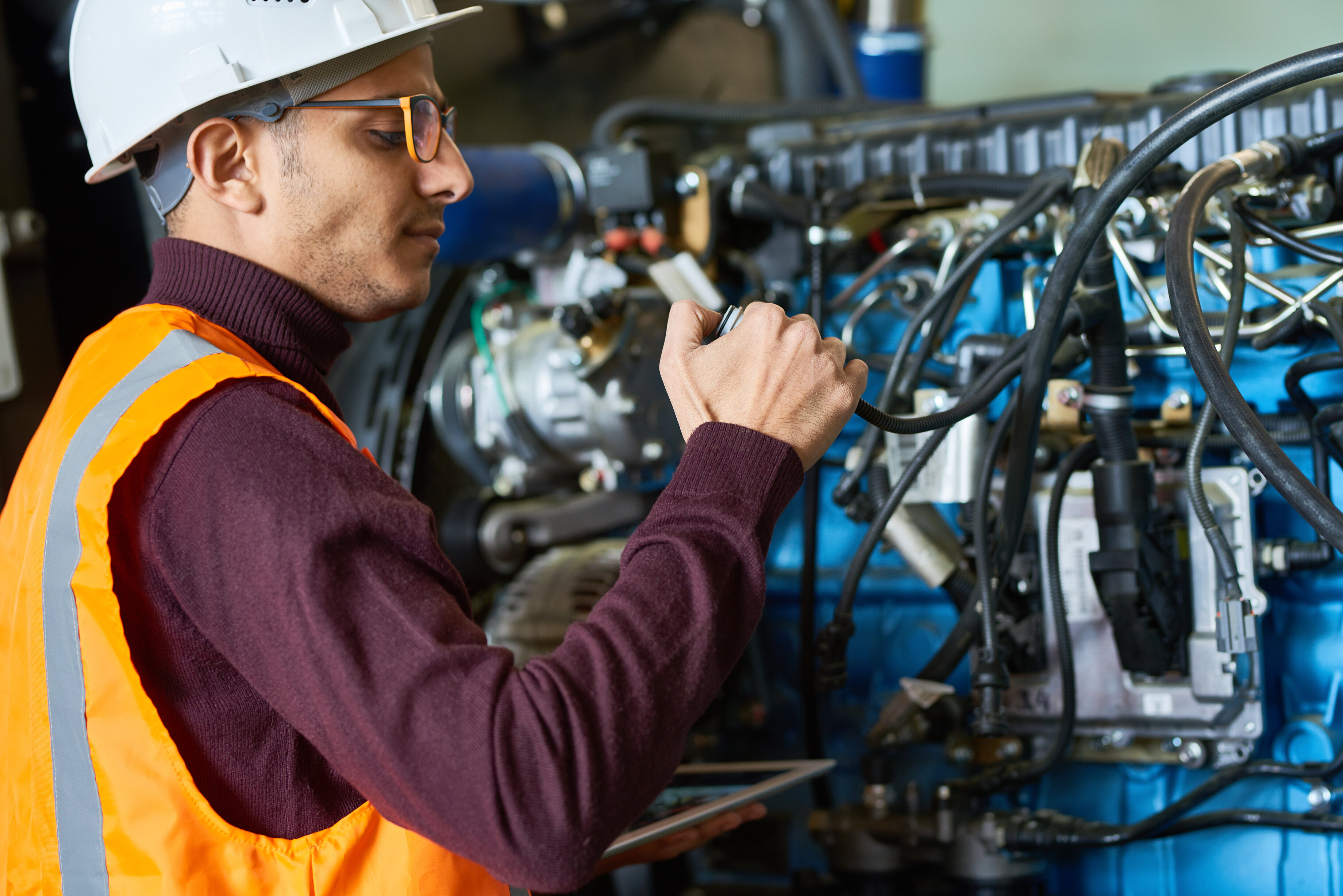
Embora o FMEA seja uma excelente ferramenta para gerar informações qualitativas, o FMECA incorpora uma avaliação adicional chamada de análise de criticidade na mistura.
A ISO 31000:2009: Princípios e Diretrizes de Gestão de Riscos descreve uma análise de criticidade como o processo de atribuir aos ativos uma classificação de criticidade com base em seus riscos potenciais.
Nesse caso, qualquer fator que introduza incerteza no alcance das metas de produção é classificado como um “risco”. Simplificando, o FMECA é o FMEA+, uma análise de criticidade.
É mais provável que fabricantes, armazéns e fornecedores de petróleo e gás usem esse componente adicional para informar os programas de manutenção baseados em sensores.
Com isso dito, tanto a FMEA quanto a FMECA ajudam as organizações a atender às crescentes demandas dos clientes, permitindo que elas forneçam produtos de qualidade, funcionais e seguros. No entanto, no restante deste artigo, vamos nos concentrar nos meandros do FMEA.
A história do FMEA
Durante a década de 1940, o As Forças Armadas dos EUA desenvolveram o FMEA classificar as falhas “de acordo com seu impacto no sucesso da missão e na segurança de pessoal/equipamento”.
Avance para meio bilhão de pessoas assistindo Neil Armstrong dar “um pequeno passo para o homem e um grande salto para a humanidade” em 1969. A maioria dos espectadores não percebeu que a Apollo 11 nunca teria pousado na lua sem o FMEA.
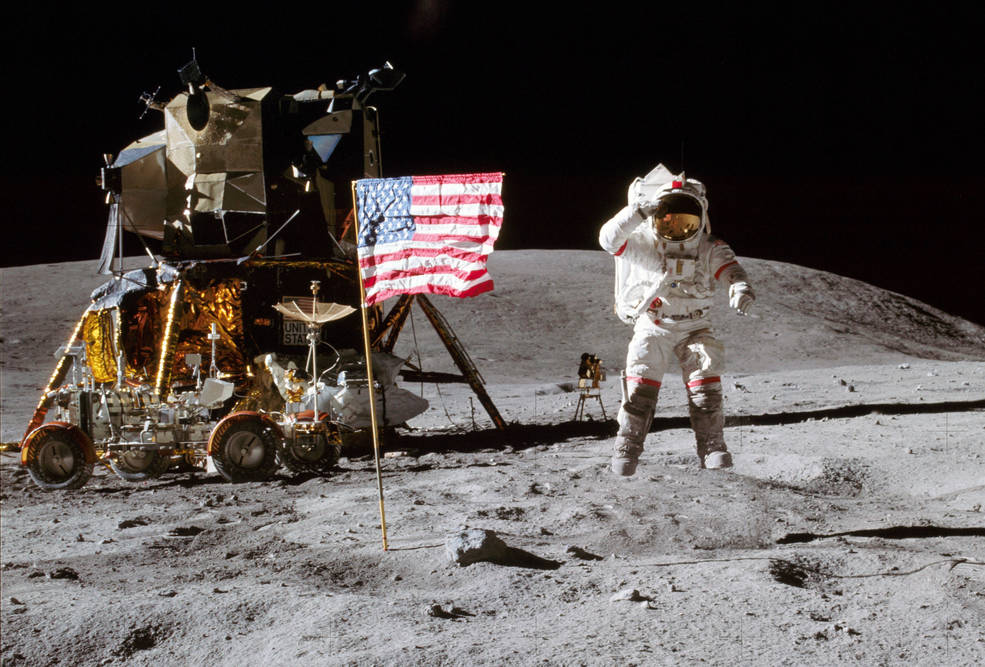
Durante uma entrevista para o Projeto de História Oral do Johnson Space Center, Armstrong disse que as especificações de confiabilidade de hardware da NASA permitiram até quatro falhas em cada 100.000 operações.
“Só posso atribuir isso ao fato de que cada pessoa no projeto, cada cara na bancada construindo alguma coisa, cada montador, cada inspetor, todo cara que está configurando os testes, acionando a chave dinamométrica e assim por diante, está dizendo: 'Se alguma coisa der errado aqui, não será minha culpa, porque minha peça vai funcionar melhor do que eu tenho para fazê-la. '”
Ele continuou dizendo que sua equipe não teria tido sucesso sem o compromisso de milhares de trabalhadores da NASA com excelência operacional. Logo após a NASA adotar o FMEA, outras indústrias importantes dependentes da confiabilidade do equipamento — automotiva, saúde, mineração e petróleo — seguiram o exemplo.
Como o FMEA se relaciona com a manutenção?
O FMEA ajuda os profissionais de manutenção a responder à velha pergunta: o que devemos corrigir primeiro? Priorizar a manutenção de centenas de milhares de máquinas e peças não é fácil.
Todo gerente de O&M sabe que correr manutenção preventiva em ativos críticos é o ideal, mas isso não significa que isso sempre aconteça. Orçamentos limitados, restrições de tempo e escassez de mão de obra geralmente forçam os líderes operacionais a tomarem decisões difíceis ao atribuir ordens de serviço.
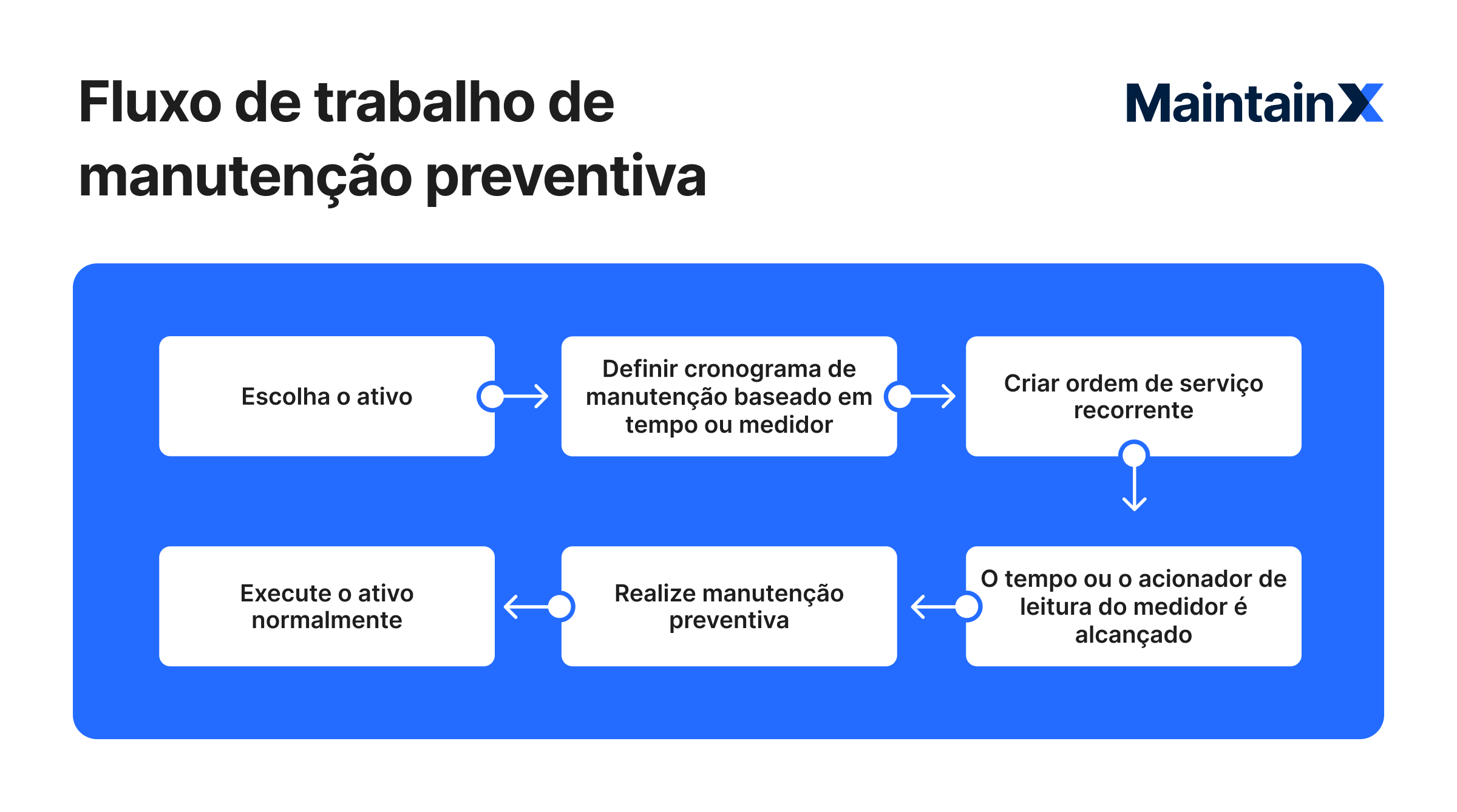
É aqui que o FMEA pode ser particularmente útil. Os líderes de manutenção podem usar essa abordagem sistemática para identificar o potencial. falha de equipamento modos, estime a frequência de sua ocorrência e avalie a gravidade do impacto.
O resultado é uma imagem mais clara de como diferentes processos operacionais impactam uns aos outros, o que se traduz em otimização agendamento de manutenção.
Agir com base em dados realistas de FMEA leva à redução do tempo de inatividade do equipamento, diminuída manutenção de avarias despesas e maior segurança dos membros da equipe.
Mas lançar um programa de FMEA não é para o departamento de manutenção executado casualmente. Para serem bem-sucedidas, as equipes de manutenção devem se comprometer a seguir as recomendações da força-tarefa.
Além disso, os gerentes de manutenção devem aplicar procedimentos operacionais padrão para avaliar o progresso do programa de forma consistente. A maneira mais fácil de organizar, analisar e agir com base nos dados do programa é usar um celular software computadorizado de gerenciamento de manutenção (CMMS) sistema.
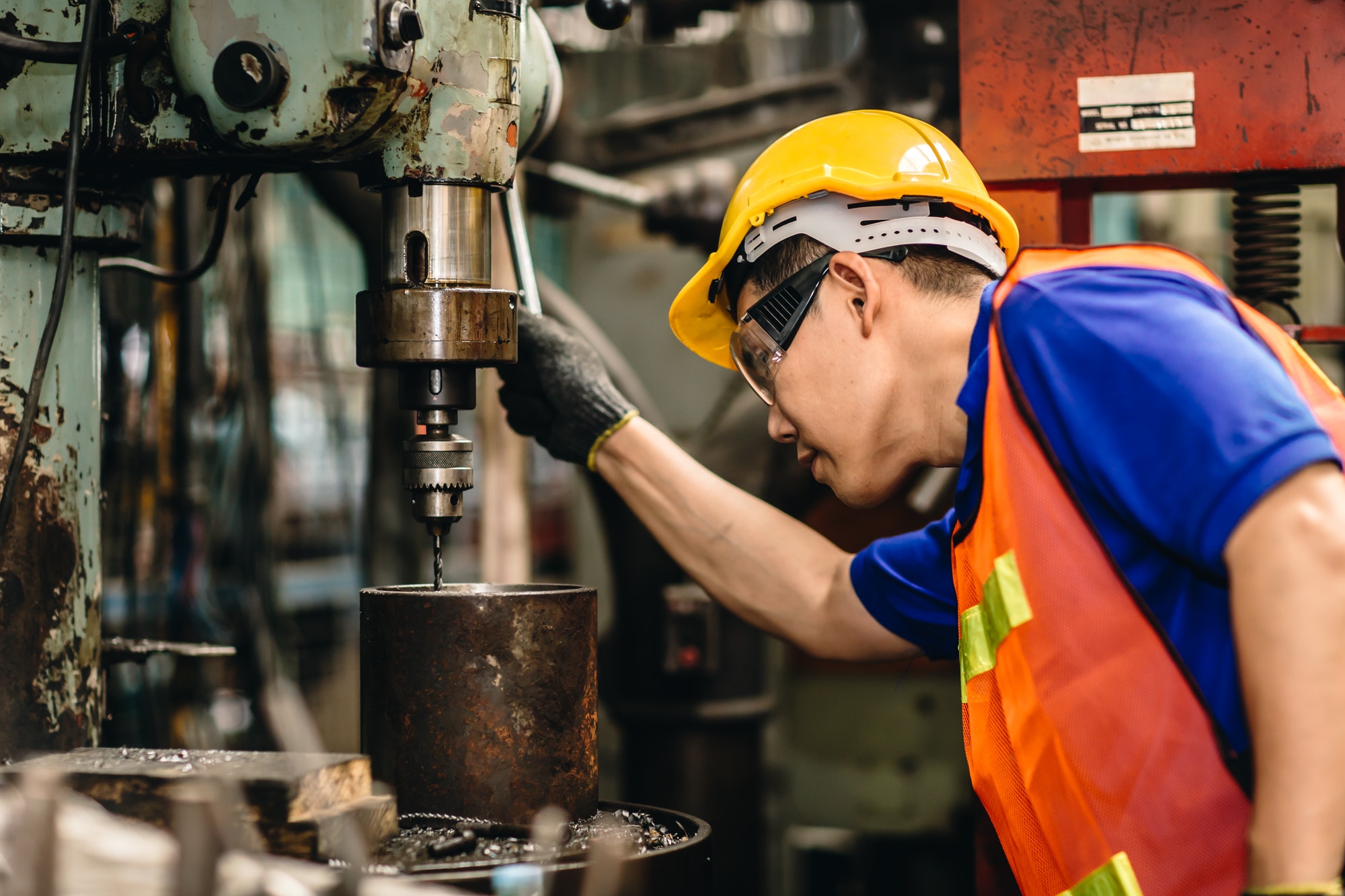
3 tipos de FMEA
Os líderes de negócios geralmente conduzem FMEAs ao projetar, redesenhar e reimplantar produtos e processos. Também é útil ao preparar planos de controle para processos operacionais. Embora o método analítico inclua vários subconjuntos, ele geralmente é dividido em três categorias:
1. Sistema FMEA
Sistema FMEA, também conhecido como f_unctional FMEA_, analisa os modos de falha do ponto de vista de um pássaro. Ele se concentra em sistemas e subsistemas inteiros relacionados à integração de sistemas, segurança no local de trabalho e qualquer outra coisa que possa afetar a produtividade geral.
O FMEA do sistema se concentra no fato de que falhas podem ocorrer entre vários ativos e processos. Em outras palavras, raramente uma falha do sistema é um evento isolado. Isso inclui modos de falha de ponto único que afetam vários pontos de contato e modos de falha complexos isolados em máquinas específicas. Os especialistas recomendam realizar o FMEA do sistema antes de decidir pelos projetos funcionais do sistema.
2. Projeto FMEA
Como o nome sugere, o foco principal do Projeto FMEA é o design de produtos e serviços. Os líderes organizacionais realizam o projeto FMEA para avaliar possíveis falhas, questões de segurança e requisitos regulatórios relacionados aos produtos finais.
O objetivo é garantir que os produtos da empresa sejam seguros, confiáveis e de alta qualidade para os clientes. Os líderes operacionais realizam o FMEA de projeto antes de novos produtos entrarem em produção e durante as reiterações do design do produto. O resultado de uma sessão bem-sucedida de FMEA de design são itens de ação que mitigarão o mau funcionamento do produto.
3. Processo FMEA
Processo FMEA concentra-se no processo usado para fabricar o produto em vez do próprio produto final. Os gerentes usam processo FMEA identificar problemas nos processos de produção envolvidos na colocação de um produto no mercado.
Por exemplo, um laptop inclui várias peças, cada uma delas resultante de processos de produção exclusivos. Supondo que a liderança identifique um problema com o processador do computador, ela terá que avaliar todos os procedimentos necessários para instalá-lo no computador.
O escopo do Process FMEA inclui operações de montagem, rotulagem de produtos, gerenciamento de peças e transporte de materiais. As organizações normalmente realizam esse tipo de FMEA durante a “fase de estudo de viabilidade” na pré-produção. O objetivo final é criar processos de produção robustos que suportem as especificações de projeto com o mínimo de tempo de inatividade e os retrabalhos necessários.
Vale ressaltar que alguns líderes operacionais segmentam o FMEA em categorias adicionais. Concept FMEA, Service FMEA, Hazard Analysis FMEA e Software FMEA são alguns dos termos que você pode ouvir ao discutir o tópico com outras pessoas. Independentemente do tipo de FMEA, o processo sempre contém facetas semelhantes.

Quatro elementos-chave do FMEA
O FMEA se baseia nos seguintes elementos para detalhar possíveis problemas operacionais:
- Modos de falha: Os modos de falha se referem às várias maneiras pelas quais um ativo, ou suas partes, podem parar de funcionar corretamente. Por exemplo, uma bomba centrífuga pode apresentar falha hidráulica, falha mecânica ou corrosão.
- Causas da falha: Esse componente da análise envolve um bom e antiquado brainstorming. Os líderes da força-tarefa devem executar avaliações de risco sistêmico de cada modo de falha em potencial com base em experiências anteriores. Surpreendentemente, as causas principais geralmente remontam a procedimentos comuns, departamentos irmãos, gargalos do sistema e formas de desperdício operacional.
- Análise do modo de falha: Depois que a liderança identificou as possíveis causas do fracasso, é hora de medir a frequência e a gravidade de suas ocorrências. Esse aspecto do FMEA envolve a classificação da gravidade estimada dos efeitos de cada falha (por exemplo, segurança dos funcionários, lucratividade do negócio, confiabilidade dos ativos), a probabilidade de sua ocorrência e sua probabilidade de detecção. A equipe então multiplica as três classificações para chegar a um Número de Prioridade de Risco (RPN) para informar a priorização de tarefas para manutenção e operações.
- Ação e revisão: Finalmente, a equipe desenvolve um plano de ação para executar as recomendações do FMEA. Novamente, o CMMS certo pode automatizar todo o processo, desde a atribuição de listas de verificação digitais até o gerenciamento de ativos e a análise de custo/tempo, depilando até 20 horas por semana em comparação com os processos analógicos de gerenciamento de dados.
Agora que você entende os conceitos básicos do FMEA, vamos nos aprofundar na essência do processo: o processo de análise do modo de falha, que inclui a classificação das pontuações de falha.
Entendendo as pontuações de falha do F
Uma análise do modo de falha do FMEA inclui os três atributos de pontuação a seguir:
- Severidade: As classificações de severidade revelam quais modos de falha devem ter prioridade. Ele considera quais fatores são essenciais para a empresa, seus clientes e o setor em geral. A liderança pode pesar os padrões de segurança, a continuidade dos negócios, os requisitos ambientais e os danos à reputação ao atribuir classificações de severidade. Uma classificação de baixa gravidade significa que um modo de falha tem impacto mínimo em uma empresa ou em seus clientes, enquanto uma classificação alta significa um efeito prejudicial mais severo.
- Detecção: A classificação de detecção determina a probabilidade de prevenção antes que uma possível falha ocorra. Em outras palavras, ele mede a probabilidade de os trabalhadores detectarem o problema antes que ele aconteça. As classificações de baixa detecção representam problemas facilmente detectáveis, enquanto as classificações de alta detecção representam problemas imprevisíveis.
- Ocorrência: Essa classificação mostra a probabilidade de um modo de falha ocorrer durante a vida útil de um ativo. Uma classificação de baixa ocorrência significa que é improvável que a falha aconteça, enquanto uma classificação de alta ocorrência implica que a falha do ativo é uma ocorrência mais provável.
Cada atributo recebe uma classificação por categoria, normalmente entre um e 10. Os modos de falha que provavelmente não ocorrerão recebem uma classificação de um. As três métricas são então multiplicadas para gerar um número de prioridade de risco (RPN) para cada modo de falha.
Exemplo de pontuação de falha
Por exemplo, se uma máquina de café expresso tiver uma classificação de gravidade de 10, uma classificação de detecção de dois e uma classificação de ocorrência de quatro, seu número de prioridade de risco seria 80. Lembre-se de que a meta de longo prazo é reduzir seus RPNs corrigindo proativamente os catalisadores de risco.
Em alguns casos, não é possível reduzir as classificações de severidade dos ativos. Por esse motivo, é melhor se concentrar em reduzir o que você pode controlar: as classificações de ocorrência e detecção. Isso significa que você minimizará as chances de um problema ocorrer e, ao mesmo tempo, aprimorará sua capacidade de detectar falhas antes que elas aconteçam.
Em última análise, quanto maior a classificação de gravidade, maior será o impacto da falha na produtividade dos negócios, na satisfação do cliente e nos resultados financeiros.
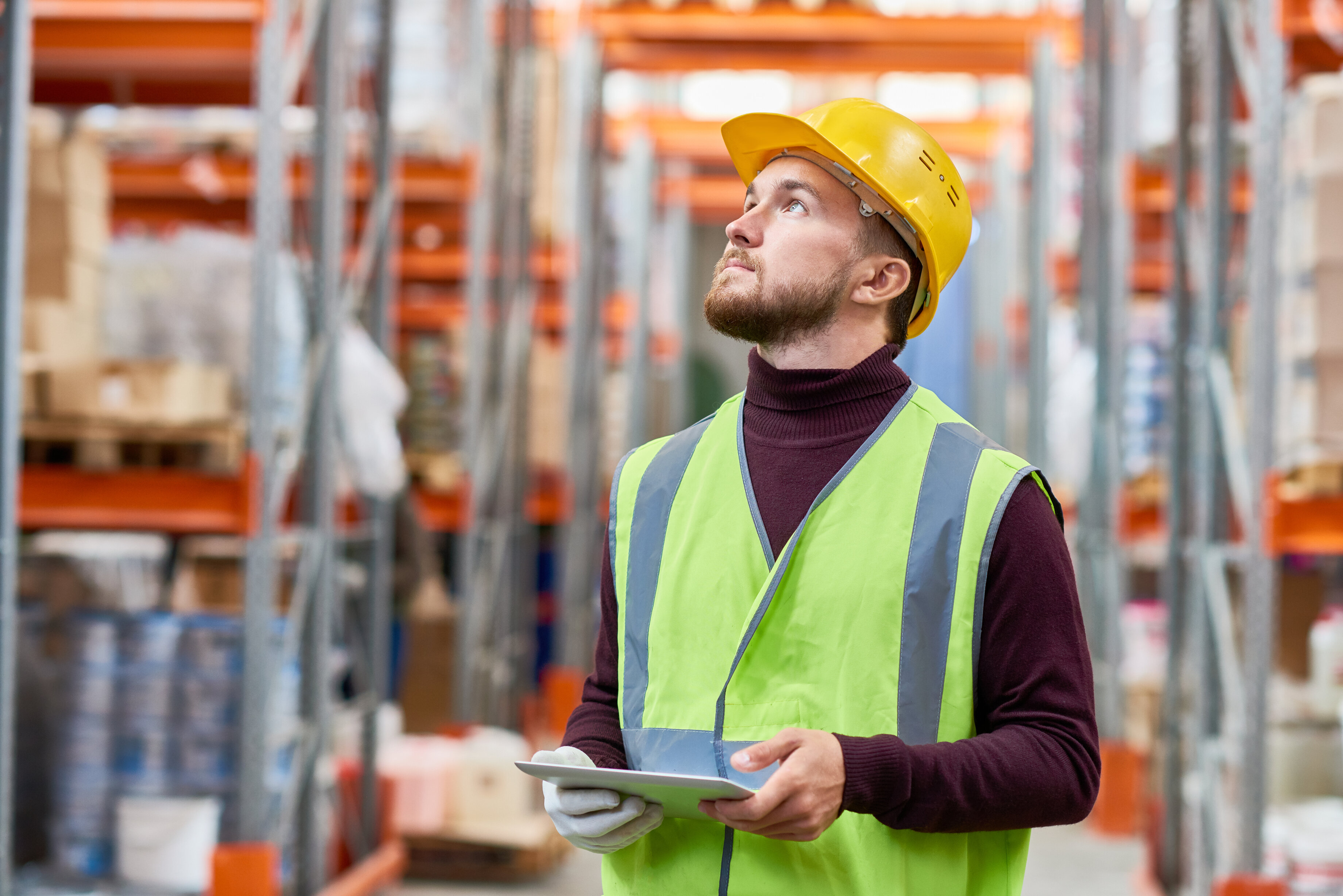
Como conduzir uma análise dos efeitos do modo de falha
O melhor momento para executar um FMEA inicial é durante a fase de desenvolvimento de produtos da sua organização. Isso permite bastante tempo para implementar modificações para agilizar o design do produto e processos de fabricação. Obviamente, você pode executar o FMEA sempre que quiser melhorar o controle de qualidade, aumentar a lucratividade ou aumentar a eficiência.
Antes de começarmos, vale a pena mencionar que uma análise mais abrangente de como conduzir um FMEA pode ser encontrada em J1739_202101: Análise de efeitos e modos de falha potenciais (FMEA), incluindo FMEA de projeto, FMEA-MSR suplementar e FMEA de processo.
Continue lendo para obter uma visão geral para começar:
Etapa 1: Monte sua equipe de FMEA
Apesar da palavra “eu” no FMEA, a análise deve incluir muitos membros-chave da equipe para ter sucesso.
Com isso em mente, monte uma força-tarefa para liderar a iniciativa. Na maioria dos casos, um engenheiro de produção ou gerente de manutenção liderará a equipe. Outras funções potencialmente relevantes incluem engenheiros de processo, designers de processos, fornecedores, profissionais de marketing e até mesmo clientes.
Etapa 2: reunir seus dados
Depois de montar sua equipe, reúna as seguintes informações:
- Diagramas de limite
- Diagramas de parâmetros
- Manutenção de ativos
- Diagramas de fluxo de trabalho
- Matriz de características
Em seguida, determine qual tipo de FMEA você conduzirá.
Etapa 3: especifique seu escopo
Identifique os sistemas, subsistemas, montagens e relacionamentos de peças que sua equipe avaliará no FMEA. Além disso, configure procedimentos operacionais padrão para conduzir, executar e acompanhar seus esforços.
Você pode usar um fluxograma para visualizar os detalhes com mais clareza. É fundamental garantir que todos os membros da equipe estejam na mesma página antes do início do projeto.
Etapa 4: Identificar possíveis modos de falha
Neste ponto, você está pronto para considerar as várias maneiras pelas quais seus ativos podem falhar. Use o histórico de manutenção, o conhecimento dos funcionários da linha de frente, as diretrizes do fabricante e outros recursos úteis para debater possíveis resultados.
Seu objetivo é gerar uma lista exaustiva do que pode dar errado. É essencial enfatizar que modos de falha específicos podem desencadear outras falhas em sistemas ou subsistemas. Por esse motivo, sempre considere o contexto geral ao identificar possíveis problemas. Além dos modos de falha que resultam na quebra completa dos ativos, considere aqueles que podem resultar em:
- Funções ou resultados não intencionais de um ativo.
- Desempenho abaixo do padrão.
- Funcionalidade reduzida.
Isole cada ativo e seus componentes para identificar todos os possíveis modos de falha, incluindo os ocultos. Os modos de falha padrão do equipamento incluem rachaduras, deformação do produto, fadiga de torque e curtos-circuitos elétricos.
Etapa 5: Determinar classificações de severidade
Conforme mencionado anteriormente, as classificações de severidade medem o efeito geral dos modos de falha. Os gerentes de manutenção geralmente usam uma escala de um a 10 para classificar o impacto de baixo para alto.
Geralmente, os modos de falha que afetam a segurança ou os resultados financeiros da empresa recebem classificações de severidade mais altas. Os modos de falha com classificações de severidade altas devem sempre ter prioridade. Por exemplo, um fabricante de automóveis pode atribuir a um problema de instalação de airbag uma classificação de alta severidade devido ao seu impacto prejudicial na segurança e nos atrasos na produção.
Etapa 6: Determinar classificações de ocorrências
A classificação de ocorrências mede a frequência na qual é provável que os modos de falha ocorram. Também é medido em uma escala de um a 10.
Ao determinar a classificação da ocorrência, é essencial considerar todas as causas potenciais do modo de falha e o controle de prevenção existente para evitar que isso aconteça.
Usando o exemplo mencionado na etapa anterior, por que o fabricante do carro receberia airbags com defeito ou entregas atrasadas? Pode ser uma confusão do fornecedor, discrepâncias no pedido ou uma falha na comunicação. Há algum controle para garantir que isso não aconteça? Se sim, a instalação incorreta do airbag receberá uma classificação de ocorrência baixa ou moderada.
Etapa 7: Determinar as classificações de detecção
Nesse estágio, determine a classificação de detecção para os modos de falha identificados. Isso significa estabelecer como será fácil identificar a falha antes que ela ocorra. As altas classificações de detecção significam que é quase impossível identificar e resolver problemas antes que as falhas ocorram.
Etapa 8: Calcular o RPN e priorizar ações
Agora, calcule o Número de Prioridade de Risco (RPN) para cada modo de falha multiplicando as três classificações: detecção, ocorrência e gravidade. Isso permitirá que você priorize iniciativas de design, melhoria de processos e manutenção. Veja a fórmula do RPN:
Número de prioridade de risco (RPN) = severidade * ocorrência * detecção
Lembre-se de que diferentes setores e organizações têm diferentes definições de “crítico”. Portanto, cabe à sua equipe determinar o que considerar como RPN para modos de falha crítica que devem ter prioridade.
No entanto, você deve avaliar RPNs não críticos para determinar sua relação com outros sistemas e se existe a possibilidade de provocar falhas nesses sistemas. Esses modos de falha também devem ter prioridade.
Etapa 9: Desenvolver um programa de manutenção preventiva
Esse é o estágio em que você se concentra no objetivo principal do seu programa de FMEA: mitigar os riscos identificados por meio de ações baseadas em dados. Desenvolva um manutenção proativa programa para ajudar a minimizar o risco de falha de ativos. A prioridade sempre deve ser dada aos modos de falha com altos RPNs.
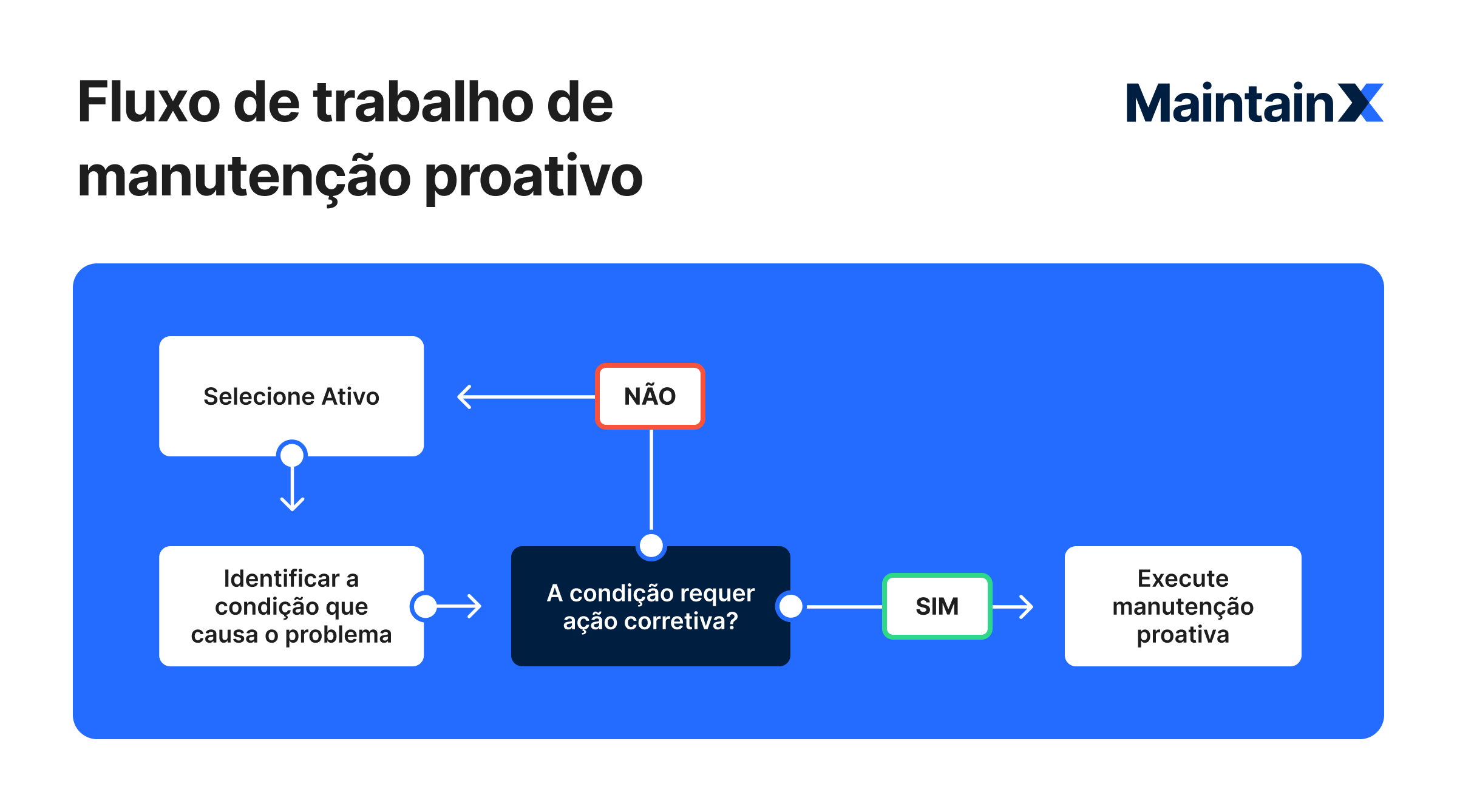
Como é impossível lidar com todos os modos de falha em potencial de uma só vez, concentre sua energia nos que mais afetam a produtividade, segurança, e satisfação do cliente.
Colete dados de manutenção e analise seus esforços para determinar o curso de ação mais adequado para cada modo de falha. Você também pode fazer alterações nas funções ou considerar melhorias no processo e no design.
Além disso, priorize os ativos com classificações de severidade altas, independentemente de seu RPN ser baixo. Por quê? Porque uma classificação de severidade alta significa que a falha afetará significativamente a produtividade dos negócios, a satisfação do cliente e a segurança.
Etapa 10: Recalcular seus RPNs
Por fim, recalcule periodicamente seus RPNs para ver se as ações que você implementou estão gerando resultados. Sua força-tarefa deve reclassificar cada valor (gravidade, ocorrência e detecção) para calcular uma nova RPN para cada modo de falha e, em seguida, compará-la com a RPN antiga.
O objetivo é desenvolver e implementar continuamente novas estratégias que reduzam os RPNs a ponto de não precisarem mais de intervenções. Por esse motivo, o FMEA é um processo contínuo, não um evento único.
Exemplo de processo FMEA
Aqui está um exemplo rápido de um processo de FMEA conduzido para a instalação de um airbag de veículo:
Função: Instalação de airbag
Modo de falha: Airbag instalado incorreto
Efeitos de falha: Avaria na implantação, resultando em ferimentos físicos ao motorista
Classificação de severidade: 10
Causas da falha: Erro humano
Classificação de ocorrências: 4
Controles de prevenção: Inspecione manualmente os airbags após o fornecedor entregá-los
Controles de detecção: Use sensores para testar a funcionalidade do airbag após a instalação
Classificação de detecção: 6
RPN: 240
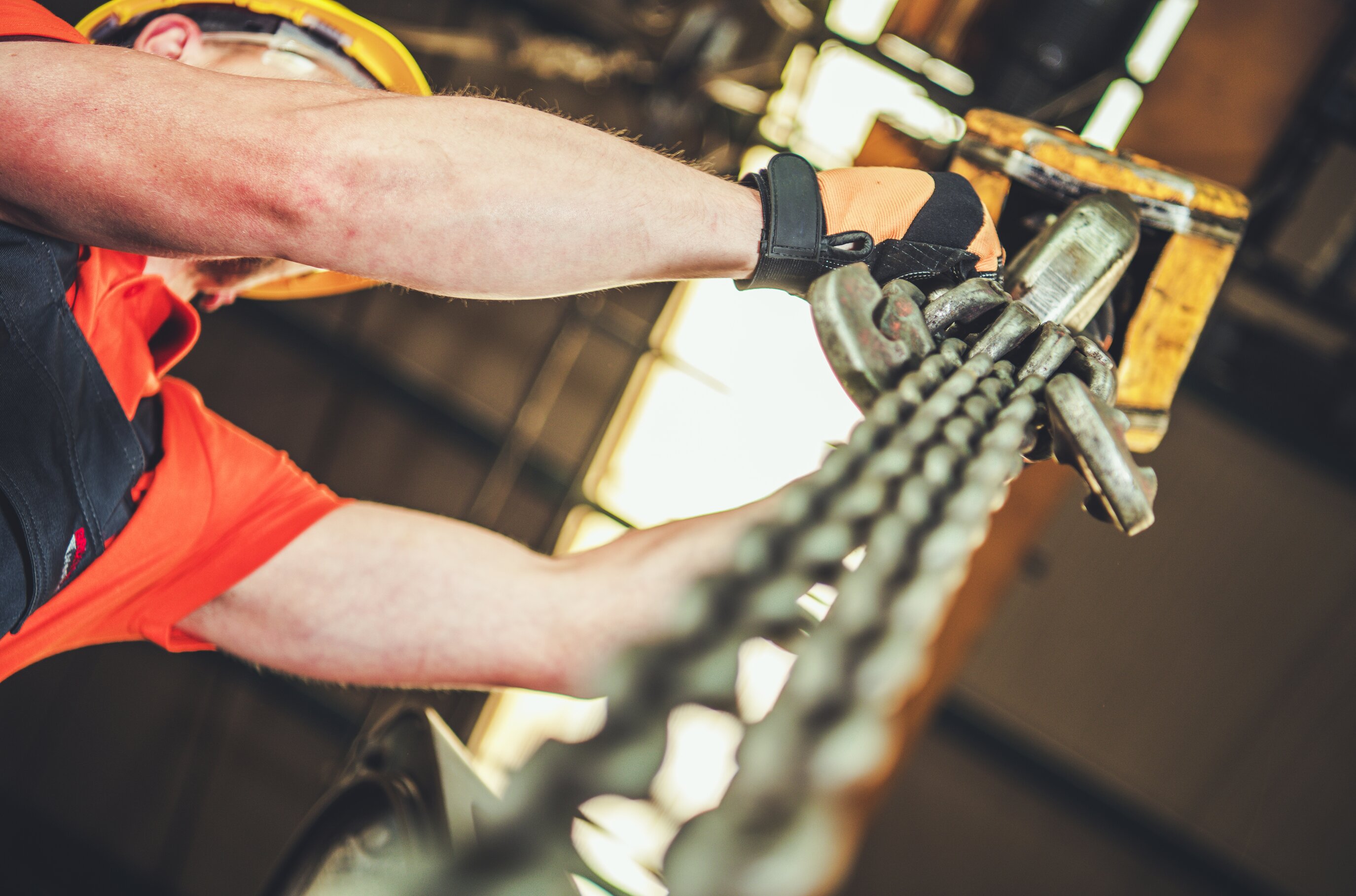
Obstáculos comuns com o FMEA
O FMEA é uma ferramenta poderosa para melhorar a confiabilidade do processo e do produto. Quando conduzido com precisão, está comprovado que ajuda os líderes organizacionais a mitigar riscos, minimizar os cronogramas de desenvolvimento de produtos e proteger o controle de qualidade.
Mas nem todo mundo que realiza um processo de FMEA alcança os resultados esperados. Algumas organizações enfrentam os seguintes obstáculos comuns:
- Comunicação deficiente: Muitas empresas abordam o FMEA como um item de conformidade que precisa ser riscado da lista de verificação. Deixar de ver o FMEA como uma ferramenta para melhorar a qualidade e a confiabilidade leva a um processo indiferente, sem nenhum sucesso real.
- Equipe ineficaz: Montar uma equipe de FMEA sem a representação de partes do ciclo de vida do produto ou do processo provavelmente será ineficaz. A equipe não terá conhecimento suficiente de todo o ciclo de vida do produto ou do processo. O FMEA é um processo contínuo que abrange todo o ciclo de vida do produto. Isso significa que você precisa resolver todos os problemas, desde o estágio inicial do projeto até o desenvolvimento, a fabricação e a implantação, para que o processo seja um sucesso.
- Documentos desorganizados: Algumas equipes, com pressa em concluir o processo, compilam informações e documentos aleatoriamente de forma desorganizada. Infelizmente, eles se tornam vítimas das falhas de seus próprios sistemas ao tentar revisar o progresso. Frustração, sobrecarga e confusão os impedem de recalcular o RPNS e direcionar seus esforços conforme necessário.
- Confiança excessiva na RPN: Por fim, equipes que se concentram exclusivamente em RPNs tiram conclusões imprecisas sobre os modos de falha. É melhor usar o RPN como referência geral e, ao mesmo tempo, considerar o impacto das pontuações individuais.

Simplifique o FMEA com o MaintainX
Como mostramos, o FMEA é uma ferramenta valiosa para empresas que desejam aumentar a confiabilidade dos ativos, priorizar iniciativas de O&M e otimizar o design de produtos. A chave para o sucesso?
Implemente as recomendações resultantes de sua força-tarefa e siga um processo periódico de revisão de dados! O progresso não acontecerá da noite para o dia, então faça planos para revisitar os RPNs e os esforços da equipe.
O MaintainX permite que as equipes de manufatura compartilhem pontos de dados cruciais, aprimorem a comunicação da equipe e obtenham insights de relatórios avançados fáceis de usar. Nosso software de ordem de serviço recebe consistentemente notas altas em usabilidade, abrangência e valor em sites de avaliação de terceiros.
Mas não acredite na palavra de ninguém — experimente você mesmo o MaintainX.
Perguntas frequentes
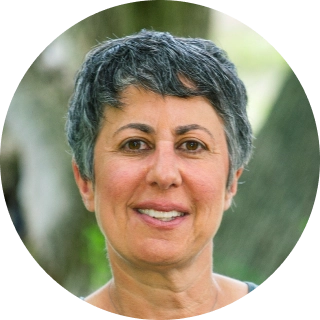
Caroline Eisner é escritora e editora com experiência nos setores de fins lucrativos e sem fins lucrativos, governo, educação e organizações financeiras. Ela ocupou posições de liderança em instituições de ensino fundamental e médio e liderou projetos digitais de grande escala, sites interativos e uma consultoria de redação comercial.