As a manufacturing professional, you know that production equipment is the backbone of your business. If your equipment fails, production grinds to a halt, orders get delayed, and you lose revenue. That's why effective asset management is critical for your manufacturing success. It helps ensure equipment reliability, optimize performance, and extend useful life while controlling costs.
The average manufacturing facility loses around $25,000 for every hour of unplanned downtime. For larger organizations, this figure can exceed $500,000. In automotive manufacturing, for example, you’re looking at costs up to $2.3 million per hour.
Effective asset management provides a structured approach to handle these challenges. By properly managing your machines, tools, and other physical assets, you can reduce unplanned stoppages and optimize production schedules. Doing this also extends the useful life of your equipment, delaying expensive replacements and ensuring better return on capital investments.
Key Takeaways
- Effective asset management reduces unplanned downtime, which costs manufacturing facilities an average of $25,000 per hour and up to $2.3 million per hour in automotive manufacturing.
- A comprehensive asset management strategy includes five key components: inventory management, preventive maintenance, condition monitoring, lifecycle management, and documentation/reporting.
- When you shift from reactive to preventive maintenance, you can reduce overall downtime by up to 32% on average.
- Modern CMMS and EAM software systems centralize your asset data, automate maintenance workflows, and provide analytics that transform maintenance from a cost center into a strategic function.
What is asset management in manufacturing?
Asset management in the manufacturing industry refers to the process of maximizing your asset’s value and performance in the most cost-effective way. Here, "assets" include all physical equipment and infrastructure vital to your production, such as machines, production lines, tools, vehicles, and facilities. The goal is to ensure these assets are available, reliable, safe, and efficiently used from acquisition to disposal.
What does asset management involve? Key activities and best practices include:
- Tracking asset information and performance data
- Scheduling routine maintenance
- Predicting potential failures
- Making data-driven decisions that minimize downtime and extend equipment life
For example, a food processing plant might use sensors on its conveyors and motors. The sensors send real-time data on vibration and heat. When your asset management system flags a motor showing abnormal vibration trends indicating wear, your maintenance team schedules bearing replacement during a planned downtime window. This prevents a sudden failure that would halt production. This scenario demonstrates asset management in action: Your team tracks the asset's condition, makes a preventative fix, avoids downtime, and documents the intervention for future reference.
Asset management in manufacturing gives you a holistic approach to controlling and optimizing assets. It blends maintenance management, operations, and strategic planning. When you excel in asset management, you enjoy higher reliability, lower operational costs, and better agility when responding to market demands.
Why asset management is critical in manufacturing
Given the high stakes of equipment performance, asset management is critical for several reasons:
- Minimizing unplanned downtime: Downtime is extremely expensive and disruptive in your operation. The 2024 State of Industrial Maintenance report identifies aging equipment (29%) as the leading cause of unplanned downtime, followed by equipment failure (22%). By investing in regular maintenance, upgrades, and condition monitoring, you can catch problems before they escalate.
- Improved operational efficiency: Well-maintained assets operate more efficiently, consuming less energy and fewer resources. When machines are running optimally, they process materials faster, generate less waste, and require fewer operator interventions, contributing directly to your bottom-line results.
- Cost control and ROI: Asset management helps you control both maintenance expenses and capital expenditures by using data to optimize maintenance schedules and extend the useful life of your equipment.
- Regulatory compliance and safety: In industrial environments, equipment upkeep is closely tied to safety and compliance. Effective asset management ensures that safety-critical equipment is regularly inspected and maintained, reducing the risk of catastrophic failures.
- Optimized asset utilization and lifecycle management: Your company invests heavily in equipment, so it's important to use those assets wisely. Asset management is critical for optimizing asset usage over its entire lifecycle. Industries that implement asset performance management have seen asset utilization improvements on the order of 20% and significant extension of asset life in many cases.
To address these needs, companies increasingly rely on computerized maintenance management systems (CMMS) and enterprise asset management (EAM) software. These digital solutions centralize your asset information, automate maintenance schedules, track performance metrics, and provide actionable insights.
A robust CMMS can serve as the backbone of effective asset management by streamlining workflows, capturing historical data, and empowering your team to use proactive rather than reactive maintenance approaches.
Key components of asset management in manufacturing
Asset management in manufacturing encompasses several key components or pillars. Each plays a role in creating a comprehensive strategy to track, care for, and optimize your assets.
1. Asset inventory management
The foundation of asset management is knowing what assets you have. Asset inventory management is the process of identifying, cataloging, and tracking all physical assets in your organization. This includes maintaining a centralized registry or database of equipment—capturing details like asset name, ID/tag, location, manufacturer, purchase date, specifications, and maintenance history.
A robust asset inventory ensures nothing falls through the cracks. For example, every forklift, CNC machine, compressor, or conveyor in your facility should be logged so you can properly maintain it. Your CMMS/Enterprise Asset Management software can manage this inventory.
Asset inventory management supports planning and risk management. If you don't know an asset exists, you can't maintain it, which could lead to an unexpected failure. Conversely, knowing your asset base helps in spare parts management and financial planning.
2. Preventive maintenance
Regular preventive maintenance (PM) is a cornerstone of your asset management, preventing failures before they happen with planned activities. This can include routine inspections, lubrication, adjustments, parts replacements, and cleaning—all done on a scheduled basis rather than waiting for something to break.
The key is planning. In preventive maintenance, you generate work orders in advance and ideally complete them when the machine is not in active production (like during off-shifts or planned downtime). A well-executed PM program significantly reduces unplanned breakdowns. When you shift from reactive to preventive maintenance, you can cut overall downtime by a large margin—even a partial preventive maintenance strategy can yield a reduction in downtime over reactive maintenance on average.
3. Condition monitoring and predictive maintenance
Condition monitoring is how you continuously track your assets’ status through sensors, inspections, and data analysis to detect early signs of problems. Rather than servicing equipment strictly on a calendar basis, condition monitoring feeds into predictive maintenance (PdM)—maintenance that you perform based on the actual condition or performance indicators of equipment.
According to McKinsey, 84% of companies are now at least piloting predictive maintenance on critical assets, showing industry-wide recognition of its value.
Examples of condition monitoring include vibration analysis on rotating equipment, thermal imaging on electrical panels, oil analysis, and simple sensor readings like temperature, pressure, or power draw that can indicate if a machine is straining. When your system notices an anomaly, it can trigger an alert or work order. Your maintenance team then schedules repairs in time to fix that specific issue.
4. Asset lifecycle management
Asset lifecycle management gives you strategic oversight of equipment from purchase to retirement. This approach extends beyond routine maintenance to encompass the entire equipment journey—acquisition, operation, maintenance, upgrade, and eventual replacement.
Effective lifecycle management begins with informed procurement decisions that consider not just purchase price but long-term value. Throughout an asset's life, your CMMS software tracks performance data, maintenance history, and operational costs, enabling you to make data-driven decisions about when to repair, upgrade, or replace equipment. Financial tools like lifecycle cost (LCC) analysis and total cost of ownership (TCO) calculations help quantify these decisions.
By taking this comprehensive view, you avoid costly surprises and optimize capital investments. Your assets remain productive longer, reaching or exceeding their intended lifespan without performance degradation. Companies skilled in lifecycle management consistently demonstrate lower total costs. They time upgrades and replacements strategically.
5. Documentation and reporting
The final component is documentation and reporting, which involves keeping detailed records of asset information, maintenance activities, performance metrics, and compliance data and then analyzing and reporting on this information to drive decisions.
Accurate documentation provides you with traceability and accountability. It also allows your team to calculate key metrics like mean time between failures (MTBF), mean time to repair (MTTR), uptime percentage, maintenance cost per unit produced, etc. Many organizations struggle with this—only 55% of companies have formal systems to capture and share maintenance knowledge.
From a compliance standpoint, documentation is non-negotiable. If an accident or audit occurs, you must produce maintenance records to demonstrate you were performing due diligence.
Reporting takes your raw data and turns it into actionable information for decision-makers. Regular reports might include things like monthly downtime by asset, top 10 causes of downtime, maintenance backlog, PM compliance rate, and cost reports. These reports help you prioritize where to focus improvement efforts.
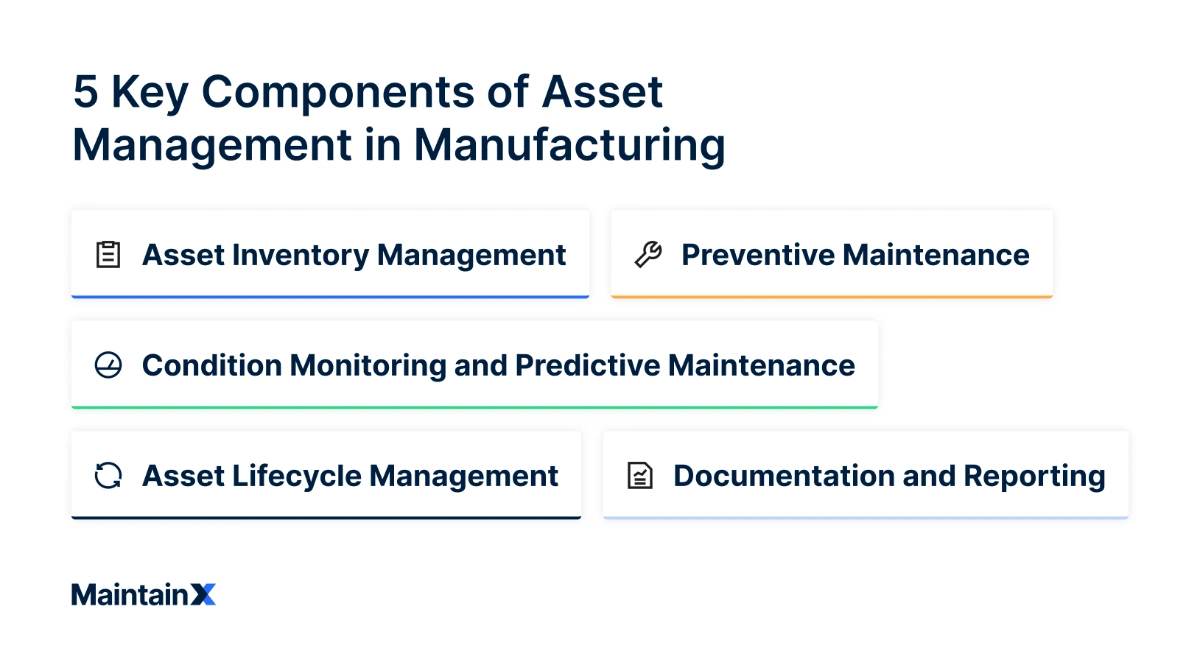
Unlock the full potential of your manufacturing assets
Asset management isn’t just about maintaining equipment—it's about strategically optimizing your manufacturing operations to maximize uptime, quality, and profitability. By implementing the key components above, your team can transform maintenance from a reactive cost center into a strategic function that drives continuous improvement and gives you a competitive advantage.
As we outlined in the examples above, enterprise asset management software plays a crucial role in this transformation. Modern CMMS/EAM platforms centralize your asset data, automate work order generation, streamline maintenance scheduling, and provide powerful analytics capabilities.
These systems make it easier to track maintenance history, monitor equipment performance, manage inventory, and make data-driven decisions. With mobile access, your technicians can document issues, access repair manuals, and update work orders in real time from the shop floor, significantly improving efficiency and accuracy.
Your journey toward optimization doesn't require an immediate overhaul of your entire operation. Begin by assessing your current asset management practices and identifying specific opportunities for improvement. A measured, step-by-step approach often yields the most sustainable results.
Remember that even small initiatives can deliver significant benefits. Starting with basics like establishing a proper asset inventory in your CMMS, implementing fundamental preventive maintenance schedules, or training your staff on new processes can create momentum for your asset management program. As these initial efforts start to show value, you can gradually expand to more advanced practices like condition monitoring and predictive maintenance.
FAQs on Manufacturing Asset Management
En la industria manufacturera, un activo es cualquier elemento físico que proporciona valor a su organización. Esto incluye la maquinaria de producción, las herramientas, los vehículos, las instalaciones, la infraestructura e incluso los sistemas digitales que respaldan las operaciones. Los activos son recursos de su propiedad o bajo su control que permiten los procesos de fabricación.
Los tres tipos principales de activos en la industria manufacturera son:
1) Activos fijos (equipos, edificios, terrenos),
2) Activos móviles (vehículos, herramientas portátiles, maquinaria móvil) y
3) Activos de inventario (materias primas, trabajos en curso, productos terminados).
Cada uno requiere diferentes enfoques de administración para maximizar su valor.
MAM significa gestión de activos de fabricación, que se refiere al proceso estratégico de seguimiento, mantenimiento y optimización de todos los activos físicos utilizados en sus operaciones de fabricación. Se centra en maximizar el valor de los equipos a lo largo de su ciclo de vida y, al mismo tiempo, minimizar los costos y los riesgos.
Las 5 P de la gestión de activos son:
- Personas: Contar con personal capacitado que comprenda cómo mantener y operar los activos de manera efectiva
- Procesos: Establecer procedimientos estandarizados para las actividades de mantenimiento y la toma de decisiones
- Productos: Seleccionar las herramientas, las tecnologías y los sistemas adecuados para respaldar la gestión de activos
- Rendimiento: Medir y supervisar las métricas clave para garantizar que los activos generen los resultados esperados
- Planificación: Adoptar un enfoque proactivo para la gestión del ciclo de vida de los activos y la programación del mantenimiento
See MaintainX in action