Infrastructure assets - from roads and bridges to power grids and manufacturing equipment- form the backbone of modern society. If not properly managed, the consequences of infrastructure failures can be costly and severe, ranging from service disruptions to catastrophic breakdowns.
Many of these systems are also aging. For instance, the average age of fixed assets in operation is around 24 years - the highest since 1947. This combination of aging equipment and high stakes makes infrastructure asset management (IAM) more important than ever. Adopting a strategic approach to IAM helps organizations extend asset lifespans, reduce lifecycle costs, improve service delivery, and prevent failures before they happen.
Key takeaways
- Strategic asset prioritization helps organizations focus limited resources on the infrastructure that matters most and boost reliability without overspending.
- Technology-enabled infrastructure can extend asset lifespans and defer capital expenditures, providing significant ROI through fewer emergency repairs and improved utilization.
- Measuring success with clear KPIs like asset availability, MTBF, and maintenance costs is key to tracking progress and continuously improving your asset management strategy.
- Implementing a CMMS centralizes asset data and enables data-driven decisions that can reduce unplanned downtime by up to 32% through preventive maintenance programs.
What is infrastructure asset management?
Infrastructure asset management is about making smart, long-term decisions to keep critical assets like roads, pipelines, and facilities working reliably and efficiently over time. The goal is to ensure that all infrastructure projects deliver their intended service efficiently and reliably at the lowest lifecycle cost while managing risk and meeting required standards.
IAM applies to a broad range of assets and sectors. Public infrastructure, like wastewater treatment plants, roads, bridges, utility grids, and railways, are all classic examples from local and central governments. But IAM principles also apply to private sector assets, such as manufacturing equipment, facility systems (HVAC, power supply), and transportation fleets.
A successful IAM program typically includes:
- Asset inventory & condition assessment: Documenting assets, their location, age, and current condition
- Defined levels of service (LOS): Setting performance targets for assets (e.g., reliability, capacity, response times) that align with business or community needs set by local governments.
- Lifecycle costing & budgeting: Forecasting all costs over an asset’s life (maintenance, operations, renewal) and planning budgets accordingly
- Risk management: Identifying critical assets and failure risks, then prioritizing actions to reduce those risks
- Long-term capital planning: Developing long-term strategies and securing sustainable funding to renew or replace assets at the right time
A strategic, system-wide approach to IAM helps teams make smarter decisions across the asset lifecycle that balance performance, cost, and risk. Ultimately, it’s about keeping assets reliable and service-ready, whether that means delivering clean water, minimizing plant downtime, or maintaining safety in critical infrastructure.
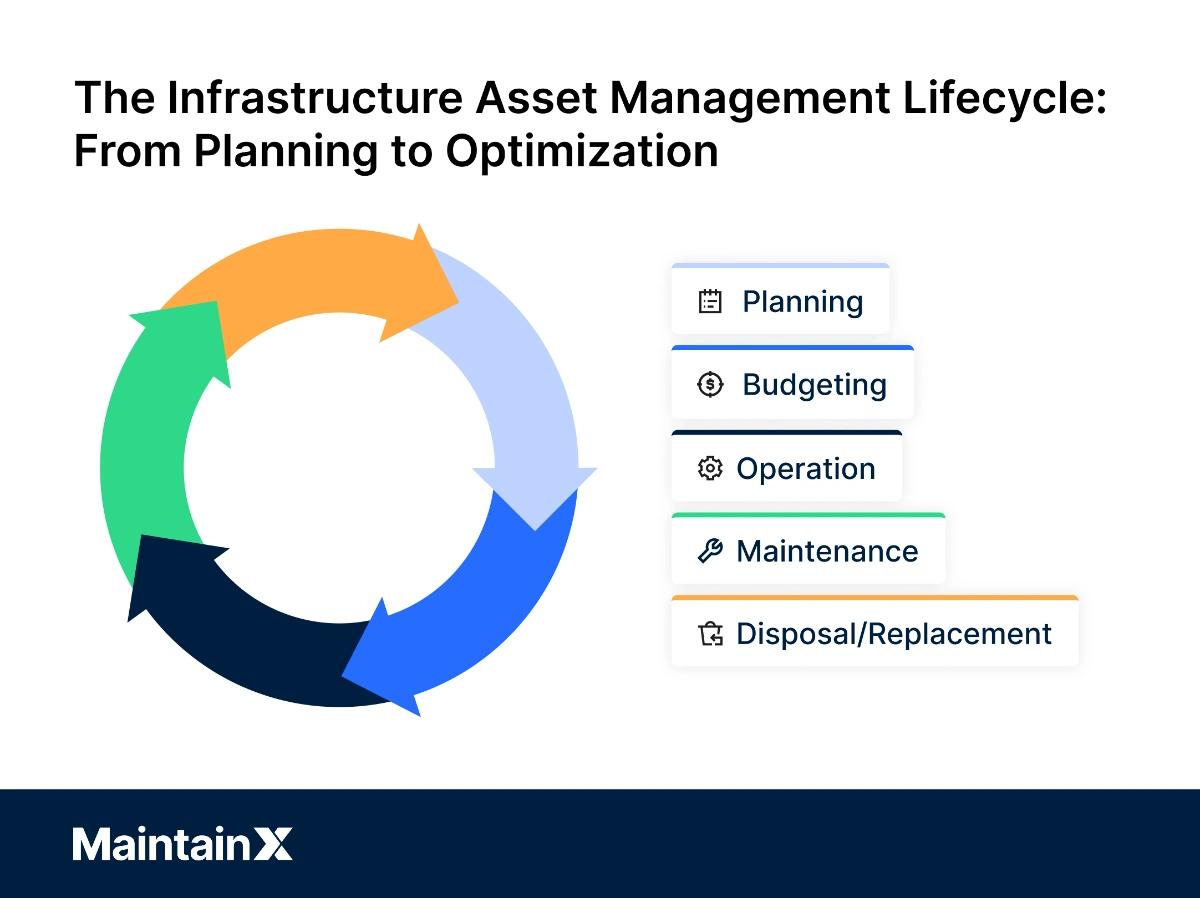
Challenges in optimizing infrastructure asset management
Implementing effective IAM is not without its challenges. Infrastructure and maintenance managers often face a combination of technical, organizational, and financial hurdles. Key challenges include:
- Aging infrastructure: Much of today’s infrastructure is decades old and operating beyond its intended lifespan. Aging roads, pipelines, and machines require increasing maintenance just to stay running, stressing maintenance teams and budgets. In the MaintainX 2024 State of Industrial Maintenance Report, “29% of respondents anticipate aging equipment to be the leading cause of unplanned downtime.”
- Budget constraints: Maintenance and infrastructure departments often operate under tight budgets. There is constant pressure to do more with less, and maintenance is sometimes deferred to save money in the short term. However, delaying necessary upkeep usually leads to higher costs later. Optimizing IAM requires convincing stakeholders that significant investments now will yield savings and avoid costly emergency fixes.
- Data overload: Modern assets and sensors generate enormous amounts of data, but organizations struggle to harness it. Maintenance teams can be overwhelmed by data on asset performance, inspections, and repairs coming from different sources. Without a way to aggregate and analyze this information, the value of data-driven decision-making is lost.
- Regulatory compliance: Infrastructure-intensive industries face strict regulations on safety, environmental protection, and reliability. Ensuring compliance adds another layer of complexity. Maintenance activities must adhere to legal and technical standards (for example, OSHA safety regulations or environmental rules on emissions and waste). Failure to comply can result in serious penalties and legal liabilities.
- Data silos: It’s common to find maintenance and asset information spread across disparate infrastructure systems or even on paper. Such disconnected systems lead to information silos, duplicate data entry, and lack of real-time visibility. When work orders, inventory, and asset histories reside in separate silos, it’s difficult to coordinate asset management activities efficiently.
These challenges highlight the need for a strategic, optimized approach to asset management that can handle aging infrastructure, tight budgets, and growing performance demands.
Key strategies for optimizing infrastructure asset management
To overcome these challenges and get the full value from IAM, organizations need a clear, multi-faceted strategy. The following approaches are essential to improving your overall infrastructure asset management.
Implement a data-driven approach
Basing your decisions on data, rather than reactive habits or guesswork, is the first step toward more effective asset management. By collecting the right information and turning it into insights, you can make sure every move you make supports reliability, reduces risk, and uses resources where they matter most.
For instance, instead of scheduling maintenance at fixed intervals or reacting to breakdowns, teams can use performance trends and failure history to target the assets that actually need attention. This might mean increasing maintenance on equipment showing early signs of decline, or safely extending intervals for assets that are performing well. It also helps prioritize spending, focusing limited budgets on the highest-risk areas.
Modern enterprise asset management (EAM) software or a computerized maintenance management system (CMMS) platform like MaintainX is crucial here, as they centralize data from different sources.
Adopt preventive and predictive maintenance
Preventive maintenance (PM) and predictive maintenance (PdM) are two essential tools you can use to improve asset performance and avoid unplanned downtime.
- Preventive maintenance means performing regular, scheduled servicing on assets (such as inspections, lubrication, and part replacements) based on time or usage thresholds.
- Predictive maintenance takes all of this a step further by using sensor data and condition monitoring to service equipment only when needed i.e., when indicators show an impending problem but before a failure occurs.
Moving away from a reactive “run-to-failure” approach and toward preventive and predictive strategies yields enormous benefits. Our research confirms that a proactive maintenance approach is far more cost-effective than reacting to breakdowns. Even a partially preventive maintenance program reduces unplanned downtime by 32%.
If you want to implement these strategies, here are some basic steps to follow:
- Start by scheduling routine maintenance at the right intervals, using manufacturer guidance or historical performance data.
- Use condition monitoring tools to collect and analyze data on your assets. Consider trying IoT sensors, vibration analysis, thermal imaging, or oil analysis on high-priority equipment.
- Track performance trends so you can optimize your maintenance intervals and ensure that work is done just in time to prevent failure, not after it happens.
By implementing preventive and predictive maintenance strategies, teams can maximize uptime, reduce unexpected failures, and extend the life of their equipment. These approaches also support a safer work environment. While they may require upfront planning and investment, the long-term payoff will be fewer breakdowns and lower maintenance costs overall.
Prioritize critical assets
Not all assets are equally important to your operations or service delivery, and not all pose the same risk if they fail. Prioritizing critical assets means focusing your management efforts and resources on the assets that matter most.
By understanding which assets are highly critical, maintenance teams can give them more attention and resources, for example, more frequent inspections, higher priority on the maintenance schedule, and faster responses to any issues. Less critical assets (e.g., non-essential equipment or those with easy workarounds) can be maintained at a less aggressive interval without major risk. This risk-based prioritization ensures limited resources are used where they add the most value.
To get started, create a list of all your assets and assign each one a criticality rating - high, medium, or low based on how much impact a failure would have. If you're unsure, use your CMMS or EAM system to look at maintenance history and downtime trends. Once you've identified your most critical assets, review their maintenance plans to make sure they’re getting the right level of attention. It’s also a good idea to stock spare parts for key equipment and ensure your team is trained to handle them.
This kind of strategic prioritization will make sure your most important assets always get the attention they need to keep operations running smoothly.
Support and streamline IAM with technology
Data silos and manual processes make it hard to manage assets effectively, but the right technology can change that. Modern maintenance tools help streamline workflows, centralize information, and give teams real-time visibility into what’s happening on the ground.
Here are some of the best tools worth investing in:
- Centralized CMMS/EAM software: A CMMS/EAM serves as a single source of truth for all asset information. It logs work orders, schedules preventive tasks, tracks asset history, and records costs.
- Mobile and cloud platforms: Modern IAM solutions provide mobile apps and cloud access. This means technicians can receive and update work orders in the field on tablets or phones, and managers can monitor asset status in real time. Going paperless and mobile dramatically speeds up workflows.
- Analytics, dashboards, and AI: Software that analyzes maintenance data can provide dashboards of KPIs, send alerts for anomalies, or even use AI to predict failures. Today’s top asset management platforms include data analytics that transform raw data into actionable insights. These advanced tools help organizations make faster, smarter decisions and continuously improve asset strategies.
With the right technology on your side, all the work you’re putting into infrastructure asset management gets that much easier. These tools give you the power to make data-driven decisions, plan preventive maintenance more effectively, and stay focused on the assets that matter most.
How to measure the success of optimized infrastructure asset management
After putting these optimization strategies in place, it’s important to track whether they’re actually delivering results. The KPIs and metrics below can help you measure what’s working and where you might need to make adjustments.
- Asset availability/uptime: This is the percentage of time an asset or system is operational and available for use. Improved IAM should increase availability because assets fail less and repairs are quicker. Tracking downtime hours per asset and calculating availability (%) monthly or annually will show if reliability is improving.
- Mean time between failures (MTBF): MTBF measures the average operating time between breakdowns for repairable assets. A longer MTBF indicates better reliability. If your optimizations are effective, you should see the MTBF for critical equipment lengthen over time (meaning failures are happening less frequently).
- Maintenance costs: There are several ways to track cost performance. You might look at maintenance costs as a percentage of asset value or as a portion of the operating budget and aim to reduce them without sacrificing reliability. Alternatively, track unplanned maintenance vs. planned maintenance costs. As IAM optimizes operations, unexpected emergency repair costs should drop.
- Asset utilization: Particularly in manufacturing and facilities, asset utilization (the degree to which equipment capacity is used) is a key metric. Better asset management practices can improve utilization, for instance, by reducing breakdowns that leave capacity idle or by coordinating maintenance so that it minimally impacts production.
Beyond these operational KPIs, consider broader outcome metrics:
- ROI and cost savings: Calculate the return on investment for your asset management improvements. This can be done through case studies or before-and-after comparisons.
- Asset lifespan and replacement deferrals: If a goal is to extend the useful life of aging assets, track how long assets are staying in service before replacement. If optimized maintenance adds a few years of life to a set of assets, that translates to capital expenditure deferrals.
- Sustainability and environmental impact: As organizations prioritize sustainability, IAM plays a role here, too. Well-maintained infrastructure operates more efficiently, which can reduce energy consumption and emissions. Track energy usage of assets (energy per unit of output, for example) to see if maintenance improvements are yielding efficiency gains.
In essence, define a set of KPIs that align with your objectives (reliability, cost, safety, sustainability) and regularly review them. An IAM program should establish baseline metrics at the start, set targets, and then measure periodically (monthly, quarterly, annually) to track progress.
Set yourself up for long-term success through optimized asset management
Taking a more strategic approach to infrastructure asset management can make a real difference for organizations of all sizes. It helps teams reduce downtime, extend the life of aging assets, and make better use of maintenance resources. A centralized CMMS like MaintainX supports that strategy by making it easier to track asset data, coordinate work, and make informed decisions based on real-time information.
When these systems are paired with the right strategies and tracked through clear KPIs, they create a strong foundation for long-term performance. The goal is to improve day-to-day operations while also ensuring your infrastructure can support your organization’s needs well into the future.
FAQs on Infrastructure Asset Management
La gestión de activos de infraestructura se aplica en varios sectores, incluidos los municipales (carreteras, puentes, alcantarillado), los servicios públicos (redes eléctricas, tuberías de agua), el transporte (ferrocarriles, aviación) y la fabricación (equipos de fábrica). Cualquier proceso sistemático para gestionar los activos físicos y los proyectos de infraestructura a lo largo de su ciclo de vida se califica como IAM, lo que ayuda a garantizar que los sistemas críticos permanezcan seguros y funcionales.
Un plan de administración de activos de infraestructura es una estrategia documentada que describe cómo una organización administrará sus activos para lograr objetivos específicos. Por lo general, incluye el inventario de activos, las evaluaciones del estado, los objetivos de nivel de servicio, las estrategias de mantenimiento y los planes financieros. Esta hoja de ruta guía tanto las actividades de mantenimiento diarias como las inversiones de capital a largo plazo, al tiempo que incorpora consideraciones de gestión de riesgos.
Las 5 P de la gestión de activos son:
- Personas: Contar con personal capacitado que comprenda cómo mantener y operar los activos de manera efectiva
- Procesos: Establecer procedimientos estandarizados para las actividades de mantenimiento y la toma de decisiones
- Productos: Selección de las herramientas, tecnologías y sistemas adecuados para respaldar la administración de activos
- Rendimiento: Medir y monitorear las métricas clave para garantizar que los activos brinden los resultados esperados
- Planificación: Adoptar un enfoque proactivo para la gestión del ciclo de vida de los activos y programación de mantenimiento
See MaintainX in action