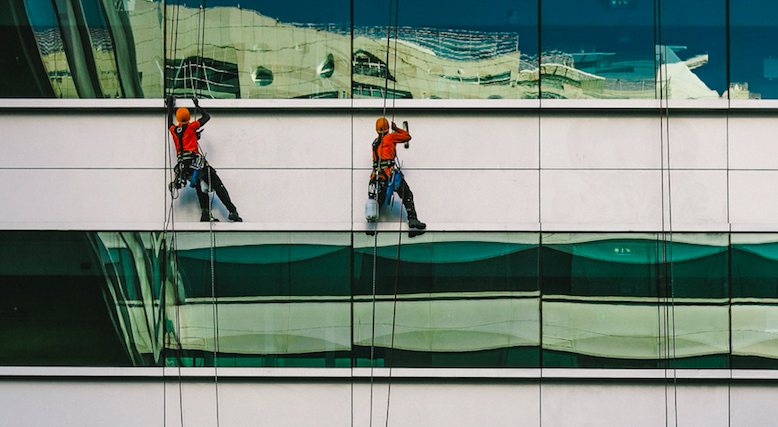
Según el Consejo Nacional de Seguridad, un trabajador se lesiona en el trabajo cada siete segundos en los Estados Unidos. Lamentablemente, muchas de estas lesiones en el lugar de trabajo son graves. La organización afirma que en 2018 se produjeron 4.493 muertes evitables en el lugar de trabajo. ¿Por qué ocurrieron estas tragedias innecesarias? Con demasiada frecuencia se debe a que no existían procedimientos de seguridad en el lugar de trabajo.
Si bien es imposible especular exactamente qué ocurrió en cada situación, es probable que las instalaciones asociadas no estandarizaran ni hicieran cumplir los procedimientos de seguridad recomendados. Los gerentes generales, de seguridad y de planta son responsables de cumplir con procedimientos operativos estándar (SOP) que protegen a los compañeros de trabajo de cualquier daño. Los buenos gerentes de seguridad siguen la ley de Murphy para bien o para mal: «Todo lo que pueda salir mal, saldrá mal».
Desafortunadamente, no es inusual que los gerentes de las instalaciones y los técnicos de mantenimiento no sigan las reglas de seguridad cuando las cosas se ponen difíciles. Los procedimientos de seguridad por sí solos no protegen a los trabajadores de las lesiones; los líderes deben hacerlos cumplir mediante programas de capacitación en seguridad que les permitan a los empleados tomar buenas decisiones.
En esta publicación, revisaremos algunos de los peligros laborales industriales y de oficina más comunes, junto con los procedimientos de trabajo estandarizados para evitarlos. También haremos sugerencias para mejorar el cumplimiento, digitalizar los registros de auditoría de seguridad y ahorrar tiempo como administradores de instalaciones.
Empecemos por definir los procedimientos de seguridad en el lugar de trabajo.
¿Qué son los procedimientos de seguridad en el lugar de trabajo?
Los procedimientos de seguridad en el lugar de trabajo, también conocidos como protocolos o pautas de seguridad, son un conjunto de medidas e instrucciones establecidas diseñadas para garantizar el bienestar y la seguridad física de los empleados, visitantes y cualquier otra persona presente en un lugar de trabajo. Estos procedimientos se implementan para prevenir accidentes, lesiones y riesgos laborales y para responder de manera efectiva en caso de emergencias.
Los procedimientos incluyen tareas relacionadas con el trabajo que abordan los problemas de seguridad, el equipo de seguridad y las precauciones de seguridad en el área de trabajo.
Las organizaciones pueden medir el éxito de sus procedimientos de seguridad ocupacional en función de la constancia con la que se siguen. Por lo tanto, es crucial capacitar a los empleados con los conocimientos, las habilidades y las herramientas que necesitan para evitar posibles peligros.
Al desarrollar procedimientos de seguridad en el lugar de trabajo, es esencial llevar a cabo evaluaciones exhaustivas de todos los tipos de riesgos potenciales. Veamos los tipos de riesgos más comunes y sus procedimientos de seguridad asociados.
6 tipos de procedimientos de seguridad
Las condiciones inseguras se clasifican en varias categorías que justifican los siguientes tipos de procedimientos de seguridad:
- Físico: Los peligros físicos son factores ambientales que pueden causar daño a los empleados sin tocarlos necesariamente. Algunos ejemplos son la presión, la radiación, el ruido y las alturas.
- Seguridad: Los riesgos de seguridad incluyen los cables expuestos que hacen tropezar a los empleados, los peligros eléctricos que los electrocutan y cualquier objeto que cause lesiones relacionadas con el trabajo por contacto.
- Ergonómico: Los riesgos ergonómicos son factores físicos que dañan el sistema musculoesquelético de los empleados. Algunos ejemplos son los movimientos demasiado repetitivos, los asientos incómodos que provocan una mala postura y las estaciones de trabajo mal configuradas.
- Sustancia química: Esta categoría incluye las amenazas que representan las sustancias peligrosas que pueden causar lesiones graves o riesgos para la salud. La exposición a sustancias químicas puede provocar irritación de la piel, ceguera, irritación del sistema respiratorio, corrosión y explosiones.
- Biológico: Algunos ejemplos de peligros biológicos son los animales, los insectos, las bacterias y los virus que pueden afectar negativamente a la salud de los empleados. A menudo son el resultado del moho, los fluidos corporales como la sangre, el polvo, las alimañas, las aguas residuales y las plantas dañinas de los entornos de trabajo.
- Psicológico: Se refieren a los peligros que afectan la salud mental y el bienestar de los empleados. Los ejemplos incluyen la violencia en el lugar de trabajo, el estrés, la victimización y el acoso sexual.
Es importante tener en cuenta todas estas categorías al desarrollar procedimientos de seguridad para proteger a los empleados. La negligencia puede poner en peligro el bienestar de los empleados y resultar en sanciones privativas de libertad y financieras para la organización.
Los 5 riesgos de seguridad industrial y procedimientos de prevención más comunes
1. Accidentes de montacargas
Los accidentes con montacargas provocaron 79 muertes en lugares de trabajo en EE. UU. y 8.140 lesiones en 2019. según Injury Facts. ¿Qué hace que estas máquinas sean tan peligrosas? Pueden pesar hasta 9,000 libras y son propensas a volcarse cuando están sobrecargadas.
Desafortunadamente, se sabe que las carretillas elevadoras a veces caen sobre los operadores de las máquinas cuando saltan durante los vuelcos. La buena noticia es que la mayoría de los accidentes con montacargas se pueden prevenir. La elaboración de listas de verificación preoperatorias puede ayudar a prevenir los accidentes con montacargas en el lugar de trabajo.
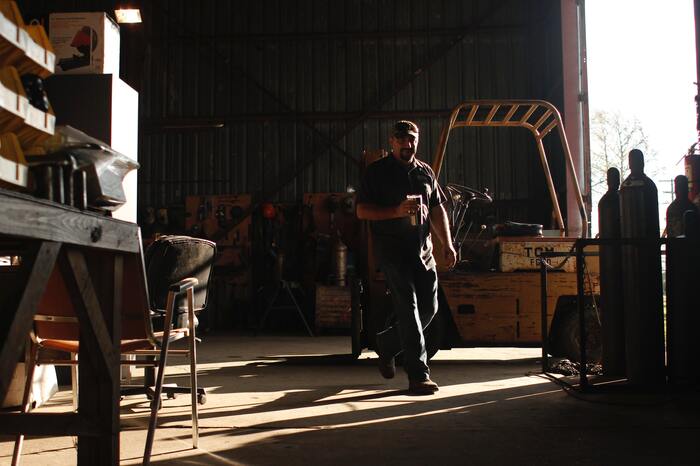
OSHA (Administración de Seguridad y Salud Ocupacional) proporciona directrices recomendadas para prevenir accidentes con montacargas en plantas, fábricas e instalaciones de fabricación. Por ejemplo, se alienta a las organizaciones a prohibir que los conductores no certificados y los menores de 18 años conduzcan los vehículos.
Las tareas que se deben incluir en las listas de verificación de seguridad de montacargas incluyen:
- Compruebe si hay fugas y otros defectos visibles.
- Asegúrese de que la extensión del respaldo de carga funciona correctamente.
- Revise las mangueras hidráulicas y las cadenas del mástil.
- Asegúrese de que los protectores de dedos funcionan bien.
- Elimine la suciedad del compartimento manual.
- Asegúrese de que los operadores lleven cascos.
- Inspeccione los niveles de líquido, incluidos los de frenos, hidráulicos y de transmisión.
- Asegúrese de que el cinturón de seguridad funcione.
- Compruebe los controles de la dirección y los frenos.
- Evalúe el estado general de la carretilla elevadora, incluida la presión de los neumáticos.
Además, cada montacargas viene con recomendaciones del fabricante para la inspección y el mantenimiento específicas del modelo. Realice lo sugerido mantenimiento preventivo (PM) para mantener los vehículos en óptimas condiciones de rendimiento. Por último, los operadores deben distribuir los materiales de manera uniforme para evitar que la carretilla elevadora se vuelque.
2. Incidentes de incendio
Según la Oficina de Estadísticas Laborales, 99 trabajadores murieron a causa de incendios y explosiones en el lugar de trabajo en 2019. Las plantas industriales y de fabricación se ocupan de más de 37 000 incendios cada año. Y las organizaciones pierden miles de millones de dólares cada año debido a incendios y explosiones accidentales. Por supuesto, los procedimientos de seguridad adecuados pueden contener los incendios en sus etapas iniciales.
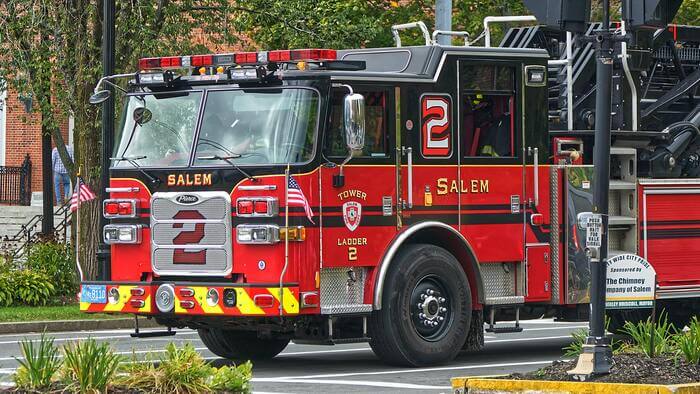
Tareas que se deben incluir en las listas de verificación de seguridad contra incendios:
- Asegúrese de que los extintores estén en buenas condiciones de funcionamiento.
- Compruebe que las señales de los ascensores de bomberos sean visibles y legibles.
- Asegúrese de que las bocas de riego y los enrolladores de mangueras funcionen.
- Inspeccione y limpie los sistemas de ventilación de los edificios.
- Mantenga los materiales inflamables alejados de las máquinas que se sabe que se sobrecalientan.
- Elimine las obstrucciones de las salidas de emergencia.
- Compruebe que los circuitos eléctricos no estén sobrecargados.
- Tenga a mano el equipo de protección contra incendios adecuado.
- Apague los aparatos eléctricos que no estén en uso.
- Deseche adecuadamente el papel, la basura y otros materiales inflamables.
- Mantenga los cables eléctricos separados en lugar de tenderlos en cadena.
Además, las organizaciones deben instalar alarmas contra incendios y detectores de humo para alertarlas de los incendios lo antes posible.
3. Resbalones y caídas accidentales
Según el Instituto Nacional de Seguridad de Suelos (NFSI), más de 1 millón de visitas a la sala de emergencias del hospital son el resultado de resbalones y caídas accidentales. Y aproximadamente el 5 por ciento de esas personas sufren fracturas.
Los resbalones y caídas rara vez resultan en muertes. Sin embargo, pueden provocar que las organizaciones se retrasen en los objetivos de producción y pierdan dinero debido a las reclamaciones de compensación de los empleados. Un hecho poco conocido: los resbalones y las caídas son la causa principal de las reclamaciones de compensación de los empleados en los Estados Unidos. La mayoría de estos accidentes se deben a superficies resbaladizas y a la poca iluminación de las instalaciones.
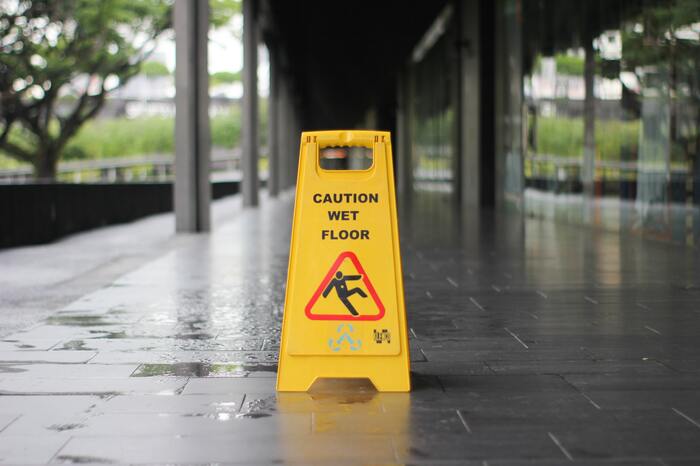
Procedimientos de seguridad para prevenir resbalones y caídas:
- Muestre letreros de resbalones al limpiar.
- Limpie inmediatamente los derrames con las soluciones adecuadas.
- Cubra los cordones y cables que puedan provocar tropiezos.
- Use zapatos cerrados y mantenga los cordones atados.
- Cierre los cajones y armarios inmediatamente después de usarlos.
- Garantice una iluminación adecuada en todos los edificios.
- Coloque letreros en áreas peligrosas, como terrenos irregulares.
- Coloque de forma segura los pasamanos junto a las escaleras.
Los resbalones y las caídas se pueden prevenir si todos actúan con suficiente precaución. Las inspecciones periódicas y el mantenimiento proactivo también pueden ayudar a garantizar que las instalaciones funcionen correctamente para evitar resbalones y caídas.
4. Arranques accidentales de máquinas
En ocasiones, las máquinas pueden encenderse accidentalmente durante el mantenimiento o la reparación. En la mayoría de los casos, estos accidentes son mortales o provocan una discapacidad permanente. Por esta razón, es vital garantizar que las piezas del equipo eléctrico estén correctamente apagadas y bloqueadas durante el servicio de mantenimiento.
Los operadores solo deben reiniciar las máquinas una vez que sea seguro hacerlo; este proceso de seguridad industrial se conoce como Etiqueta de bloqueo. Este procedimiento de seguridad ayuda a prevenir alrededor de 50 000 lesiones y 120 muertes cada año, según OSHA. Procedimientos LOTO implican el uso de mecanismos de bloqueo para bloquear las máquinas en su lugar y señalización visual para etiquetar los equipos con advertencias para no usar el equipo.
Los procedimientos de etiquetado de bloqueo incluyen los siguientes pasos:
- Paso 1: Identifique el activo que se va a bloquear y etiquetar, su ubicación específica, las fuentes de energía y los procedimientos para cerrar y reiniciar el activo.
- Paso 2: Notifique a los empleados el cierre previsto y el tiempo durante el cual el activo no estará disponible.
- Paso 3: Cierre el activo siguiendo los procedimientos descritos.
- Paso 4: Desconecte las fuentes de energía principales del activo. Estas pueden incluir aire comprimido, gas, agua, vapor y electricidad.
- Paso 5: Desconecte las fuentes de energía secundarias. Estas pueden incluir la energía residual, como el calor atrapado, las presiones, los humos y la tensión del resorte.
- Paso 6: Bloquee los activos y etiquételos con un dispositivo Lockout Tagout. Una persona de mantenimiento designada y autorizada para instalar y retirar el dispositivo debe ser la única persona que administre este proceso. El dispositivo debe permanecer en su lugar durante los cambios de turno.
- Paso 7: Una vez finalizados los trabajos de mantenimiento, el personal autorizado puede retirar los dispositivos Lockout Tagout y volver a encender el equipo.
Es crucial que las organizaciones revisen y actualicen periódicamente sus procedimientos de bloqueo y etiquetado de acuerdo con los cambios en los activos, sin importar cuán pequeños sean.
5. Accidentes químicos
Según OSHA, las organizaciones utilizan aproximadamente 650.000 tipos diferentes de productos químicos en el lugar de trabajo cada año.
Alrededor de 32 millones de trabajadores están expuestos a una o más sustancias químicas peligrosas en el trabajo. Los peligros asociados con la exposición a sustancias químicas incluyen quemaduras y erupciones cutáneas, intoxicaciones, trastornos del sistema nervioso y la muerte. Por estas razones, los empleadores deben hacer todo lo posible para proteger a los trabajadores contra el mal manejo y la interacción incorrecta con los productos químicos.
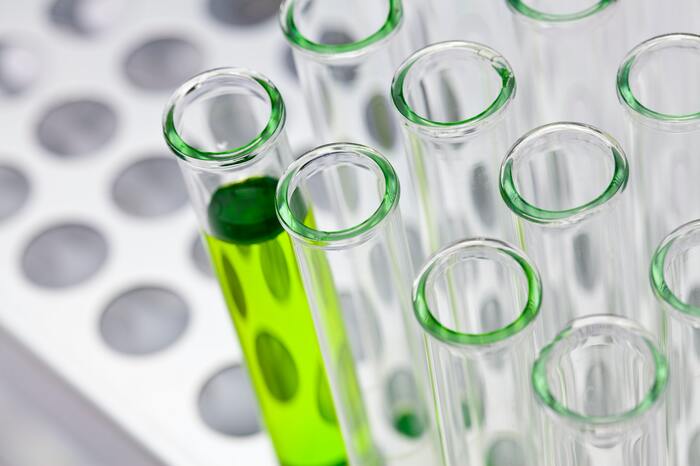
Las listas de verificación de seguridad química de Osha suelen indicar a los trabajadores que:
- Etiquete cada producto químico y anote sus efectos secundarios.
- Asegúrese de que los productos químicos se almacenen adecuadamente lejos de otros empleados. Solo quienes trabajan con productos químicos deben tener acceso a ellos.
- Proporcione a los trabajadores un equipo de protección personal cuando manipulen productos químicos.
- Almacene los productos químicos combustibles en unidades de almacenamiento a prueba de fuego.
- Guarde los productos químicos en su embalaje original.
- Almacene muchos botiquines de primeros auxilios disponibles.
- Compruebe si hay derrames de productos químicos dentro de plazos periódicos.
Además, se alienta a los empleadores a capacitar a los empleados sobre los aspectos básicos de los primeros auxilios en caso de exposición accidental a sustancias químicas. Además, todos los empleados deben dar su aprobación para leer y comprender fichas de datos de seguridad (MSDS) antes de usar productos químicos.
Los 8 riesgos de seguridad más comunes en la oficina
No es sorprendente que los almacenes industriales, las plantas y las fábricas generalmente implementen procedimientos de seguridad más completos que sus homólogos que viven en oficinas.
Estos trabajadores suelen operar maquinaria compleja y, con mayor frecuencia, entran en contacto con materiales de alto riesgo que requieren cuidados cruciales. Pero eso no significa que los trabajadores de oficina no deban seguir también las pautas recomendadas.
A principios de 2020, los espacios de oficina se preocuparon cada vez más por hacer cumplir las listas de verificación de saneamiento para proteger a los empleados de la COVID-19. Sin embargo, también existen riesgos de seguridad comunes que los equipos de gestión pretenden mitigar en los entornos de escritorio.
Los riesgos de seguridad más comunes en la oficina incluyen:
- Caídas (por escombros sueltos y superficies irregulares)
- Tensiones ergonómicas (causadas por movimientos repetitivos y mala postura)
- Tensión ocular (causada por monitores de computadora)
- Brotes de incendios
- Mala calidad del aire
- Electrocución
- Exposición a peligros químicos y biológicos
- Proyectiles
Obviamente, los riesgos de seguridad anteriores requieren menos explicación que los experimentados por los trabajadores industriales que operan equipos complejos. Por lo tanto, mitigar el riesgo requiere mucho menos esfuerzo en un entorno de oficina. Consulte la revista Salud y Seguridad»Reconociendo los peligros ocultos: 25 pasos para una oficina más segura» para obtener más información.
Los gerentes de oficinas y almacenes pueden mejorar el cumplimiento mediante listas de verificación de auditoría de seguridad. ¿Cuál es la forma más fácil de organizar un programa excepcional de seguridad en el lugar de trabajo? ¡Digitalízate!
Mejore el cumplimiento con la digitalización de los procedimientos de seguridad
Como se mencionó anteriormente, los empleados pueden estar expuestos a muchos posibles riesgos de seguridad tanto en entornos industriales como de oficina. La mejor manera de organizar las auditorías de seguridad y reducir el estrés que supone hacer cumplir la ley es asignar listas de verificación como órdenes de trabajo de mantenimiento preventivo mediante un Sistema computarizado de gestión del mantenimiento (CMMS).
Un CMMS es una plataforma digital centralizada que organiza las operaciones de mantenimiento de una empresa, agiliza los procedimientos de todo tipo (auditorías de seguridad, control de calidad, mantenimiento preventivo) y elimina las listas de verificación en papel.
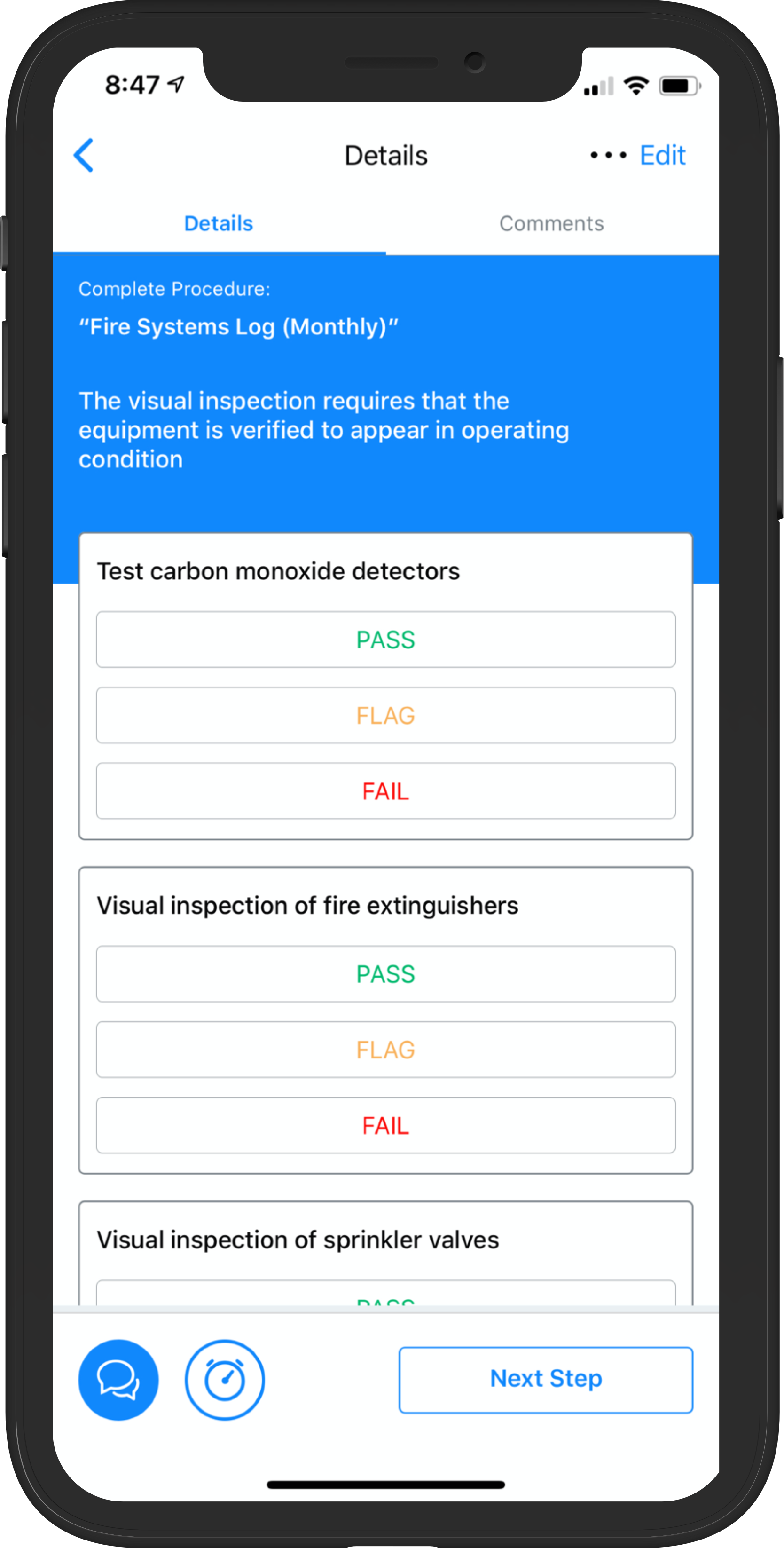
Si bien la tecnología ha sido históricamente el dominio de los almacenes, el CMMS moderno ahora es accesible para todos los sectores. Con las aplicaciones basadas en la nube, las organizaciones, tanto pequeñas como grandes, pueden descargar una aplicación, crear una lista de verificación digital y asignarla a los empleados en cuestión de minutos.
Los beneficios de digitalizar los procedimientos de seguridad en el lugar de trabajo incluyen:
- Simplificación de la supervisión de la gestión: Facilita el seguimiento y la estandarización de los riesgos y los procesos de mitigación.
- Mejora de la comunicación: Algunas plataformas de CMMS, como MaintainX, incluso incluyen mensajes de equipo que permiten la solución de problemas en tiempo real.
- Ahorro de tiempo: Los administradores pueden crear, asignar y editar rápidamente plantillas de listas de verificación digitales a las que se puede acceder fácilmente a través de dispositivos móviles.
- Reducir la confusión: La transferencia del cumplimiento de las funciones es más fácil de facilitar durante los cambios de turno de los empleados.
- Aumentar la transparencia: Todo el mundo sabe quién está trabajando en qué tarea a través del calendario de órdenes de trabajo del CMMS.
- Optimización de las auditorías: Los gerentes pueden entregar fácilmente los registros digitales exportados para cumplir con las auditorías reglamentarias.
- Mejora de la eficiencia: El CMMS proporciona acceso a los indicadores clave de rendimiento (KPI) que destacan las oportunidades de mejora.
En resumen: las herramientas digitales de seguridad en el lugar de trabajo facilitan a las organizaciones monitorear, predecir y prevenir las vulnerabilidades de seguridad.
Recursos sobre procedimientos de seguridad
OSHA proporciona varios recursos para ayudar a las organizaciones a mejorar la seguridad en el lugar de trabajo. A continuación se presentan algunas de sus publicaciones más útiles y un par de otras guías dignas de mención:
- Prácticas recomendadas por la OSHA para los programas de seguridad y salud
- Recursos de seguridad y salud de la OSHA para pequeñas empresas
- Manual de OSHA para pequeñas empresas
- Otros recursos de capacitación sobre seguridad y salud de la OSHA
- Prácticas recomendadas por la OSHA para los programas de seguridad y salud en la construcción
- Departamento de Trabajo de los Estados Unidos, Seguridad y Salud en el Trabajo
- Mano de obra de Missouri: Programa de seguridad de los trabajadores de Missouri
- Guía de recursos para pequeñas empresas del Instituto Nacional de Seguridad y Salud Ocupacional (NIOSH)
Manténgase seguro con MaintainX
Tanto las grandes organizaciones como las pequeñas empresas deben hacer todo lo posible para cumplir con las normas de seguridad. No hacer cumplir las prácticas seguras en el lugar de trabajo puede provocar daños a los empleados y a la propiedad, litigios y compensaciones laborales. Organizar los protocolos de seguridad en el lugar de trabajo con herramientas de cumplimiento digital es la forma más fácil de cumplir con las regulaciones.
El CMMS móvil de MaintainX facilita:
- Cree, asigne y supervise listas de verificación editables.
- Supervise el cumplimiento con actualizaciones en tiempo real.
- Chatea con tus compañeros de trabajo mediante mensajería instantánea.
- Mantenga las pruebas de auditoría digital de cumplimiento.
- Sube y comparte documentos importantes.
Los empleados pueden acceder a las listas de verificación empresariales, los documentos importantes y las políticas de seguridad desde la comodidad de sus teléfonos inteligentes. Si cree que MaintainX puede ayudar a su organización a mejorar la seguridad de los empleados, los clientes y las partes interesadas, lo invitamos a descargar nuestra aplicación gratuita ahora.
Preguntas frecuentes sobre procedimientos de seguridad en el lugar de trabajo
¿Qué son los procedimientos de seguridad?
Los procedimientos de seguridad son protocolos documentados diseñados para prevenir accidentes y proteger a los empleados de los peligros en el lugar de trabajo. Incluyen instrucciones paso a paso para realizar las tareas de manera segura, pautas para manipular equipos y materiales, planes de respuesta ante emergencias y medidas preventivas para identificar y controlar los riesgos antes de que ocurran los incidentes. Los procedimientos de seguridad eficaces incorporan los requisitos reglamentarios, las mejores prácticas del sector y los peligros específicos de la organización.
¿Qué es el procedimiento de seguridad de Take 5?
El procedimiento de seguridad Take 5 es un proceso simple de evaluación de riesgos de cinco pasos que los trabajadores realizan antes de comenzar una tarea. Alienta a los empleados a: (1) detenerse y pensar en el trabajo que deben realizar, (2) detectar los peligros, (3) evaluar los riesgos que presentan estos peligros, (4) controlar los peligros mediante la implementación de medidas de seguridad y (5) monitorear la eficacia de los controles mientras trabajan. Esta rápida lista de control mental ayuda a los trabajadores a desarrollar un conocimiento de la situación e identificar de manera proactiva los peligros potenciales.
¿Cuáles son los 5 pasos de seguridad?
Los 5 pasos de la seguridad forman un marco integral para la gestión de la seguridad en el lugar de trabajo:
- Identifique los peligros mediante inspecciones en el lugar de trabajo, análisis de tareas y comentarios de los empleados.
- Evalúe los riesgos evaluando la gravedad y la probabilidad de posibles daños.
- Controle los riesgos mediante la jerarquía de controles (eliminación, sustitución, controles de ingeniería, controles administrativos, PPE).
- Implemente y comunique las medidas de seguridad a través de la capacitación, los procedimientos y las señales visuales.
- Revise y actualice supervisando continuamente la eficacia y realizando mejoras en función de los datos de rendimiento y las investigaciones de incidentes.
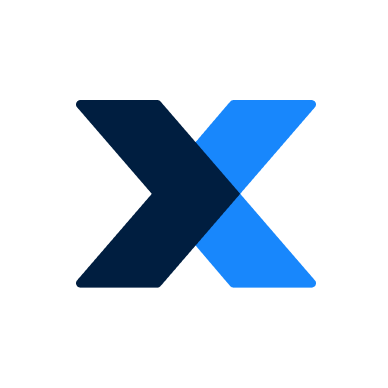
El equipo de MaintainX está formado por expertos en mantenimiento y fabricación. ¡Están aquí para compartir el conocimiento de la industria, explicar las características del producto y ayudar a los trabajadores a hacer más con MaintainX!