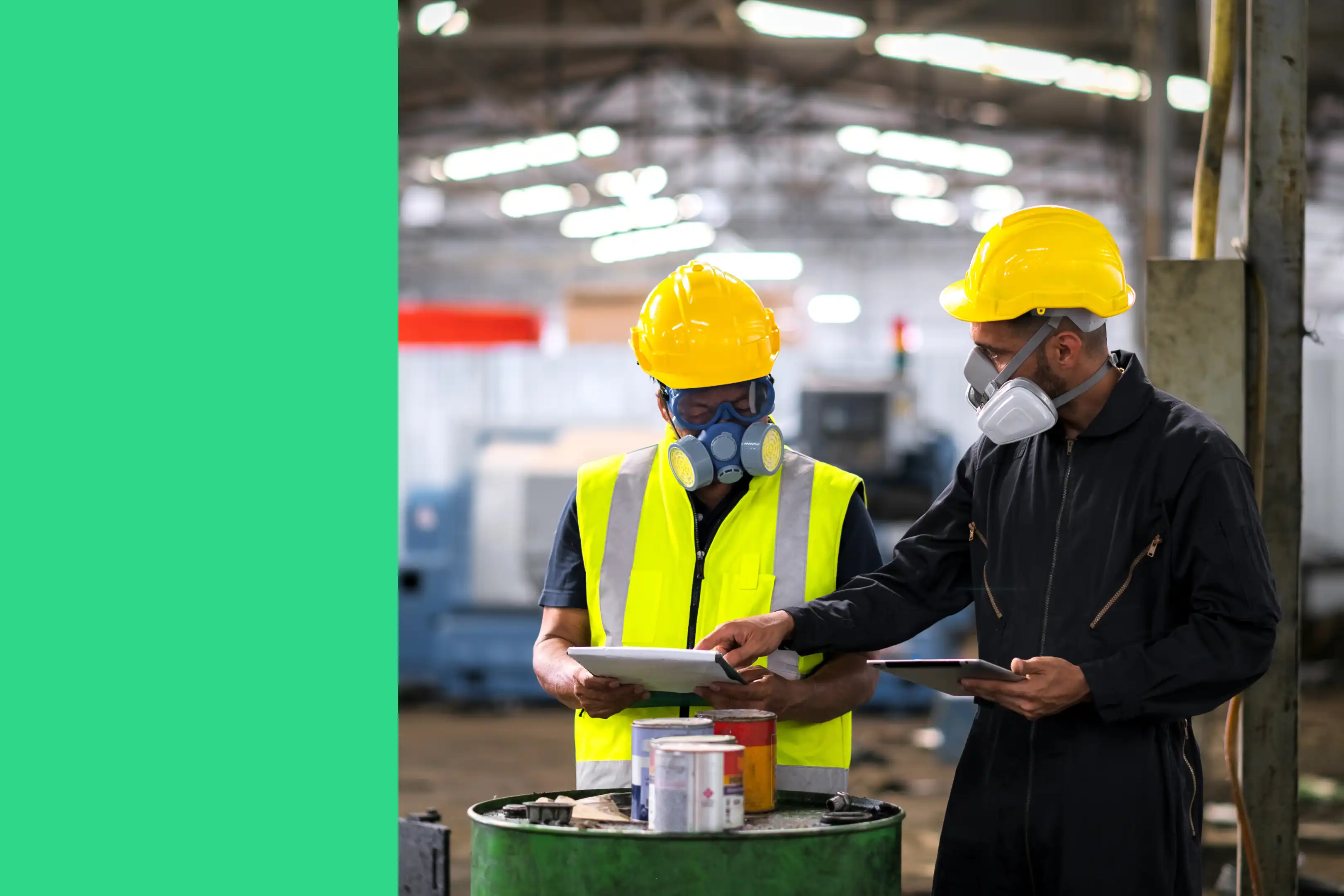
De acordo com o Bureau de Estatísticas do Trabalho dos EUA, um trabalhador morreu a cada 99 minutos devido a uma lesão relacionada ao trabalho nos Estados Unidos em 2023. Também houve 5.283 acidentes de trabalho fatais registrados em todo o país. E embora essa seja uma redução de 3,7% em relação a 5.486 em 2022, você sabe que as preocupações com a segurança persistem em setores onde procedimentos de segurança adequados poderia evitar inúmeros acidentes.
Quando as organizações não conseguem implementar e aplicar procedimentos de segurança eficazes, as consequências podem ser devastadoras. Como gerente geral, de segurança ou fábrica, você é responsável por aderir aos procedimentos operacionais padrão (SOPs) que protegem os trabalhadores contra danos e minimizam a exposição a condições inseguras. Regras abrangentes de segurança no local de trabalho servem como base para a criação de um ambiente de trabalho seguro, onde a segurança pessoal se torna tarefa de todos.
Em situações de alta pressão em uma instalação, os procedimentos de segurança às vezes podem ficar em segundo plano quando as demandas do local de trabalho aumentam. Até mesmo as melhores equipes ocasionalmente se deparam com equipamentos de segurança que precisam de inspeção, riscos elétricos que exigem atenção ou requisitos de equipamento de proteção individual que são negligenciados durante os períodos de maior movimento.
Simplesmente estabelecer protocolos de segurança não é suficiente. Você precisa aplicá-las continuamente em programas robustos de treinamento de segurança que capacitem seus funcionários a identificar possíveis riscos e fazer escolhas seguras que protejam a si mesmos e a seus colegas de trabalho.
Neste post, examinaremos os riscos mais comuns de segurança industrial e de escritório, juntamente com procedimentos padronizados para prevenir lesões no local de trabalho. Você receberá orientação sobre como conduzir avaliações de risco completas e implementar inspeções de segurança adequadas. Também mostraremos como usar ferramentas digitais para melhorar a conformidade com as normas de segurança e, ao mesmo tempo, manter uma documentação abrangente do seu programa de segurança.
Principais conclusões
- A implementação de procedimentos de segurança consistentes em suas instalações evita acidentes e protege sua equipe contra riscos evitáveis.
- As principais violações da OSHA em 2024 incluem proteção contra quedas, comunicação de risco e procedimentos de bloqueio/sinalização. Priorizar essas áreas pode reduzir significativamente os acidentes de trabalho.
- Os ambientes industriais enfrentam desafios de segurança exclusivos, incluindo lesões ergonômicas, problemas de qualidade do ar interno e riscos psicológicos que exigem estratégias de prevenção específicas.
- Ao digitalizar os procedimentos de segurança por meio de plataformas CMMS, você melhora as taxas de conformidade, simplifica os relatórios e cria responsabilidade, preservando o conhecimento de segurança organizacional.
Quais são os procedimentos de segurança no local de trabalho?
Como profissional de manutenção, você sabe que os procedimentos de segurança no local de trabalho protegem sua equipe contra perigos, evitam acidentes e garantem a conformidade regulatória. Esses procedimentos vão além da conformidade básica para estabelecer uma abordagem proativa cultura de segurança que integra a segurança ocupacional em todos os aspectos de suas operações diárias.
De acordo com OSHA (Administração de Segurança e Saúde Ocupacional), os empregadores devem “manter seu local de trabalho livre de sérios riscos reconhecidos” de acordo com a Cláusula de Dever Geral da Lei de SST. Procedimentos de segurança eficazes ajudam as organizações a cumprir essa obrigação identificando, avaliando e controlando as questões de segurança no local de trabalho antes que os acidentes ocorram.
UM programa robusto de segurança no local de trabalho em sua instalação deve incluir esses elementos interconectados:
- Identificação de perigos e avaliação de riscos: Avaliar sistematicamente seu local de trabalho para identificar possíveis riscos à segurança, incluindo riscos físicos, químicos, elétricos, ergonômicos e psicológicos
- Políticas de segurança escritas e SOPs: Desenvolver documentação clara e acessível que descreva protocolos específicos para operar equipamentos com segurança, manusear materiais perigosos e responder a emergências
- Programas de treinamento de segurança: Fornecer instruções abrangentes à sua equipe sobre o reconhecimento de perigos, o uso adequado do equipamento de proteção individual e o cumprimento das regras de segurança estabelecidas
- Inspeções de segurança regulares: Realização periódica inspeções de segurança para verificar a conformidade com os procedimentos de segurança e identificar áreas que precisam ser melhoradas
- Notificação e investigação de incidentes: Estabelecer protocolos claros para relatar acidentes, quase-acidentes e condições inseguras, seguidos de investigações completas para evitar a recorrência
- Planejamento de resposta a emergências: Criação de procedimentos detalhados para lidar com incêndios, derramamentos de produtos químicos, desastres naturais, emergências médicas e outras situações de crise
A OSHA está enfatizando cada vez mais os esforços reforçados de fiscalização com o aumento das inspeções, particularmente em setores de alto risco, como construção e manufatura. A agência também se concentrou na coleta aprimorada de dados para identificar padrões de acidentes de trabalho, com os empregadores de certos setores agora obrigados a enviar informações mais detalhadas sobre lesões e doenças eletronicamente.
Seis tipos de procedimentos de segurança
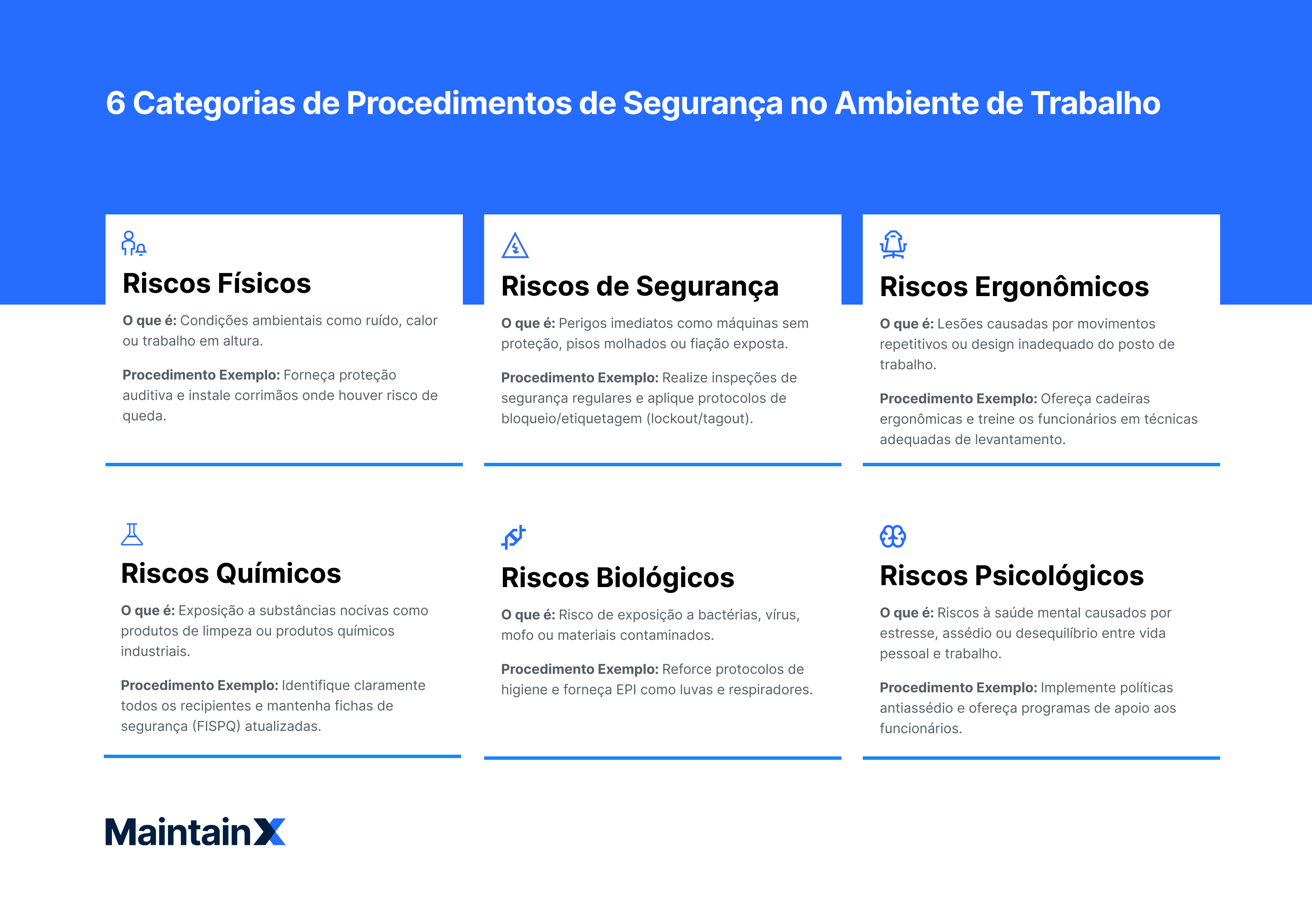
As condições inseguras em seu local de trabalho se enquadram em várias categorias, cada uma exigindo procedimentos de segurança específicos para proteger efetivamente sua equipe e evitar acidentes.
- Riscos físicos: Esses fatores ambientais podem prejudicar seus funcionários sem necessariamente fazer contato direto. Os exemplos incluem ruído excessivo que pode prejudicar a audição, exposição à radiação, temperaturas extremas que podem causar estresse térmico ou ferimentos causados pelo frio e trabalho em alturas sem a proteção adequada contra quedas. Os procedimentos de segurança para riscos físicos geralmente envolvem controles de engenharia, controles administrativos e fornecimento de equipamento de proteção individual apropriado.
- Riscos de segurança: Isso inclui condições que podem causar acidentes e ferimentos imediatos por meio do contato direto. Riscos de segurança comuns em suas instalações podem incluir fiação elétrica exposta que cria riscos elétricos, máquinas desprotegidas com partes móveis, pisos úmidos que contribuem para incidentes de escorregões e quedas e materiais armazenados inadequadamente que podem cair e causar greves nos trabalhadores. Os procedimentos de segurança adequados incluem inspeções de segurança regulares, implementação de protocolos de bloqueio/sinalização para equipamentos elétricos e garantia de práticas domésticas adequadas.
- Riscos ergonômicos: Esses fatores danificam o sistema musculoesquelético de um funcionário por meio de movimentos repetitivos, técnicas de elevação inadequadas ou estações de trabalho mal projetadas. Os procedimentos de segurança que tratam dos riscos ergonômicos incluem ajustes na estação de trabalho, rotação de tarefas para evitar esforços repetitivos, treinamento adequado em técnicas de elevação e fornecimento de equipamentos ergonômicos projetados para minimizar a tensão física.
- Riscos químicos: Eles representam ameaças por meio de substâncias perigosas que podem causar ferimentos graves ou riscos à saúde após a exposição. A exposição a produtos químicos pode resultar em irritação da pele, problemas respiratórios, cegueira, danos por corrosão ou, em casos graves, explosões e incêndios. Seus procedimentos de segurança para o manuseio de produtos químicos devem incluir rotulagem adequada, manutenção de fichas de dados de segurança detalhadas, fornecimento de sistemas de ventilação, implementação de protocolos de armazenamento de produtos químicos e exigência de equipamento de proteção individual como luvas, óculos e respiradores.
- Riscos biológicos: Isso inclui a exposição a organismos prejudiciais, como bactérias, vírus, insetos, animais ou plantas, que podem afetar adversamente a saúde dos funcionários. Eles geralmente resultam do contato com mofo, sangue, esgoto, materiais contaminados ou plantas nocivas no ambiente de trabalho. Os procedimentos de segurança eficazes incluem programas de vacinação, protocolos de higiene, sistemas adequados de descarte de resíduos, medidas de contenção e equipamento de proteção individual apropriado para o risco biológico específico.
- Riscos psicológicos: Esses riscos afetam a saúde mental e o bem-estar geral de seus funcionários. Os exemplos incluem violência no local de trabalho, estresse excessivo, assédio, vitimização e falta de equilíbrio entre vida profissional e pessoal. Os procedimentos de segurança que abordam os riscos psicológicos incluem programas de prevenção da violência, treinamento em gerenciamento de estresse, políticas claras de combate ao assédio, programas de assistência aos funcionários e a criação de uma cultura positiva no local de trabalho que apoie a saúde mental.
Negligenciar qualquer categoria pode comprometer a saúde e o bem-estar de sua equipe e, ao mesmo tempo, expor sua organização a responsabilidades, multas regulatórias e aumento dos custos de compensação dos trabalhadores.
Cinco riscos e procedimentos de prevenção de segurança industrial mais comuns
Todos os anos, a OSHA publica uma lista dos Os 10 padrões mais citados. Aqui estão os cinco principais dessa lista para o ano fiscal de 2024:
1. Proteção contra quedas
As quedas continuam sendo a principal causa de lesões e mortes graves no local de trabalho. Em 2024, a OSHA emitiu 7.036 violações relacionadas aos requisitos de proteção contra quedas.
Procedimentos de prevenção que você pode implementar:
- Realize avaliações de risco completas para identificar possíveis riscos de queda.
- Instale grades de proteção, redes de segurança ou sistemas pessoais de proteção contra quedas adequados ao trabalhar em alturas.
- Mantenha seu piso limpo, seco e livre de riscos de tropeçar.
- Implemente programas abrangentes de treinamento em proteção contra quedas.
- Inspecione regularmente o equipamento de proteção contra quedas quanto a danos ou desgaste.
2. Comunicação de risco
Com 3.277 violações em 2024, a comunicação de perigos continua sendo uma preocupação crítica de segurança. Sua instalação provavelmente usa produtos químicos diferentes, com trabalhadores potencialmente expostos a substâncias perigosas.
Procedimentos de prevenção que você pode implementar:
- Identifique claramente todos os recipientes de produtos químicos com identificadores de produtos e avisos de perigo.
- Mantenha fichas de dados de segurança (SDS) detalhadas para todos os produtos químicos perigosos.
- Desenvolva um programa escrito de comunicação de riscos para sua equipe.
- Treine seus funcionários sobre riscos químicos e medidas de proteção.
- Implemente protocolos adequados de ventilação e armazenamento para materiais perigosos.
3. Controle de energia perigosa (bloqueio/sinalização)
A OSHA emitiu 2.967 citações por violações de bloqueio/sinalização em 2024. Paradas acidentais da máquina durante a manutenção ou manutenção podem resultar em ferimentos graves ou fatalidades.
Procedimentos de prevenção que você pode implementar:
- Desenvolva procedimentos abrangentes de bloqueio/sinalização para todos os equipamentos.
- Treine funcionários autorizados em técnicas adequadas de bloqueio/sinalização.
- Use bloqueios e etiquetas padronizados que identifiquem o funcionário que está executando o trabalho.
- Realize inspeções periódicas de seus procedimentos de bloqueio/sinalização.
- Certifique-se de que todas as fontes de energia em seu equipamento (elétricas, hidráulicas, pneumáticas etc.) sejam controladas adequadamente.
4. Segurança de escada
Com 2.897 violações em 2024, a segurança nas escadas continua sendo uma preocupação significativa em todos os setores.
Procedimentos de prevenção que você pode implementar:
- Selecione a escada certa para o trabalho (tipo e altura corretos).
- Inspecione as escadas em busca de danos ou defeitos antes de usá-las.
- Configure escadas em superfícies estáveis e niveladas, longe de portas ou áreas de tráfego intenso.
- Mantenha três pontos de contato ao escalar (duas mãos e um pé, ou dois pés e uma mão).
- Garanta que seus funcionários entendam o uso adequado da escada e os procedimentos de segurança.
5. Proteção respiratória
Com 2.835 violações, a proteção respiratória completa os cinco padrões mais citados.
Procedimentos de prevenção que você pode implementar:
- Realize avaliações no local de trabalho para identificar riscos respiratórios.
- Desenvolva um programa escrito de proteção respiratória para sua equipe.
- Selecione respiradores apropriados com base nos riscos específicos do local de trabalho.
- Forneça avaliações médicas e testes de ajuste para seus funcionários usando respiradores.
- Treine os funcionários sobre o uso, manutenção e limitações adequados do respirador.
Ao priorizar essas áreas de segurança no trabalho, as organizações podem abordar as causas mais comuns de acidentes e lesões industriais. Sistemas digitais de gerenciamento de segurança pode ajudar a simplificar a conformidade com esses procedimentos críticos de segurança e, ao mesmo tempo, manter uma documentação abrangente para os requisitos regulatórios.
Oito riscos de segurança mais comuns no escritório
Seus espaços de escritório não apresentam os mesmos perigos óbvios que os ambientes industriais, mas eles abrigam seu próprio conjunto de riscos de segurança que podem causar ferimentos, doenças e perda de produtividade quando negligenciados.
- Escorrega, tropeça e cai. Os acidentes de escritório mais comuns envolvem escorregões, tropeções e quedas, geralmente resultantes de pisos molhados, carpetes soltos, iluminação deficiente ou passarelas desordenadas. As medidas de prevenção incluem a manutenção de caminhos desobstruídos, o tratamento imediato de derramamentos, a proteção de cabos soltos, o fornecimento de iluminação adequada e a colocação de sinais de alerta para possíveis riscos.
- Lesões ergonômicas. O uso prolongado do computador, a configuração inadequada da estação de trabalho e as tarefas repetitivas podem causar distúrbios musculoesqueléticos, como síndrome do túnel do carpo, distensão no pescoço e dores nas costas. Implemente avaliações ergonômicas, forneça móveis e equipamentos ajustáveis, incentive pausas regulares e treine os funcionários sobre a postura correta e a configuração da estação de trabalho.
- Problemas de qualidade do ar interno. Ventilação deficiente, contaminantes químicos de produtos de limpeza e poluentes biológicos, como mofo, podem afetar a saúde e a produtividade dos funcionários. A manutenção regular do HVAC, os protocolos de limpeza adequados, o tratamento imediato dos danos causados pela água e a ventilação adequada ajudam a manter a qualidade saudável do ar interno.
- Riscos de incêndio. Tomadas elétricas sobrecarregadas, cabos elétricos danificados, armazenamento inadequado de materiais inflamáveis e saídas de emergência bloqueadas criam sérios riscos de incêndio. Evite incêndios em escritórios por meio de inspeções regulares do sistema elétrico, práticas adequadas de armazenamento, vias de saída de emergência limpas, extintores de incêndio em funcionamento e procedimentos abrangentes de simulação de incêndio.
- Riscos elétricos. Cabos desgastados, circuitos sobrecarregados e uso inadequado de cabos de extensão podem causar choques elétricos, queimaduras ou incêndios. Implemente inspeções elétricas regulares, evite o uso de réguas elétricas em série, substitua imediatamente os cabos danificados e treine os funcionários sobre as práticas de segurança elétrica.
- Fadiga ocular e problemas de visão. A síndrome da visão computacional afeta muitos funcionários de escritório que passam horas olhando para telas. As estratégias de prevenção incluem a implementação da regra 20-20-20 (observar algo a 20 pés de distância por 20 segundos a cada 20 minutos), posicionamento adequado do monitor, iluminação adequada e exames regulares da visão.
- Violência no local de trabalho e preocupações com a segurança. Os ambientes de escritório não estão imunes à violência no local de trabalho ou às violações de segurança. Desenvolva protocolos de segurança abrangentes, proteja pontos de entrada, forneça treinamento de resposta a emergências, implemente sistemas de gerenciamento de visitantes e estabeleça procedimentos claros de relatórios sobre comportamentos preocupantes.
- Saúde mental e riscos relacionados ao estresse. Estresse no local de trabalho, cargas de trabalho excessivas, assédio e falta de equilíbrio entre vida pessoal e profissional podem afetar gravemente a saúde mental dos funcionários. Resolva esses problemas por meio de gerenciamento razoável da carga de trabalho, políticas antiassédio, programas de assistência aos funcionários, recursos de gerenciamento de estresse e criação de uma cultura solidária no local de trabalho.
Ao identificar e abordar esses riscos comuns no escritório, você pode criar um ambiente de trabalho mais seguro que promova o bem-estar e a produtividade dos funcionários. Treinamento regular de segurança, comunicação clara e documentação adequada dos procedimentos de segurança são essenciais para manter uma cultura em que a segurança seja priorizada em todas as atividades do seu local de trabalho.
Melhore a conformidade com a digitalização de procedimentos de segurança
À medida que você trabalha para implementar procedimentos de segurança abrangentes, o desafio geralmente está na execução, na documentação e no rastreamento consistentes. As soluções digitais transformaram a forma como sua equipe pode gerenciar programas de segurança no local de trabalho, tornando a conformidade mais acessível e fornecendo informações de dados valiosas que impulsionam a melhoria contínua.
Sistemas modernos de gerenciamento de segurança digital, como sistemas computadorizados de gerenciamento de manutenção (CMMS) oferecem vantagens significativas em relação às abordagens tradicionais baseadas em papel. Essas plataformas centralizam os protocolos de segurança, simplificam as inspeções e criam trilhas de auditoria digital que demonstram conformidade regulatória ao mesmo tempo em que identificam possíveis lacunas de segurança.
Os benefícios da digitalização dos procedimentos de segurança no local de trabalho incluem:
- Monitoramento e alertas em tempo real: Os sistemas digitais fornecem visibilidade imediata do status de conformidade de segurança e podem notificar automaticamente as partes responsáveis quando as inspeções estão previstas ou quando os problemas precisam ser resolvidos.
- Responsabilidade aprimorada: Os fluxos de trabalho eletrônicos monitoram a conclusão das tarefas, criando cadeias de responsabilidade claras e garantindo que os procedimentos de segurança não sejam negligenciados durante os períodos de maior movimento.
- Coleta de dados aprimorada: As ferramentas digitais capturam informações de segurança abrangentes que podem ser analisadas para identificar tendências, problemas recorrentes e oportunidades de melhoria.
- Relatórios simplificados: gere relatórios de conformidade instantaneamente, economizando horas de trabalho administrativo para sua equipe e, ao mesmo tempo, fornecendo uma melhor documentação para inspeções regulatórias.
- Acessibilidade móvel: Seus funcionários de campo podem acessar procedimentos de segurança, relatar problemas e concluir inspeções usando smartphones ou tablets, permitindo o gerenciamento da segurança em tempo real em locais de trabalho distribuídos.
- Retenção de conhecimento: Os sistemas digitais preservam o conhecimento de segurança organizacional mesmo durante a rotatividade de funcionários, garantindo a aplicação consistente dos protocolos de segurança.
Ao implementar ferramentas de gerenciamento de segurança digital, sua equipe pode transformar a segurança de uma obrigação de conformidade em uma vantagem estratégica. Esses sistemas não apenas ajudam a evitar acidentes de trabalho, mas também melhoram a eficiência operacional, reduzindo o tempo de inatividade, diminuindo os custos de compensação dos trabalhadores e criando uma cultura em que a segurança se torna parte integrante das operações diárias, em vez de uma carga administrativa separada.
Ao selecionar uma solução de gerenciamento de segurança digital, priorize interfaces fáceis de usar, recursos móveis, fluxos de trabalho personalizáveis, recursos robustos de relatórios e potencial de integração com os sistemas existentes. A plataforma digital certa deve se adaptar às necessidades específicas de segurança da sua organização e, ao mesmo tempo, ser escalada para acomodar o crescimento e a evolução dos requisitos regulatórios.
Recursos de procedimentos de segurança
A OSHA fornece vários recursos para ajudar as organizações a melhorar a segurança no local de trabalho. Abaixo estão algumas de suas publicações mais úteis e alguns outros guias dignos de nota:
- Práticas recomendadas pela OSHA para programas de segurança e saúde
- Recursos de segurança e saúde da OSHA para pequenas empresas
- Outros recursos de treinamento em segurança e saúde da OSHA
- Práticas recomendadas pela OSHA para programas de segurança e saúde na construção
- Departamento do Trabalho dos EUA, Segurança e Saúde no Trabalho
- Guia de recursos para pequenas empresas do Instituto Nacional de Segurança e Saúde Ocupacional (NIOSH)
Construindo um local de trabalho mais seguro
Criar e manter um ambiente de trabalho seguro exige mais do que apenas estabelecer protocolos; exige comprometimento contínuo, engajamento da liderança e uma cultura em que a segurança se torne responsabilidade de todos. Programas de segurança eficazes nunca são estáticos, mas evoluem por meio de ciclos de melhoria contínua que respondem às mudanças nas condições do local de trabalho, aos riscos emergentes e às lições aprendidas com incidentes e quase-acidentes.
As organizações que se destacam em segurança no trabalho reconhecem que a prevenção é sempre mais eficaz do que a reação. Ao implementar avaliações de risco, procedimentos claros, treinamento completo e inspeções regulares, sua equipe cria ambientes onde os acidentes se tornam cada vez mais raros. Ferramentas digitais como o MaintainX ajudam as equipes a se manterem proativas, simplificando os procedimentos de segurança, automatizando os cronogramas de inspeção e fornecendo visibilidade em tempo real do status de conformidade em todas as instalações.
Perguntas frequentes sobre procedimentos de segurança no local de trabalho
Quais são os procedimentos de segurança?
Procedimentos de segurança são protocolos documentados projetados para prevenir acidentes e proteger os funcionários contra perigos no local de trabalho. Eles incluem instruções passo a passo para realizar tarefas com segurança, diretrizes para manuseio de equipamentos e materiais, planos de resposta a emergências e medidas preventivas para identificar e controlar riscos antes que ocorram incidentes. Procedimentos de segurança eficazes incorporam requisitos regulatórios, melhores práticas da indústria e perigos específicos da organização.
O que é o procedimento de segurança Take 5?
O procedimento de segurança Take 5 é um processo simples de avaliação de riscos em cinco etapas que os trabalhadores realizam antes de iniciar uma tarefa. Ele incentiva os funcionários a:
- Parar e pensar sobre o trabalho a ser feito
- Procurar perigos
- Avaliar os riscos que esses perigos apresentam
- Controlar os perigos implementando medidas de segurança
- Monitorar a eficácia dos controles durante o trabalho
Esta lista de verificação mental rápida ajuda os trabalhadores a desenvolver consciência situacional e identificar proativamente perigos potenciais.
Quais são os 5 passos da segurança?
Os 5 passos da segurança formam uma estrutura abrangente para a gestão da segurança no local de trabalho:
- Identificar perigos por meio de inspeções no local de trabalho, análise de tarefas e feedback dos funcionários.
- Avaliar riscos examinando a gravidade e a probabilidade de danos potenciais.
- Controlar riscos usando a hierarquia de controles (eliminação, substituição, controles de engenharia, controles administrativos, EPI).
- Implementar e comunicar medidas de segurança por meio de treinamento, procedimentos e sinais visuais.
- Revisar e atualizar continuamente monitorando a eficácia e fazendo melhorias com base em dados de desempenho e investigações de incidentes.
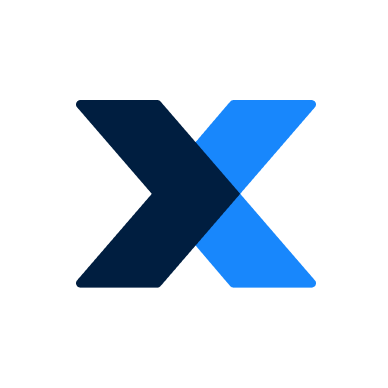
A equipe da MaintainX é formada por especialistas em manutenção e fabricação. Eles estão aqui para compartilhar o conhecimento do setor, explicar as características do produto e ajudar os funcionários a fazerem mais com o MaintainX!