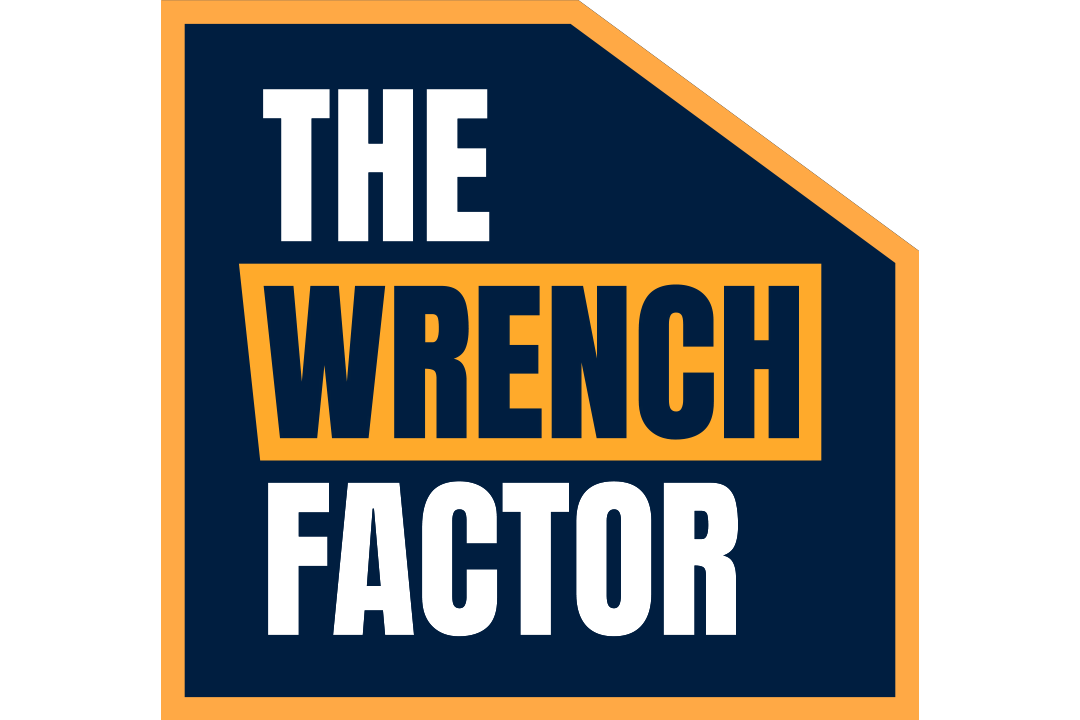
AI isn’t magic, and Willem Sundblad isn’t afraid to say it. Willem is the CEO of Oden Technologies, a data and AI company focused on helping manufacturers improve their processes. In other words, he’s all about finding practical ways AI can support operators as they look to cut costs, increase speed, and improve quality.
We got together with him to chat about how AI is being used across the manufacturing industry, and what manufacturers can expect to gain from the technology.
Willem and MaintainX Co-Founder Nick Haase dug into:
- Where most manufacturers currently stand when it comes to AI adoption
- The biggest AI myth in manufacturing
- How to get ROI from AI
- Under-hyped opportunities for AI tools
- One KPI every plant should track
Read on or watch the Wrench Factor conversation for answers to some of the most frequently asked questions about AI in manufacturing today.
Where are most manufacturers on their AI journey?
According to our 2025 State of Industrial Maintenance report, 44% of maintenance leaders say they’ve already implemented AI in their operations in some capacity.
But where do manufacturers fall in their implementation process? Are most of them still in the pilot phase? In Willem’s experience, the stages of implementation are all over the map: “It is very much all over the place. What I've seen is that the larger the company, the more likely they are to have gone further.”
While bigger companies are usually further along in their AI journeys, smaller manufacturers are showing they can be nimble and are eager to jump in. Across the board, manufacturers have high expectations for what AI can do for their operations.
Why are expectations for AI in manufacturing so high?
When it comes to AI-focused projects, manufacturers are setting ambitious targets. Nick describes a common conversation with executives about AI: “They're actually expecting a higher payback—three to five times higher than what they would ask for another type of digital transformation project that didn't have AI.”
Not every AI project will see that level of ROI, but when AI hits the mark, it can blow past even the highest expectations. ”[Leaders] know that not everything will be successful, that the winners will pay for the experiments that don't bear fruit,” Willem explains. “I think they've also seen that when it works, it works really well. Even that three to five times payback is probably low when it's really working.”
However, it’s wise to leave room for experimentation and discovery, as not every project is going to be a home run. “When these projects work, they tend to have pretty high ROI. But it's more fun when that's a bit of a surprise and not the expectation,” says Nick. “We're so early on this AI journey that you’ve got to give yourself an opportunity to learn.”
Where is AI most successful in manufacturing today?
As much as 40% of the maintenance and reliability workforce could retire over the next five years, according to the Hudson Institute. Already, the growing shortage of skilled workers requires maintenance teams and manufacturers to do more with less.
AI can help address the impact of the skills gap, not by replacing your team, but by creating workflows that help your team solve problems faster. “Maybe you can't find a hundred engineers, even if you have the resources to bring them in. The talent's just not there,” says Nick. “Most of it is just about speeding up workflows so one person can do way more than they were able to do before. But you still need that human judgment for [AI] to be really high value.”
AI-powered tools can also help teams share knowledge to close gaps between seasoned pros and new technicians, leading to quick productivity gains.
Willem describes this scenario from one of his customers: “No operator on the night shift had been [at the company] for more than seven months. So the performance difference between seasoned operators who had been there for 20 years on the day shift versus the new starters on the night shift was dramatic,” he explains. “By giving AI-driven recommendations to both of them—taking what the seasoned people were doing and providing those recommendations to the operators—they're now even, with an average increase in output between 18 and 20 percent.”
Why do AI projects fail?
The most effective AI projects begin with clarity on the outcome you want to drive. “Do you have unclear expectations? Do you have unclear goals? Given your data or infrastructure, is it possible to achieve your goals? If you don't have those things, your chances of success are pretty slim,” Willem says. “I think it's a bit compounded with AI because there might be a lack of clarity on what’s possible and what’s a good use case.”
Sometimes, lack of clarity can come from the executive side. For AI projects to succeed, executives need to align on goals with workers on the frontline. “The executive says, ‘let's go do AI here.’ And the frontline says, ‘I don't want to do this. I want you to help me solve this tangible problem right here,'" Willem explains. "Maybe you think [the best use case] is to help the operator with a certain thing, but the more realistic and achievable thing to do is speed up the workflow for the engineer so they can be more effective in their interactions with the operators or the supervisors.”
Getting your entire team up to speed on AI basics could help them more effectively identify ways to use the technology. Willem cites an example of a customer who saw better outcomes after AI training: “They trained the leadership team on the fundamentals of AI: What it is, what it isn't, and what's a requirement for a good use case, so that they could be better stewards of the decisions [about what to focus on].”
Willem’s most successful customers start with high-value, specific processes that give their teams quick wins. This ultimately sets the stage for bigger AI projects. “They're deploying machine learning engineers to very discrete processes where there's a high-value opportunity to improve. It's not even necessarily an entire line. It's just a specific process on the line. Once you're able to get those results, start to scale that specific function across your site or your organization.”
What’s the biggest AI myth in manufacturing today?
Many believe that AI is a magic wand for efficiency. But the truth is, AI tools are only as powerful as the data you give them. “I think a big problem can be when there are root challenges with the data itself, because [AI] isn't magic,” Willem says.
When you don’t have a data foundation, it will be challenging to get quality results from any AI model. Willem explains that a lack of quality data can come in several different forms: “It can mean that there’s low precision, which means that the [AI] model isn't trained with a real ground truth. It can mean that anything that’s manually recorded has inaccurate time stamps or has a little bit of judgment in it.”
Before moving forward with AI initiatives, take a closer look at your data inaccuracies and gaps. How much of your team's knowledge is in databases versus spreadsheets versus their heads? Who actually uses each data source, and for what?
What’s the most under-hyped AI opportunity for manufacturers?
To the point above, messy data and human guesswork can throw a wrench in AI technology’s effectiveness, which is why Willem argues that data labeling is the biggest AI opportunity that manufacturers miss.
"[Data labeling] makes all the other systems that you can integrate that data with more effective, because these systems are often missing the context." Willem explains. "The operators on the line have full context in the moment because they see things, they hear things, they're looking at multiple different things. But from a system perspective, a lot of that is stripped, and then you have to go to multiple systems to try to piece it all together again.”
Nick agrees: “You’ve got to eat your vegetables. It's not the most exciting project you'll get to work on, but it will pay the most dividends if you do it right. And you don't generally have to do it over and over again if you do it right upfront.”
What’s one KPI that shows AI’s value?
For Willem, the answer to this question isn’t definitive. The metric that matters most depends on the specific headaches a plant is dealing with.
"The answer for a lot of people is OEE, but then you'll have a lot of people fighting about how that's a really bad metric. We've got customers that have good quality, so it's all about performance and utilization. We've got customers that have quality problems, and performance or utilization doesn’t matter because they're fighting to maintain quality.”
However, he argues that the building blocks of OEE are a good jumping-off point, helping you pinpoint the issues you should consider taking on with AI. “I still think the pillars of OEE are an indicator of where you should start,” Willem explains. “It's at least a starting point to find the biggest problem you can tackle right now.”
Getting Started
By setting clear goals and expectations upfront, involving frontline workers in the AI conversation, and capturing quality data, manufacturers can cut through the AI hype and drive real results.
Want to learn more about how AI-powered tools like MaintainX CoPilot can help your team? Schedule a tour today.
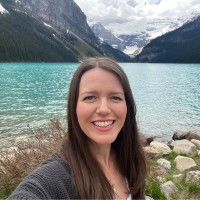
Senior Content Writer, MaintainX