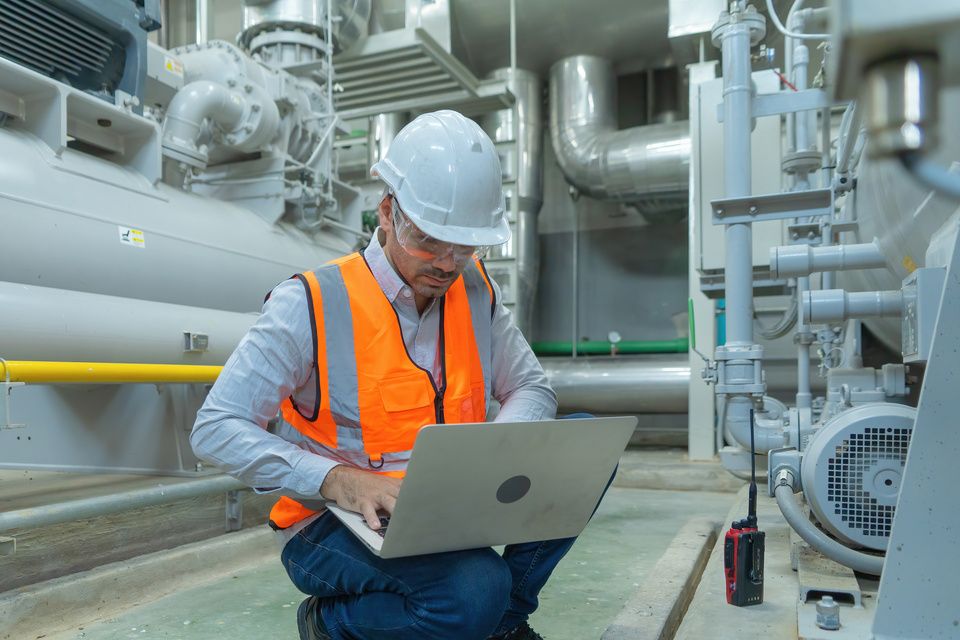
Os fabricantes usam o FMEA (Análise de efeitos e modo de falha) para identificar as possíveis formas pelas quais uma falha pode ocorrer em seus fluxos de trabalho. Obviamente, isso pode incluir uma ampla variedade de falhas (como falhas no equipamento, no processo ou no projeto). Esta publicação compara dois tipos de FMEA (PFMEA versus DFMEA), que ajudam a identificar os modos de falha do processo e do projeto.
Primeiro, o que é o FMEA?
O FMEA é uma abordagem estratégica para identificar possíveis falhas em um processo (fabricação, montagem ou logística) ou design (de um produto ou serviço).
Como o A Sociedade Americana de Qualidade explica:
“A análise de modos e efeitos de falha (FMEA) é uma abordagem passo a passo para identificar todas as falhas possíveis em um projeto, processo de fabricação ou montagem ou produto ou serviço. É uma ferramenta comum de análise de processos.”
O FMEA envolve dois componentes principais:
- Modos de falha: a maneira ou o modo pelo qual um processo ou projeto pode falhar. Por exemplo, um funcionário sobrecarregado pode perder um defeito quando é responsável pelas inspeções.
- Análise de efeitos: as consequências do fracasso. Por exemplo, um cliente pode processá-lo se um produto com defeito o prejudicar de alguma forma.
DFMEA e PFMEA são tipos de FMEA. Embora os processos DFMEA e PFMEA sejam semelhantes, as entradas e saídas são diferentes.
“A solução de problemas de causa raiz, usando abordagens como análise de árvore de falhas, bem como análise de causa e efeito ou modos e efeitos de falha (FMEA), é uma parte fundamental da estratégia de manutenção e confiabilidade de qualquer organização.”
McKinsey
O que é o DFMEA?
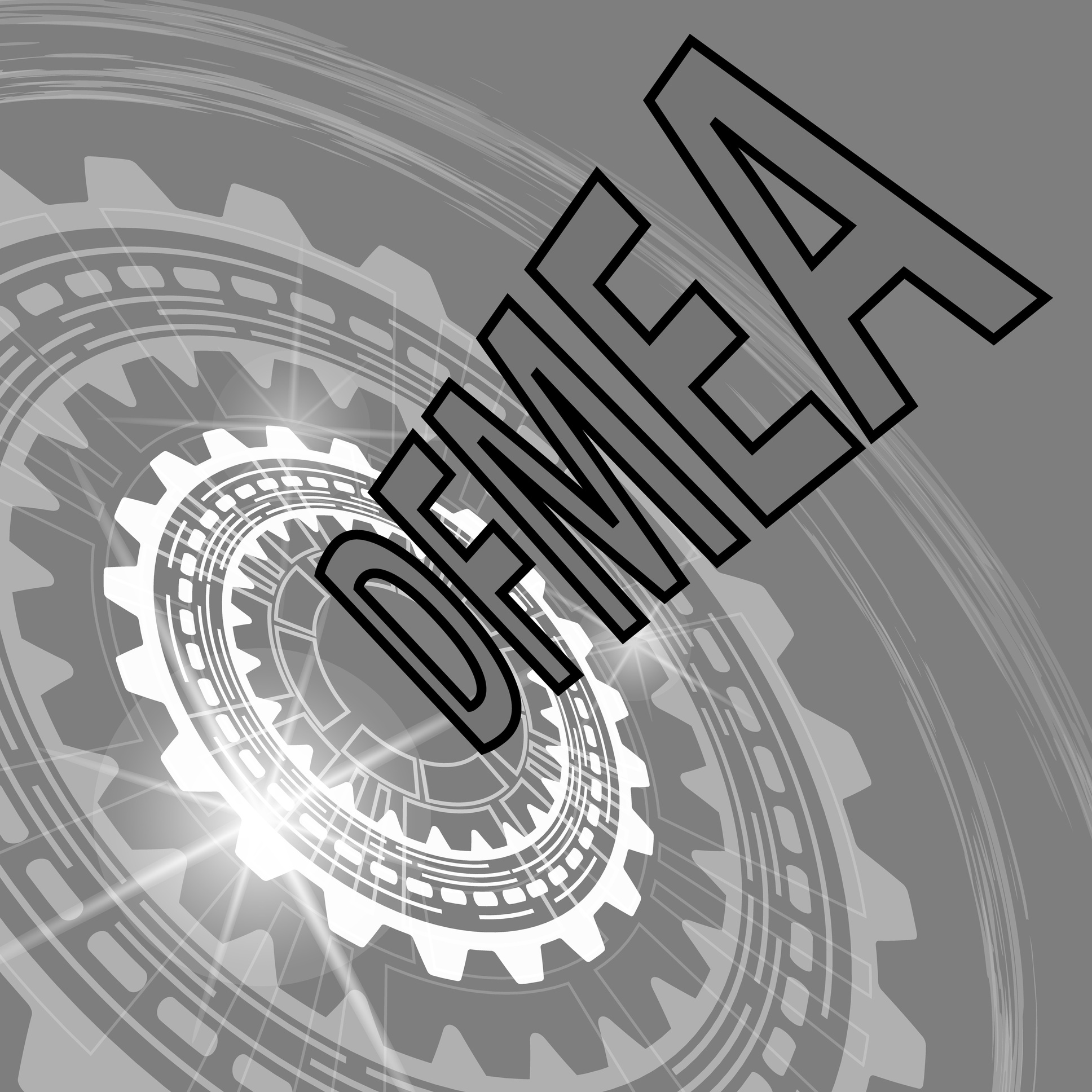
DFMEA (Design FMEA) é uma técnica que ajuda a identificar e corrigir falhas de projeto. O método é usado em todos os setores para minimizar os custos associados à falha no projeto, como recalls de produtos ou ações judiciais de clientes afetados pela falha no projeto.
O DFMEA envolve a listagem de possíveis modos de falha e seus efeitos potenciais, juntamente com uma classificação de gravidade, detecção, ocorrências e segurança. Em seguida, calcule um RPN.
O RPN é o Número de prioridade de risco, uma avaliação numérica do risco atribuído a um processo, ou etapas de um processo, como parte da Análise de Modos e Efeitos de Falha (FMEA). Uma equipe atribui a cada modo de falha valores numéricos que quantificam a probabilidade de ocorrência, a probabilidade de detecção e a gravidade do impacto.”
Você deve executar o DFMEA quando ainda estiver desenvolvendo o design do produto. Pensar nos possíveis modos de falha durante o desenvolvimento do produto ajuda a evitar falhas que, de outra forma, poderiam ser incorporadas diretamente ao design.
“Resolver problemas conhecidos com soluções conhecidas ajuda você a obter um rápido retorno sobre o investimento e vitórias antecipadas que podem ser duplicadas em todas as instalações. Essas pequenas vitórias também ajudam a aprimorar o suporte organizacional dos funcionários — o que é essencial para qualquer programa de análise — e da gerência para investimentos contínuos.”
Forbes
O que é o PFMEA?
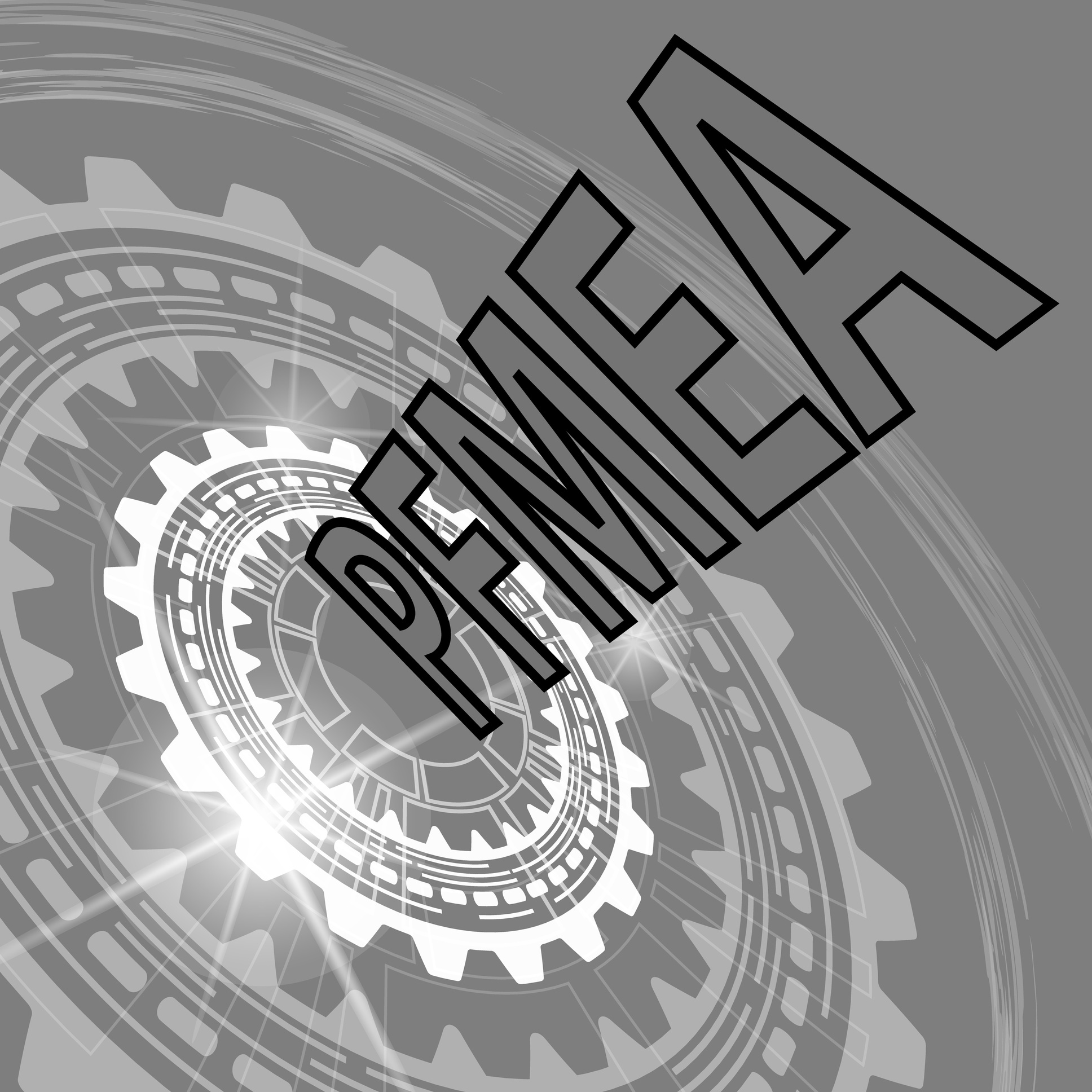
PFMEA (Process FMEA) ajuda analisar modos de falha do processo. Em outras palavras, o PFMEA ajuda a identificar possíveis falhas causadas por um processo. Um PFMEA atua como um documento vivo (físico ou digital) criado para cada processo e atualizado durante todo o ciclo de vida do produto.
Nesse caso, você precisa entender o impacto de uma falha no processo para minimizar o efeito da falha ou evitar completamente a falha.
Observe que você pode encontrar falhas mesmo ao usar o PFMEA. Caso contrário, você não precisaria de gerentes de confiabilidade e manutenção. No entanto, o PFMEA pode ajudar a minimizar o potencial de falha. Você deve analisar o PFMEA quando ocorrer uma falha ou se houver uma mudança significativa em seu equipamento, ambiente de fabricação e recursos.
DFMEA versus PFMEA: principais diferenças
Agora que você sabe o significado de PFMEA e DFMEA, vamos discutir algumas diferenças importantes entre os dois:
FMEA versus PFMEA: o processo
Ambos os tipos de FMEA seguem um processo ilustrado na Manual do AIAG-VDA FMEA—você pode usá-lo como um guia para ajudar a desenvolver o modo de falha e a análise dos efeitos do seu produto e do projeto.
O manual inclui as melhores práticas desenvolvidas por uma equipe global de OEMs (Fabricantes de equipamentos originais) e PME de nível 1 (especialistas no assunto). Ele combina as metodologias da AIAG (Grupo de Ação da Indústria Automotiva) e VDA (Associação Alemã da Indústria Automotiva) em uma abordagem mais estruturada.
Aqui estão as etapas do processo de FMEA de acordo com o manual AIAG-VGA:
- Etapa 1: Planejamento e preparação
- Etapa 2: Análise da estrutura
- Etapa 3: Análise de funções
- Etapa 4: Análise de falhas
- Etapa 5: Análise de risco
- Etapa 6: Otimização
- Etapa 7: Resultados e documentação
Qual modo de falha você deve priorizar?
A etapa 5 do processo DFMEA e PFMEA permite determinar os modos de falha que você deve abordar primeiro. Você pode priorizar os modos de falha com base na gravidade, na frequência e na facilidade com que é possível detectá-los.
Você precisa fornecer uma classificação para os seguintes fatores durante o FMEA:
- Severidade: Qual será a gravidade do impacto da falha do sistema ou da máquina?
- Detecção: Qual a probabilidade de a falha ser detectada quando ela se tornar uma possibilidade?
- Ocorrências: Qual é a probabilidade de ocorrer uma falha em um determinado período de tempo?
- Segurança: Qual é o risco para as pessoas e os sistemas se o sistema ou o maquinário falharem?
- Número de prioridade de risco (RPN): O RPN é calculado com base na gravidade, nas ocorrências e na detecção.RPN = gravidade x ocorrências x detecção Um RPN menor é desejável. Um alto RPN indica alto risco.
Depois de listar os modos de falha e atribuir uma classificação, você precisa listar a causa potencial da falha para cada modo de falha (usando técnicas como análise de causa raiz). Em seguida, você precisa determinar uma ação corretiva para minimizar o impacto de um modo de falha com base em sua RPN.
Quando usar o PFMEA e o DFMEA
Você pode usar o PFMEA ou o DFMEA nas seguintes situações:
- Você está prestes a desenvolver planos de controle para um processo
- Quando você aplica um produto existente ou processo diferentemente
- Antes de introduzir um novo produto, processo, etapa, método ou tecnologia
- Antes de implementar um processo de fabricação reprojetado
- Durante o processo como controle de qualidade ferramenta
- Ao analisar falhas de um processo ou produto existente
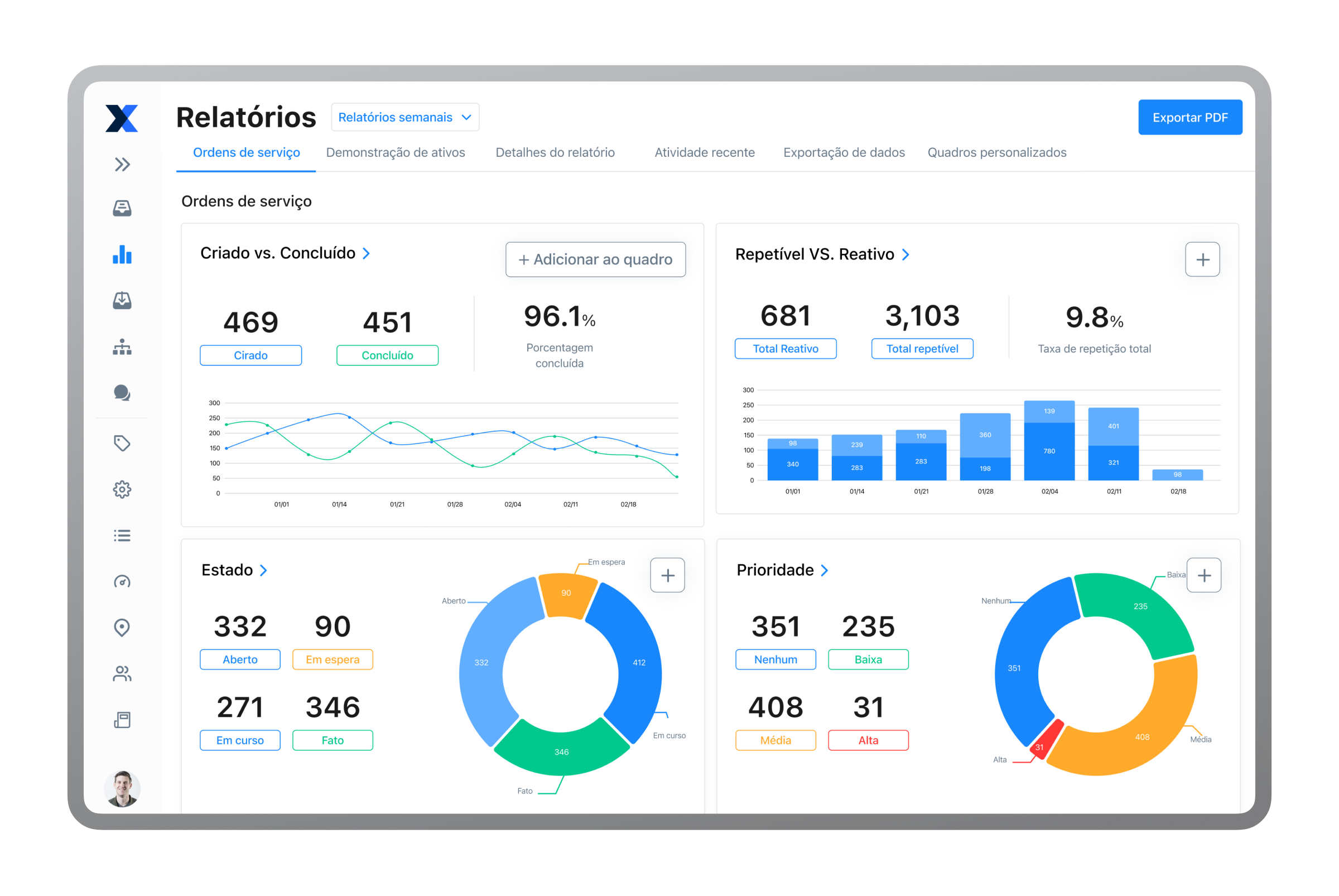
Colete dados para melhorar a precisão do DFMEA e do PFMEA
UM CMMS (sistema computadorizado de gerenciamento de manutenção) pode ajudar a coletar os dados necessários para melhorar a precisão do FMEA. Exemplos do tipo de dados que o CMMS pode coletar incluem avaria do equipamento história, tempo de inatividade histórico e o custo de reparar um ativo cada vez que ele falhou no passado.
Esses dados podem fornecer informações valiosas ao avaliar e revisar os modos de falha. Além de coletar dados, um CMMS simplifica os processos de manutenção, reduzindo o risco de falha. Com o MaintainX, você pode rastrear ativos, emitir ordens de serviço e colaborar usando a opção de bate-papo integrada.
Se você deseja usar o FMEA em suas instalações, experimente o MaintainX hoje.
FAQs
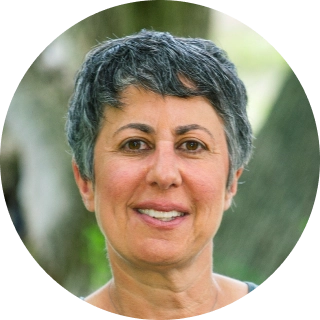
Caroline Eisner é escritora e editora com experiência nos setores de fins lucrativos e sem fins lucrativos, governo, educação e organizações financeiras. Ela ocupou posições de liderança em instituições de ensino fundamental e médio e liderou projetos digitais de grande escala, sites interativos e uma consultoria de redação comercial.