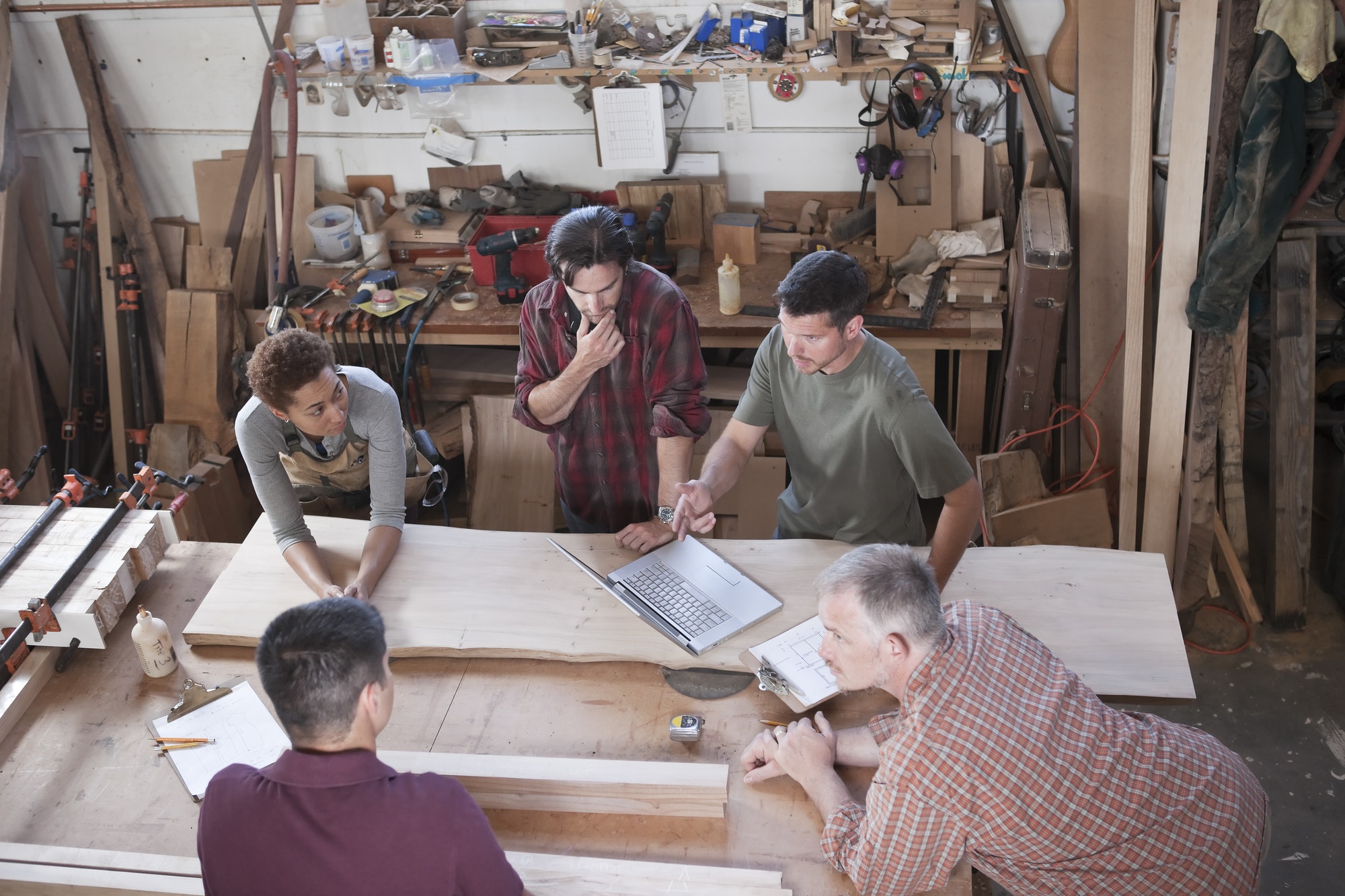
Você é novo no Modo de Falha de Projeto e Análise de Efeitos (DFMEA)? Este guia passo a passo fornecerá dicas úteis para conduzir seu primeiro DFMEA, incluindo alguns erros comuns a serem observados.
Nos últimos anos, esse subconjunto de FMEA silenciosamente ganhou popularidade em ambientes corporativos. Por quê? Porque permite que os engenheiros identifiquem os fatores de risco associados ao design do produto antes que as empresas invistam dinheiro em materiais, processos e equipamentos de fabricação ineficazes.
O que significa DFMEA?
Vamos começar respondendo à pergunta mais básica: o que é o DFMEA?
DFMEA significa “Design Failure Mode and Effect Analysis”. Os engenheiros executam o DFMEA para evitar problemas desnecessários no desenvolvimento de produtos. É um processo analítico que as empresas usam para identificar, mitigar e eliminar os riscos do design do produto. Na verdade, Capgemini explica que “a eficiência por design pode contribuir para ganhos de produtividade ao ajudar em áreas como utilização de ativos e custo de defeitos. Também terá um impacto positivo em áreas como rotação do portfólio de produtos e tempo de colocação no mercado, o que se traduzirá em maior participação de mercado.”
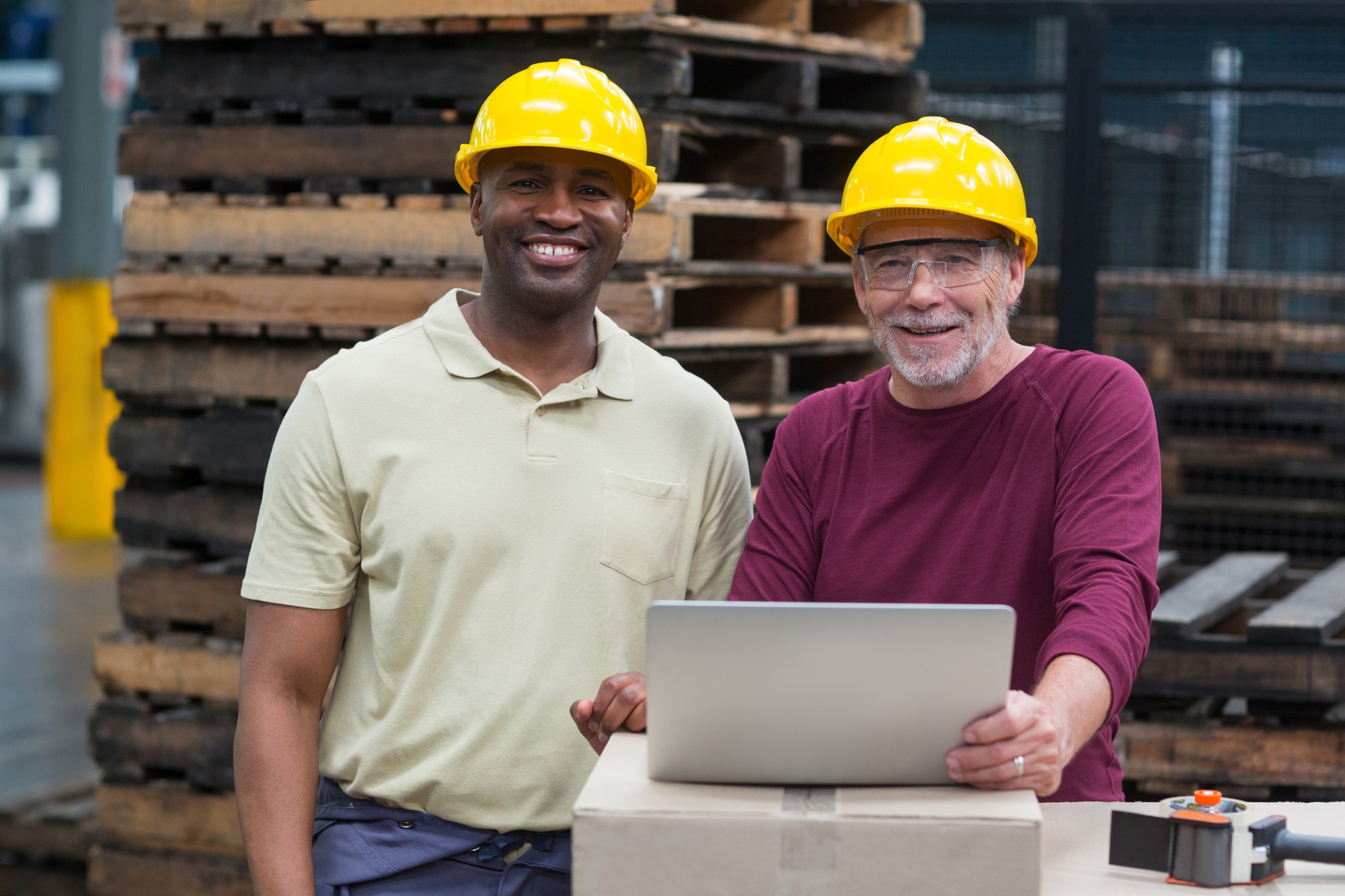
Qual é o objetivo do DFMEA?
O DFMEA é uma ferramenta indispensável de engenharia de produto para garantir que as empresas produzam produtos e serviços confiáveis que satisfaçam os clientes no cenário comercial competitivo atual.
Conforme mencionado anteriormente, as empresas usam o DFMEA para reduzir o número de defeitos de projeto. Idealmente, o processo ajuda as empresas a evitar que qualquer problema relacionado ao design ocorra. Qualquer coisa que impeça um produto de funcionar corretamente é considerada um “defeito”.
O resultado? A produção, fabricação e produção consistentes de produtos de alta qualidade. As empresas envolvidas nos setores de manufatura, tecnologia de ponta, prestação de serviços e construção têm maior probabilidade de usar o DFMEA.
Mas as organizações responsáveis pela produção de uma variedade de produtos e serviços também usam o método para gerenciamento de riscos. Por esses motivos, o DFMEA é uma parte vital do gestão da qualidade total processos.
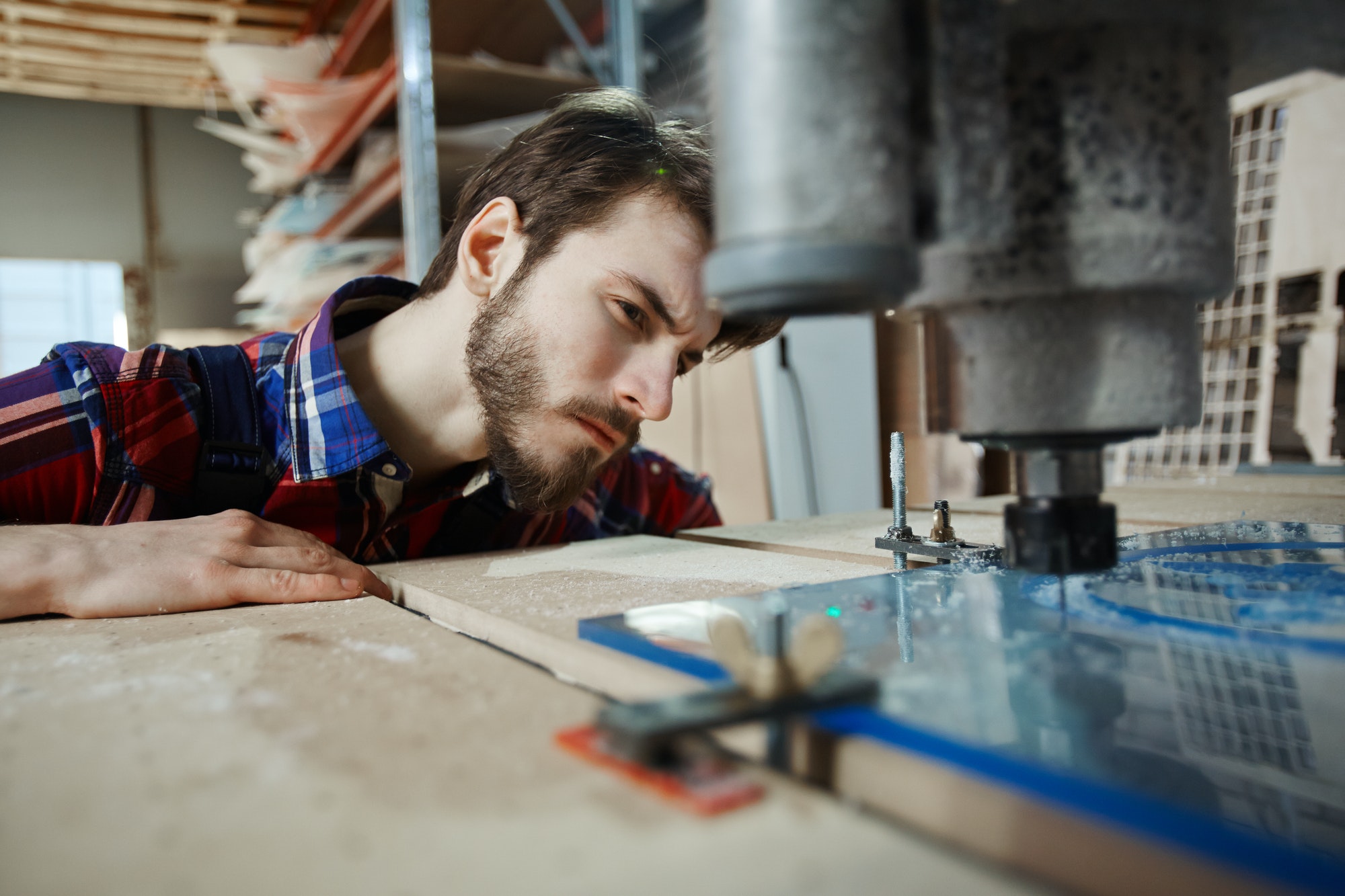
Como funciona o DFMEA?
O DFMEA analisa possíveis falhas de projeto de todos os ângulos para determinar o que poderia impedir que a função pretendida do produto acontecesse. Ele se concentra em quatro áreas de análise:
- Modo de falha: As formas pelas quais uma falha relacionada ao design pode ocorrer. Por exemplo, a interface do laptop congela quando um número X de programas está aberto por um número X de horas.
- Causa da falha: A causa raiz do modo de falha pode ser um defeito no design, no sistema, na qualidade ou na aplicação de peças de um dispositivo.
- Efeito de falha: As consequências imediatas da falha. Por exemplo, a interface congelada leva a uma experiência frustrante para o usuário.
- Gravidade da falha: A gravidade da falha afeta a produtividade, a qualidade e a segurança. Os engenheiros de qualidade geralmente pensam em termos dos piores resultados.
Em essência, o DFMEA ajuda a determinar o que pode dar errado, quão prejudiciais seriam as consequências e como mitigar os modos de falha antes que eles ocorram.
O DFMEA ajudou muitos setores, como manufatura, desenvolvimento de software, saúde e produção de alimentos, a adotar uma abordagem proativa de prevenção e redução de riscos.
Diferença entre DFMEA e FMEA
Modo de falha e análise de efeitos (FMEA) é simplesmente uma forma ampla de DFMEA. Essencialmente, é a mesma ferramenta de avaliação de risco aplicada a um escopo mais amplo de operações.
Equipes multifuncionais usam o FMEA para identificar possíveis falhas no design do produto, nos processos de produção e no tempo de inatividade do equipamento. Eles aplicam o método analítico a uma infinidade de aplicações, não apenas aos modos de falha relacionados ao projeto. Como resultado, as empresas gastam menos tempo, dinheiro e recursos no DFMEA em comparação com o FMEA.
As organizações realizam o DFMEA nos seguintes cenários:
- Antes de lançar um novo produto, processo ou serviço
- Antes de implantar estratégias ou produtos existentes em novas capacidades
- Antes de desenvolver planos de controle do sistema para processos existentes e novos
- Ao fazer melhorias nos processos, produtos e serviços existentes
- Quando os clientes reclamam rotineiramente de uma entrega
Conforme mencionado anteriormente, o objetivo do FMEA é minimizar grandes falhas em produtos, processos e serviços. Tanto o FMEA quanto o DFMEA buscam identificar possíveis falhas, determinar a gravidade das consequências da falha e recomendar melhorias para mitigar esse risco.
E tanto o DFMEA quanto o FMEA se concentram na redução dos custos operacionais, enquanto o FMEA visa reduzir as despesas relacionadas à manutenção de equipamentos.
Benefícios do DFMEA
O DFMEA é uma poderosa ferramenta de controle de qualidade que oferece vários benefícios, incluindo:
- Gerenciamento eficaz de riscos: É quase impossível criar um produto ou serviço sem algum tipo de supervisão. Quanto mais complexa mecanicamente a entrega, maior a probabilidade de seus processos de produção conterem ineficiências. O DFMEA facilita a identificação de possíveis problemas que, de outra forma, não seriam detectados até as fases de produção experimental.
- Altos índices de satisfação do cliente: Problemas de design, por menores que sejam, podem incomodar seriamente os clientes. A identificação de possíveis modos de falha durante o estágio de projeto com o DFMEA fornece uma rede de segurança para detectar os tipos de falhas que incomodam os clientes. Empresas que oferecem experiências perfeitas aos clientes conquistam seguidores mais fiéis do que aquelas que não o fazem, o que leva a um maior reconhecimento, longevidade e lucratividade da marca.
- Custos de produção mais baixos: Produtos problemáticos geralmente acabam sendo retirados. Isso não apenas aumenta os custos de produção, mas também resulta em atrasos no lançamento de produtos. O DFMEA ajuda a evitar tais problemas, apoiando a criação de soluções realistas.
- Priorize os itens de ação: O DFMEA não é apenas eficaz na identificação de possíveis falhas de projeto, mas também é eficaz na priorização de ações de mitigação. O DFMEA classifica os diferentes modos de falha com base na gravidade, ocorrência e capacidade de detectar as falhas.
Agora que você entende por que as equipes de design praticam o DFMEA e o que o processo envolve, vamos nos aprofundar em como elas o fazem.
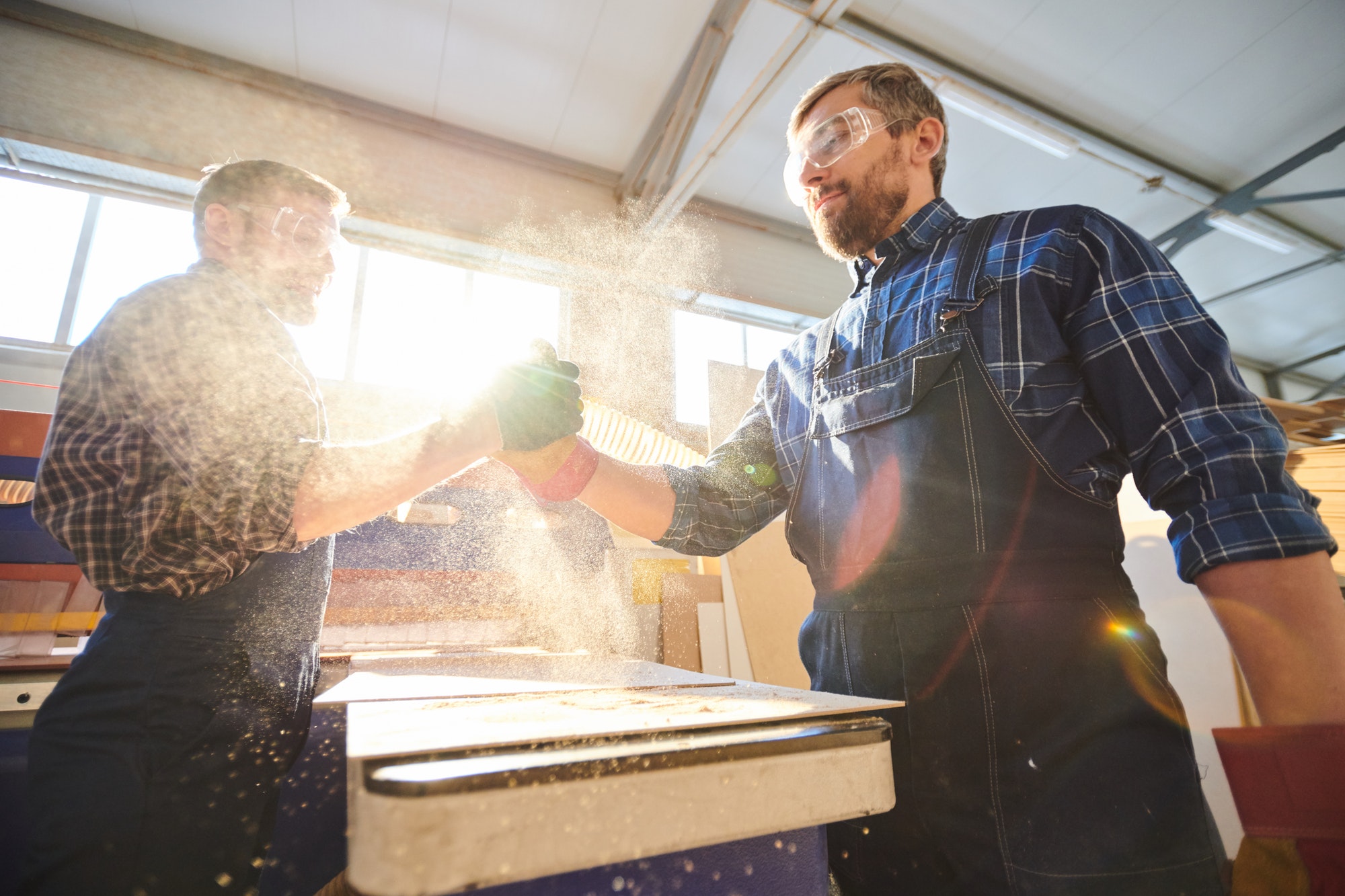
Como executar o DFMEA?
Como o DFMEA envolve muitas variáveis e vários membros da equipe, as coisas podem ficar um pouco complicadas sem sistemas adequados. Por esse motivo, siga as diretrizes padrão em todo o processo de planejamento e execução.
Abaixo está um resumo passo a passo para realizar o DFMEA:
Etapa 1: Revise o design
A primeira etapa envolve a montagem de uma equipe multidisciplinar para participar da análise. As equipes do DFMEA geralmente consistem em um engenheiro de qualidade de produto, engenheiro de análise de testes, engenheiro de materiais e equipes de produção, serviço e logística.
Sua equipe multifuncional avaliará todos os sistemas, subsistemas, interfaces e componentes para identificar os possíveis modos de falha do seu produto. O ideal é incluir representantes de cada ponto de contato do processo de produção para avaliar possíveis modos de falha de todos os ângulos.
O objetivo nesse estágio é determinar o quão bom é o design do produto e ver melhorias que possam torná-lo melhor. Cada item é isolado e investigado para que os engenheiros de qualidade possam identificar os modos de falha de cada um.
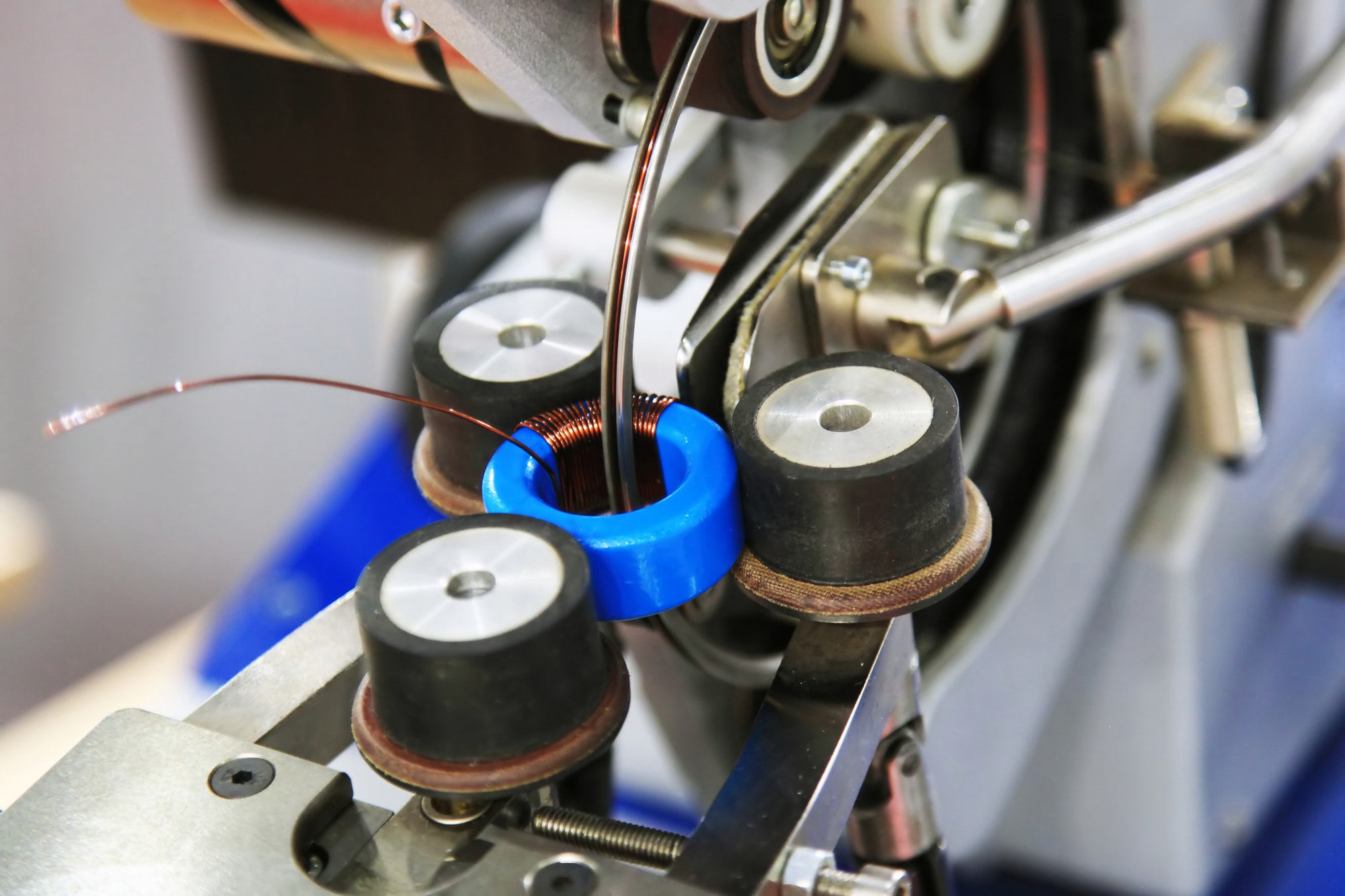
Etapa 2: Identificar todos os modos de falha
Avalie minuciosamente cada item e identifique todos os possíveis modos de falha, incluindo:
- Falhas completas: Esse tipo de modo de falha prejudica o sistema ou seus componentes. O sistema não pode funcionar até que a peça defeituosa seja totalmente substituída.
- Falhas parciais: Enquanto o sistema ou produto ainda está funcionando, o modo de falha impede que ele funcione totalmente. Isso resulta em produtividade reduzida.
- Falhas intermitentes: O mau funcionamento é irregular e imprevisível para esse tipo de modo de falha.
- Falhas degradadas: Esse tipo de modo de falha é resultado da fadiga causada pelo uso frequente. O sistema eventualmente fica mais fraco.
- Falhas não intencionais: Em caso de falha não intencional, a falha geralmente é resultado da falha de outro item.
É fundamental reconhecer que um único sistema ou componente pode experimentar mais de um tipo de modo de falha. Documente cada modo de falha — nenhum detalhe é pequeno demais. Também existem certas condições operacionais, de uso e operações de serviço que podem afetar os modos de falha.
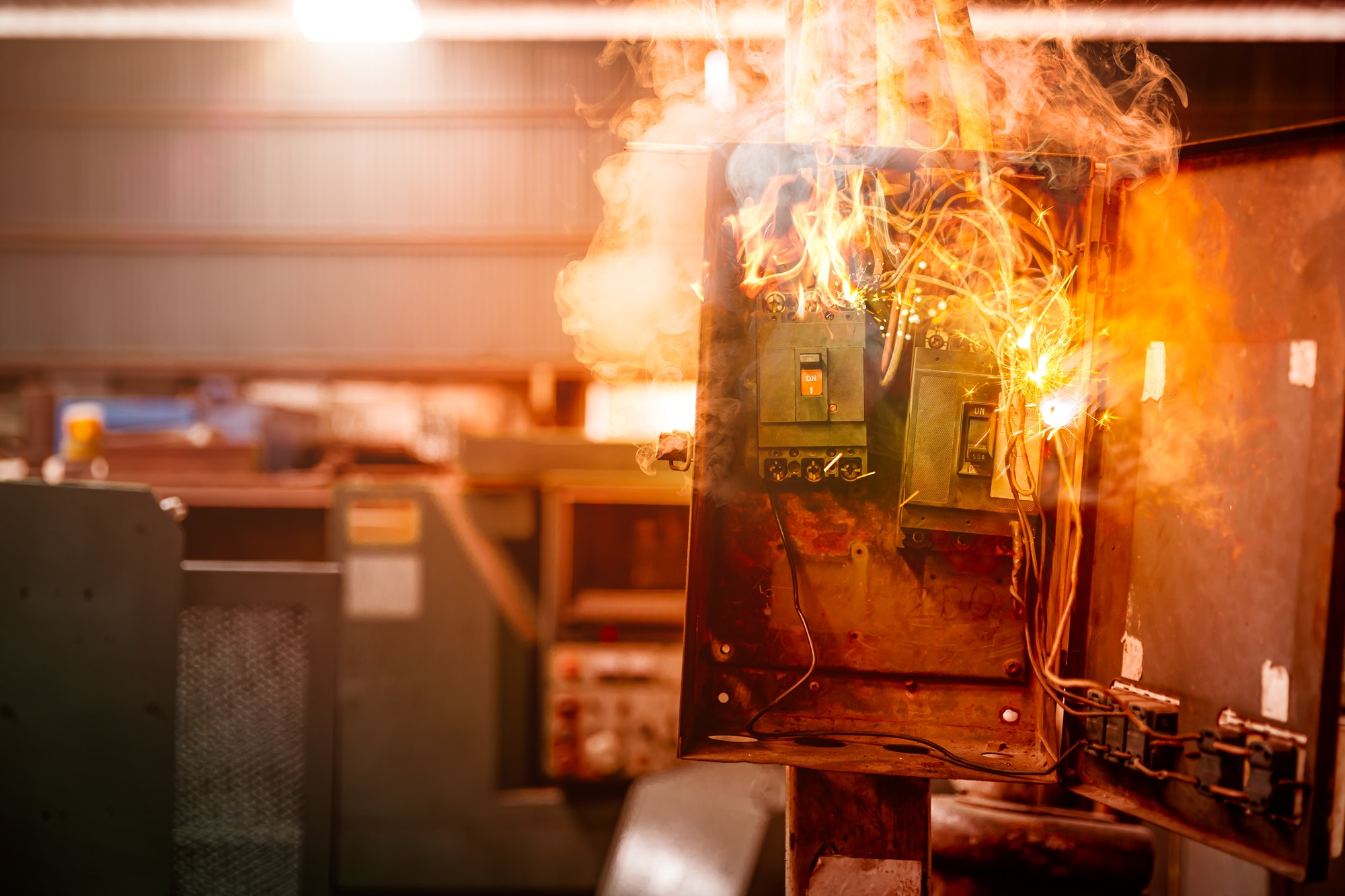
Etapa 3: descreva as consequências de cada modo de falha
Depois de identificar todos os modos de falha em potencial, a próxima etapa é identificar as consequências de cada modo de falha. Os efeitos podem ser menores ou graves.
Por exemplo, um surto elétrico (modo de falha) pode resultar em lâmpadas queimadas (consequências menores) ou em um incidente de incêndio (impacto severo).
Etapa 4: atribuir classificação de gravidade a cada modo de falha
Em seguida, determine a gravidade de cada modo de falha no sistema, nos subsistemas, nos componentes, nos usuários e em outras partes interessadas relevantes. O grau de severidade variará para cada modo de falha, sistema e componente. Quanto maior a classificação de gravidade, mais sério é o modo de falha.
Classifique os modos de falha com base nos seguintes critérios:
- 9-10: Qualquer coisa que afete a segurança e a conformidade regulatória.
- 7-8: O modo de falha faz com que o sistema ou componente perca ou sofra uma degradação de sua função principal.
- 5-6: O sistema/componente só perde ou degrada sua função secundária. O modo de falha não afeta a função principal.
- 2-4: O modo de falha só causa incômodo, mas não afeta em nada a funcionalidade do sistema/componente.
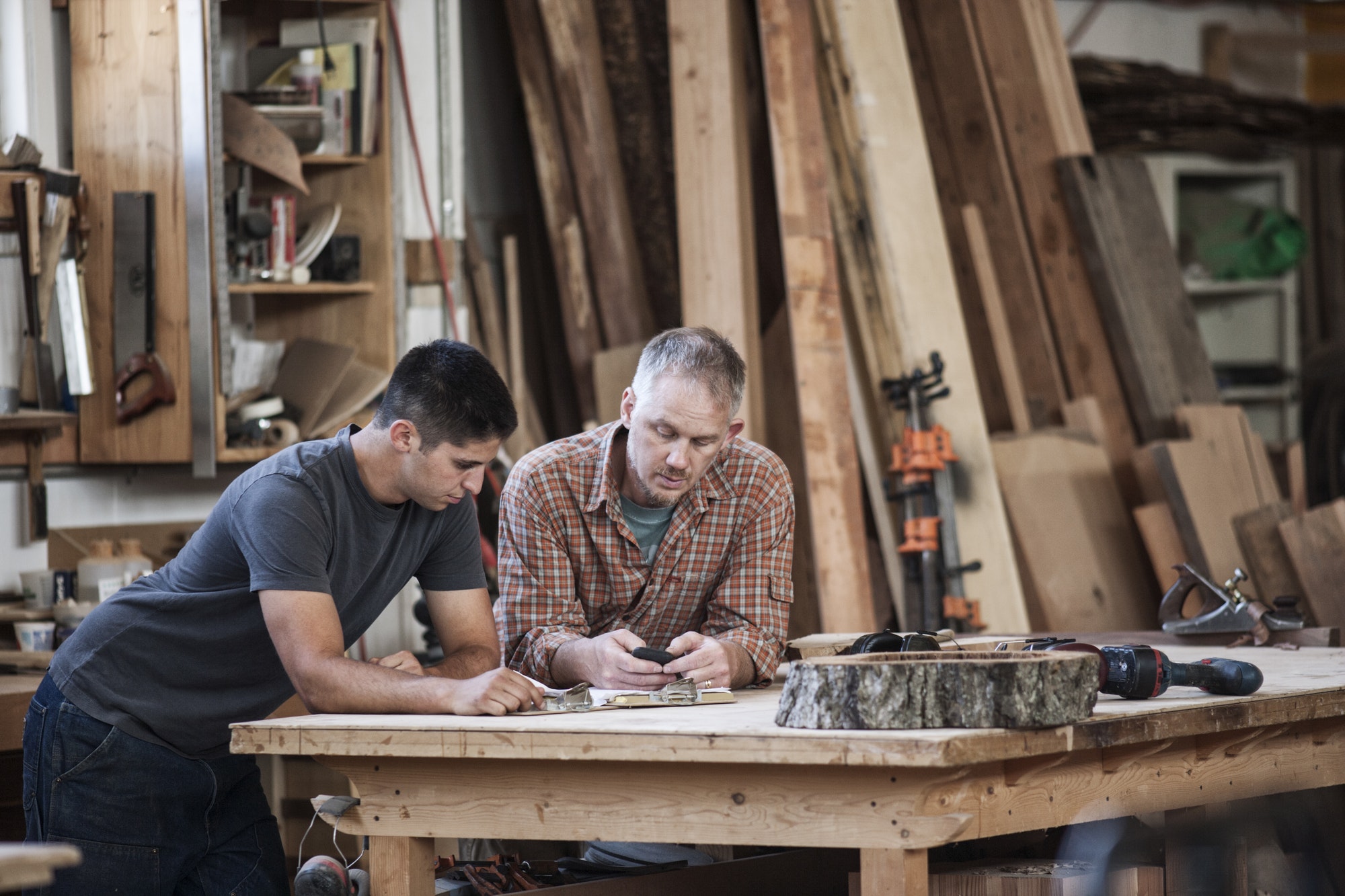
Etapa 5: Identificar as causas principais da falha
Em algum momento, toda organização, por mais consciente que seja, experimenta uma falha de design. É inevitável! Mas processos abrangentes do DFMEA podem facilitar menos problemas após o lançamento.
Para resolver os modos de falha, você precisa primeiro identificar suas causas principais. Isso é o que você fará nesta fase.
Etapa 6: avaliar os controles de projeto existentes
Em seguida, avalie seus controles de projeto existentes para determinar a eficácia com que eles podem detectar e evitar as falhas discutidas anteriormente. Controles de projeto robustos devem ser capazes de evitar, ou pelo menos prever, os modos de falha. Há dois tipos de controles de design:
- Controles de prevenção: Esses controles ajudam a eliminar a ocorrência de falhas. Eles incluem requisitos de design, material e engenharia, bem como documentação. Os controles de prevenção geralmente servem como procedimentos operacionais padrão (SOPs) ao realizar projetos.
- Controles de detecção: Confie nos controles de detecção para identificar as causas da falha e da falha antes que elas ocorram. Você pode usar controles de detecção durante a prototipagem, testes de confiabilidade, testes funcionais e simulações.
Lembre-se: o objetivo principal dos controles de design é permitir que você evite incidentes antes do lançamento final do produto.
Etapa 7: atribuir classificações de ocorrência a cada modo de falha
Use classificações de ocorrência para determinar a probabilidade de cada modo de falha ocorrer. As equipes do DFMEA geralmente contam com uma escala de classificação de 1 a 10. Os modos de falha com classificações de ocorrência mais baixas têm chances mínimas de ocorrer, enquanto aqueles com números mais altos quase certamente ocorrerão.
Etapa 8: atribuir classificações de detecção a cada modo de falha
Assim como nas classificações de gravidade e ocorrência, avalie as classificações de detecção em uma escala de 1 a 10. Só que desta vez, pergunte a si mesmo: qual a probabilidade de detectarmos cada um dos modos de falha identificados antes que eles ocorram?
O objetivo é determinar a eficácia dos controles de projeto existentes na detecção de problemas antes que eles ocorram. Classificações de detecção mais baixas significam que é muito provável que sua equipe descubra problemas. Como alternativa, quanto maior a classificação de detecção, menos plausível é prever a ocorrência do modo de falha.
Etapa 9: Calcular números de prioridade de risco (RPN)
Infelizmente, há poucas horas em um dia para se dedicar ao desenvolvimento de produtos! Conhecer seus RPNs é fundamental para determinar quais problemas de design os membros da equipe devem resolver primeiro.
Dê prioridade máxima aos modos de falha com os RPNs mais altos. Depois que as classificações forem atribuídas, o RPN para cada problema é calculado multiplicando Gravidade x Ocorrência x Detecção
Fórmula do número de prioridade de risco:
RPN = Ocorrência × Gravidade × Detecção
Etapa 10: Estabelecer ações corretivas
Nesse estágio, você pode ter descoberto informações que sugerem a necessidade de modificações nos processos de design existentes. Estabeleça um RPN aceitável para os modos de falha e documente suas ações corretivas. Além disso, identifique todas as ferramentas necessárias para reduzir sua RPN.
Etapa 11: Implementar o plano de ação corretiva (recalcular RPNs)
Depois de desenvolver seu (s) plano (s) de ação, é hora de começar a trabalhar! Faça com que todos participem e implemente seu plano de ação de design de produto. Ao final do período de implementação, recalcule o RPN para avaliar o progresso mensurável.
Sua equipe conseguiu reduzir seus rankings de ocorrência e gravidade? A classificação de detecção aumentou? Quando se trata de manutenção, gerenciamento de ativos e gerenciamento de inventário de equipamentos, recomendamos o uso de um CMMS (sistema computadorizado de gerenciamento de manutenção) como o MaintainX para acompanhar seu progresso.
Um CMMS fácil de usar simplificará o gerenciamento de dados, economizará tempo com listas de verificação processuais digitais e fornecerá métricas significativas que apoiam a tomada de decisões eficazes de O&M.
Exemplo de prática do DFMEA
Quer ver como é o DFMEA em ação?
Confira este exemplo de um DFMEA conduzido para o desenvolvimento de uma porta frontal de automóvel em uma fábrica compilada pela ReliantSoft.
A próxima seção destacará alguns dos erros mais comuns que as empresas cometem ao implementar análises gerais e de modo de falha de projeto e efeitos.
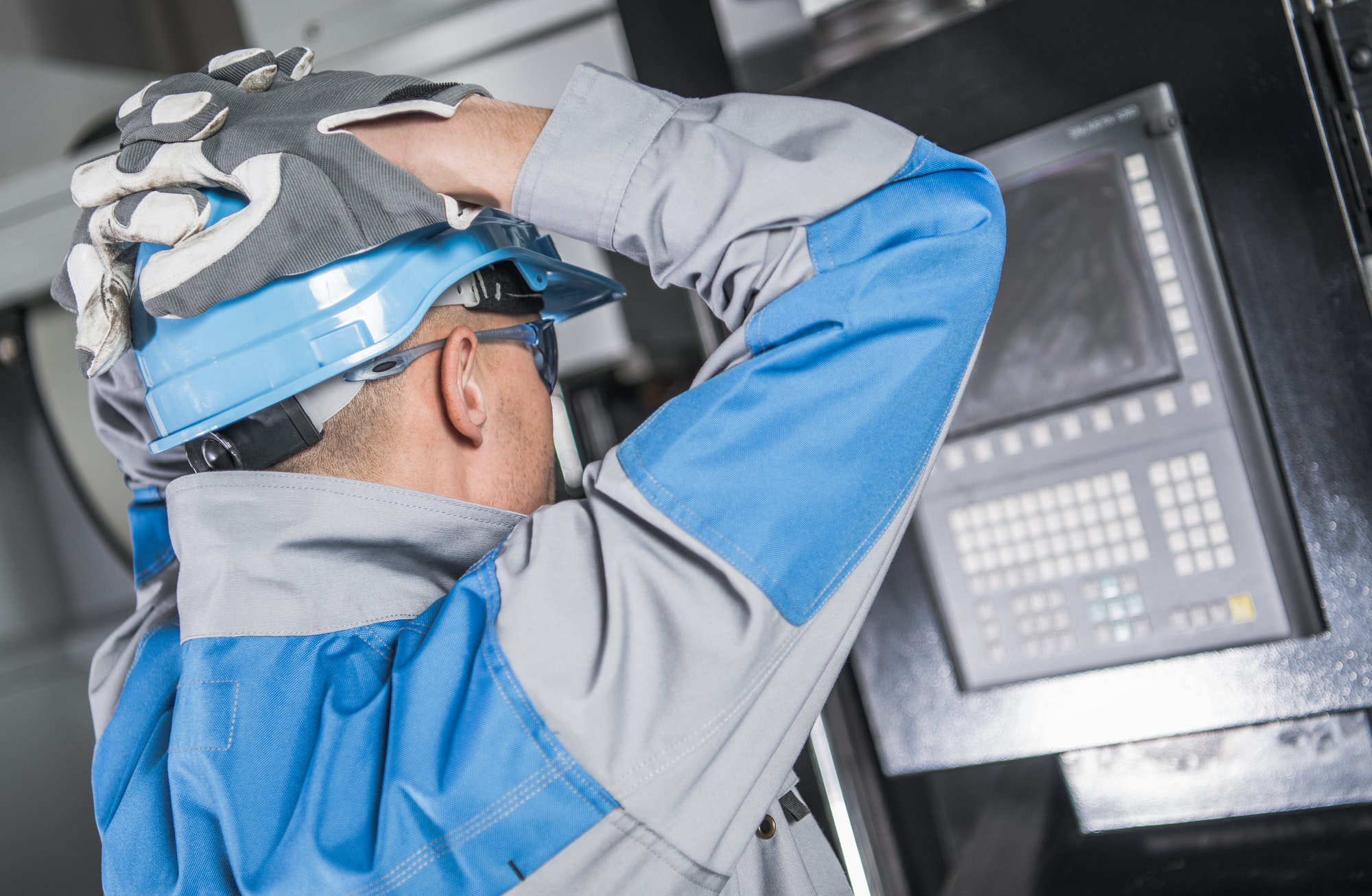
Erros comuns cometidos com o DFMEA
Abaixo estão alguns dos erros mais comuns que as organizações cometem ao tentar FMEAs pela primeira vez:
1. Não integre os tipos de FMEA
A falta de integração com o FMEA é uma ocorrência comum em muitas organizações. Não é incomum que a liderança lide com vários projetos de FMEA isoladamente, apesar da significativa sobreposição entre funções e departamentos.
Você não pode executar o DFMEA de forma eficaz enquanto ignora processo FMEA (PFMÉIA). O PFMEA se concentra na avaliação de possíveis contratempos nos processos operacionais que interrompem os resultados. Isso ajuda os departamentos de manutenção a priorizar manutenção preventiva (PM) fornecendo um método para medir as diversas consequências da quebra de ativos. O PFMEA também pode servir como um catalisador para diminuir os custos de produção, eliminar o desperdício de produção e reduzir o tempo de inatividade.
2. Propriedade incorreta do FMEA
Outro erro comum de iniciantes é atribuir aos departamentos de controle de qualidade a propriedade total do DFMEA. Essa supervisão é prejudicial porque os engenheiros de qualidade normalmente não são os principais executores dos processos de projeto e produção em análise.
Eles podem não ter conhecimento em primeira mão sobre detalhes do sistema, requisitos de design e como as mudanças no desenvolvimento de produtos acabarão afetando os usuários finais. Por esse motivo, é aconselhável atribuir o projeto aos designers de produto e atribuir funções de apoio a outros membros do departamento.
3. Forças-tarefa incompletas
Além da propriedade do FMEA, a composição da equipe do FMEA também costuma ser um grande desafio para as organizações. Se você selecionar as pessoas erradas para compor a equipe, acabará com medidas ineficazes de mitigação de riscos. Na verdade, você pode acabar piorando as coisas.
A equipe do FMEA deve sempre ser formada por pessoas com conhecimento sobre design e requisitos do cliente e como atendê-los. O departamento principal do sistema deve ser incluído na equipe.
4. Tempo ruim
Infelizmente, às vezes é possível fazer tudo certo, mas na hora errada. Como realizar o FMEA na hora errada? Eles não pensam no FMEA até que algo dê errado!
Isso pode fazer com que as organizações executem o FMEA apenas para preencher a papelada. Isso se torna outro processo a ser cumprido, em vez de procurar proativamente maneiras de melhorar seus sistemas e produtos.
Em vez de tornar o DFMEA uma reflexão tardia cara, tente concluir a análise durante a fase de design do produto. Você não pode iniciar o PFMEA e o System FMEA primeiro e depois concluir o DFMEA. O DFMEA vem em primeiro lugar, seguido pelos outros.
Simplifique o gerenciamento de ativos com o MaintainX
Uma das maneiras mais fáceis de organizar as informações relacionadas ao equipamento é com o MaintainX.
Nossa plataforma compatível com dispositivos móveis permite que as equipes operacionais cataloguem, analisem e atuem de acordo com métricas cruciais para reduzir a ocorrência de gargalos de produção. Sem nenhum treinamento, a maioria dos trabalhadores se sente à vontade para criar, atribuir e monitorar ordens de serviço em minutos.
Perguntas frequentes
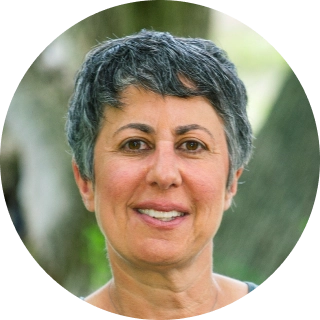
Caroline Eisner é escritora e editora com experiência nos setores de fins lucrativos e sem fins lucrativos, governo, educação e organizações financeiras. Ela ocupou posições de liderança em instituições de ensino fundamental e médio e liderou projetos digitais de grande escala, sites interativos e uma consultoria de redação comercial.